Оглавление:
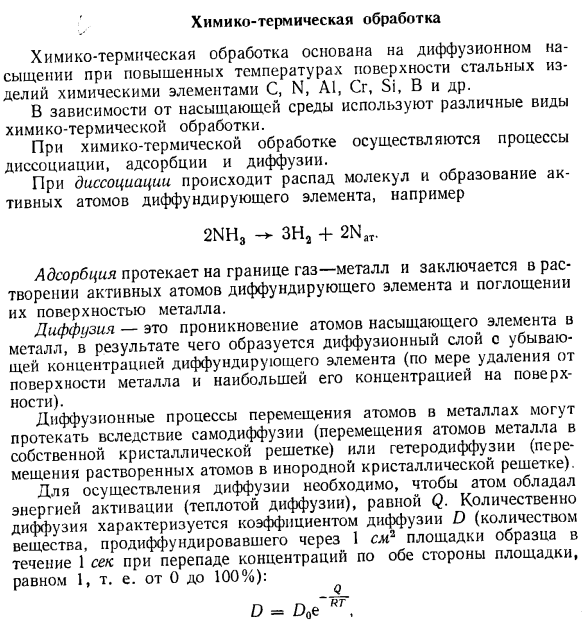
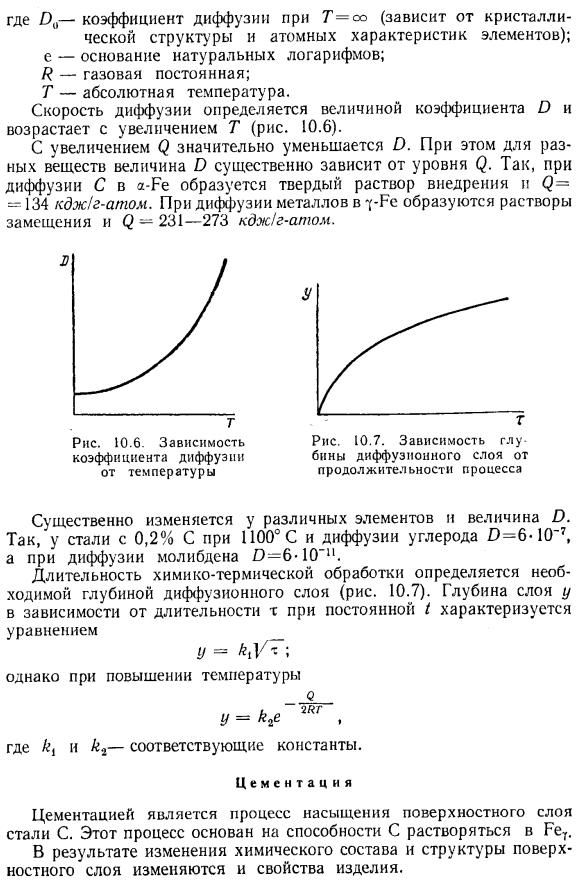
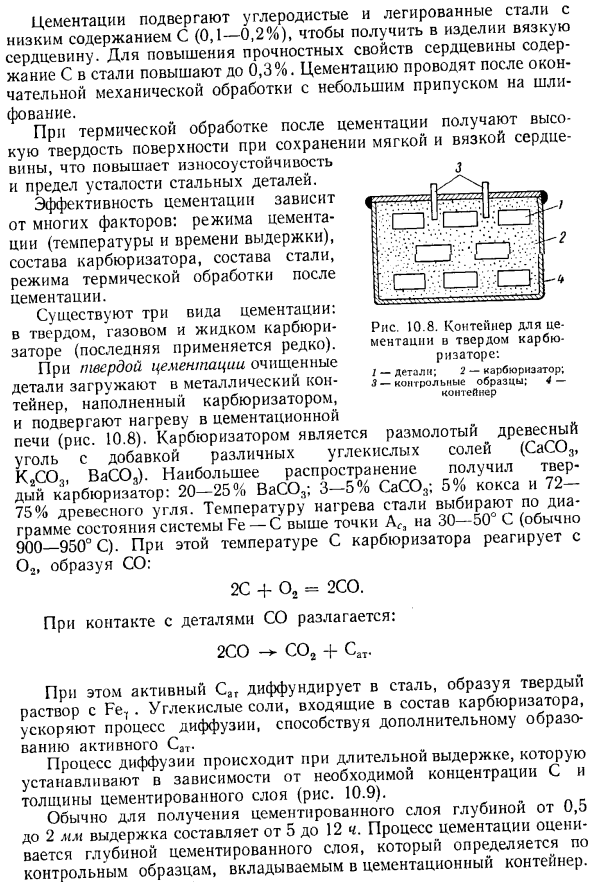
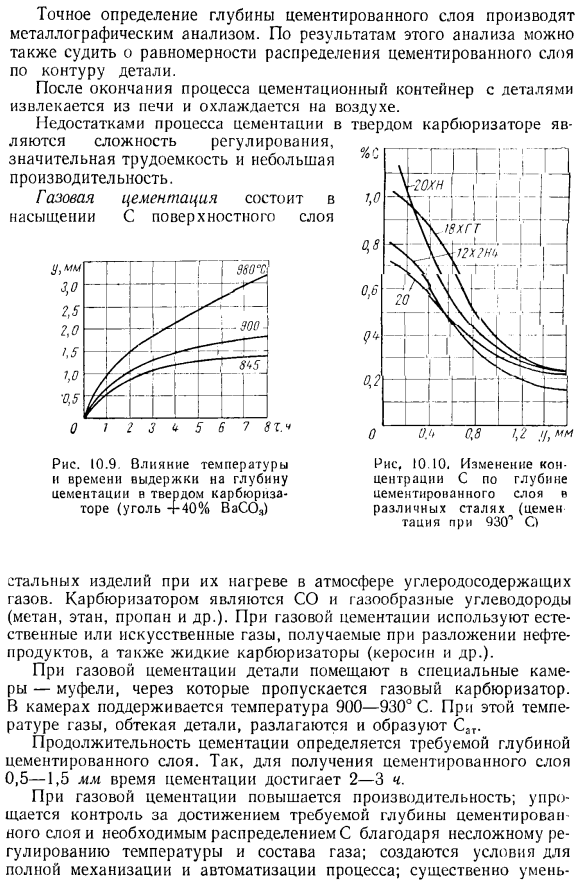
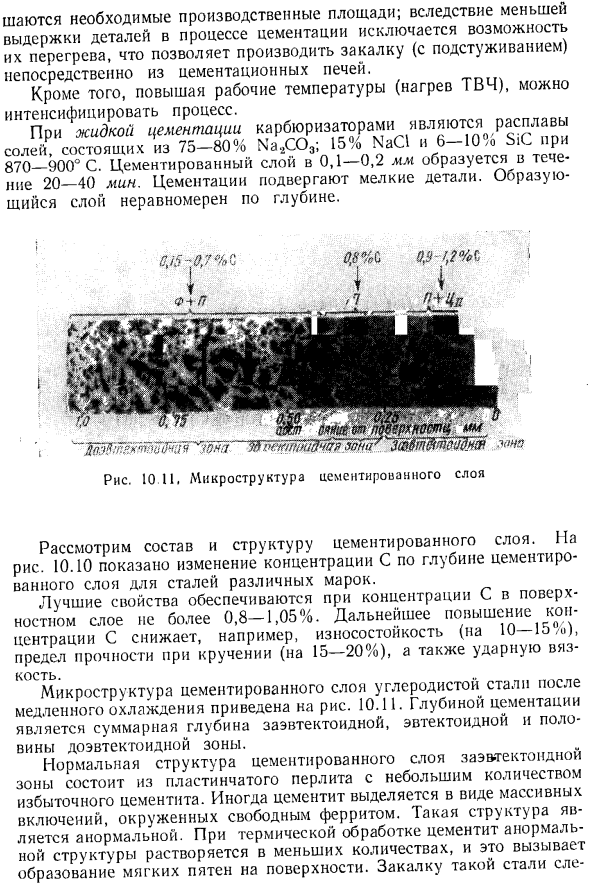
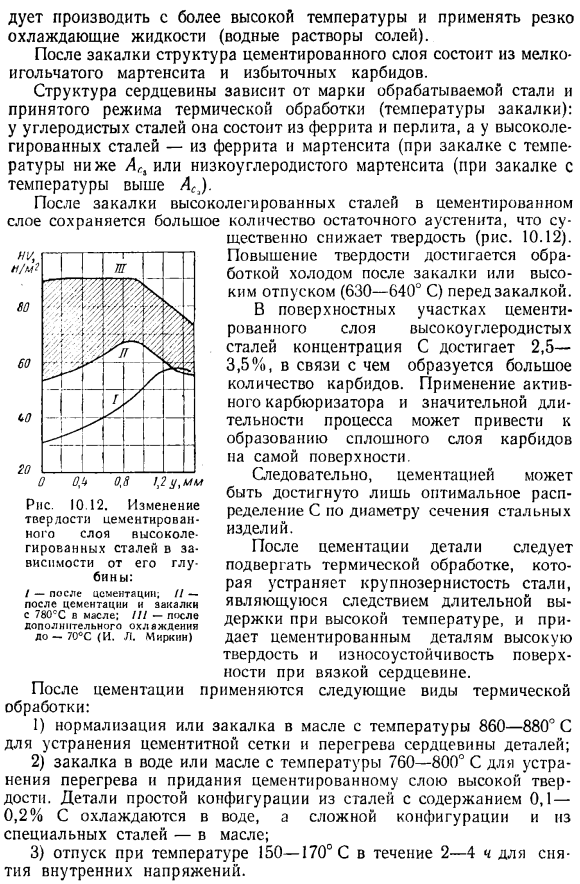
