Оглавление:
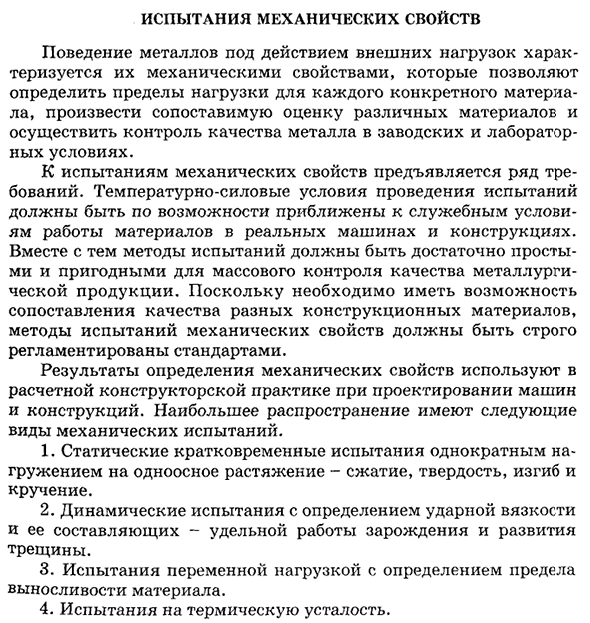

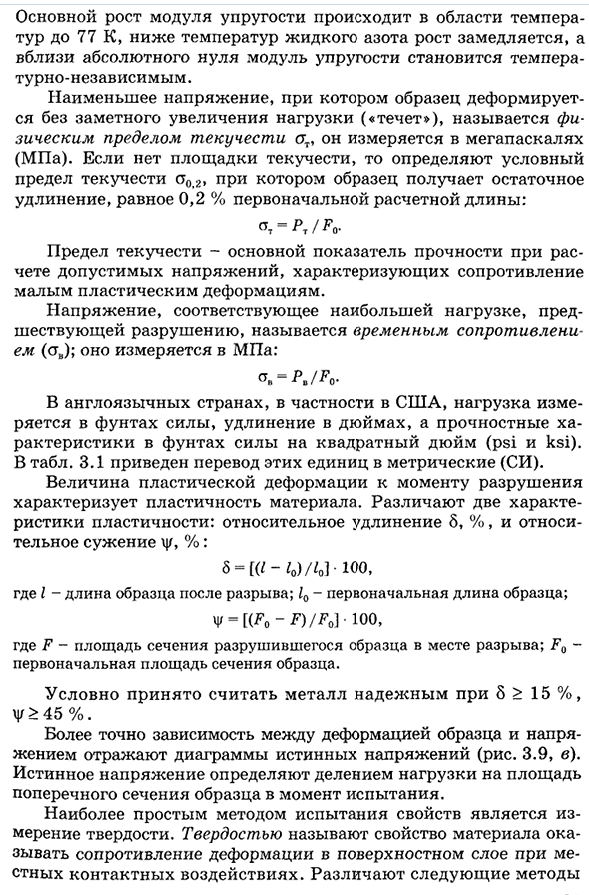
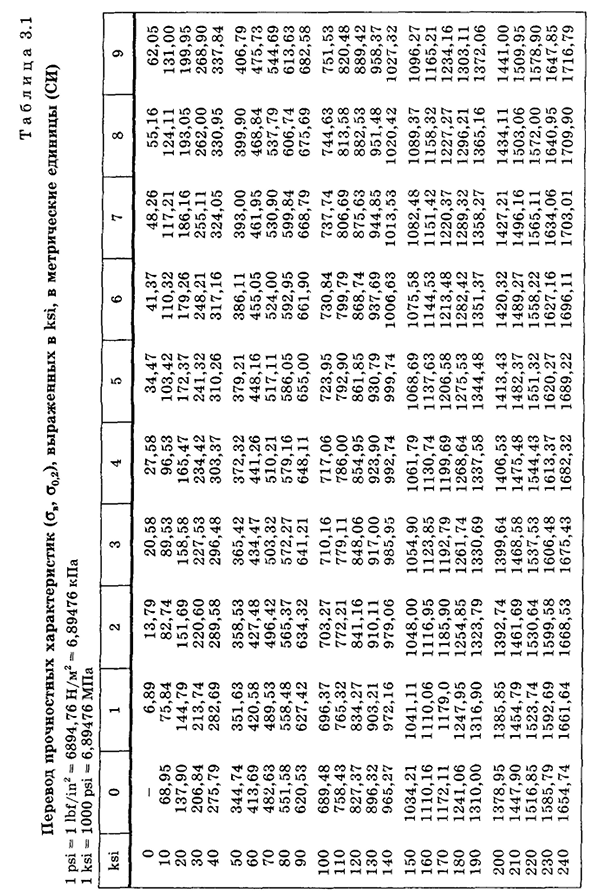
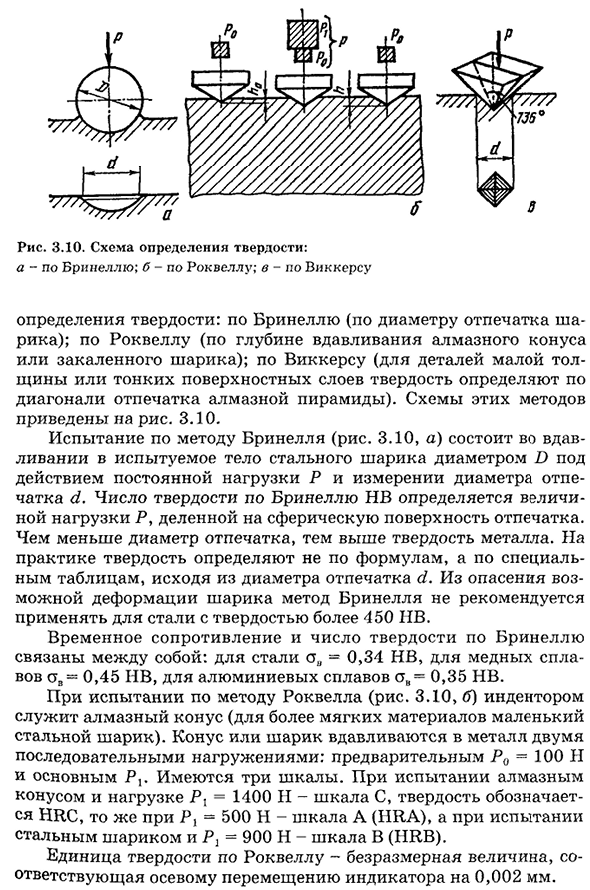
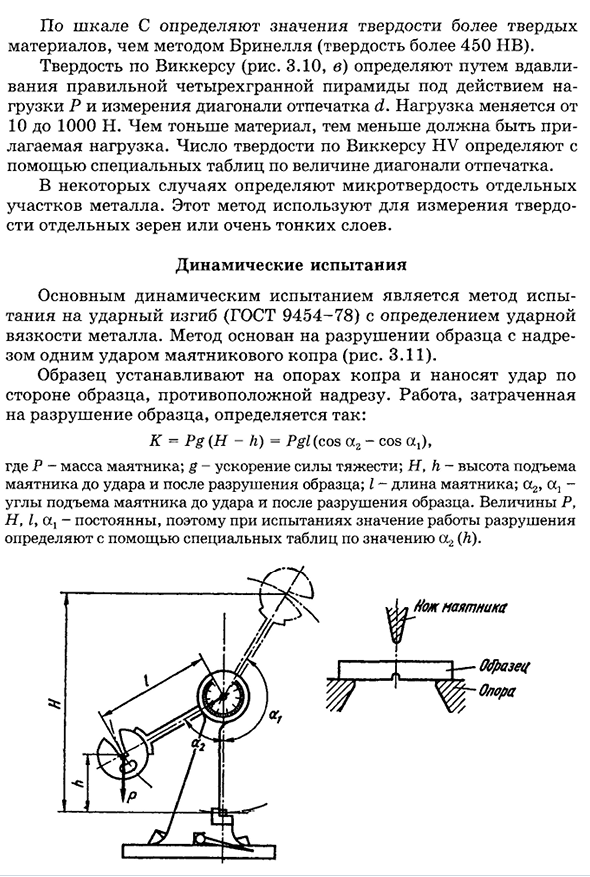
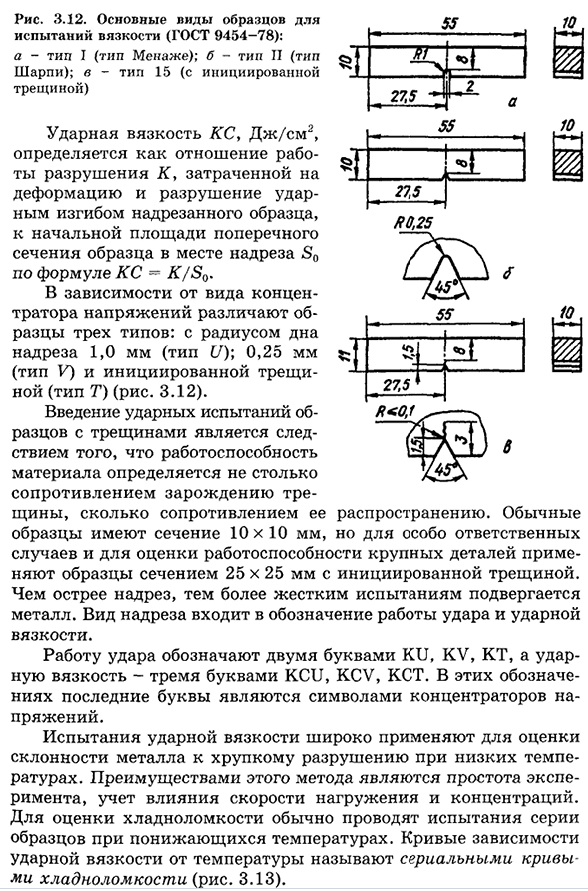
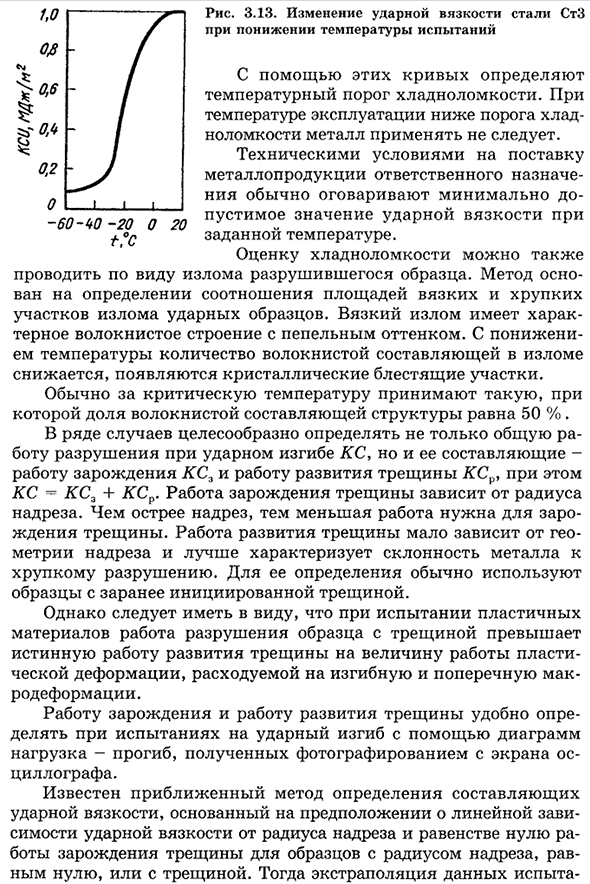


Испытания механических свойств
- Испытание механических свойств Поведение металлов при внешних нагрузках определяет пределы нагрузки каждого конкретного материала, выполняет эквивалентную оценку различных материалов и отвечает за работоспособность металлов в заводских и лабораторных условиях. Существует несколько условий для проверки механических свойств. Состояние температуры и силы испытания должно быть как можно ближе к состоянию обслуживания реальных машины и конструкционных материалов. Однако метод испытаний достаточно прост и должен быть пригоден для массового контроля качества металлургической продукции.
