Оглавление:
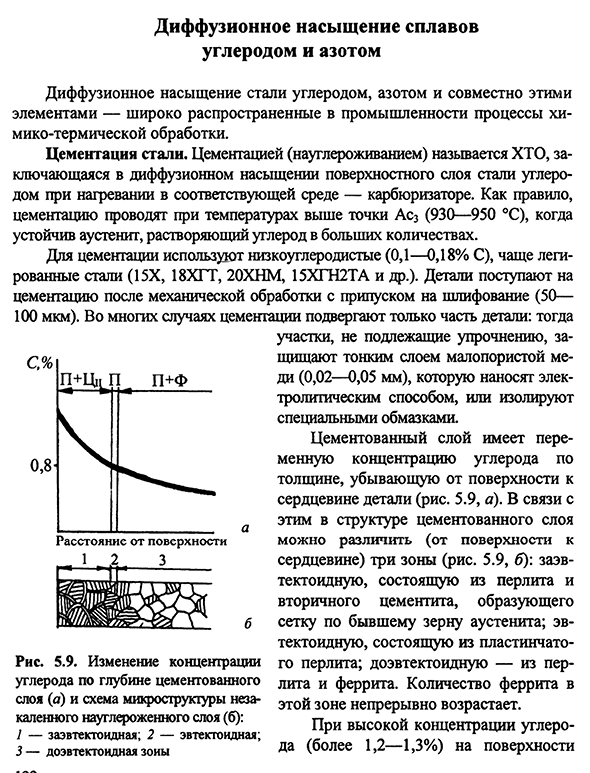

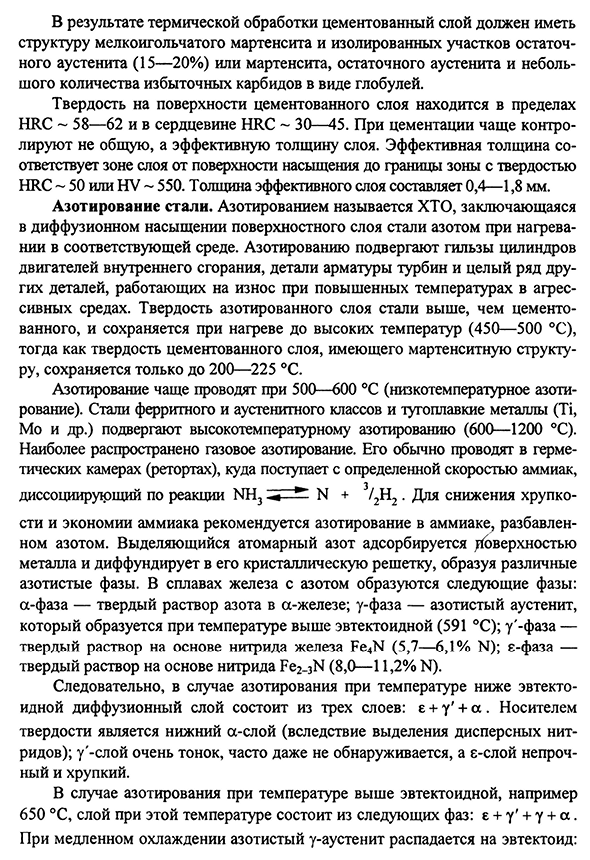
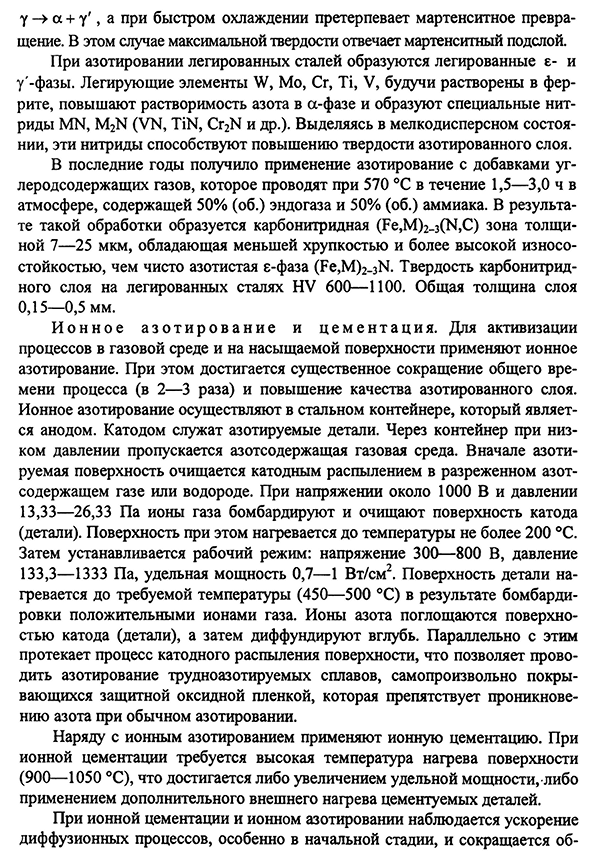
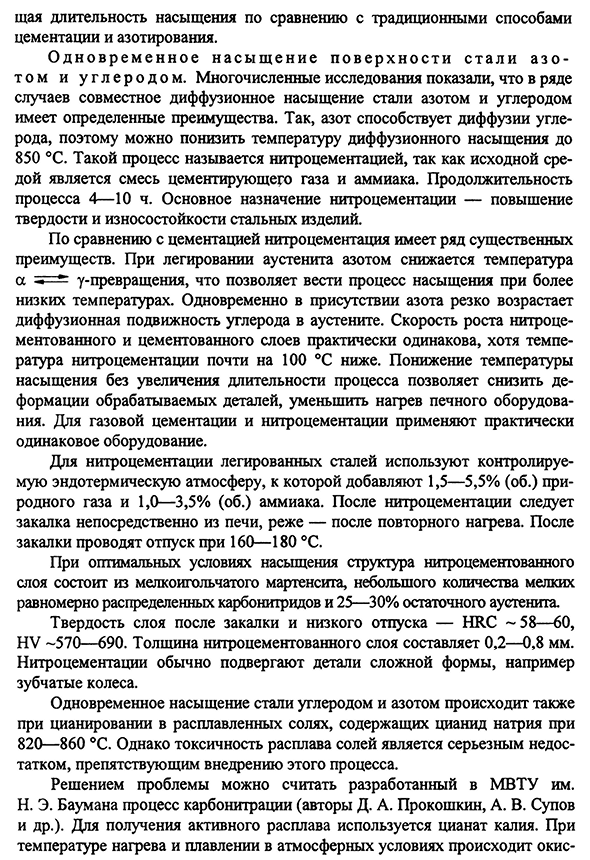
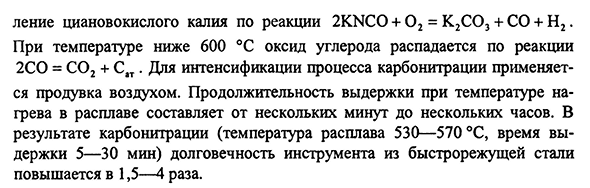

Диффузионное насыщение сплавов углеродом и азотом
- Диффузионное насыщение сплавов углеродом и азотом Диффузионное насыщение углерода, азота и стали этими элементами широко распространено в промышленных процессах химико-термической обработки. Цементирование стали. Цементацией (карбюризацией) называют CTO, диффузионное насыщение поверхностного слоя стали углеродом при нагреве в подходящей среде-карбюраторе. Как правило, его подвергают цементации при температуре выше AC3 (930-950 ° С), когда аустенит стабилен и растворяет большое количество углерода.