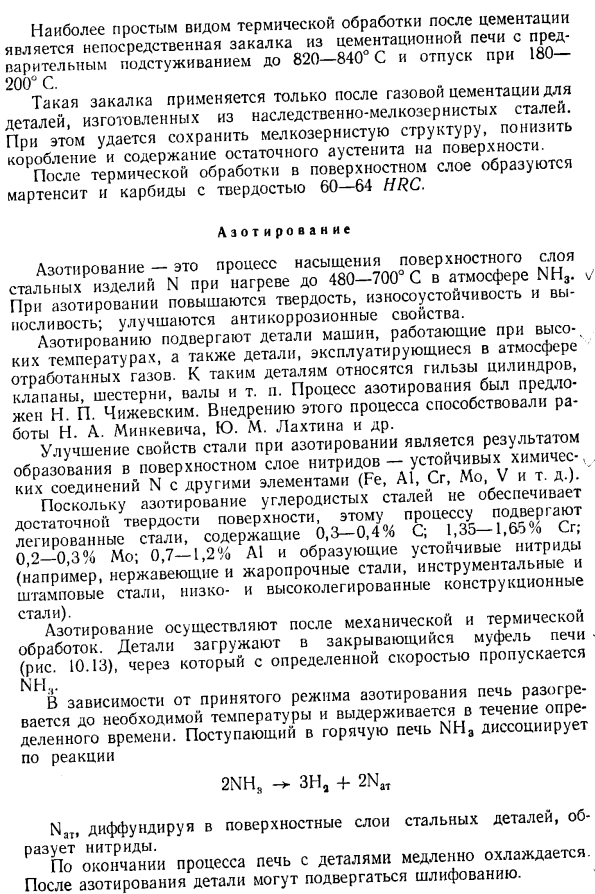
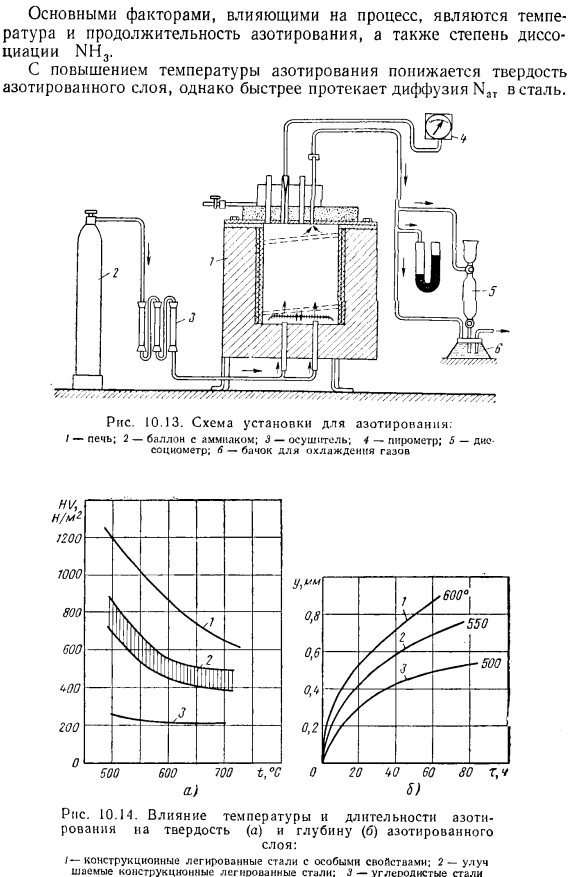
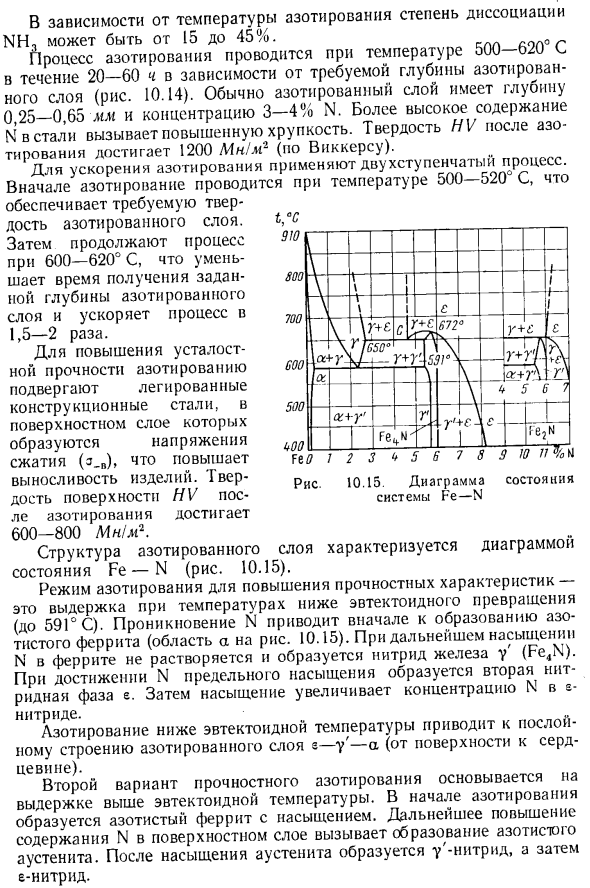
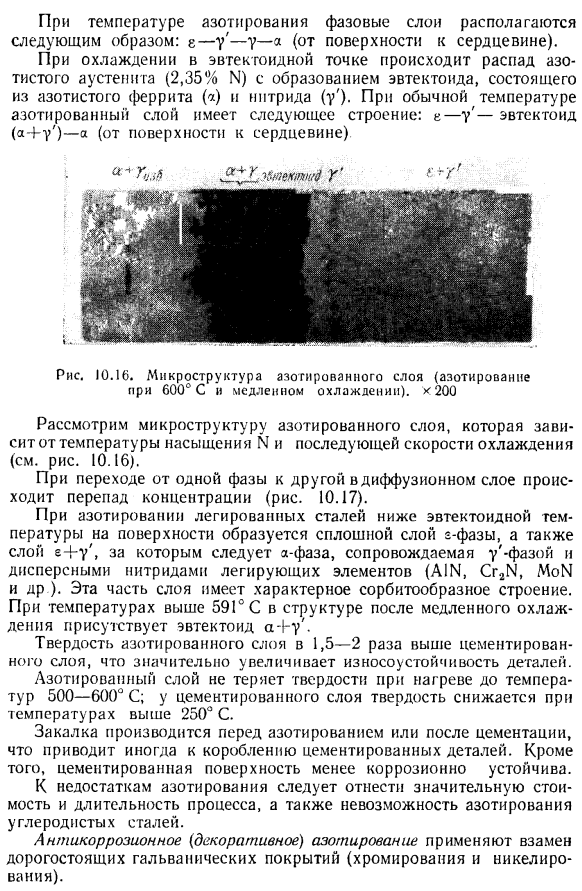
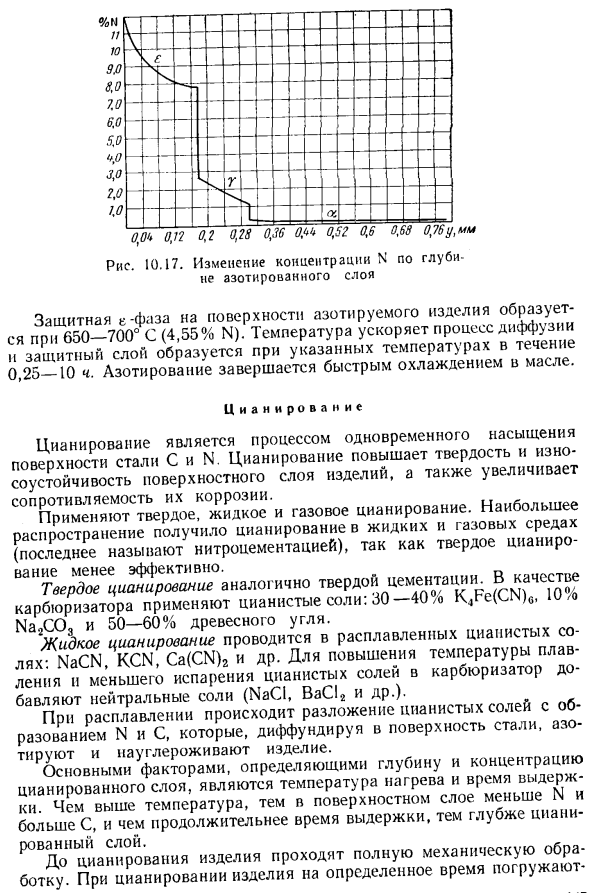
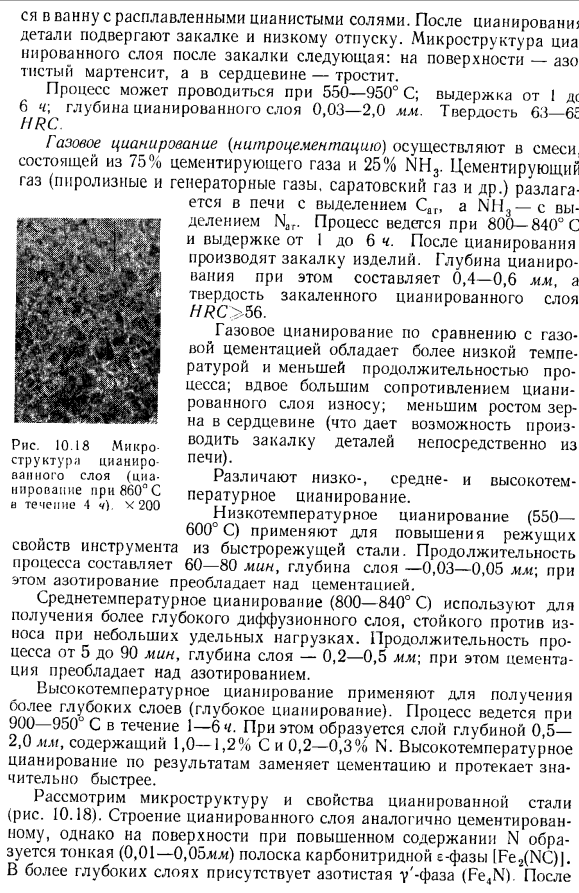
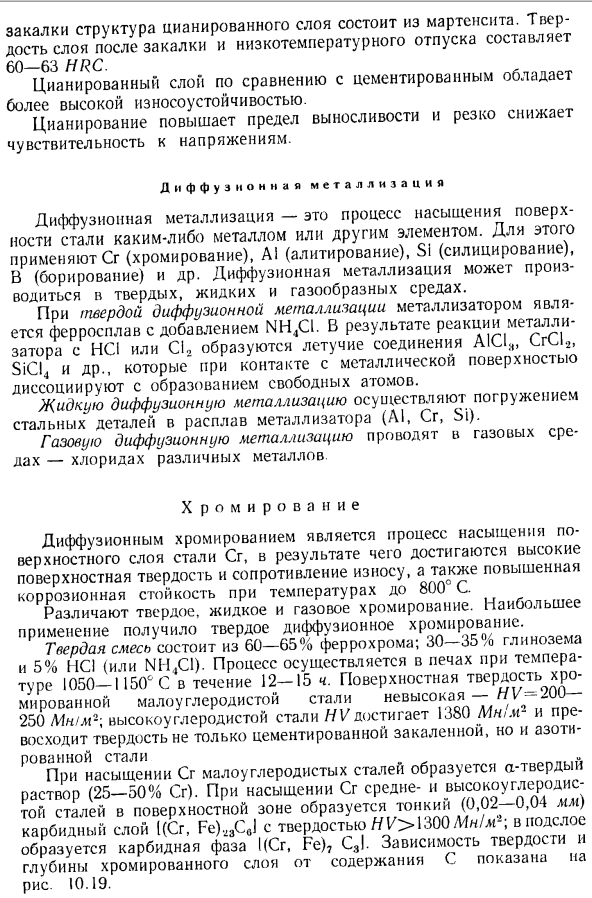