Метод испытания механических свойств должен быть строго регламентирован стандартами, так как необходимо уметь сравнивать качества различных конструкционных материалов. Результаты определения механических свойств используются в конструкторской практике при проектировании машин и конструкций. Наиболее распространенными являются следующие виды механических испытаний: 1. Статическое недолгосрочное испытание одиночн-нагрузки для одноосных растяжимых обжатия, твердости, гнуть и кручения. 2. Динамические испытания ударной вязкости определение и развитие трещиностойкости компонентов конкретных задач. 3.
Испытание на переменную нагрузку при определении предела выносливости материала. 4. Людмила Фирмаль
Термическое испытание на усталость. 795 ползучесть и длительный тест на прочность. 6. Испытание устойчивости к развитию трещин путем определения параметров трещиностойкости. 7. Натурные испытания материалов, деталей, узлов и готовых конструкций в условиях сложных напряжений. Статические испытания чаще всего проводят в условиях испытания на растяжение(ГОСТ1497-84). Обычно используется небольшой пятикратный образец круглого сечения (диаметр 5 мм, расчетная длина 25 мм).
Для риса. 3.9 приведены два типа диаграмм растяжения: нагрузка p, с точкой текучести или без нее-расширенные координаты AZ. Фигура просто преобразуется в фигуру с координатным напряжением o-относительной деформацией 8. В то же время, o=P / Fo;8=(i\l/10)■100%, где Fo, 10-первый участок и длина образца перед испытанием. Диаграмма растяжения состоит из упругой деформации OA, равномерной пластической деформации AB и концентрированной деформации шейки BC. Область упругой деформации имеет линейный вид и характеризует жесткость материала. Чем меньше упругая деформация материала подвергается нагрузке, тем выше его жесткость и характеризуется модуль упругости: е= = о / 8. Модуль упругости-это структурно нечувствительное свойство, которое определяется силой атомного взаимодействия-константой материала. Упругие свойства зависят от температуры металла. С уменьшением температуры межатомное расстояние уменьшается, кристаллы сжимаются, а модуль упругости увеличивается.
- Рис 3.9. Диаграмма растяжения: а-доходность колодки…;Б-без площадки текучести; с-истинное напряжение график 80-базовый рост модуля упругости происходит в интервале температур до 77 К ниже температуры роста жидкого азота, вблизи абсолютного нуля модуль упругости становится температурно независимым. Минимальное напряжение («текучее»), при котором образец деформируется без заметного увеличения нагрузки, называется физическим пределом текучести Sgt и измеряется в МПА. При отсутствии предела текучести определяют условный предел текучести O2, при котором образец будет подвергаться остаточному удлинению, равному 0,2% от первоначальной расчетной длины: СЧ=РТ/Р0. Предел текучести является основным показателем прочности при расчете допустимого напряжения, характеризующего устойчивость к малым пластическим деформациям. Напряжение, соответствующее наибольшей нагрузке до отказа, называется временным сопротивлением
(СТВ) и измеряется в Мпа: ов=Р»/Р0. В англоязычных странах, особенно в Соединенных Штатах, нагрузка измеряется в фунтах силы, удлинение в дюймах и прочностные характеристики в фунтах/квадратных дюймах (psi и ksi) силы. За столом. 3.1 преобразуйте эти единицы измерения в Метрику (Си). Величина пластической деформации при разрушении характеризует пластичность материала. Есть две особенности пластика: удлинение 8,% и относительная усадка: 8 = [ ( /- /» ) /kl100, Где I-длина образца после разрыва, а 10-исходная длина образца; В=[(П О-П)/Л? о] Лу, Здесь F-площадь поперечного сечения разрушенного образца в месте разрушения, Fo-начальная площадь поперечного сечения образца. Условно считается, что металл надежен при 8>15%, а V>45%.
