Оглавление:
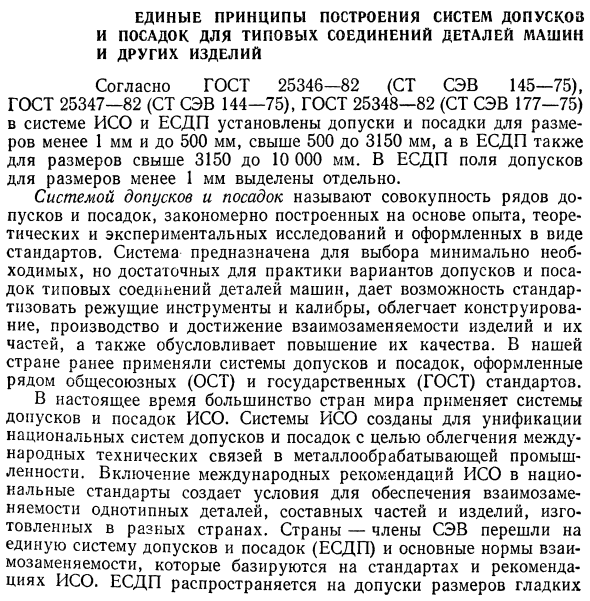
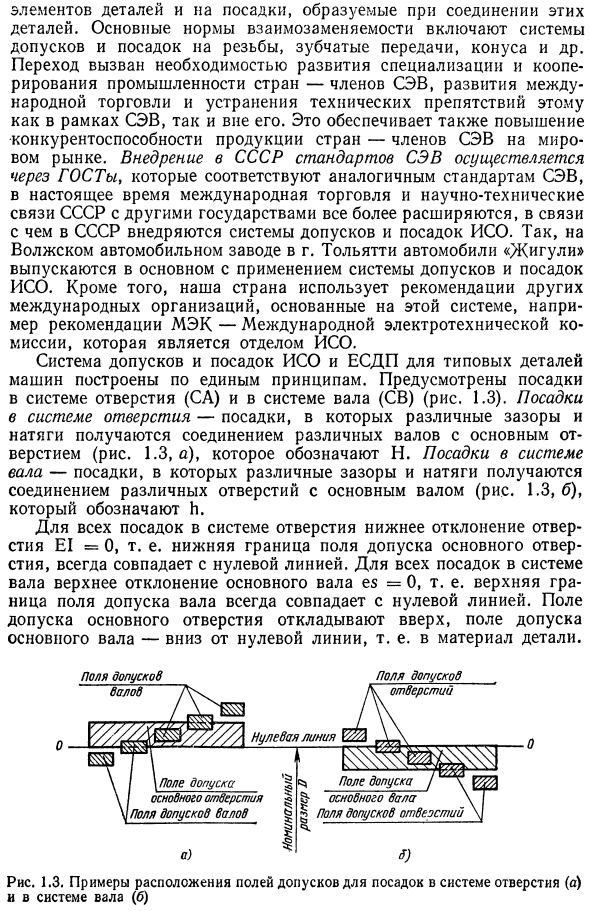
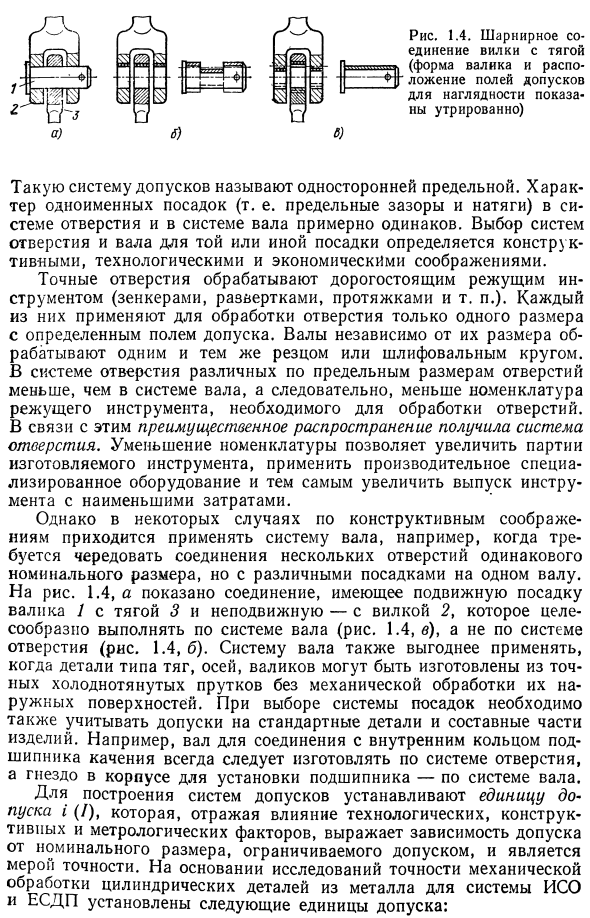
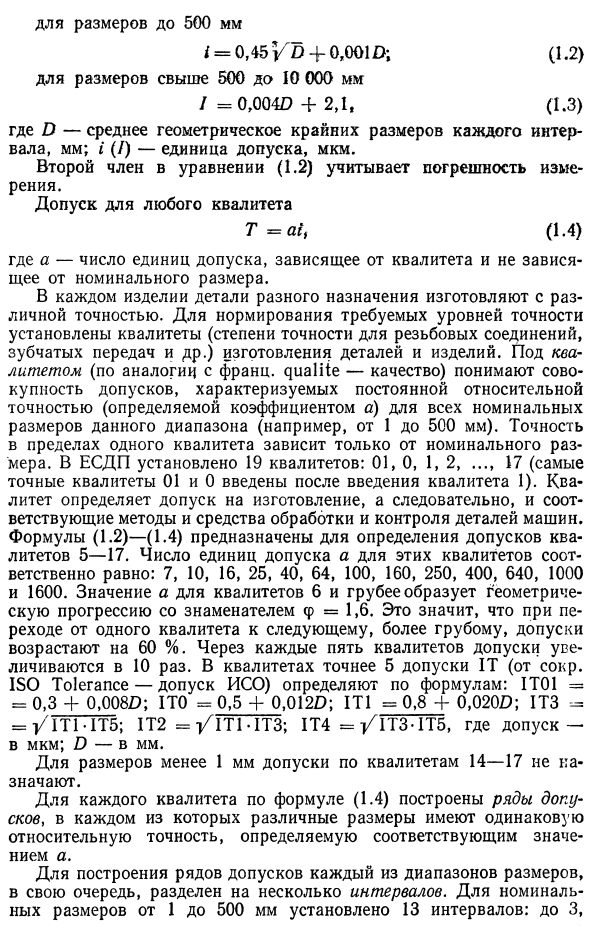
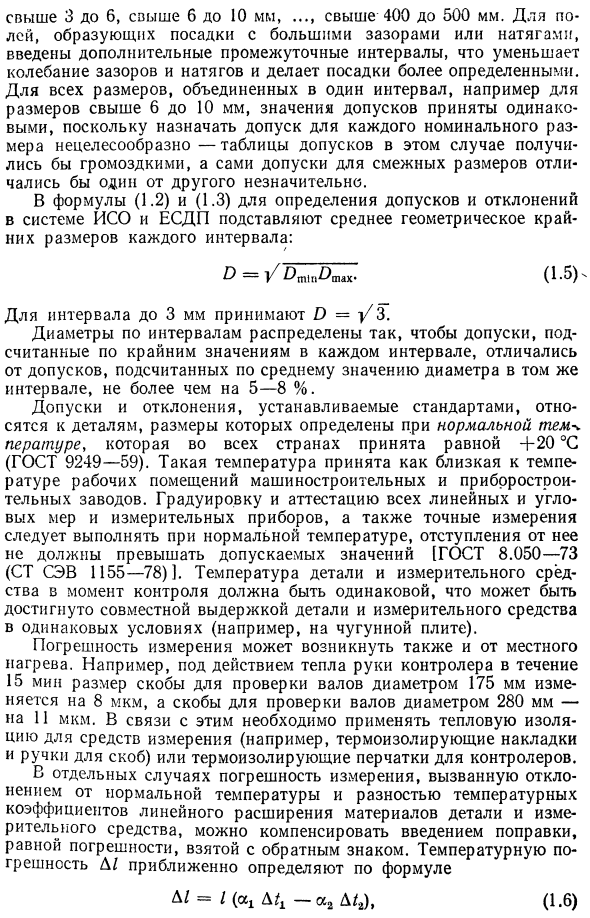
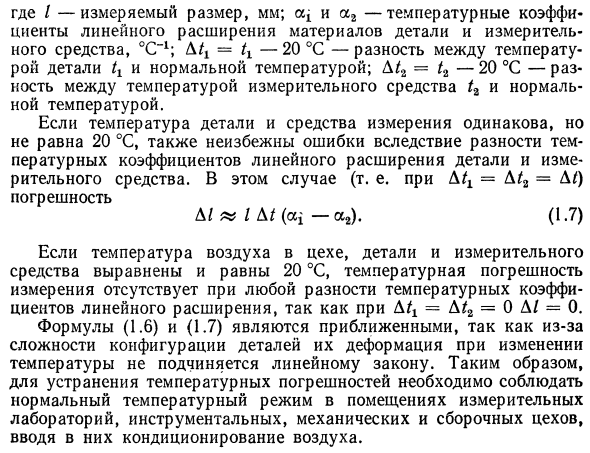

Единые принципы построения систем допусков и посадок для типовых соединений деталей машин и других изделий
- Согласно ГОСТ 25346-82 (СТ СЭВ 145 75), ГОСТ 25347 82 (СТ СЭВ 144 75), ГОСТ 25348 82 (СТ СЭВ 177 75), допуски и фитинги размером менее 1 мм являются ISO и Установлено с системой ESDP. Размеры до 500 мм, 500-3150 мм и выше, а также ESDP размеры от 3150 до 10000 мм также поддерживаются. В ESDP поля допусков с размерами менее 1 мм выделяются индивидуально. Система допусков и посадок представляет собой набор допусков и посадок, которые естественным образом построены на основе опыта, теоретических и экспериментальных исследований и разработаны в стандартной форме.
Система предназначена для выбора минимальных практических параметров, необходимых для общих допусков соединения и подгонки деталей машин, что позволяет стандартизировать режущие инструменты и калибры, а также для продукта и его частей. Это способствует достижению дизайна, изготовления и совместимости, что ведет к улучшению качества. В нашей стране ранее использовались системы допуска и посадки, но был выпущен ряд общесоюзных (ОСТ) и государственных (ГОСТ) стандартов. В настоящее время большинство стран мира применяют допуски ISO и системы посадки.
До или в процессе вычисления рекомендуется анализировать округляемые цифры, так как неосмотрительно выполненные округления могут исказить результат. Людмила Фирмаль
Система ИСО предназначена для унификации национальных допусков и систем посадки для продвижения международных технических связей в металлургической промышленности. Включая международные рекомендации ИСО в национальные стандарты, создаются условия для обеспечения совместимости аналогичных деталей, компонентов и изделий, изготовленных в разных странах. Страны-члены СЭВ перешли на базовые стандарты совместимости и унифицированной посадки (ESDP) и совместимости, основанные на стандартах и рекомендациях ISO. ESDP применяется к гладким допускам на размеры Элементы детали и посадка образуются, когда эти части соединены.
Основные стандарты совместимости включают допуски, такие как резьба, шестерни, конусы и системы посадки. Переход обусловлен необходимостью развития отраслевой специализации и сотрудничества в странах-членах СЭВ, развития международной торговли и устранения технических препятствий внутри и за пределами СЭВ. Это также повысит конкурентоспособность продукции стран-членов СЭВ на мировом рынке. Внедрение стандарта CMEA в Советском Союзе осуществляется через ГОСТ, соответствующий аналогичному стандарту CMEA.
В настоящее время расширяются советские международные торговые и научно-технические связи с другими государствами, и в этом контексте были введены допуски ISO и системы посадки. Поэтому на Волжском автозаводе в городе Тольятти автомобили jiggri в основном производятся с использованием допусков ISO и систем посадки. Кроме того, Япония использует рекомендации других международных организаций, основанные на этой системе, например, рекомендации Международной электротехнической комиссии, департамента МЭК-ИСО. Общие механические детали ISO и ESDP допуски и системы посадки построены на тех же принципах.
Посадки находятся в системе отверстий (CA) и системе валов (CB) (рисунок 1.3). Система посадочных отверстий — укажите N для приземления (рис. 1.3, а), где можно получить различные зазоры и помехи, подключив разные валы к основному отверстию. Система посадочных валов — посадочный главный вал (рис. 1.3.6), где могут быть соединены различные отверстия и отверстия для обеспечения различных зазоров и помех, обозначенных как I. Для всех посадок в системе отверстий низкое отклонение отверстия E1 = 0, то есть нижний предел допуска основного отверстия, всегда совпадает с нулевой линией.
Для всех посадок в системе валов верхнее отклонение основного вала составляет e = 0. Другими словами, верхний предел поля допуска вала всегда совпадает с нулевой линией. Поле допусков основного отверстия заложено, а поле допусков шпинделя расположено ниже нулевой линии, то есть в материале детали. Рисунок 1.3. Пример положения поля допуска в системе валов и системе валов (б) Система посадочных отверстий (А) Стенка отверстия и система стволов практически одинаковы. Выбор системы отверстия и вала для конкретной посадки зависит от конструктивных, технических и экономических соображений.
Точные отверстия обрабатываются с помощью дорогих режущих инструментов, таких как утопленные отверстия, развертки и протяжки. Каждый из них используется для обработки только одного размера отверстия с определенными допусками. Вал обрабатывается одним и тем же резцом или шлифовальным кругом независимо от размера. В этой системе номенклатура режущих инструментов, необходимых для сверления отверстий, меньше, потому что отверстия различных отверстий разных конечных размеров меньше, чем отверстия системы валов.
В связи с этим основное распространение получила дырочная система. Сокращая область применения, вы можете увеличить партию производимого инструмента, применить специализированное специализированное оборудование и увеличить производительность инструмента с минимальными затратами. Однако в некоторых случаях по конструктивным причинам, например, когда необходимо соединить несколько отверстий одинакового номинального размера с одним и тем же валом в разных посадках, необходимо использовать систему валов.
На рисунке 1.4 показано соединение ролика с посадкой штоком 3 и неподвижной вилкой 2. Вилку 2 рекомендуется использовать в соответствии с системой вала (рис. 1.4, в), а не системой отверстий (рис. 1.4, б). Шахтные системы еще более выгодны, когда такие детали, как стержни, оси и ролики, могут быть изготовлены с помощью точных холоднотянутых стержней без механической обработки внешней поверхности. При выборе системы посадки необходимо также учитывать допуски для стандартных и составных частей.
- Например, вал для соединения с внутренним кольцом подшипника качения всегда должен быть выполнен в соответствии с системой отверстий, а гнездо в корпусе для установки подшипника должно быть выполнено в соответствии с системой вала. Для построения системы допусков устанавливается единица допусков I (I). Единица допуска I (I) представляет собой меру точности, отражающую влияние технических, структурных и метрологических факторов, представляющую допуски в соответствии с номинальным размером, ограниченным допусками. Следующие допуски были установлены на основе исследований точности обработки цилиндрических металлических деталей для систем ISO и ESDP.
Для размеров до 500 мм 1 = 0,45 y-b 4-0,0010; (1,2) Для размеров свыше 500-10 000 мм 7 = 0,0040 4-2,1, (1,3) Где O — среднее геометрическое значение экстремальных значений в каждом интервале, мм. ( ) — допустимая единица измерения, микрон. Второе слагаемое в уравнении (1.2) учитывает погрешность измерения. Стойкость к любому качеству T = a1, (1.4) Где a — количество разрешенных единиц, которое зависит от качества, а не от номинального размера. В каждом продукте детали для разных целей изготавливаются с разной точностью. Для нормализации требуемого уровня точности устанавливаются квалификации для изготовления деталей и изделий (точность винтовых соединений, зубчатых колес и т. Д.).
Основные методы поверки размеров плоскопараллельных концевых мер: абсолютный интерференционный, относительный интерференционный, технический интерференционный и относительный контактный на интерферометрах, измерительных машинах, оптиметрах, оптикаторах и микрокаторах. Людмила Фирмаль
Качество (сходство с французским dia1He-качеством) означает набор допусков, характеризующихся постоянной относительной точностью (определяемой коэффициентом а) для всех номинальных размеров в этом диапазоне (например, от 1 до 500 мм). вы. Точность в пределах одного диапазона качества зависит только от номинального размера. ESDP устанавливает 19 квалификаций. 01, 0, 1, 2, …. 17 (наиболее точные квалификации 01 и 0 вводятся после введения квалификации
1). Качество определяет производственные допуски и, как следствие, определяет соответствующий метод и средства для обработки и контроля деталей машин. Уравнения (1.2) — (1.4) предназначены для определения приемлемого диапазона квалификации 5-17. Количество единиц допуска a для этих квалификаций равно 7, 10, 16, 25, 40, 64, 100, 160, 250, 400, 640, 1000 и 1600. Значение a для квалификации 6 является знаменателем p = 1.6. Эго означает, что при переходе от одного качества к следующему грубому качеству допуск увеличивается на 60%.
Для каждой из пяти квалификаций допуск увеличивается в 10 раз. В квалификации более точно 5 допуск 1T (аббревиатура 180 To1egaps-ISO допуск) определяется по формуле: 1T01 = = 0,3 4-0,0080; 1T0 = 0,5-4-0,0120; 1T1 = 0,8 4-0,0200; 1ТЗ = = 1Т11Т5; 1T2 = 1T1-1TZ; 1Т4 = 1ТЗ-1Т5, где допуск в микронах. Ой Для размеров менее 1 мм допуск 14-17 не назначается. Ряд допусков строится для каждого качества в соответствии с уравнением (1.4). Каждый допуск определяется соответствующим значением с разными размерами, имеющими одинаковую относительную точность.
Чтобы построить ряд допусков, каждый диапазон размеров делится на несколько интервалов по очереди. Если номинальный размер составляет от 1 до 500 мм, устанавливается 13 интервалов: максимум 3 От 3 до 6 или более, от 6 до 10 мм или более … от 400 до 500 мм или более. Дополнительный промежуточный интервал был введен для полей, которые образуют большие промежутки или посадки с помехами. Это уменьшает разрывы и колебания помех и делает посадку более четкой. Для всех размеров, комбинированных с одним интервалом, например, более 6-10 мм, нецелесообразно назначать допуски для каждого номинального размера, поэтому предполагается, что значение допуска одинаково — в этом случае.
Таблица допусков громоздкая, допуск смежных размеров один другой и немного другой. Уравнения (1.2) и (1.3), которые определяют допуски и отклонения для систем ISO и ESDP, заменяют среднее геометрическое значений экстремальных размеров для каждого интервала. P = From1 Ошм. (1.5). Для расстояний до 3 мм используется O = 3. Поскольку диаметр разделен на интервалы, допуск, рассчитанный по предельному значению каждого интервала, только на 5-8% отличается от допуска, рассчитанного по среднему диаметру того же интервала. Допуски и отклонения, установленные в стандарте, относятся к деталям, размеры которых измеряются при комнатной температуре, которая предполагается равной + 20 ° C (ГОСТ 9249-59) во всех странах.
Эта температура принимается как близкая к температуре рабочего помещения машиностроительного завода. Все линейные и угловые измерения, а также калибровка и сертификация измерительного оборудования и точные измерения должны выполняться при комнатной температуре. Отклонение не должно превышать допуск ГОСТ 8.050 73 (СТ СЭВ 1155 78) . Температура управляющей части и измерительного инструмента должна быть одинаковой. Это может быть достигнуто путем экспонирования детали и измерительного инструмента вместе в одинаковых условиях (таких как чугунная пластина). Кроме того, ошибки измерения могут возникать из-за локального нагрева.
Например, под воздействием тепла контроллера в течение 15 минут размер кронштейна, проверяющего вал диаметром 175 мм, будет меняться на 8 микрон, а размер кронштейна, проверяющего вал диаметром 280 мм, будет варьироваться на 11 микрон. В этом контексте необходимо применять изоляцию к инструментам (например, изоляционная прокладка и ручки для скоб) и изоляционные перчатки контроллера. В некоторых случаях погрешности измерения, вызванные отклонениями от нормальной температуры и температурного коэффициента линейного расширения деталей и материала средств измерений, компенсируются путем введения поправки, равной погрешности, взятой с противоположным знаком Я могу.
Погрешность температуры D приблизительно определяется по следующей формуле D = I (топор D — Аа Ду, (1-6) Где я размер измерения мм. sc и a2 — температурный коэффициент линейного расширения деталей и материала средств измерений, ° С-1; D x = -20 ° C — перепад температур Часть 4 и нормальная температура стекаются; D 2 = 2 20 ° C — Средства измерения 2 Разница между температурой 2 и нормальной температурой. Если температура детали и измерительного прибора одинакова, но не равна 20 ° C, ошибка неизбежна из-за разницы температурного коэффициента линейного расширения между деталью и измерительным прибором. В этом случае (т.е. D 2 = D 2 = D ) Ошибка D ID ( 1-ар). (1.7).
Если температура воздуха в мастерской, деталях и измерительном оборудовании выровнена и равна 20 ° C, D 2 = D 2 = 0 D = 0, то для разности температур коэффициент линейного расширения Нет ошибки измерения температуры. Уравнения (1.6) и (1.7) являются приближенными. Это связано с тем, что состав деталей является сложным, а деформация при изменении температуры не подчиняется линейному закону. Поэтому, чтобы исключить температурные ошибки, необходимо соблюдать нормальные температурные условия в помещениях измерительных лабораторий, оборудования, машин и сборочных заводов, а также вводить кондиционирование воздуха.
Смотрите также:
Принцип Тейлора | Исходные положения, используемые при производстве изделии |
Приборы с электроконтактными преобразователями | Агрегатирование машин и других изделий |