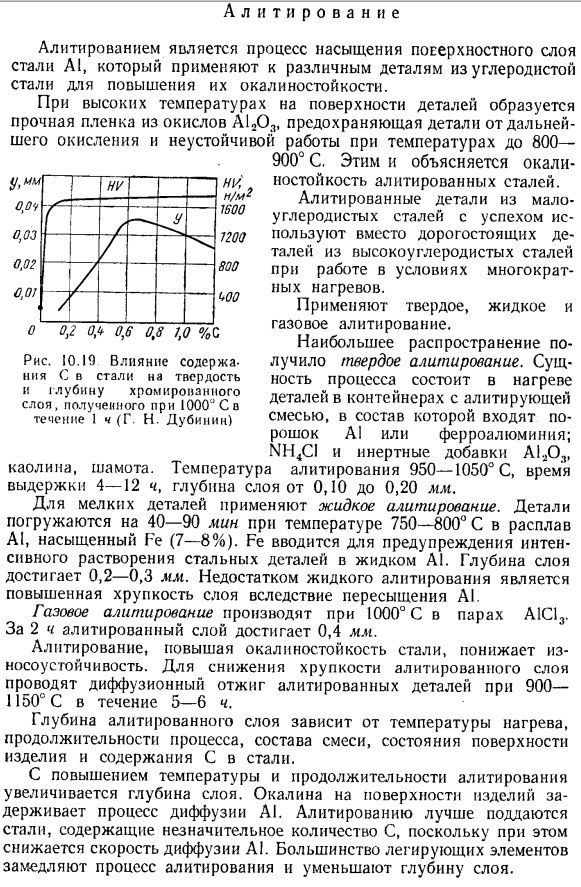
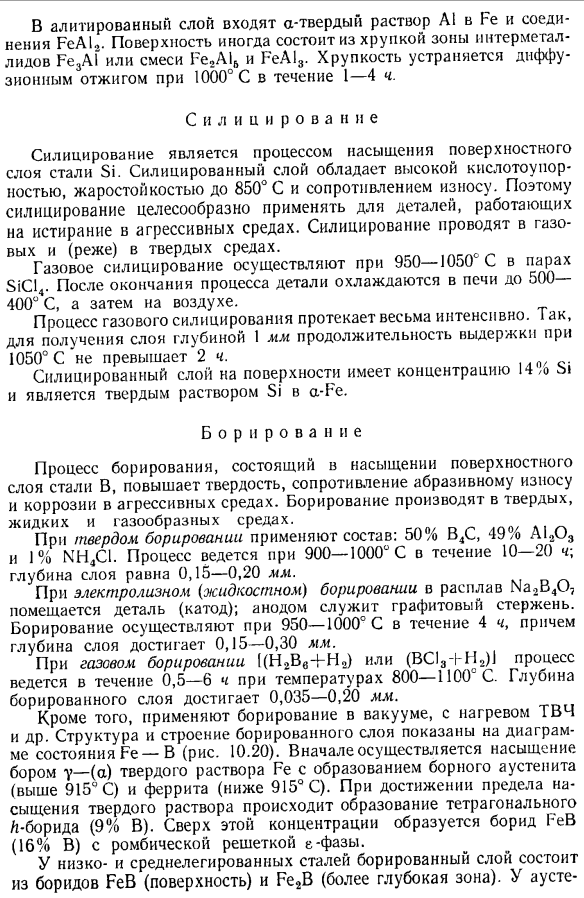
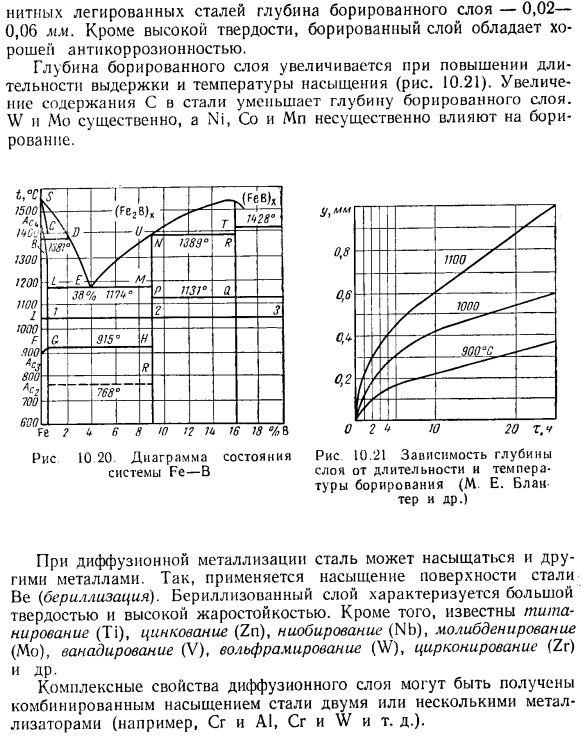

Химико-термическая обработка
- Химико-термическая обработка Химико-термическая обработка основана на диффузионном насыщении при повышенной температуре поверхности стальных изделий, содержащих химические элементы C, N, Al, Cr, Si, B и др. В зависимости от насыщенной среды применяются различные виды химико-термической обработки. В процессе химико-термической обработки осуществляются процессы диссоциации, адсорбции и диффузии.
При диссоциации молекулы разлагаются, образуя активные атомы диффузионных элементов, например 2NH3 — > 3H2 + 2NaT. Адсорбция происходит на границе раздела газа и металла, состоящей из растворения активных атомов диффузионных элементов и их поглощения поверхностью металла. Диффузия — это проникновение атомов насыщенных элементов в металл, в котором концентрация диффузных элементов снижается (по мере их удаления от поверхности металла и достижения максимальной концентрации на поверхности). Диффузионный процесс движения атомов в металле происходит либо путем самодиффузии (движение атомов металла в собственной кристаллической решетке), либо путем гетеродиффузии
(движение растворенных атомов в чужой кристаллической решетке). Людмила Фирмаль
Для получения диффузии атомы должны иметь энергию активации, равную Q (диффузное тепло). другими словами, от 0 до 100%): Q. КТ. D = = Доуд. Do-коэффициент диффузии при 7 =ω (в зависимости от кристаллической структуры и атомных свойств элемента). е-основание натуральных логарифмов; R — газовая постоянная. T-абсолютная температура. Скорость диффузии определяется величиной коэффициента D, которая возрастает с увеличением Т(рис. 10.6). Кроме того, для различных веществ величина D практически зависит от уровня Q.
таким образом, при диффузии C в a-Fe образуется твердый интерстициальный раствор, Q = 134 кДж / г-апум. При диффузии металла при 7-Fe образуется раствор замещения, Q составляет 231-273 кДж! Это атом G. Рис. 10.6.Температурная зависимость коэффициента диффузии Рис. 10.7.Зависимость глубины диффузионного слоя от продолжительности процесса Значение D также сильно варьируется в зависимости от различных элементов. Поэтому при 1100°C диффузия углерода со сталью при 0,2% C составляет£> = 6 «при 10’7, а диффузия молибдена-O = 6 −10». Продолжительность химико-термической обработки определяется необходимой глубиной диффузионного слоя (рис. 10.7).
- Глубина слоя y характеризуется следующим уравнением, зависящим от длительности m в константе t: Однако, когда температура повышается Q. Где h и K% — соответствующие константы. Цемент Цементация — это процесс, при котором поверхностный слой стали с насыщается. Этот процесс основан на способности C растворяться в Fe7. В результате изменения химического состава и структуры поверхностного слоя изменяются и свойства продукта. Углеродистая сталь и легированная сталь с низким содержанием C (0,1〜6,2%) цементируются для получения вязкого сердечника к product.
To увеличьте прочностные характеристики сердечника, содержание стали C увеличено до 0.3%.После окончательной обработки цементацию проводят с небольшим количеством припуска на полировку. поверхности при сохранении мягкого и вязкого сердечника, что повышает износостойкость и предел усталости стальной детали. 3. 7. ^ 2 Рис. 10.8 твердый карбюраторный цементный контейнер: I-детали; 2-карбюратор; 3-контрольный образец; 4-контейнер
При постцементационной термообработке достигается высокая твердость Людмила Фирмаль
Действие цемента зависит от многих факторов: режима цементирования(температуры и времени выдержки), состава цементирующего агента, состава стали, термической обработки после цементирования. Существует 3 вида отверждения: науглероживание твердого, газообразного и жидкого (последние используются редко). С твердым цементом очищенные детали помещают в металлическую емкость, заполненную цементирующими агентами и нагревают цементом Печь (рис. 10.8).Карбюратор используется для различных карбонатов (CaCO3、 K2CO3, BaCO3).Наиболее широко используется твердое вещество Карбюратор дыма:20-25%BaCO3; 3-5%CaCO3; Кокс 5% и уголь 72-75%.
Температура нагрева стали выбирается из фазовой диаграммы системы Fe-C, которая на 30-50°С (обычно 900-950°С) выше, чем Afj point. At эта температура, машина к обуглероживая реагирует с О2им для того чтобы сформировать ко. 2С + О2 = 2со. При соприкосновении с компонентами разбираются следующие компоненты: 2ПК-> СО2 +Сат В этом случае активные провесы диффундируют В железо, образуя твердый раствор вместе с Fe7.Карбонаты, входящие в состав цементирующего агента, ускоряют диффузионный процесс и способствуют дополнительному образованию активного грунта. Диффузионный процесс происходит при длительной выдержке, которая устанавливается в зависимости от требуемой концентрации С и толщины цементного слоя (рис. 10.9).
Для получения цементного слоя глубиной 0,5-2 мм выдержка обычно составляет 5-12 часов, а процесс цементирования оценивается по глубине цементного слоя, которая определяется контрольным образцом, введенным в цементный сосуд. Точное определение глубины связующего слоя производится методом металлографического анализа. По результатам этого анализа можно также определить равномерность распределения цементного слоя по контуру детали. После окончания процесса, цементный контейнер с деталями Достаньте его из духовки и охладите на воздухе.
Недостатки процесса цементации в твердых углеводных банках Это свидетельствует о сложности регулирования, значительной трудоемкости и низкой производительности труда. Газ-цемента Насыщенность поверхностного слоя Стальные изделия при нагреве в атмосфере углеродсодержащих газов. Науглероживающими агентами являются СО и газообразные углеводороды (метан, этан, пропан и др.).При использовании газоцементного, природного или искусственного газа, получаемого при разложении нефтепродуктов, а также жидких цементирующих агентов (например, керосина). Рис, 1010.
Изменение концентрации С по глубине цементного слоя различных сталей (цемент закрепляется при 930 ^ с) Рисунок 10.9 влияние температуры и времени выдержки на глубину цементации твердого карбюратора (уголь 4-40% Baco3) Во время газоцементной обработки детали помещают в специальные камеры-муфели, через которые проходит газовая цементировочная машина. Температура в камере поддерживается на уровне 900-930 ° C, и при этой температуре газ, обтекающий деталь, разлагается с образованием грунта.
Продолжительность цементирования зависит от глубины залегания необходимого цемента layer. So, чтобы получить цементный слой 0,5-1,5 мм, время цементирования достигает 2-3 м Впрыск газа повышает производительность. Простая регулировка температуры и состава газов позволяет легко контролировать достижение необходимой глубины цементного слоя и необходимого распределения С. создаются условия для полной механизации и автоматизации процесса. Значительно сократить
Требуемая производственная площадь; короткая выдержка деталей при цементации исключает возможность перегрева и может быть погашена (закалена) непосредственно из печи цементации. Кроме того, процесс может быть улучшен за счет повышения рабочей температуры (нагрев HDTV). При жидкой цементации карбюратор представляет собой расплавленную соль, состоящую из 75-80% Na2CO3. При 870-900°15%NaCl и 6-10%SiCC. В течение 20-40 минут образуется цементный слой толщиной 0,1-0,2 мм.
Мелкие детали подвергаются цементации. Получившийся слой неравномерен по глубине. 10 11, микроструктура цементного слоя Рассмотрим состав и структуру цементного слоя. На рисунке 10.10 показано изменение концентрации С по глубине цементного слоя различных марок стали. Наилучшие свойства обеспечиваются при концентрации С в поверхностном слое не более 0,8-1,05%. При дальнейшем увеличении концентрации С, например, снижается износостойкость (10-15%), прочность на растяжение (15-20%) и ударная вязкость. Микроструктура слоя цементированного карбида после отжига показана на рисунке. 10.11.
Глубина залегания цемента равна сумме половины глубины заэвтектоидных, эвтектоидных и заэвтектоидных зон. Нормальная структура цементирующего слоя в гиперэвтектоидной зоне сложена слоистым перлитом с небольшим количеством избыточного цементита. Иногда цементит выделяется в виде гигантских включений, окруженных свободным ферритом. Такая структура ненормальна. В процессе термообработки цементит с необычной структурой растворяется в меньшем количестве, что приводит к образованию мягкого пятна на поверхности.
Закалки такой стали практически нет Количество остаточного аустенита. Это приводит к значительному снижению твердости (рисунок 10.12).Повышение твердости достигается холодной обработкой после закалки или обработкой при высоких температурах (630-640°C) до hardening. In поверхностный плоский слой стали, концентрация C достигает 2.5-3.5%, поэтому большое количество карбида сформировано. При использовании активных науглероживающих агентов и необходимости значительного времени обработки на самой поверхности образуется непрерывный карбидный слой.
Необходимо применять жидкость (водный раствор соли), которая получается из более высокой температуры и резко охлаждается. После отверждения структура цементного слоя состоит из тонкого игольчатого мартенсита и избыточного карбида. Структура сердечника зависит от марки обрабатываемой стали и принятого режима термической обработки (температуры закалки): для углеродистой стали он состоит из феррита и перлита, а для высоколегированной стали он состоит из феррита и мартенсита (если он должен быть закален от температуры L, или если он должен быть подвергнут от).
После твердеть стали высок-сплава в слое цемента, большой Площадь цемента высокоуглеродистая Рис. 10.12.Изменение твердости связующего слоя высоколегированной стали в зависимости от глубины: / — После цементирования; Таким образом, цементацией можно добиться только оптимального распределения С, но диаметр поперечного сечения стали отличается. После сопряжения деталь необходимо подвергнуть термообработке. Это позволяет удалить крупнозернистую сталь, вызванную длительным воздействием высоких температур, придавая соединениям поверхностей с вязким сердечником высокую степень твердости и износостойкости.
После цементирования применяются следующие виды термообработки: 1) масло унифицировано или погашено от температуры 860-880°C для того чтобы исключить cementitious сетку и перегревать части сердечника. 2) гасить водой или маслом от температуры 760 до 800°C, чтобы предотвратить перегрев и придать цементному слою высокую твердость. Простые детали конфигурации, изготовленные из стали с содержанием 0,1-0,2% C, охлажденной водой и изготовленные из специальной стали сложные детали конфигурации-с маслом; 3) закаленный на 150 до 170°C температура 2-4 часа для того чтобы сбросить внутреннее усилие. После цементации и отверждения от 780°С в масле:/ / / после дополнительного охлаждения до — 70°с (И. Л. Миркин.)
Простейшей постцементационной термообработкой является прямая закалка из цементационной печи, которая подвергается предварительному грунтованию при 820-840 ° С и отпуску при 180-200 ° С. Такое упрочнение применяется только после газосемянной обработки деталей, изготовленных из генетически тонких steel. At в то же время, он может поддерживать мелкозернистую структуру и уменьшать поверхностное искривление и остаточное содержание аустенита. После термической обработки, поверхностный слой сформирован мартенсита и карбида 60-64 HRC.
Азотирование Азотирование-это процесс, в котором поверхностные слои стальных изделий N насыщаются при нагреве до 480-700°С в атмосфере NH3. \ / Азотирование повышает твердость, износостойкость и долговечность. Улучшает антикоррозионные. Азотированию подвергается высокая работоспособность механических деталей. Температура, и части которые работают в атмосфере выхлопного газа. К таким деталям относятся гильзы цилиндров, клапаны, шестерни и валы. Процесс азотирования такой же, как у N. P. s. It было предложено Чижевским.
Реализация этого процесса зависит от Н. А. Минкеевича, Ю. М. деятельность научно-исследовательской группы была стимулирована. Улучшение свойств стали при азотировании происходит в результате образования нитридов в поверхностном слое-стабильного химического вещества G. N соединения с другими элементами (Fe, Al, Cr, Mo, V и др.).
Азотирование углеродистой стали не обеспечивает достаточной поверхностной твердости, поэтому этот процесс применяется к легированной стали, содержащей от 0,3 до 0,4% C. 1.35-1.65%Cr; 0.2-O, 3?6 МО; образование 0,7 ~ 1,2% А1 и стабильных нитридов(например, нержавеющая сталь и жаропрочная сталь, инструментальная сталь и литейная сталь, низколегированная и высоколегированная конструкционная сталь). Азотирование проводят после механической и термической обработки. Детали загружаются в муфель закрывающей печи(рис. 10.13).NH проходит с постоянной скоростью.
В зависимости от принятого способа азотирования печь нагревают до необходимой температуры и выдерживают в течение определенного времени. NH3 в высокотемпературной печи диссоциируется по реакции 2NHS — >ЗН24-2N» НАР, который диффундирует в поверхностный слой стальной детали, образует нитрид. В конце процесса печь с деталями медленно охлаждают. После азотирования детали могут быть измельчены. Основными факторами, влияющими на процесс, являются температура и время азотирования, степень диссоциации NH3.
