Оглавление:
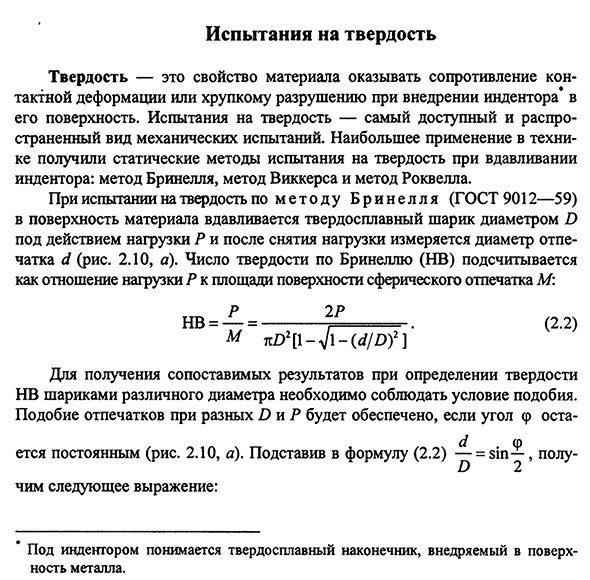

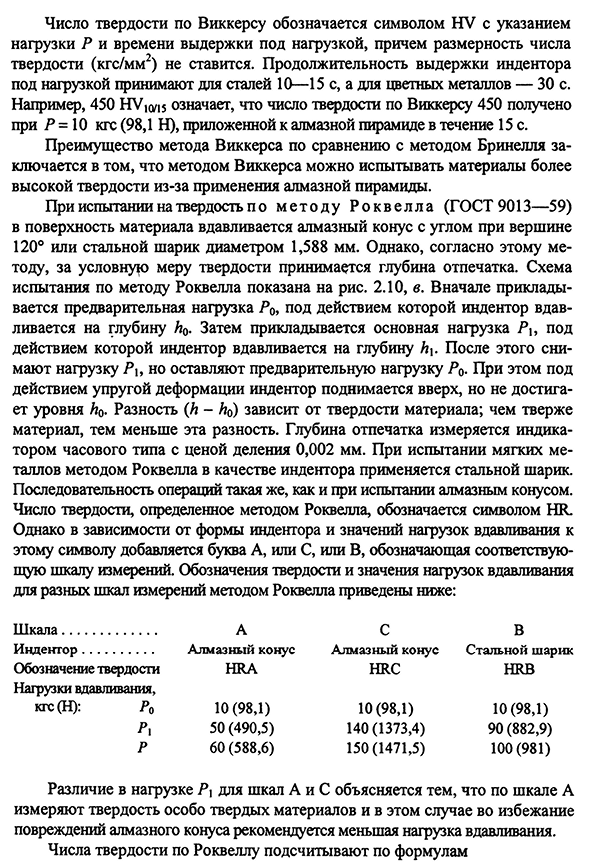
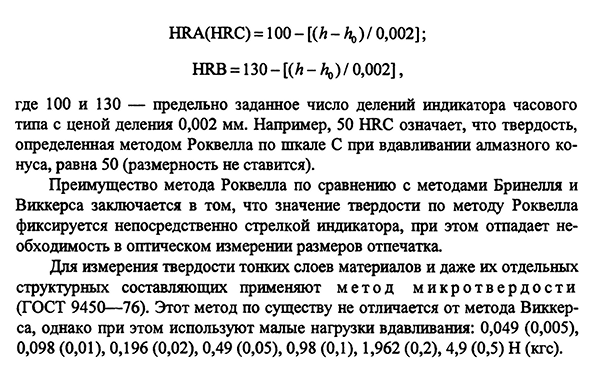

Испытания на твердость
- Испытание на твердость Твердость-это свойство материала, которое сопротивляется контактной деформации или хрупкому разрушению, когда индентор вставляется в его поверхность. Определение твердости является наиболее доступным и распространенным видом механических испытаний. Наибольшее применение этот метод получил статический метод определения твердости вдавливания: метод Бринелла, метод Виккерса и метод Роквелла. * Индентор отмечает карбидные наконечники, встроенные в металлическую поверхность. При испытаниях на твердость по М ето д у б р и н е л ь я (гост9012—59)твердосплавные шарики диаметром D и нагрузкой 2.10, а) под действием нагрузки Р. число твердости по Бринеллю(НВ) рассчитывается как отношение нагрузки Р К площади поверхности сферического отпечатка м\ (2.2)
Необходимо соблюдать условие подобия, чтобы получить результат, сравнимый с получением твердости шарика HB разного диаметра. Если угол f остается постоянным, то обеспечивается сходство отпечатков в разных DUP P (рис. 2.10 а). Подставим выражение(2.2) — ^-=sin -,. Чим следующее выражение: Триста семьдесят два •(23) п П\ В R есть. 2.10 механизм определения твердости: а-Бринелл; б-Викерс; к-Роквелл Из Формулы (2.3) следует, что если P/D1=const и f=const, то значение HB остается постоянным. Выбор соотношения p / B2, а следовательно и толкающей нагрузки P зависит от уровня твердости материала. Чем тверже материал, тем больше рекомендуется соотношение P / D2. Исходя из этого, ГОСТ 9012-59 показывает твердость Р/Д2 в соотношении (МПа) 294 (сталь, чугун, высокопрочные сплавы), 98 (алюминий, медь, никель и их сплавы), 49 (магний и его сплавы), 24,5 (медведь Р>=10 мм,
время выдержки при р=29400 Н (Р/=294мпа) и 10С блинелевой твердости. он обозначается символом HB. Людмила Фирмаль
В этом случае размеры (кгс/мм2) не закладываются, а, например, 200НВ. При использовании шариков других диаметров (1,2, 2,5 и 5 мм) толкающая нагрузка изменяется, а символ твердости HB дополняется тремя индикаторами. Например, 180HB2, 5/187, 5/zo,£> = 2,5 мм, 187,5 кгс (1839N) и время выдержки 30 секунд под нагрузкой, указывающее, что число Бринелля твердости составляет 180. Метод Бринелла не рекомендуется для материалов с твердостью более 450NV, так как стальные шарики могут значительно деформироваться. На поверхность материала (ГОСТ29999-75) и на ЭП напрессована Алмазная тетраэдрическая пирамида с углом в вершине M eto du B и K=136 около 2.10, b). После снятия нагрузки отступа измеряются диагонали печати DX.