Для цементации, низкоуглеродистая (0.1-0.18% C), легированная сталь (15X, 18XGT, 20XNM, 15XGN2TA, etc.) чаще.(Это значение по умолчанию). Детали поступают на цементацию после механической обработки с припуском на шлифование (50-100 мкм). Часто цементируется только часть детали. Расстояние от поверхности Рис. 5.9 изменение концентрации углерода в глубине цементного слоя (а) и схема микроструктуры неотвержденного
карбонизированного слоя(Б): 1-соэвтектоид;2-соэвтектоид; 3-предэвтектоид. Людмила Фирмаль
Участок, не подвергающийся упрочнению, защищен тонким слоем низкопористой меди (0,02-0,05 мм), который изолируется электролизом или специальным покрытием. Толщина цементного слоя представляет собой изменяющуюся концентрацию углерода, которая уменьшается от поверхности к сердцевине детали(рис. 5.9, а). В связи с этим в структуре цементного слоя можно выделить три зоны (от поверхности до сердцевины) (рисунок). 5.9,
б): Заев-тектодоид, состоящий из перлита и вторичного цементита, образующего зернистую сетку перед аустенитом; эвтекит, выполненный из пластинчатого перлита; парла количество феррита в пределах этой зоны непрерывно увеличивается. При высоких концентрациях углерода (более 1,2-1,3%) на поверхности Крупнозернистая цементитная сетка или цементит, образованный 122layer, высвобождается в виде игл, которые отрицательно влияют на прочность диффузионного слоя.
- Основные виды цемента-твердый и газовый. Газовая цементация является более совершенным технологическим процессом, чем твердая цементация. Он имеет ряд преимуществ перед цементирующими твердыми карбюраторами. В случае газовой цементации может быть получена заранее определенная концентрация углерода в пластах; сокращается продолжительность процесса; возможна полная механическая обработка процесса.
Цементный слой высшего качества почти полностью состоит из метана (Snd) и пропан-бутановых смесей, а также жидких углеводородов, основная реакция, обеспечивающая цементацию в процессе газовой цементации, которая использует природный газ в качестве испарителя, осуществляется в 2CO->CO2+Cat; Cat->yFe © (технологический процесс составляет 910-930 C6-12h). Конечные свойства цементного продукта получаются в результате термообработки после цементирования. Такая обработка необходима для коррекции структуры и измельчения
сердцевины и цементного слоя, которые неизбежно увеличиваются при длительной выдержке при высоких температурах цемента. Людмила Фирмаль
В большинстве случаев, особенно при обработке зернистой стали по своей сути, закалка составляет 820-850°C. It наносится на верхнюю часть точки Acj (центр). Газовое цементирование часто применяют отвержденным без предварительного подогрева, и при такой обработке непосредственно из цементной печи после подстуживания изделий до 840-860 ° с структура цементного слоя может быть изменена. После цемента, термическая обработка иногда сделана двойной гасить и закалять. Для закрепления структуры сердцевины назначают первую закалку (или нормализацию), нагретую до 880-900 ° С (выше точки AC3 сердцевины).
Второе упрочнение проводят нагревом до 760-780 ° С для устранения перегрева цементного слоя и придания ему высокой степени твердости. Недостатками такой термической обработки являются сложность технологического процесса, возможность окисления и обезуглероживания. Заключительная операция термической обработки цементированных изделий заключается в переводе закалочного мартенсита поверхностного слоя в закаленный мартенсит и снижении давления. 123 в результате термообработки цементный слой разделяется на тонкоигольчатую мартенситную структуру и остаточный аустенит (15-20%) или мартенсит, остаточный аустенит и остаточный аустенит. Поверхностная твердость цементированного слоя находится в пределах HRC ~ 58-62 и Центра HRC ~ 30-45. Если цементация чаще контролируется, то это не вся, а эффективная толщина слоя.
Эффективная толщина соответствует зоне слоя, где твердость находится от насыщенной поверхности до границы зоны, HRC-50 или HV-550. Эффективная толщина слоя составляет 0,4-1,8 мм. Азотирование стали. Азотирование называется CTO и заключается в диффузионном насыщении поверхностного слоя стали азотом при нагревании в подходящей среде. Азотированию подвергаются гильзы цилиндров двигателей внутреннего сгорания, детали турбинных клапанов и многие другие детали, которые изнашиваются при высоких температурах в агрессивных средах. Твердость нитридного слоя стали выше, чем у цементного слоя, и сохраняется при нагреве до высокой температуры (450-500 ° С), в то время как твердость цементного слоя с мартенситной структурой составляет 200 ~ 225 ° С. Азотирование часто проводят при температуре 500-600 ° C (криогенное азотирование).