Чем выше температура азотирования, тем тверже будет азотирующий слой, но тем быстрее происходит диффузия NaT в сталь. Рис. 10.13.Схема установки азотирования. / — Печи; 2-баллоны, содержащие аммиак; <3-осушители воздуха; 4-пирометры; 5-Дис-корреляторы; 6-емкости для охлаждения газов Рис. 10.14.Влияние температуры и времени азотирования на твердость (а) и глубину (б) азотированного слоя: / — Конструкционная легированная сталь со специальными свойствами; 2-исследование конструкционной легированной стали. 3-углеродистая сталь 0 20 40 60 80 т, ч 8.)В зависимости от температуры азотирования, степень диссоциации НФЛ составляет 15-45%.
Процесс азотирования осуществляется при температуре 500-620°С в течение 20-60 часов, в зависимости от глубины требуемого слоя азотирования(рис. 10.14).Обычно глубина азотированного слоя составляет 0,25-0,65 lel<, а концентрация составляет 3-4%N. высокое содержание N в стали повышает хрупкость. Твердость HV после азотирования достигает 1200 МН / м2(по Виккерсу). Для ускорения азотирования используются 2-х ступенчатые процессы. Сначала азотирование проводят при температуре от 500 до 520°С, что обеспечивает необходимую твердость. Он достигает азотированного слоя. Затем процесс продолжается при 600-620 ° С.
Это сокращает время получения азотированного слоя на заданной глубине и ускоряет процесс в 1,5〜2 раза быстрее. Рис. 10.15.Диаграмма состояния системы It-N Для повышения усталостной прочности легированную конструкционную сталь обрабатывают азотированием, формируют сжимающие напряжения на ее поверхностном слое (а. п.), что повышает долговечность изделия. Поверхностная твердость HV после азотирования достигает 600-800 МН / м2. Структура нитридного слоя характеризуется диаграммой состояния Fe-N(рис. 10-15).
Режим азотирования для повышения прочностных характеристик- Это воздействие эвтектоидного превращения при более низких температурах (до 591°C). При проникновении N в первую очередь образуется азотсодержащий феррит(область а на рис. 10-15).При дальнейшем насыщении N не растворяется в Феррите, и образуется нитрид железа y ’(Fe4N). Когда N достигает максимального насыщения, образуется 2-я нитридная фаза e. Нитриды. Нитридирование ниже температуры эвтектоида приводит к слоистой структуре азотированного слоя, g_y’ — a (от поверхности до ядра). 2-я вариация прочности азотирования основана на воздействии выше эвтектоида temperature. At начало азотирования, нитрит-феррит образуется в насыщенном state.
As содержание N в поверхностном слое увеличивается еще больше, образуется азотный аустенит. После насыщения аустенита образуются y ’ — нитриды, после чего Нитриды. При температуре азотирования фазовый слой располагается следующим образом: e-y’ — y-a(от поверхности к сердцевине). При охлаждении в точке эвтектоида аустенит азота (2,35% N) разлагается с образованием совместного осаждения нитритного феррита (a) и нитрида (y’). при нормальной температуре структура азотированного слоя выглядит следующим образом: e-y ’- эвтектоид (a4-y’) — a (от поверхности к сердцевине) Рисунок 10. 16.Микроструктура азотированного слоя (азотированного при 600°С при медленном охлаждении), х 200 Рассмотрим микроструктуру азотированного слоя, которая зависит от температуры насыщения N и последующей скорости охлаждения(см. Рисунок 10.16).
При переходе диффузионного слоя из одной Фазы в другую наблюдается разница в концентрации (рис.10.17). Азотирование легированной стали ниже температуры эвтектоида создает непрерывную s-фазу, e-bj, a-фазу, y ’ — фазу и дисперсионный нитрид легирующих элементов (AIN, Cr2N, MoN и др.) на поверхности. 。Эта часть слоя имеет характерный сорбит-как структура. При температурах выше 59 ° C, после медленного охлаждения, происходит совместное осаждение а-скважины в структуре.
Твердость азотированного слоя в 1,5-2 раза выше, чем цементного слоя, что значительно повышает износостойкость деталей. Азотированный слой не теряет своей твердости даже при нагревании до температуры 500-600u. твердость цементного слоя снижается при температурах выше 250°C Упрочнение проводят до азотирования или после цементации. Это может вызвать деформацию цементного камня components. In кроме того, коррозионная стойкость поверхности соединения низкая. К недостаткам азотирования относятся огромная стоимость и длительность процесса, а также невозможность азотирования углеродистой стали.
Вместо дорогостоящего гальванического покрытия (хромирование и никелирование) используется антикоррозионное (декоративное) азотирование. Рис. 10.17.Изменение концентрации N в глубине Не азотированных слоев Защитная b-фаза поверхности азотированного продукта образуется при 650-700 ° С(4,55%N).Температура ускоряет процесс диффузии, при указанной температуре защитный слой образуется в течение 0,25-10 часов, а быстрое охлаждение в масле завершает азотирование.
Цианид. Цианирование — это процесс одновременного насыщения поверхностей стали С и N. Цианирование повышает твердость и износостойкость поверхностного слоя изделия, а также стойкость к коррозии. Используются цианиды твердого, жидкого и газового происхождения. Цианирование в жидких и газообразных средах является наиболее распространенным из-за низкого эффекта твердого цианирования(последнее называется мягким азотированием). Твердотельное цианирование подобно твердому телу carburization. As используются цементирующие агенты, цианидные соли: 30-40%K4Fe (CN) 0, 10% Na2CO3 и 50-60% древесного угля. Жидкое цианирование проводят расплавленными солями цианидов (NaCN, KCN, Ca (CN)2 и др.).
Нейтральные соли (NaCl, BaCl2 и др.) добавляются в карбюратор для повышения температуры плавления цианидной соли и подавления испарения. В процессе плавки происходит разложение цианидных солей, что приводит к образованию N и C. Они диффундируют на поверхность стали, азотируя и обугливая продукт. Основными факторами, определяющими глубину и концентрацию слоя цианида, являются температура нагрева и время экспозиции. Чем выше температура, тем ниже N поверхностного слоя, тем дольше время экспозиции и тем глубже цианирующий слой. Перед цианидом продукт подвергается полному механическому воздействию treatment. In в случае цианирования продукт погружают на определенное время в ванну, содержащую расплавленные соли цианида.
После цианирования деталь закаливают и доводят до более низкой температуры. Тонкая структура упрочненного слоя после закалки выглядит следующим образом. На поверхности находится мартенсит с нитритом, а на ядре-трооцит. Этот процесс можно выполнить на 550-950°С. Выписка из I ДС в течение 6 часов. Глубина слоя цианида 0.03 ~ 2.0 мм. Твердость 63-6s HRC. Цианирование газа (мягкое азотирование) осуществляется смесью 75% цементного газа и 25% NH3.Цементирующий газ (пиролизный и добываемый газ, Саратовский газ и др.) разлагается в печи при высвобождении Cflr, и NIL разлагается при высвобождении Naf.
