Оглавление:
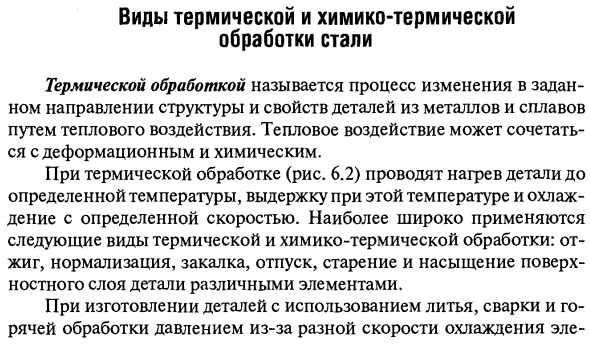
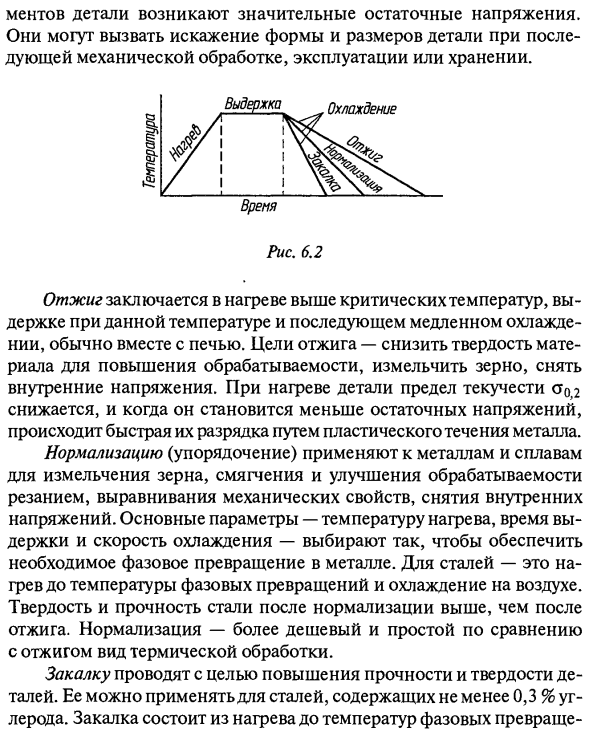
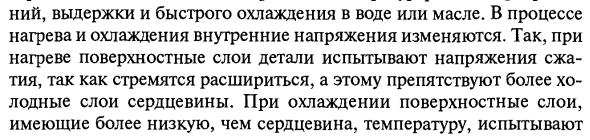
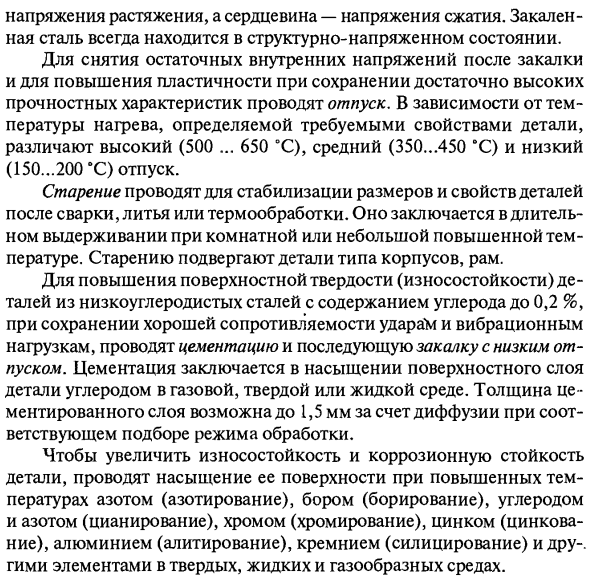

Виды термической и химико-термической обработки стали
- Виды термообработки и химической термообработки стали Термическая обработка — это процесс, при котором структура и характеристики детали, изготовленной из металла или сплава, изменяются в заданном направлении под действием тепла. Термическое воздействие может сочетаться с деформацией и химическими веществами. Во время термообработки (рис. 6.2) деталь нагревается до определенной температуры, выдерживается при этой температуре и охлаждается с определенной скоростью.
