Оглавление:
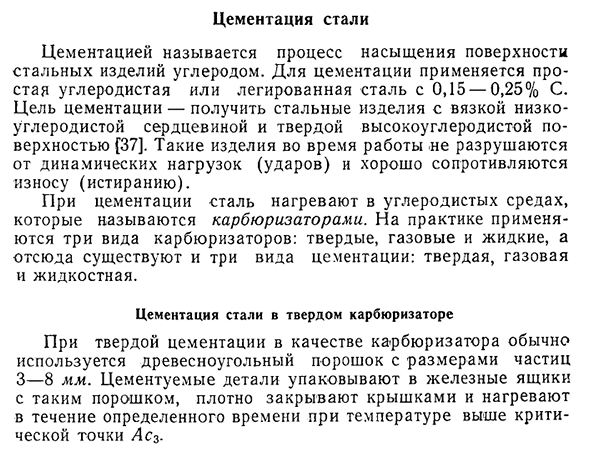
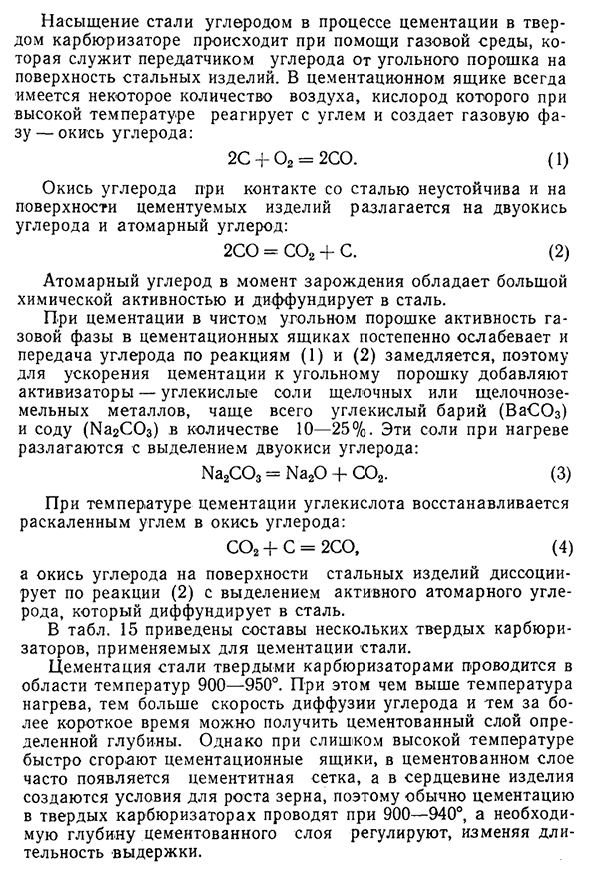
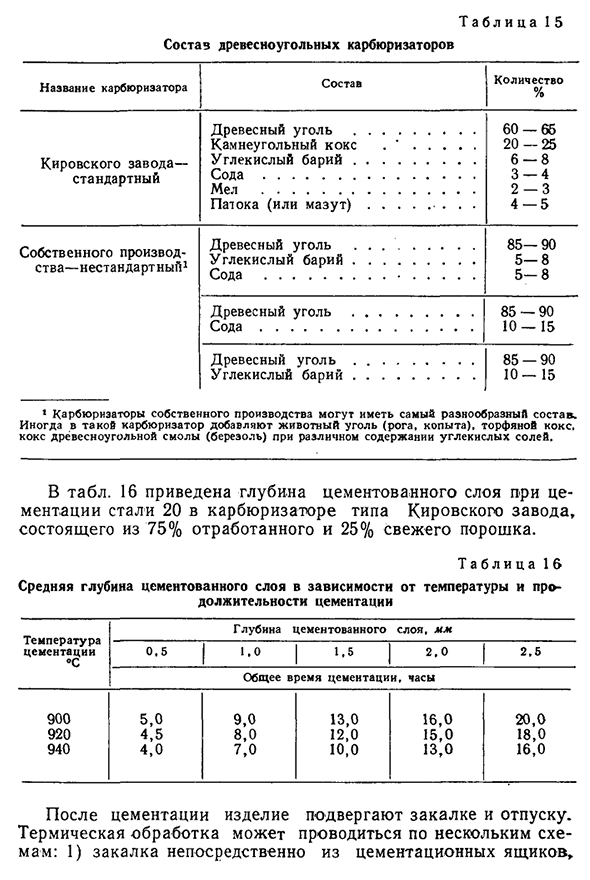
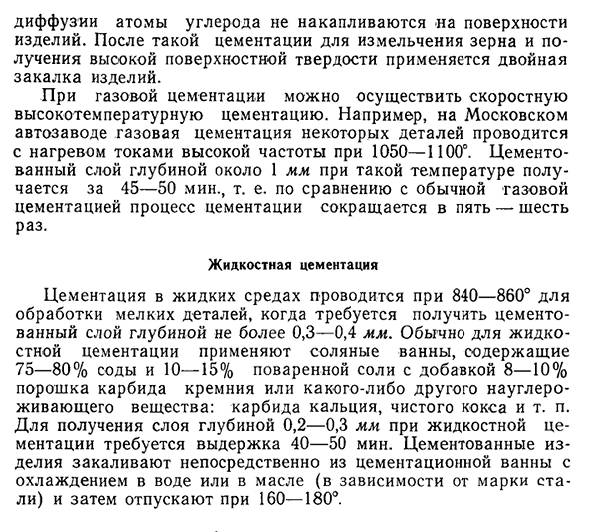
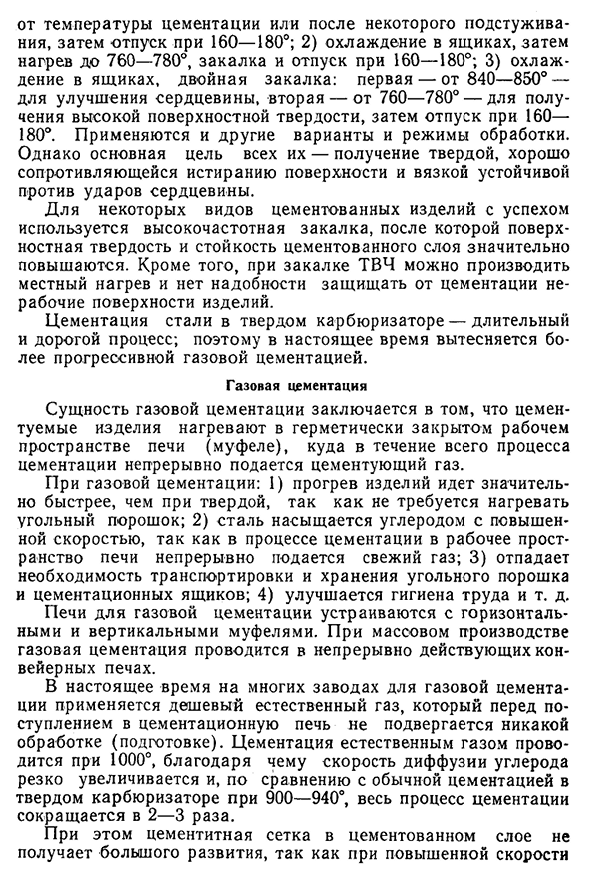

Цементация стали
- Стальной цемент Цементация-это процесс, при котором поверхность стального изделия насыщается углеродом. Для цементации используют простые углеродистые или легированные стали с содержанием 0,15〜0,25% C. Цель цементации-получение стальных изделий с вязкой низкоуглеродистой сердцевиной и твердой высокоуглеродистой поверхностью[37].