Ферритный и аустенитный класс и тугоплавкие металлы (титан, Мо и др.) сталь.) Подвергают высокотемпературному азотированию (600-1200°с). Наиболее распространено азотирование газа. Обычно это делается в герметичной камере (реторте), куда аммиак поступает с определенной скоростью и диссоциирует по реакции NH3N+3/2H2. Азотирование аммиака, разбавленное азотом, рекомендуется для снижения хрупкости и экономии аммиака. Высвобожденный атомарный азот адсорбировался под поверхностью металла и диффундировал в кристаллическую решетку с образованием различных азотных фаз. В сплаве железа и азота образуются следующие фазы: а-фаза-твердый раствор азота в железе; U-фаза-аустенит азота, образующийся при температурах выше 591 ° с; u’ — фаза-твердый раствор на основе нитрида железа Fe4N(5,7-6,1% N); e-фаза-нитрид Fe2_n (8,0-11,2% N).
Таким образом, для азотирования при температуре под эвтектоидом диффузионный слой состоит из трех слоев: e+u ’ +A. носителем твердости является нижний слой(за счет разделения дисперсного нитрида); u-слой очень тонкий, не часто обнаруживается, А Е-слой хрупкий и хрупкий. При азотировании при температуре выше эвтектоидной (например, 650 ° с) слой этой температуры состоит из следующих фаз: e+u’+u+A. При медленном охлаждении азот u-аустенит разъедается до эвтектоида: Претерпевает метаморфоз мартенситной под 124u->с+Щ’, и быстрым охлаждением. В этом случае максимальная твердость соответствует подслою мартенсита. Азотирование легированной стали позволяет получать легированные е — и u ’ — фазы. Элементы сплава W, Mo, Cr, Ti, V, растворяются в феррите, MN, M2N (VN, tin, Cr2N и др.), который увеличивает растворимость азота в фазе А и образует специальные нитриды. да что с тобой такое?
Эти нитриды, выделяющиеся в мелкодисперсном состоянии, способствуют повышению твердости нитридного слоя. В последние годы применяется азотирование с добавками углеродсодержащих газов, которое при 570 ° с составляет 1,5-3,0 часа 50% (об.) эндогаз и 50% (т. В результате такой обработки образуется чистая азотистая е-фаза (Fe, M) 2_3N. легированная сталь ХВ600-1100 обладает твердостью карбонитридного слоя общей толщиной 7-25 мкм, что составляет 0,15-0,5 мм, обладающая меньшей хрупкостью и высокой износостойкостью. I o n o e a z o t I R O V i E C e m e n t a C I i. ионное азотирование используется для активации газовой среды и процессов на насыщенной поверхности. При этом достигается значительное сокращение общего времени процесса(в 2-3 раза) и улучшается качество азотированного слоя.
Ионное азотирование осуществляется в стальных емкостях, которые являются анодами. Катод является азотирующей частью. Азотсодержащая газовая среда проходит через контейнер при низком давлении. Содержит азотную кислоту. во-первых, азотированная поверхность очищается разбавленным азотсодержащим газом или водородным катодным распылением. При напряжении около 1000 В и давлении 13,33-26,33 ПА ионы газа бомбардируют и очищают поверхность катода (детали). Поверхность нагревают до температуры не более 200 ° С. Затем устанавливается рабочий режим: напряжение 300-800 в, давление 133,3-1333 ПА, удельная мощность 0,7-1 Вт / см2. Поверхность детали нагревается до требуемой температуры (450-500 ° С) в результате воздействия положительных ионов газа.
Ионы азота поглощаются поверхностью катода(детали) и диффундируют глубже. Параллельно с этим протекает процесс катодного распыления поверхности, которая самопроизвольно покрывается защитной оксидной пленкой, препятствующей проникновению азота при нормальном азотировании. В дополнение к ионному азотированию используется ионная цементация. Ионное цементирование требует высокой температуры нагрева поверхности (900-1050°С), что может быть достигнуто за счет увеличения удельной мощности или за счет использования дополнительного внешнего нагрева шва.
Смотрите также: