Оглавление:
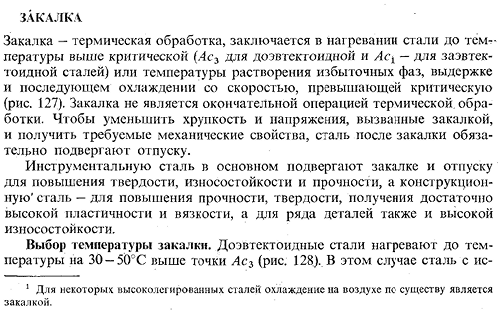
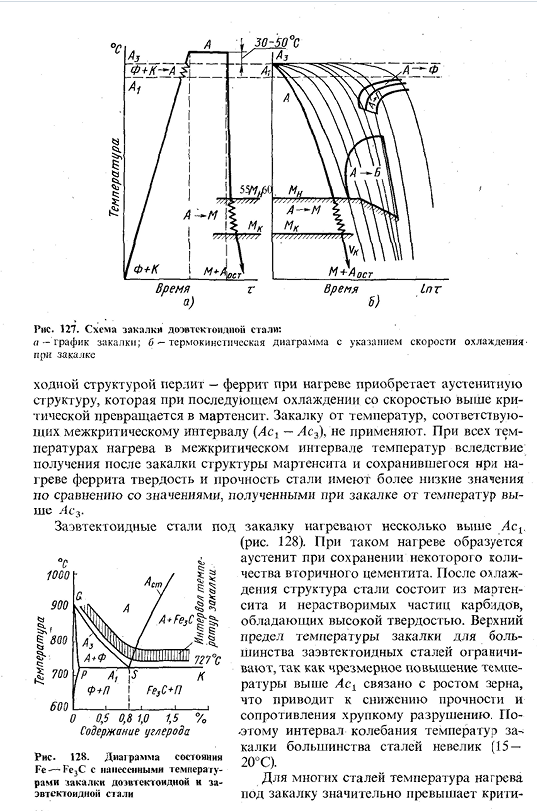
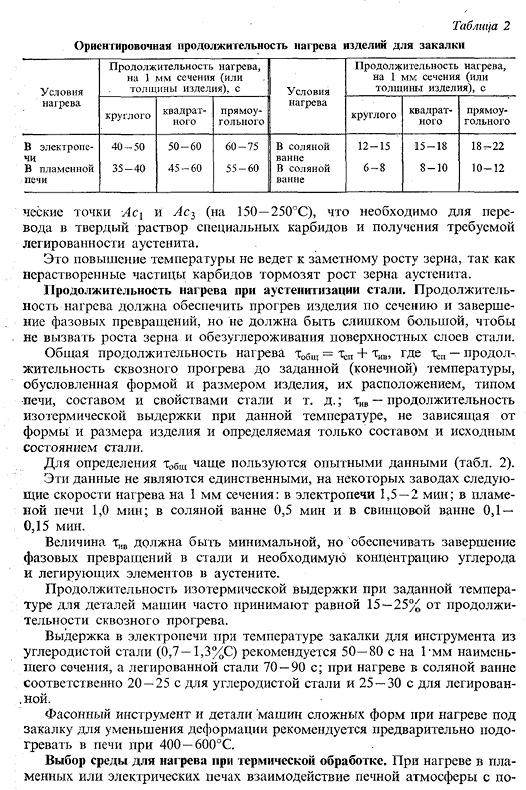
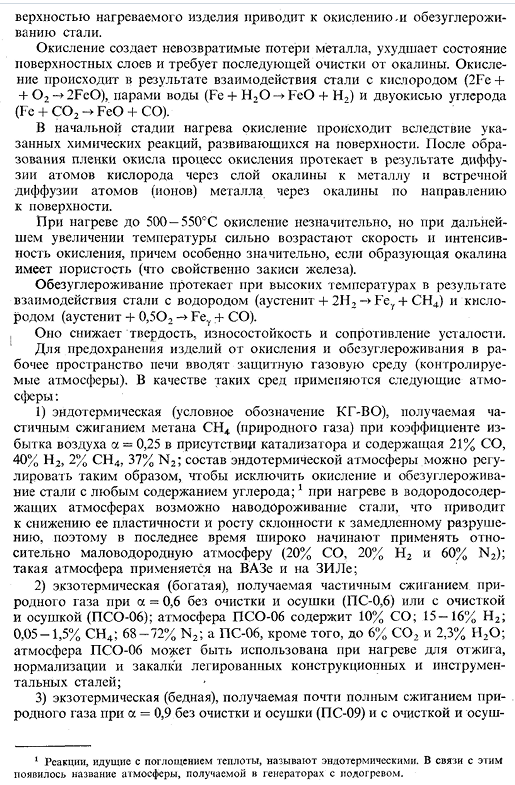
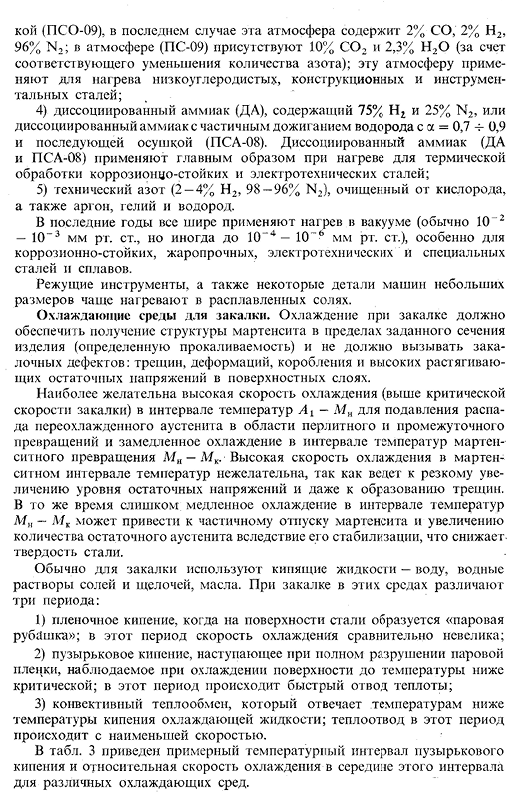
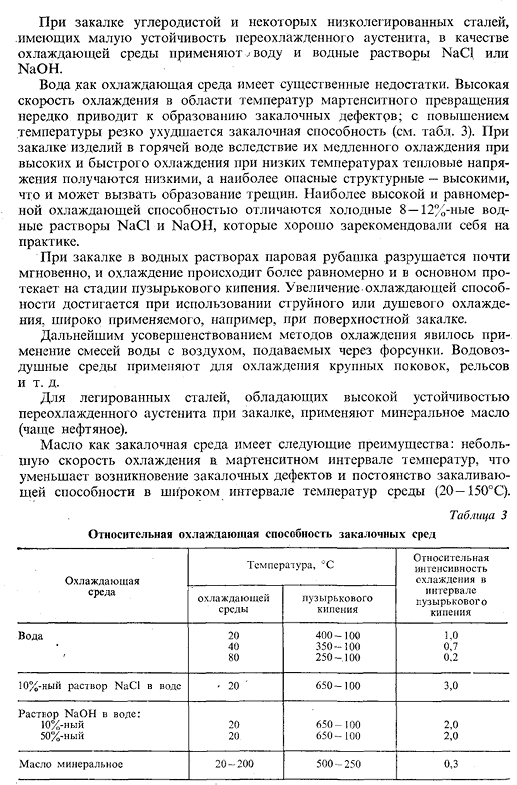
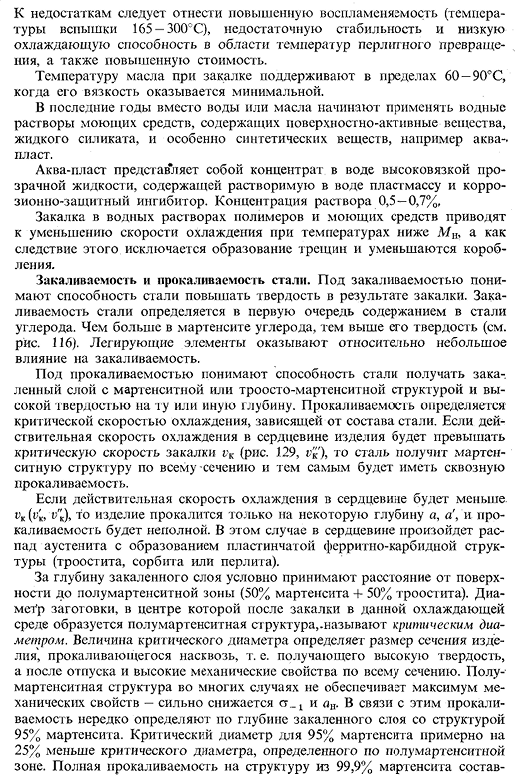
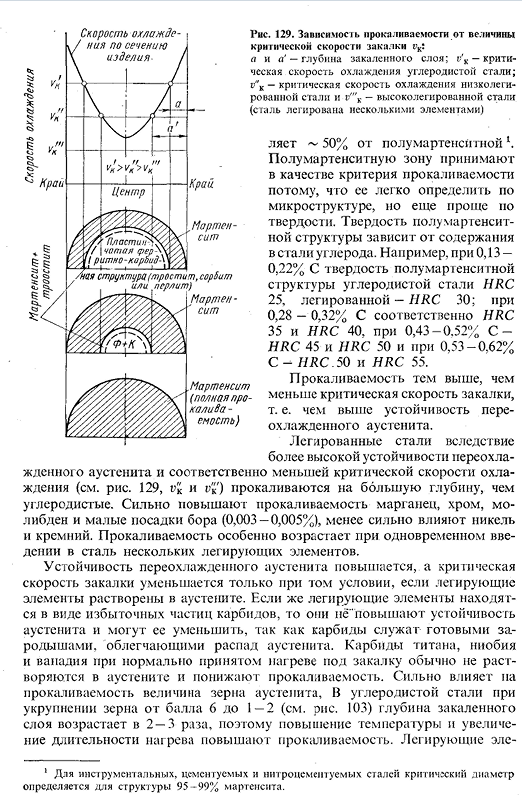
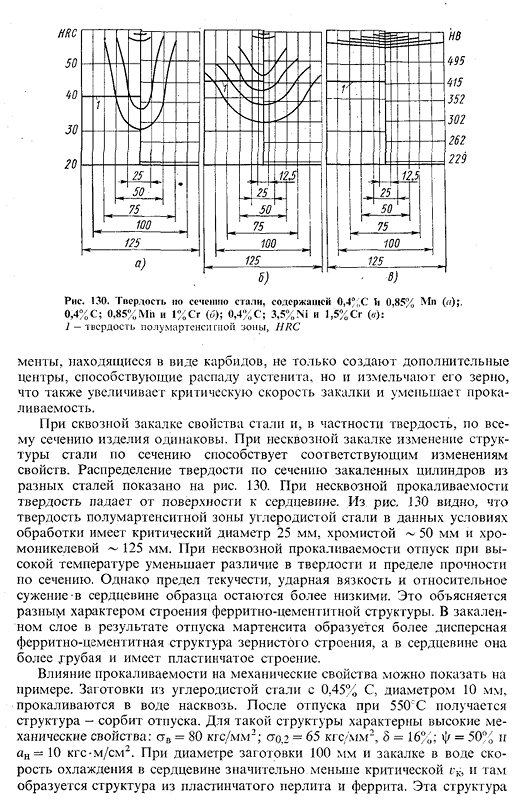
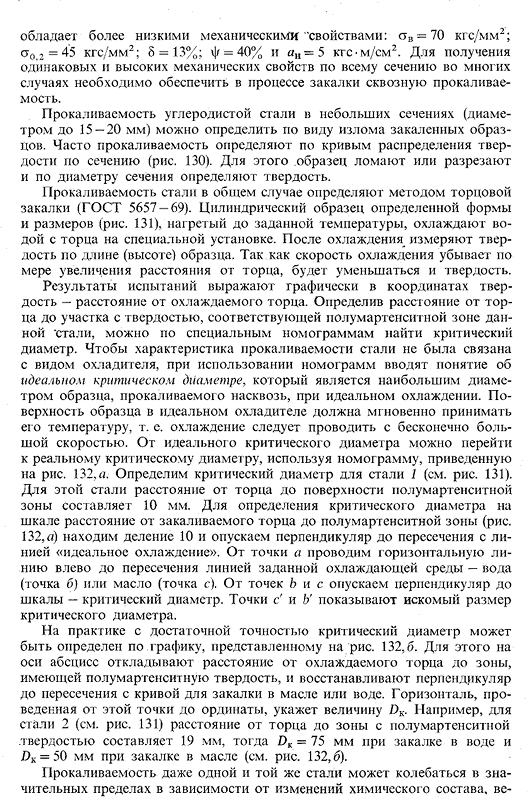
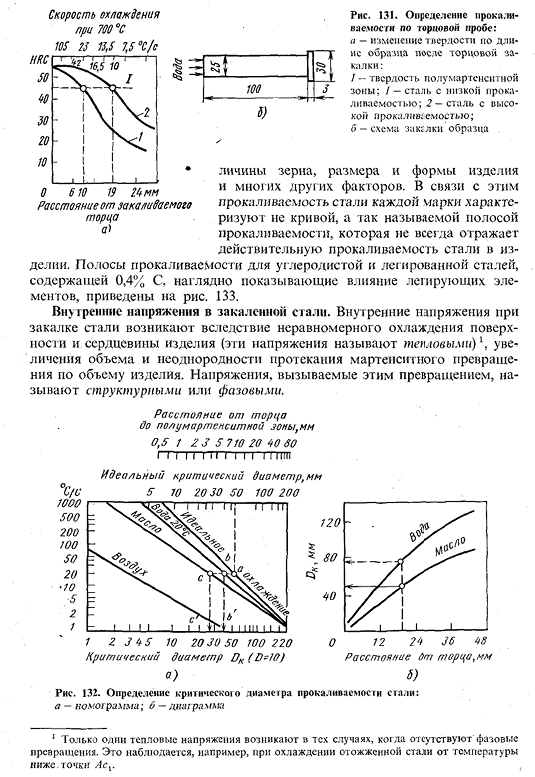
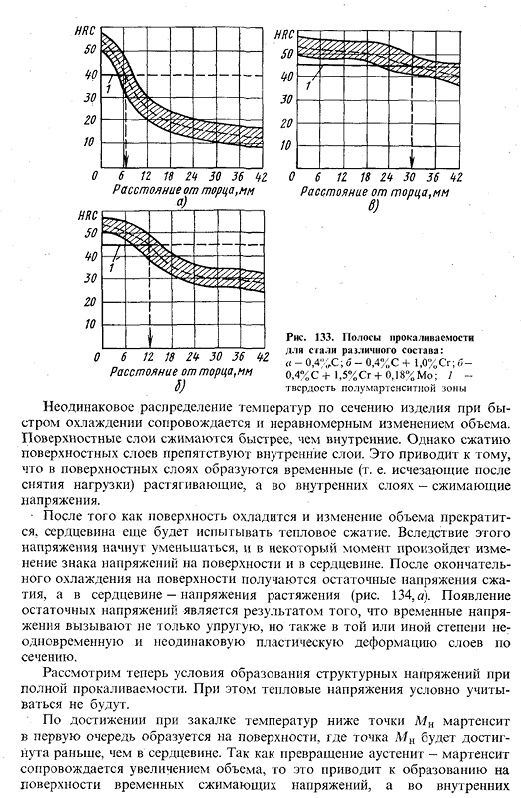
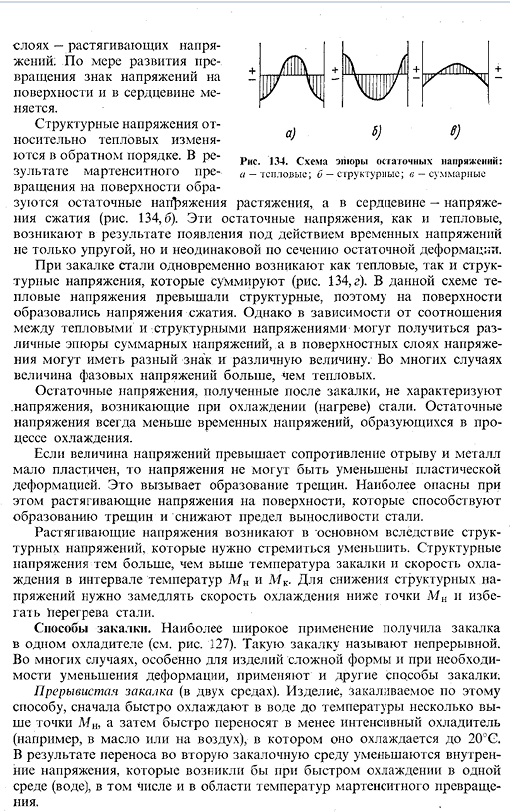

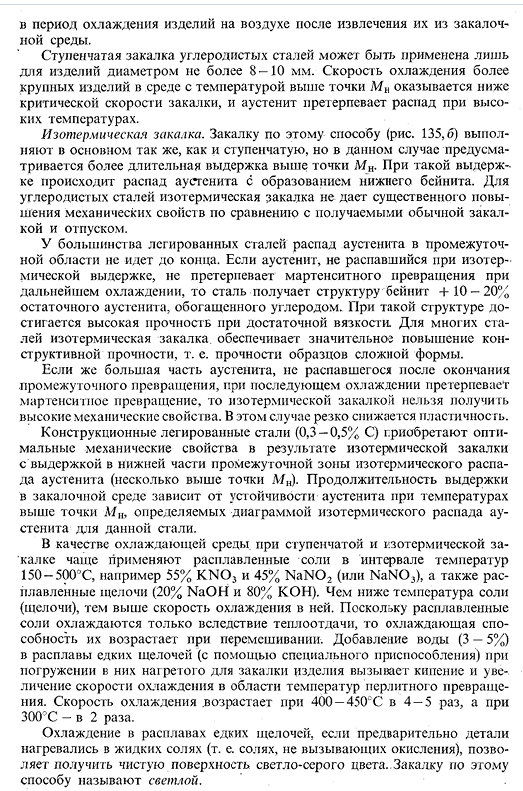
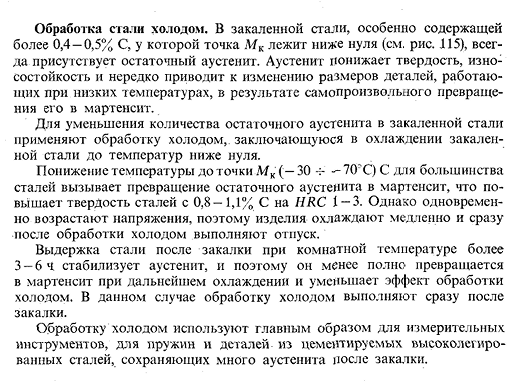

Закалка
- Гашение Закалка — это термическая обработка, состоящая из нагрева стали до температуры выше критической (Ac3 для случая Суперэвтектоидной стали, Ac ^для случая Суперэвтектоидной стали) или температуры растворения избыточной фазы, выдерживания ее со скоростью, превышающей критическое значение, и последующего охлаждения (рис.127).
Тушение не является конечной задачей тепла treatment. In для того чтобы уменьшить хрупкость и напряжения, вызванные закалкой и получить необходимые механические свойства, сталь после закалки обязательно закаляют. Инструментальная сталь в основном подвергается закалке, отпуску для повышения твердости, износостойкости и прочности, но конструкционная сталь используется для повышения прочности, твердости и получения достаточно высокой пластичности и ударной вязкости, а многие детали также имеют высокую износостойкость.
Выбор температуры отверждения. Людмила Фирмаль
Субдуцированная сталь нагревается до температуры выше Ac3 на 30-50°C (рис. 128). в этом случае сталь 197! Рисунок 127.Схема закаливания супер-эвтектоидная сталь: — Улучшенное расписание. b-термодинамическая диаграмма, показывающая скорость охлаждения при быстром охлаждении Около 0.5 0.8 1.0 1.5% Содержание углерода Перлит-ферритовая структура тока приобретает аустенитную структуру при нагревании, а затем охлаждается со скоростью, превышающей критическое значение, в результате чего martensite. No используется отверждение от температур, соответствующих критическому интервалу (Xcj-Ac3).
Из-за мартенситной структуры, полученной после закалки при всех температурах нагрева в пределах критического температурного диапазона, и феррита, сохраненного в неотапливаемых условиях, твердость и прочность стали ниже, чем при закалке при температурах выше Ac3. Закалку нагревают несколько выше, чем а(рис. 128).Такой нагрев создает аустенит при сохранении определенного количества вторичного цементита. После охлаждать, стальная структура составлена мартенсита и неразрешимых частиц карбида с высокой твердостью.
- Верхний предел температуры закалки для большинства суперэвтектоидных сталей ограничен. Это связано с тем, что чрезмерное повышение температуры выше Ac3 связано с ростом зерна и приводит к снижению прочности и стойкости к хрупкому разрушению. Поэтому диапазон температур закалки большинства сталей невелик (15-20°С). Во многих сталях температура отпуска значительно превышает критическую температуру. Переохлажденная сталь °С je. 1000. 900. Ф§ 800 1,700. 600. Рисунок 128.Диаграмма состояния системы Fe-Fe3C с нанесенными закалочной температуры заэвтектоидного Н-эвтектоидная сталь 198 расчетный период нагрева изделий для отверждения Таблица 2 Условия Время нагрева, 1 мм на секцию (или толщину изделия), с Время нагрева, 1 мм на секцию (или толщину изделия), с Отопление круглое квадратное Прямоугольный Отопление круглое квадратное Прямоугольный Электрические печи огонь печи 40-50. 35-40. 50-60 45, 60. От 60 до 75. От 55 до 60.
В соляных ваннах в соляных ваннах 12-15. 6-8. 15-18 8-10. 18-22 10-12. Точки Tci и Ac3(150-250 ° С).Это необходимо для того, чтобы перевести специальные карбиды в твердые растворы и получить необходимые аустенитные сплавы. Поскольку нерастворенные частицы карбида ингибируют рост зерен аустенита, это повышение температуры не приводит к значительному увеличению зерен. Время нагрева при аустенитизации стали. Время нагрева должно обеспечивать завершение всего поперечного разогрева и фазового превращения изделия, но не должно быть слишком длительным, чтобы не вызвать рост зерен и обезуглероживание поверхностного слоя стали. Общее время нагрева составляет to6sh = tsp + tiv. Здесь ТСП — это время нагрева до определенной (конечной) температуры, обусловленное формой и размерами изделия, расположением изделия, типом печи, составом и свойствами стали и др. тив — это период изотермической выдержки при определенной температуре, который определяется только составом и начальным
состоянием стали, независимо от формы и размеров изделия. Людмила Фирмаль
Для определения суммы чаще используются экспериментальные данные (табл.2). Не только эти данные, но и в некоторых установках существует следующая скорость нагрева на 1 мм сечение.1,5-2 минуты в электропечи. Пламя духовки в течение 1,0 минуты. На 0,5 минуты в соляной ванне и на 0,1-0,15 в свинцовой ванне. величина тив должна быть минимальной, но с завершением фазового превращения стали необходимо обеспечить необходимую концентрацию углерода и легирующих элементов аустенита. Время изотермической выдержки при определенной температуре механических деталей часто равно 15-25% от времени прохождения тепла. Выдержка в электропечи при температуре закалки инструмента из углеродистой стали (0,7-1,3% С) рекомендуется с минимальным сечением 1-50-80 секунд, легированной стали-70-90 секунд.
При нагревании в соляной ванне она составляет 20-25 секунд для углеродистой стали, соответственно, 25-30 секунд для легирования. Ной. Рекомендуется предварительно нагревать формовочные инструменты и механические детали сложной формы при нагреве при быстром охлаждении для уменьшения деформации В духовке при температуре 400-600°C Выбор теплоносителя при термообработке. При нагревании в пламени или электрической печи, атмосфера печи и Поверхность нагретого изделия приводит к окислению и обезуглероживанию стали. Окисление вызывает необратимые потери металла, ухудшая состояние поверхностного слоя, и необходима последующая ошпаривание.
Окисление происходит в результате взаимодействия стали с кислородом (2Fe + + О2 — > 2FeO), водяным паром (Fe + H2O-> FeO +Н2) и углекислым газом (Fe +СО2-> FEO +со). На начальной стадии нагрева происходит окисление, так как указанная химическая реакция происходит на поверхности. После образования оксидной пленки процесс окисления протекает в результате диффузии атомов кислорода к металлу через слой накипи и обратной диффузии атомов металла (ионов) к поверхности через накипь. При нагревании до 500-550 ° С окисление незначительно, но по мере дальнейшего повышения температуры скорость и интенсивность окисления возрастают significantly. In в частности, если есть пористость в формовочной окалине (свойство оксида железа). Обезуглероживание происходит при высоких температурах в результате взаимодействия стали с водородом(аустенит+2Н2-> Fey +СН4) и кислородом (аустенит + 0,5о2-«Fey + со).
Он уменьшает твердость, сопротивление износа и сопротивление усталости. Для защиты продукта от окисления и обезуглероживания в рабочее пространство аппарата вводится защитная газовая среда(контролируемая атмосфера). furnace. As в такой среде используются следующие атмосферы: 1)в присутствии катализатора происходит частичное сгорание метана CH4 (природный газ) с коэффициентом избытка воздуха 21% CO, 40% a = 0,25 (кг-BO) поглощение тепла (N2) 2% CH4, 37%.1 нагрев в водородсодержащей атмосфере позволяет проводить гидрирование стали, что приводит к снижению ее пластичности и увеличению тенденции к замедлению деструкции, поэтому в последнее время сравнительно начинают применяться маловодородные атмосферы(20% CO, 20% H2 и 60% N2); такие атмосферы используются на ВАЗ и ЗИЛе. 2) тепловыделение, полученное частичным сжиганием природного газа при a = 0,6 без рафинирования и сушки (PS-0,6) или с рафинированием и сушкой (PSO-06); атмосфера PSO-06 содержит 10% СО. 15-16%Н2; 0.05 ~ 1.5%СН4; 68-72%N2; кроме того, PS-06, до 6% CO2 и 2,3%H2O.
атмосфера PSO-06 может использоваться при нагреве для отжига, отпуска и упрочнения легированных конструкционных и инструментальных сталей. 3) получена практически полным сжиганием природного газа при a = 0,9 без подогрева (плохой), очистки и сушки (ПС-09) и очистки и сушки 1 реакция поглощения тепла называется endothermic. In в связи с этим появилось название атмосферы, получаемой нагретым генератором. 200koy(PSO-09), В последнем случае эта атмосфера включает 2%CO, 2%H2 и 96%N2.In в атмосфере (ПС-09) присутствует 10% CO2 и 2,3% H2O(за счет соответствующего уменьшения количества азота).Эта атмосфера использована для нагревать низкоуглеродистую сталь, структурную сталь и сталь инструмента. 4) диссоциация аммиака (DA), содержащего 75% Ng и 25% N2, или a = 0,7 -? 0,9 и последующая сушка(пса-08).Аммиак диссоциации (DA и PSA-08)
главным образом использован для нагревать коррозионной устойчивости и термической обработки электрической стали. 5) технология очистки азота от кислорода, аргона, гелия и водорода (2-4% H2, 98-96% N2). В последние годы, особенно коррозионная устойчивость, сопротивление жары, электрические свойства, электрические свойства, и особенные сталь и сплав. Режущие инструменты часто нагреваются с расплавленной солью, а также входят в состав небольшого станка. Охлаждающая среда для закалки. Охлаждение при упрочнении должно обеспечивать получение мартенситной структуры в пределах определенного участка изделия (постоянное упрочнение) и отсутствие дефектов упрочнения (трещины в поверхностном слое, деформация, искривление, высокие остаточные напряжения растяжения).
Высокая скорость охлаждения, которая наиболее желательна в интервале температур (выше критической скорости закалки), подавляет разложение переохлажденного аустенита в М-перлите, а высокая скорость охлаждения в интервале температур промежуточного охлаждения и замедленного охлаждения мартенсита MG-Mg мартенситного превращения нежелательна, поскольку вызывает резкое повышение уровней остаточных напряжений. В то же время слишком медленное охлаждение в интервале температур МК-МК может частично закалить мартенсит, увеличивая количество остаточного аустенита. О стабилизации для уменьшения твердости стали. Обычно для тушения используют кипящую жидкость-воду, водный раствор соли и щелочи, масло. При тушении в этих средах выделяют 3 периода.
1) пленочное кипение, когда на поверхности стали образуется «паровая рубашка».В течение этого периода скорость охлаждения будет относительно низкой. 2) пузырьковое кипение, которое происходит, когда паровая пленка полностью destroyed. It наблюдается при охлаждении поверхности ниже критической температуры. В этот период тепло быстро удаляется. 3) конвективное тепло transfer. It соответствует температуре ниже точки кипения охлаждающей жидкости. Отвод тепла в этот период осуществляется с наименьшей скоростью. Внутри таблицы.
На рис. 3 показан примерный температурный диапазон и относительная скорость охлаждения пузырькового кипения в середине этого интервала для различных охлаждающих сред. 201 когда стабильность переохлажденного аустенита погашена низкоуглеродистой и некоторой низколегированной сталью, вода и водный раствор NaCl или NaOH использованы как охлаждая средство. Вода как охлаждающая среда имеет существенный недостаток. Высокая скорость охлаждения в интервале температур мартенситного превращения часто приводит к образованию закалочных дефектов. При повышении температуры резко ухудшается закаливающая способность (см. таблицу 3).
Если продукт гасится в горячей воде из-за медленного охлаждения при высокой температуре и быстрого охлаждения при низкой температуре, тепловое напряжение будет низким, а самое опасное структурное напряжение будет увеличено, что может вызвать растрескивание. Холодная вода NaCl и NaOH и 8-12% водный раствор, которые были продемонстрированы на практике, отличаются самой высокой и наиболее равномерной охлаждающей способностью. При тушении водным раствором паровая рубашка разрушается практически мгновенно, охлаждение происходит более равномерно и протекает преимущественно на стадии пузырькового кипения. Улучшенная охлаждая емкость может быть достигана путем использование охлаждать двигателя или ливня cooling.
It широко применяется, например, для поверхностного упрочнения. Дальнейшим усовершенствованием способа охлаждения стало использование смеси воды и воздуха, подаваемой из сопла. Водовоздушная среда используется для охлаждения крупных поковок, рельсов и др. Минеральное масло (обычно нефть) используется для легированных сталей с высокой стабильностью переохлажденного аустенита при закалке. Масло как твердеющая среда имеет следующие преимущества: скорость охлаждения в мартенситном диапазоне температур низкая, что снижает возникновение дефектов закалки и постоянство закалочной способности при широкой температуре окружающей среды (20-150°С).
Относительная охлаждающая способность закалочной среды Таблица 3 Охлаждающая среда Температура°C Относительная скорость охлаждения в диапазоне пузырькового кипения Охлаждающая среда Пузырькового кипения Вода 20400-100 1.0 40350-100 0.7 80 250-100 0.2 10% водный раствор NaCl-20 ’650-100 3.0 Водный раствор NaOH:10%20 650-100 2.0 50%20 650-100 2.0 минеральное масло 20-200 500-250 0,3 Недостатками являются повышенная воспламеняемость (температура вспышки 165°С —°С), недостаточная стабильность, низкая охлаждающая способность в температурном диапазоне превращения перлита, а также повышенная стоимость. Температура масла во время закалки поддерживается на уровне 60-90°С, если вязкость минимальна.
В последние годы вместо воды и масла стали использоваться водные растворы моющих средств, содержащие поверхностно-активные вещества, жидкие силикаты, особенно воду, пласты и другие синтетические вещества. Аквапластика-это концентрат на водной основе высоковязких прозрачных жидкостей, в том числе водорастворимых пластмасс и ингибиторов коррозии. Концентрация раствора составляет 0,5-0,7%, при закалке водного раствора полимера и моющего средства скорость охлаждения снижается при температурах ниже м а, в результате устраняется образование трещин, уменьшается деформация.
Прокаливаемость и закаливаемость стали. Под закаливаемостью понимают способность стали повышать свою твердость в результате закалки. Прокаливаемость стали в основном определяется содержанием углерода в стали. Чем больше углерода в мартенсите, тем выше твердость (см. Рисунок 116).Легирующие элементы оказывают относительно небольшое влияние на прокаливаемость. Закаливаемость означает способность принимать Сталь. Мартенсит или рыхлый-слой с мартенситной структурой и высокой твердостью до 1 или другой глубины. Прокаливаемость определяется критической скоростью охлаждения, которая зависит от состава стали. Если фактическая скорость охлаждения в сердцевине изделия превышает критическую скорость закалки vK (рис. 129, Gk), то сталь приобретает мартенситную структуру по всему поперечному сечению, тем самым упрочняясь.
Если фактическая скорость охлаждения ядра ниже, чем это. gk (% , g«), продукт только зажигание Определенные глубины a, a’ и прокаливаемость являются imperfect. In в этом случае аустенит разрушается в ядре с образованием слоистой структуры карбида феррита (трустит, сорбит или перлит). Глубина от затвердевшего слоя условно считается расстоянием от поверхности до зоны полутенсита(50%мартенсита+ 50%труститов).Диаметр заготовки, в центре которой после закалки с заданной охлаждающей средой образуется полумартенситная структура, называется критическим диаметром. Величина критического диаметра определяет размер поперечного сечения изделия. Поперечное сечение изделия закалено. То есть получается высокая твердость, а после отпуска получаются высокие механические свойства по всему section.
In во многих случаях полумартенситные структуры не обеспечивают максимальной механической прочности. properties-mon. In в этом отношении прокаливаемость часто определяется глубиной упрочненного слоя, который имеет 95% мартенситную структуру. Критический диаметр 95%мартенсита приблизительно на 25% меньше критического диаметра, определяемого из зоны полутенсита. Полное отверждение 99,9% мартенситного состава ткани- 203 мартенсит Чтение ПЭП- И Р ’ИТ-кароид ^ / ная структура (Трост-плотный, сорбит-перлит)’ мартенсит Рисунок 129.Зависимость критической скорости отверждения от величины gk: a и a ’- это глубина отвержденного слоя. г Купянск является критическая скорость охлаждения углеродистой стали. «K-критическая скорость охлаждения низколегированной стали, v ’» K-высоколегированная сталь (сталь легирована некоторыми элементами) Зона −50%\half martensite semi-martensite может быть легко определена микроструктурой, но она принята как критерий для лечить, потому что она более добавочно упрощена твердостью.
Твердость полумартенситной ткани зависит от содержания углерода в стали. Например, для 0,13 к 0,22% к, твердость структуры полумартенсита стали углерода ХРК 25, сплавляя ХРК 30.It может быть 0.28-0.32% C, HRC 35 и HRC 40, 0.43-0.52% C, HRC 45 и HRC 50, и 0.53-0.62% C, HRC соответственно. 50 и HRC 55. Ешьте мартенсит(полный про-Ива) Чем выше критическая скорость закалки, т. е. чем выше стабильность переохлажденного аустенита, тем выше прокаливаемость. Легированная сталь обладает высокой стабильностью переохлажденного аустенита, из-за низкой критической скорости охлаждения соответственно(рис. 129, г? K и г Купянск) увольняют на большую глубину, чем углеродистые. Значительно улучшается отверждаемость марганца, хрома, молибдена и мелких Боровых насаждений (0,003-0,005%), никель и кремний не сильно страдают much.
In в частности, одновременное введение в сталь нескольких легирующих элементов повышает ее прокаливаемость. Стабильность переохлажденного аустенита повышается, а критическая скорость закалки снижается только при растворении легирующих элементов в аустените. Если легирующие элементы находятся в виде избыточных карбидных частиц, то карбид не может повысить стабильность аустенита и уменьшить ее, поскольку он выступает в качестве части непосредственной доставки, способствующей разложению аустенита. Карбиды титана, ниобия и ванадия при нормально принятой температуре закалки не растворяются нормально в аустените, и отверждаемость снижается. Размер зерна аустенита сильно влияет на curability. In углеродистая сталь, когда зерно расширяется от 6 до 1-2(см. Рисунок 103), глубина упрочненного слоя увеличивается в 2-3 раза.
Легирующий элемент 1 для инструментальных сталей, карбидных сталей и нитроцементирующих сталей определен предельный диаметр структуры мартенсита 95-99%. Рисунок 204 130. 0.4/, ’ с второй 0.85% Мп(а);.Включая твердость и площадь поперечного сечения стали. 0.4%с; 0.85% Мп и 1% хрома(б); 0.4%с; 3.5%никеля и 1,5%СГ(в): 1-половина зоны мартенсит, твердость, НRС Карбидсодержащие соединения не только создают дополнительный центр, способствующий разложению аустенита, но и измельчают его зерна. Это увеличивает критическую скорость отверждения и уменьшает отверждаемость. Через-твердеть, свойства стали, особенно твердость, эти же для всего поперечного сечения product. In в случае сквозного упрочнения изменение структуры стали вдоль поперечного сечения способствует соответствующему изменению характеристик. На рисунке показано распределение твердости по поперечному сечению закаленных цилиндров в различных сталях. 130
.На полное излечение, снижение твердости от поверхности к сердечнику. От. Рис. 130 твердость полумартенситной области углеродистой стали в этих рабочих условиях составляет 25 мм, при критическом диаметре 50 мм, Хроме-50 мм, хромоникеле-125 мм. Благодаря высокотемпературной закалке разница между твердостью и прочностью на растяжение всего поперечного сечения уменьшается при отпуске при высокой температуре. Однако предел текучести, ударная вязкость и относительное сужение сердцевины образца остаются низкими. Это связано с различной природой структуры феррит-цементита structure. In в упрочненном слое в результате отпуска мартенсита образуется более дисперсная феррит-цементитная структура с зернистой структурой, а в сердцевине, Он более грубый и имеет слоистую структуру. В
лияние прокаливаемости на механические свойства можно проиллюстрировать примерами. Заготовки, изготовленные из углеродистой стали 0.45% с, диаметром 10 мм, которые стреляли по воде. После отпуска при 550°С получается структура-сорбитовый отпуск. Такая структура характеризуется высокими механическими свойствами. СТВ= 80 кг / мм2; 100, 2 = 65 кг / ’мм2,5 = 16%; f = 50% и en = 10 кгс — м / см2.Если диаметр заготовки составляет 100 мм, и она закалена в воде, то скорость охлаждения сердечника будет значительно ниже, чем у ГК, в результате чего образуется пластинчатая перлитная и ферритовая структура. Эта структура Механические свойства 205 низкие: stv = 70 кгс / мм2; s> 0 2 = 45 кгс / мм2; 5 = 13%; f = 40% и yang = 5 кгс-м / cm2.
To получение же высоких механических свойств по всему сечению, зачастую необходимо обеспечить за счет упрочнения в процессе упрочнения. Отверждаемость углеродистой стали в небольших сечениях (до 15-20 мм в диаметре) определяется типом разрушения закаленной samples. In во многих случаях прокаливаемость определяется кривой распределения поперечной твердости (рис. 130). для этого разрушают или разрезают образец, твердость которого определяется диаметром поперечного сечения. Прокаливаемость стали обычно определяется поверхностным упрочнением (ГОСТ 5657-69).Цилиндрические образцы определенной формы и размера (рис.131), нагретые до определенной температуры и температуры, охлаждаются водой с краев специального оборудования.
После охлаждения измеряют твердость по длине(высоте) образца. Скорость охлаждения уменьшается по мере увеличения расстояния от края, поэтому твердость также уменьшается. Результаты испытаний графически представлены координатами твердости (расстояние от конца охлаждения).Если определить расстояние от торца до участка с твердостью, соответствующей площади полутенсита конкретной стали, то можно найти критический диаметр из специального nomogram. In для того чтобы не допустить отнесения упрочняющих свойств стали к типу охладителя, при использовании номограмм вводится понятие идеального критического диаметра, представляющего собой максимальный диаметр образца, который полностью выпекается при идеальном охлаждении.
Поверхность образца в идеальном охладителе должна немедленно приобрести свою температуру. То есть охлаждение должно осуществляться с бесконечно высокой скоростью. От идеального критического диаметра можно перейти к фактическому критическому диаметру, используя номограмму, показанную на рисунке. 132, а. определите критический диаметр стали 1(см. Рисунок 131). Для этой стали расстояние от кромки до поверхности полумартенситной зоны составляет 10 mm. To определить критический диаметр окалины, расстояние от упрочненной кромки до полумартенситной зоны (рис.132, а), найти деление 10 и опустить перпендикуляры до пересечения с линией»полного охлаждения».Из точки а проведите горизонтальную линию влево
до тех пор, пока она не пересечется с указанной охлаждающей средой (водой (точка в) или маслом (точка с)).Из точек b и c мы опускаем перпендикуляр (критический диаметр)относительно шкалы. Точки C и B указывают желаемый размер критического диаметра. На практике график, показанный на рисунке, позволяет определить критический диаметр с достаточной точностью. 132.6.To для этого на горизонтальной оси устанавливают расстояние от охлаждающего конца до зоны с полумартенситной твердостью и восстанавливают перпендикуляр до пересечения с кривой закалки маслом или водой. Горизонтальная линия, проведенная от
этой точки до ординаты, показывает значение DK. Например, для Стали 2(см. фиг.131) расстояние от кромки до зоны полутвердости мартенсита составляет 19 мм, при закалке водой£> k = 75 мм, при закалке маслом£> k = 50 мм (см. фиг. 132.6). Прокаливаемость одной и той же стали может сильно варьироваться в зависимости от изменения химического состава и скорости охлаждения при 700°C £ля 100. Рис. 131 <определение прокаливаемости методом механических испытаний: а-изменение твердости по длине образца после механического отверждения: I-твердость полумартенситной полосы. 1-менее закаленная сталь. 2-закаленная сталь. б-пример схемы усиления Расстояние а от леча конца) Степень детализации продукта, размер, форма и много другого factors.
In в связи с этим прокаливаемость каждой марки стали характеризуется не кривыми, а так называемыми полосами прокаливаемости, которые не всегда отражают фактическую прокаливаемость стали в изделии. На рисунке показаны полосы прокаливаемости углеродистых и легированных сталей, содержащих 0,4% С, которые наглядно демонстрируют действие легирующих элементов. 133. Внутреннее напряжение закаленной стали. Внутренние напряжения при закалке стали возникают в результате неравномерного охлаждения поверхности изделия и сердцевины (эти напряжения называются термическими) 1, увеличения объема, а также неравномерности протекания мартенситных превращений в объеме изделия.
Напряжение, вызванное этим преобразованием, называется структурой или фазой. 1 в этих случаях возникает только тепловое напряжение Ая, когда нет фазового превращения. Это наблюдается, например, при охлаждении отожженной стали от температуры ниже точки LC. Идеальный критический диаметр, мм ОО расстояние от края полумартенситной зоны, мм 0,5 1 2 5 5 710 20 00 80 Г Т Я Я Я Я 11 я я я я’ltiiiii Предельный диаметр DK (D-1O) расстояние от кромки, мм один.) 5.) Рисунок 132.Определение критического диаметра прокаливаемости стали: а-номограмма; б-пунаграмма Расстояние от 207 торцов, мм с) Расстояние от края, мм 8.) Рисунок 133.Диапазон закаливаемости различного состава стальной: а-0.4′%. б-0.4%с + 1.0%СГ; б-0.4%с + ст 1.5% + 0.18%МО;
1-полу-мартенсит, твердость зоны Неравномерное распределение температуры по поперечному сечению изделия при быстром охлаждении сопровождается неравномерным изменением объема. Поверхностный слой сжимается быстрее, чем внутренний. Однако сжатию поверхностного слоя препятствует внутренний слой. Это приводит к образованию временных (то есть растягивающих) и внутренних сжимающих напряжений в поверхностном слое. ■Даже после того, как поверхность остыла и объем перестал изменяться, ядро подвергается термическому воздействию shrinkage. As в результате напряжение начинает уменьшаться, и в какой-то момент признаки напряжения на поверхности и ядре меняются. После окончательного охлаждения
получают остаточные сжимающие напряжения на поверхности и растягивающие напряжения на сердечнике (рис. 134, а).Появление остаточных напряжений является следствием того, что временные напряжения вызывают не только упругость, но и 1 степень или другую несимметричную и неравномерную пластическую деформацию слоя на поперечном сечении. Рассмотрим теперь условия формирования структурных напряжений при полном hardenability. In в этом случае термическое напряжение не рассматривается условно. Когда температура ниже точки Mn достигается во время закалки, мартенсит образуется в основном на поверхности, где точка Mn достигает
раньше, чем ядро. Аустенит-мартенситные превращения сопровождаются увеличением объема, что приводит к образованию временных сжимающих напряжений на поверхности и внутри 208+ один.) С.) с.) Рисунок 134.Принципиальная схема остаточного напряжения: «- Тепловая; б-структура; в-Общая [И ядро-напряженность- Слой-растяжимое напряжение: по мере того как преобразование продолжается, знак напряжения на поверхности и ядре изменяет. Структурные напряжения к термическим напряжениям относятся reversed. As в результате мартенситного превращения на поверхности образуется остаточное сжимающее напряжение (рис.134.6).Эти остаточные
напряжения, такие как тепловые напряжения, возникают в результате появления неоднородных временных напряжений в поперечном сечении упругого элемента, а также остаточных деформаций. При упрочнении стали одновременно возникают как тепловые, так и структурные напряжения(рис.134, г). в этой схеме на поверхности образовалось сжимающее напряжение, так как тепловое напряжение было выше структурного. Однако в зависимости от соотношения между термическими напряжениями и структурными напряжениями могут быть получены различные диаграммы суммарных напряжений, причем в поверхностном слое напряжения они могут иметь различные признаки и различаться values. In во многих случаях величина фазного напряжения больше, чем теплового. Остаточное напряжение,
полученное после закалки, не характеризует напряжение, возникающее в результате охлаждения (нагрева) стали. Остаточное напряжение всегда меньше переходного напряжения, возникающего при охлаждении. Если величина напряжения превышает сопротивление разрыву, а металл слегка пластичен, то напряжение не может быть уменьшено за счет пластической деформации. Это вызовет трещину. Наиболее опасны растягивающие напряжения на поверхности. Способствует образованию трещин и снижает долговечность стали. Растягивающие напряжения возникают главным образом из-за структурных напряжений, которые необходимо стремиться уменьшить. Чем выше температура закалки и скорость охлаждения в диапазонах температур Mn и MK, тем выше структурная stress. To уменьшите
структурное усилие, охлаждая тариф должен быть уменьшен до Под пункта M и во избежание перегреть стали. Методы закалки. Наиболее широко используется охлаждение в 1 охладителе (см. Рисунок 127).Такое упрочнение называется непрерывным. Часто изделия особенно сложной формы, а при необходимости уменьшения деформации, применяют и другие способы закалки. Периодическая консолидация(2 среды).Затвердевший таким образом продукт сначала быстро охлаждают в воде до температуры чуть выше точки L1n, затем быстро переносят в охладитель с меньшей прочностью (например, масло или воздух), где охлаждают до 20°C. В результате перехода на 2-ю закалочную среду внутренние напряжения, возникающие при быстром охлаждении 1-й среды (воды), включая температурный диапазон мартенситного
превращения, уменьшаются. 209 рис. 135.Схема СТУ Ступенчатой закалке стали, содержащий 0,8% С(А) и изотермической закалки легированной стали (С5) self-tempering. in в этом случае охлаждение изделия с помощью закалочной среды приостанавливается, так что дополнительное тепло сохраняется в сердцевине изделия. Под действием теплопередачи повышается температура поверхностного слоя, который охлаждается сильнее, что сопоставимо с температурой ядра. Поэтому происходит отпуск стальной поверхности (самовоспламенение). Самоотпуск, например, применяется для таких инструментов, как долото, кувалда, верстак, керн, который работает с ударными нагрузками и требует сочетания высокой твердости поверхности и высокой вязкости керна.