Такие изделия в процессе эксплуатации не разрушаются динамическими нагрузками (ударами), они достаточно устойчивы к истиранию (истиранию). Во время цементации сталь нагревается в углеродистой среде, называемой carburetor. In практика, используются 3 типа цементирующих агентов: твердые, газообразные и жидкие. Из этого следует, что существует 3 вида цементации: твердая, газообразная и жидкая. Цементирование стали в твердом карбюраторе
В твердом цементе в качестве цементирующего агента обычно используют древесный уголь с размером частиц 3-8 мм. Людмила Фирмаль
Цементируемая часть упаковывается в железный ящик с таким порошком, плотно закрывается крышкой и нагревается в течение определенного времени при температуре выше критической точки. Насыщение стали углеродом при цементации твердыми карбюраторами происходит с использованием газовой среды, которая служит переносчиком углерода из угольного порошка на поверхность стали products. In в цементном ящике всегда присутствует определенное количество воздуха, кислород которого при высоких температурах вступает в реакцию с углем с образованием газовой фазы. Окись углерода: 2С + О= 2СО. (1)
Монооксид углерода при контакте со Сталью неустойчив и разлагается на поверхности цементных изделий на углекислый газ и атомарный углерод. 2CO = CO2 + C(2) Атомарный углерод в момент зарождения высоко химически активен и диффундирует в сталь. Во время цементации в чистом угольном порошке активность газовой фазы в цементном ящике постепенно снижается, а перенос углерода по реакции (1) и (2) происходит медленно, поэтому активный агент (карбонат щелочного или щелочноземельного металла) добавляется к углеродному порошку для содействия цементации общего Валия (BaCO3) и натрия (Na2co3co) снижается на 10%. содержится в количестве 25%.Эти соли разлагаются при нагревании, выделяя углекислый газ: Na2CO3 = Na2O + CO2. (3) при температуре цементации диоксид углерода восстанавливается до монооксида углерода горячим углем. CO2 + C = 2CO, (4)
- Монооксид углерода на поверхности стальных изделий диссоциирует по реакции (2) с выделением активных атомов углерода, диффундирующих в атом железа. В таблице. На рис. 15 показан состав твердого карбюраторного сусла, используемого при цементации стали. Цементирование стали твердым карбюратором осуществляется в интервале температур 900-950°. кроме того, чем выше температура нагрева, тем больше скорость диффузии углерода, тем меньше времени можно будет получить цементный слой определенной глубины. Однако, если температура слишком высока, то цементируя коробка сгорит вне быстро и цементирующая сетка часто будет появляться на цементированном слое, и условие роста зерна будет создано в ядре продукта, поэтому твердое затвердевание обычно бежит на 900-940°с обуглероживая машиной для того чтобы контролировать необходимую глубину цементированного слоя.
Экспозиция меняется раз 50 стали химико-термической обработки Таблица 15. состав цементирующего агента Карбюратор название состав количество Кировский заводской стандарт Уголь уголь кокс карбонат бария. Сода меловая меласса (или мазут) древесный уголь карбонат бария. Сода. Уголь сода уголь карбонат бария. 60-65 20-25 6-8 От 3 до 4. 2-3 4-5. Собственное производство-нестандартное 1 85-90 5-8 5-8 85-90 10-15. 85-90 10-15. Один Карбюратор собственного производства может иметь самую разнообразную конфигурацию. В таких науглероживающих машинах можно добавлять животный уголь(рога, копыта), торфяной Кокс,
Древесноугольный Дегтярный Кокс(Береза) с различным содержанием карбонатов. Людмила Фирмаль
В таблице. Рис 1子は、75%の使用 済み 粉末末と250%新鮮質プラントタイプの気化器内で 鋼 の 鋼20をセメメント接合するときのセメント層の 深さを示している。1 Таблица 16.Средняя глубина цементируемого слоя в зависимости от температуры и времени цементирования. Температура цементации » C 900. Девятьсот двадцать 940. 0.5 Глубина цемента 1.0 1.5 Слой мм 2, 0, 2.5 Общее время цементирования, раз 5-0 4,5 4.0 9.0 8.0 7.0 13.0 12.0 10.0 16,0 15.0 13.0 20,0 18.0 16,0 После цементации продукт подвергается упрочнению и отпуску. Термообработку можно проводить по нескольким схемам: 1) цемент 51 из стали закалять непосредственно из цементного ящика От температуры цемента или после некоторого армирования оставляют 160-180°; 2) в ящике охлаждают, затем нагревают до 760-780°, а в 160-180° — до закалки и отпуска.