Изготовление деталей с использованием литья, сварки и горячего формования вызывает значительные остаточные напряжения из-за различных скоростей охлаждения компонентов. Они могут вызвать искажение формы и размера детали при последующей обработке, эксплуатации или хранении. Охлаждение экспозиции время Рисунок 6.2
Наиболее широко используются следующие виды термообработки и химической термообработки: отжиг, нормализация, отверждение, отпуск, старение и насыщение поверхностного слоя деталей, содержащих различные элементы. Людмила Фирмаль
Отжиг обычно состоит из нагрева вместе с печью выше критической температуры, выдерживания ее при определенной температуре и последующего медленного охлаждения. Целью отжига является снижение твердости материала для улучшения обрабатываемости, дробления зерна и снятия внутренних напряжений. Когда деталь нагревают, предел текучести g0> 2 уменьшается, а когда он становится меньше остаточного напряжения, он быстро разряжается из-за пластического течения металла. Нормализация (секвенирование) применяется к металлам и сплавам для измельчения, регулировки механических свойств, смягчения и улучшения обрабатываемости за счет снятия внутренних напряжений.
Основные параметры — температура нагрева, время выдержки и скорость охлаждения — выбираются так, чтобы обеспечить необходимый фазовый переход для металла. В случае стали ее нагревают до температуры фазового перехода и охлаждают на воздухе. После нормализации твердость и прочность стали будут выше, чем после отжига. Нормализация является более дешевым и простым видом термообработки, чем отжиг. Отверждение делается для увеличения прочности и твердости детали. Может использоваться для сталей, содержащих не менее 0,3% углерода. Закалка состоит из нагрева до температуры фазового перехода
- Воздействие воды или масла, охлаждение и быстрое охлаждение. Во время нагревания и охлаждения внутреннее напряжение изменяется. В результате при нагревании поверхностный слой компонента имеет тенденцию к расширению и, следовательно, подвергается сжимающему напряжению, которое предотвращается более холодным слоем сердечника. Охлаждение дает поверхностный слой, который холоднее, чем основной слой Растягивающее напряжение и напряжение сжатия сердечника.
Каникулы применяются для снятия остаточных внутренних напряжений после отверждения и повышения пластичности при сохранении достаточно высоких прочностных свойств. В зависимости от температуры нагрева, определяемой требуемыми свойствами детали, закаливаются высокая температура (500-650 ° С), средняя (350-450 ° С) и низкая температура (150-200 ° С). Выдержка производится для стабилизации размеров и характеристик деталей после сварки, литья и термообработки.
Закаленная сталь всегда структурно напряжена. Людмила Фирмаль
Он состоит из длительного пребывания в помещении или немного более высокой температуры. На это влияет старение, износ корпусов и рам. Соединяется и затвердевает при низком отпуске, одновременно повышая твердость поверхности (износостойкость) деталей из низкоуглеродистой стали с максимальным содержанием углерода 0,2% и сохраняя хорошую стойкость к ударным и вибрационным нагрузкам. Цементация — это насыщение поверхностного слоя детали углеродом в газовой, твердой или жидкой среде. Толщина цементного слоя может составлять до 1,5 мм путем диффузии с соответствующим выбором режима обработки.
Чтобы повысить износостойкость и коррозионную стойкость деталей, поверхность нагревают при высоких температурах с помощью азота (азотирование), бора (боратирование), углерода и азота (цианирование), хрома (хромирование), цинка (цинкование), (Насыщает алюминий (алюминизированный), кремний (силиконизированный)) и другие. Элементы твердых, жидких и газообразных сред.
Смотрите также:
Решение задач по прикладной механике
Пластмассы | Разъемные соединения |
Смазочные материалы | Резьбовые соединения |