Точнее, зависимость между деформацией образца и напряжением отражает истинную диаграмму напряжений. 3.9, в). Людмила Фирмаль
Истинное напряжение определяется путем деления нагрузки на площадь поперечного сечения образца во время испытания. Самый простой способ проверить проницаемость-это измерение твердости. Твердость-это свойство материала, которое сопротивляется деформации поверхностного слоя под воздействием локального контакта. Существуют следующие методы Определение твердости: Brinell (диаметр отпечатка шарика); Rockwell (глубина вдавливания конуса Диаманта или затвердетого шарика); Vickers(твердость малая толщина или тонкий поверхностный слой этих методов) диаграммы. 3.10 Тест бринелла(рис. 3.10, а) состоит из надавливания на испытательный корпус стального шарика диаметром D под действием постоянной нагрузки Р и измерения диаметра штампованного d. Чем меньше диаметр отпечатка, тем выше твердость металла.
Из-за боязни деформации шарика, метод Бринелла не рекомендуется для сталей с твердостью более 450НВ. Сопротивление времени и чисел твердости по Бринеллю связаны между собой: для стали=0.34 НВ, для алюминиевых сплавов, медных сплавов АВ=0.45 НВ, ов=0.35 НВ. Тест Роквелла (рис. 3.10, б)индентор представляет собой алмазный конус (для небольшого стального шарика для более мягких материалов). Есть три шкалы, резерв Ro=100N и ключ PP. Испытанный с конусом Диаманта и нагрузкой P, твердость = 1400n-маштаба C показана HRC, и этим же для PJ=500N-маштаба A (HRA), тогда твердость стального шарика показана HRC. Блок твердости Роквелла представляет собой безразмерное значение, соответствующее осевому перемещению индикатора на 0,002 мм. Восемьдесят три. Шкала IPO C определяет твердость материала жестче, чем метод Бринелла(твердость более 450 НВ).
Твердость по Виккерсу (рис. 3.10, в) определяется путем прессования пирамид тетраэдра под нагрузкой Р и измерения диагонали отпечатка d. число виккера твердости HV, нагрузка которого изменяется от 10 до 1000 Н, определяется с помощью специальной таблицы по величине диагонали отпечатка. В некоторых случаях определяют микротвердость отдельных частей металла. Этот метод используется для измерения твердости отдельных частиц или очень тонких слоев. Динамические испытания основным динамическим испытанием является метод испытаний на ударный изгиб (ГОСТ9454-78) при определении ударной вязкости металлов. Этот метод называется маятниковой копрой(рис. 3.11). Образец устанавливается на опоре копры и пробивается сбоку от несходного образца в разрезе. Работа, затраченная на разрушение образца, определяется как: K=Pg(H-h)=Pgl(cos ot2-cos cq), где
P-масса маятника; g-ускорение свободного падения; H, h-высота маятника до удара и после разрушения образца и величина P, H, I, Sch постоянна, поэтому при испытании величины разрывной работы с помощью специальной таблицы (A2) она будет определяться следующим образом. Рис 3.11. Схема испытания на ударную прочность Основной тип образца для испытания на вязкость Iris 3.02 (ГОСТ9454-78): A тип I (тип Менажа); b тип II (тип Шарпи); C тип 15 (начальная трещина).) Ударная вязкость КС, Дж / см2, так как отношение работы разрушения к затрачивается на деформацию и разрушение при ударном изгибе разрезаемого образца, то рассчитывается отношение начальной площади поперечного сечения образца в месте разреза.