3) охлаждение выдвижного ящика, двойное отверждение: первое-от 840-850° — для улучшения сердечника, второе-от 760-780° — для получения высокой поверхностной твердости, отпуск при 160-180°.Применяются другие параметры и режимы обработки. Но главная цель всех них-обзавестись прочной и стойкой сестрой Поверхность и вязкую сердцевину от ударов. В некоторых видах цементных изделий успешно применяется высокочастотное упрочнение, после которого поверхностная твердость и стойкость цементного слоя значительно повышаются increased. In кроме того, при упрочнении ТВЧ можно проводить локальный нагрев, и нет необходимости защищать нерабочую поверхность изделия от цементации. Цементирование стали твердым карбюратором является трудоемким и дорогостоящим процессом.
Поэтому его сейчас заменяют на более прогрессивный газоцемент. Газ-цемента Сущность газовой цементации заключается в том, что цементный продукт нагревается в герметичном рабочем пространстве (муфеле) печи, куда цементный газ непрерывно подается на протяжении всего процесса цементации. Для газового цементирования: 1) нет необходимости нагревать угольный порошок, поэтому нагрев продукта происходит гораздо быстрее, чем в случае твердотельного цементирования. 2) сталь насыщается углеродом с повышенной скоростью, поскольку в процессе цементации свежий газ непрерывно подается в рабочее пространство печи.
3) отсутствие потребности транспортировать и хранить коробку порошка и цемента угля. 4) улучшение гигиены труда и так далее. Горизонтальные и вертикальные муфельные располагаются в газ-цементной печи. В серийное производство ГАЗ-цементирование осуществляется в непрерывно действующей конвейерной печи. В настоящее время многие заводы по производству газоцемента используют дешевый природный газ и не перерабатывают (не готовят) его перед вводом в печь для обжига цемента. Природный газ цементируют при 1000°С.
В результате скорость диффузии углерода резко возрастает, а весь процесс цементирования снижается в 900-940 раз по сравнению с традиционным цементированием твердым карбюратором в 2-3 раза. В то же время, увеличьте скорость и химико-термическую обработку стали 52 При диффузии атомы углерода не накапливаются на поверхности изделия. После такой цементации зерно измельчают с использованием двойного отверждения продукта для получения высокой поверхностной твердости. В газовом цементировании может быть выполнена высокоскоростная высокотемпературная цементация.
Например, на Московском автомобильном заводе газоцементная фиксация некоторых деталей осуществляется путем нагрева током высокой частоты 1050-1100°с. При такой температуре цементный слой глубиной около 1 мм получается за 45-50 минут. То есть, по сравнению с обычным газоцементом, процесс цементирования сокращается в 5-6 раз. Впрыск жидкости Цементирование в жидкой среде проводят на глубине не более 0,3-0,4 мм, если необходимо получить цементированный слой, то 840-860°для обработки мелких деталей.
Обычно в жидких ваннах используется от 75% до 80% соды и от 10% до 15% хлорида натрия, а также соляные ванны, содержащие от 8% до 10% порошка карбида кремния или других цементирующих агентов (таких как карбид кальция, чистый Кокс и т. д.). н. Для получения слоя глубиной 0,2-0,3 мм с жидким цементированием требуется выдержка 40-50 минут. Цементный продукт закаливают непосредственно из цементной ванны при охлаждении водой или маслом (в зависимости от марки стали) и выпускают при температуре 160-180°.
Смотрите также:
Материаловедение — решение задач с примерами
Азотирование стали | Отпуск закаленной стали |
Цианирование стали | Поверхностная закалка стали |