Число твердости Виккерса HV рассчитывается как отношение нагрузки P к площади поверхности отпечатка пирамиды m: 2р в S-2 df =»854″ — 38 номер твердости по Виккерсу обозначается символом HV, который указывает нагрузку P и время выдержки под нагрузкой, а размер номера твердости (кгс/мм2) не включается. Время выдержки индентора под нагрузкой допустимо в стали 10-15 секунд, а в цветных металлах 30 секунд. Например, 450HV10 / i5 означает, что число твердости Виккерса 450 наносится на алмазную пирамиду в течение 15 секунд при p=10kgf(98,1 Н). Преимущество метода Виккерса перед методом Бринелла состоит в том, что метод Виккерса позволяет проверить материал с более высокой твердостью с помощью алмазной пирамиды.
- При испытаниях на твердость по М етоду у р О К В Л А (ГОСТ9013-59) стальной шарик с алмазным конусом с углом наклона выше 120°или диаметром 1,588 мм. Метод испытания по Роквеллу показан на рисунке. 2.10 В. Сначала прикладывается резервная нагрузка Ро, под ее действием индентор прижимается на глубину y0. Затем основная нагрузка прикладывается под действием индентора, прижатого к глубине y, нагрузка P снимается, но резервная нагрузка ro остается-в то же время под действием упругой деформации разность давлений (y-y0) определяется твердостью материала; чем тверже материал, тем меньше разность давлений. Глубина отпечатка измеряется индикатором часового типа с ценой деления 0,002 мм. Порядок работы такой же, как и при испытании алмазного конуса. Число твердости, определенное методом Роквелла, обозначается символом HR.
Однако в зависимости от формы индентора и величины толкающей нагрузки к этому символу добавляется буква A, или C, или B, указывающая соответствующую шкалу измерения. Твердость шкалы Роквелла с различным значением нагрузки на вдавливание показана ниже: Я не уверен, что сделаю это снова……………………. И с Индентором……………….. Алмазный конус алмазный конус стальной шарик спецификации ЗПЧ твердость НRС рекуперативных отступ нагрузка, кгс (Н): Ro10(98,1) 10(98,1) 10(98,1) Л50(490,5) 140(1373,4) 90 (882,9) P60(588,6) 150(1471,5) 100 (981) Разница между нагрузкой P масштаба A и C заключается в том, что твердость особо твердых материалов измеряется в масштабе A, и в этом случае измеряется меньший материал, чтобы избежать повреждения алмазного конуса. Число твердости Роквелла вычисляется по формуле 39HRA(HRC)=100 — [(y-L)/0.002];HRB = 130-[(L-aq)/0.002] (где 100 и 130-максимальное заданное число
расщеплений индикатора типа time с ценой расщепления 0.002 мм. Людмила Фирмаль
Преимущество метода Роквелла по сравнению с методами Бринелла и Виккерса заключается в том, что значение твердости Роквелла фиксируется непосредственно стрелкой индикатора, что позволяет уменьшить размер печати. Для измерения твердости тонкого слоя материала, а тем более их отдельных конструктивных частей применяют м е т о д М и К Р О Т В Е Д О С Т и(ГОСТ9450-76). Этот метод в основном такой же, как метод Виккерса, но использует небольшую нагрузку отступа: 0,049 (0,005), 0,098 (0,01), 0,196 (0,02), 0,49 (0,05), 0,98 (0,1), 1,962 (0,2), 4,9 (0,5) N (кгс).
Смотрите также:
Методические указания по материаловедению
Испытания на трещиностойкость | Механические свойства и классификация методов механических испытаний материалов |
Испытания на ударную вязкость | Испытания на растяжение |