1,0 мм (Тип u) −0,25 мм (Тип V) и имеет радиус дна разреза открывающейся трещины (тип T). 3.12). Введение ударных испытаний образцов с трещинами является следствием того, что эксплуатационные характеристики материала не так определены Р0 25 Пятьдесят пять. Устойчивость к растрескиванию, а также к его распространению. Обычные образцы имеют поперечное сечение 10 × 10 мм, но для особо важных случаев используют образец с поперечным сечением 25×25 мм стартовой трещины. Чем острее надрезы, тем тверже тестируется металл. Тип разреза входит в обозначение ударной и ударной работы.
Результативность работы показывает две буквы КУ, КВ, КТ, и выносливость-три буквы КХУ, «КУСИКРЕАВИЖН», КСТ. В этих спецификациях последняя буква является символом редуктора напряжения. Испытания на вязкость широко используются для оценки восприимчивости металлов к хрупкому разрушению при низких температурах. Преимуществом данного метода является простота эксперимента, учитывающая влияние скорости нагрузки и концентрации. Для оценки холодных трещин обычно проводят испытания серии образцов при низких температурах. Температурно-зависимая кривая вязкости называется непрерывной кривой холодного разрушения(рис. 3.13). 85es Рис 3.13 снижение температуры испытания сталь СТЗ изменение ударной вязкости С помощью этих кривых определяется температурный порог холодного разрушения. Он не должен использоваться при рабочих температурах ниже порога холодного разрушения металла.
Технические условия на поставку металлических изделий ответственного назначения обычно предусматривают минимально допустимые значения ударной вязкости при определенных температурах. Оценки холодного разрушения также могут быть выполнены в зависимости от типа разрушения в разрушенном образце. Метод основан на определении соотношения площадей участков вязкого и хрупкого разрушения ударного образца. Вязкое разрушение имеет характерную волокнистую структуру с серым оттенком. С понижением температуры количество волокнистых компонентов в трещине уменьшается, и появляется кристаллическая глянцевая область. Обычно критическую температуру принимают таким образом, чтобы доля волокнистого компонента в структуре составляла 50%.
В ряде случаев целесообразно не только определять суммарную работу трещин при ударно-изгибном копировании, но и работу составляющих ее трещин происхождение трещины зависит от радиуса разреза. Если надрез сделать более остро, то работы, требующейся при возникновении трещины, будет меньше. Задача развития трещин практически не зависит от геометрии разреза, что лучше характеризует склонность металла к хрупкому разрушению. Для его определения обычно используют образцы с предварительно инициированными трещинами. Однако в случае испытания пластических материалов следует учитывать, что работа разрушения образца с трещиной превышает истинную работу образования трещины вследствие пластической деформации вследствие изгибной деформации и поперечной деформации.
Когда испытание на изгиб удара унесено используя диаграмму нагрузк-отклонения принятую от экрана осциллографа, работа начала и работа прогресса отказа удобны. Известен приближенный метод определения составляющих ударной вязкости, предполагающий линейную зависимость ударной вязкости от радиуса разреза и нулевую работу зарождения трещины для образца с нулевым или нулевым радиусом разреза. Тогда экстраполяция данных будет испытана- Только два типа образцов 86nii с радиусом 1 и 0,25 мм с нулевым значением радиуса разреза дают величину работы инициирования трещины. Определение составляющих ударной вязкости позволяет выявить влияние различных факторов на обе фазы разрушения.
Смотрите также:
Методические указания по материаловедению
Испытания долговечности | Наклеп и рекристаллизация |
Предмет материаловедения; современная классификация материалов, основные этапы развития материаловедения | Металлографические методы испытаний |