Шаг закалки. При закалке, проводимой таким способом(рис. 135, а), после нагрева до температуры закалки сталь охлаждают в среде с температурой несколько выше точки Mn (обычно 180-250°С) и выдерживают в течение относительно короткого времени. Затем охладите продукт на воздухе до комнатной температуры temperature. As в результате воздействия закалочной среды достигается температурная гомогенизация поперечного сечения изделия, но это не должно вызывать превращения аустенита с образованием бейнита. При охлаждении на воздухе мартенситное превращение протекает, но его целостность ниже,
чем при непрерывном hardening. As в результате сталь сохраняет больше остаточного аустенита. Ступенчатое упрочнение приводит к большему удержанию аустенита и уменьшает объемные колебания за счет возможности самоотдачи мартенсита. Риск искривления и растрескивания в результате мартенситной метаморфозы возникает практически одновременно во всех частях изделия. При фазовом превращении с участием мартенсита прочность стали снижается, а пластичность повышается. Этот вид размягчения наблюдается только при метаморфозе
(в данном случае мартенсит) и применяется при ступенчатом упрочнении для отделки изделий, склонных к короблению. Редактирование (часто под давлением) выполняется После удаления продукта из охлаждающей среды, 210 во время охлаждения продукта на воздухе. Ступенчатое упрочнение углеродистой стали применимо только к изделиям диаметром не более 8-10 мм. скорость охлаждения крупного изделия в среде, температура которой превышает точку Mn, ниже критической скорости закалки, и аустенит разлагается при высоких температурах. Изотермической вулканизации. Тушение таким способом (рис.135.6) выполняется в основном так же, как и ступенчато, но в этом случае обеспечивается большая выдержка выше точки M n. Эта выдержка причиняет аустенит разложить и сформировать более низкий бейнит.
Для углеродистой стали при изотермической закалке механические свойства существенно не улучшаются по сравнению с механическими свойствами, полученными при обычной закалке и отпуске. В большинстве легированных сталей разложение аустенита в промежуточной области не продолжается до конца. Если аустенит, не разложившийся в процессе изотермического старения, охлаждается дальше, но не претерпевает мартенситного превращения, то сталь приобретает обогащенный углеродом бейнит+ 10-20% остаточной аустенитной структуры. Благодаря этой структуре достигается высокая прочность и достаточная вязкость. Для многих сталей изотермическое отверждение значительно повышает
прочность образцов с конструкционной прочностью, то есть сложных форм. Однако если большая часть аустенита, не разложившегося после окончания промежуточного превращения, подвергается мартенситному превращению при последующем охлаждении, то высокие механические свойства не могут быть получены путем изотермического quenching. In в этом случае пластичность резко падает. Конструкционная легированная сталь (0,3-0,5% с) приобретает оптимальные механические свойства в результате изотермического упрочнения, которое сохраняется в нижней (несколько выше Mn) средней зоне изотермического разложения аустенита. Время
выдержки в закаленной среде зависит от стабильности аустенита при температурах выше точки Ма, которая определяется диаграммой изотермического разложения аустенита в данной стали. В качестве охлаждающей среды при ступенчатой и изотермической закалке часто используют расплавленную соль в интервале температур 150-500°С. Например, 55% KNO3 и 45% NaNO2 (или NaNO3), а также расплавленную щелочь (20% NaOEl и 80% KOH).Чем ниже температура соли (щелочи), тем выше скорость охлаждения соли. Поскольку расплавленная соль охлаждается только за счет теплопередачи, охлаждающая способность увеличивается при перемешивании. При погружении в нагретый продукт для закалки добавление воды (3-5%) в каустический расплав (с помощью
специального устройства) вызывает увеличение скорости охлаждения в интервале температур кипения и превращения перлита. Скорость охлаждения увеличивается на 400-450℃, в 4-5 раз, на 300℃, в 2 раза. Охлаждение расплавом едкой щелочи позволяет получить светло-серую чистую поверхность, если деталь предварительно нагревалась жидкой солью(соль, не вызывающая окисления). То.. Тушение этим методом называется светом. Холодная обработка стали 211.Особенно для закаленных сталей, содержащих более 0,4-0,5% C, точка Mk ниже нуля (см. Рисунок 115), поэтому остаточный аустенит присутствует всегда. Аустенит снижает твердость, износостойкость и в результате самопроизвольного изменения мартенсита, часто приводит к изменению размеров
деталей, работающих при низких температурах. Для уменьшения количества остаточного аустенита в закаленной стали применяют холодную обработку, которая охлаждает закаленную сталь до температуры ниже нуля. Понижая температуру до точки L1K (- 304-70С), С преобразует остаточный аустенит в мартенсит в большинстве сталей, увеличивая твердость стали от 0,8 до 1,1% С до HRC 1-3.Но в то же время продукт охлаждают, потому что стресс увеличивается после лечения простуды, медленно и быстро уходят. Выдержка стали после закалки в течение более 3-6 часов при комнатной температуре стабилизирует аустенит и при дальнейшем охлаждении
не полностью превращается в мартенсит, тем самым уменьшая воздействие холода working. In в этом случае низкотемпературную обработку проводят сразу после закалки. Холодная обработка главным образом использована для измеряя инструментов, весен карбида вольфрама стальных и частей которые держат много аустенита после гасить.
Смотрите также:
Решения задач по материаловедению
Отпуск | Отжиг 1 рода |
Термомеханическая обработка | Отжиг ii рода (фазовая перекристаллизация) |