Этот процесс бежит на 800-840°С и сохранен для I-6 hours. In в этом случае глубина цианирования составляет 6,4 мм, а твердость упрочненного цианидного слоя составляет NWF> 56. Рисунок 10. микроструктура 18 слоев цианида (860 ° C, 4 часа цианирования} X 200 По сравнению с газификацией, газификация имеет более низкую температуру и короткое время обработки. В 2 раза выше износостойкость цианидного слоя.
Рост зерна сердцевины невелик (это позволяет затвердевать детали непосредственно из печи). Различают низкую, среднюю и высокую температуру цианирования. Низкотемпературное цианирование (550-600°C) используется для улучшения резания быстрорежущей стали. Продолжительность 60-80 минут, глубина слоя-0,03-0,05 мм Это азотирование имеет приоритет над цементацией. Свойства инструмента. Процесс Средняя температура цианирования (800-840 ° С) используется для получения более глубокого диффузионного слоя, способного выдерживать износ при низких удельных нагрузках.
Продолжительность процесса 5-90 минут, глубина слоя 0,2-0,5 мм; в этом случае цемент имеет преимущество перед азотированием. Высокая температура цианирования используется для получения более глубоких слоях(глубокого цианирования).Этот процесс проводят при 900-950°С в течение 1-6 часов, при этом образуется слой С от 1,0 до 1,2%, N от 0,2 до 0,3%, глубиной от 0,5 до 2,0 мм. Согласно полученным результатам, высокотемпературное цианирование заменяет цементацию и прогрессирует значительно быстрее.
Рассмотрим микроструктуру и свойства цианистой стали (рис. 10.18).Структура цианидного слоя аналогична структуре цементного слоя, но на поверхности с повышенным N образуется тонкая (0,01-0,05 dy) полоса нитрида углерода е-фазы IFe2 (NC content. In в более глубоких слоях имеется гамма-фаза (Fe4N) азота. Позже Закалка структура цианидного слоя состоит из мартенсита. Твердость слоя после закалки и низкотемпературного отпуска составляет 60-63 HRC.
По сравнению с цементным слоем цианидный слой обладает более высокой износостойкостью. Цианирование увеличивает предел выносливости и резко снижает чувствительность к стрессу. Диффузионная металлизация Диффузионная металлизация — это процесс насыщения поверхности стали металлом или другими элементами. Для этого используют Cr (хромирование), AI(Алитизация), Si (силицирование), B (боронирование) и др. используются, причем диффузионная металлизация может осуществляться в твердых, жидких и газообразных средах.
При твердотельной диффузионной металлизации металлизатор представляет собой ферросплав с добавлением NH4Cl. As результат реакции металла с HCl или C12, летучими соединениями A1C1a, CrC1. 2, SiCl4 и др. образуются, и когда они вступают в контакт с поверхностью металла, они диссоциируют с образованием свободных атомов. Жидкая диффузионная металлизация осуществляется погружением металлических деталей в металлизированный расплав (AI, Cr, Si).
Газодиффузионная металлизация осуществляется в газовой среде-хлоридах различных металлов Хромирование Диффузионное хромирование — это процесс, при котором поверхностный слой стали Cr насыщается, и в результате достигается не только высокая поверхностная твердость и износостойкость, но и повышенная коррозионная стойкость при температурах до 800°C. Различают твердое, жидкое и газообразное хромирование. Наиболее широко применяется твердое диффузионное хромирование. Твердая смесь состоит из 60-65% феррохрома. 30-35% глинозема и 5% F ICI (или NH4Cl).Этот процесс проходит в печи при температуре 1050-1ol50°C в течение 12-15 часов.
Покрытая хромом твердость поверхности слабой стали низко-ХВ-20 () −250 МН / м2, высокоуглеродистая сталь ХВ достигла 1380 МН ’ м2 и превышает твердость затвердетой затвердетой стали При насыщении Cr мягкой сталью образуется a-твердый раствор (25-50%Cr).При насыщении Cr средними и высокоуглеродистыми сталями в поверхностной зоне образуется тонкий (0,02-0,04 лм<) карбидный слой / (Cr, Fe) 23cj твердостью 1300 А4 Li2.In подслои Образуется ли карбидная фаза l(Cr, Fe)? С31.На рисунке показана зависимость твердости и глубины хромового слоя от содержания C. 10.19. Подщелачивание — это процесс насыщения поверхностного слоя стали L1, нанесенного на различные части углеродистой стали, для повышения окалины сопротивления.
При высоких температурах на поверхности детали образуется прочное покрытие из оксида а12о3, которое дополнительно окисляет деталь и защищает ее от нестабильной работы при температурах до 800-900°С. Рисунок 10: 19 C Содержание и эффекты глубины 1000е слоев Стальная твердость хромирование При работе в условиях многократного нагрева вместо дорогостоящих деталей из высокоуглеродистой стали успешно применяются детали с алюминиевым покрытием из низкоуглеродистой стали.
Приложите алумизатион твердого тела, жидкости и газа. Наибольшее распространение получил надежный псевдоним. Суть этого процесса заключается в нагревании деталей в контейнере с алюминизированной смесью, содержащей АИ-порошок или Ферроалюминий. NH4CI и инертная добавка L12OL、 0,2-0,3 Аква. Недостатком жидкостной арихизации является повышенная хрупкость слоев из-за пересыщения А1. 1 час (Г. Нет. Дубинин.) Глинистая текстура. Температуру Altizer составляет 950-1050 ° с, Время-4-12 часов, глубина слоя составляет 0,10-0,20 мм. Каолин экстракт Для мелких деталей используется жидкое алюминирование.
Для получения деталей пропитайте его насыщенным А1 расплавом (7-8%) при температуре 750-800 ° С в течение 40-90 минут. Fe вводится в жидкость A1 для предотвращения интенсивного растворения железных и стальных деталей. Глубина слоя Газ A1c13 усваивается при 1000°C в паре. Через 2 часа слой глинозема достигает 0,4 мм. Окисление увеличивает содержание оксида железа и литой стали и уменьшает износ resistance. In для снижения хрупкости слоя алюминиевого покрытия проводят диффузионный отжиг деталей алюминиевого покрытия при температуре 900-1150°с в течение 5-6 часов.
Глубина слоя Арита зависит от температуры нагрева, продолжительности процесса, состава смеси, состояния поверхности изделия и содержания С в стали. По мере того как температура и продолжительность спирта увеличиваются, глубина слоя увеличивается. Окалина на поверхности изделия замедляет процесс диффузии А1.Сталь с небольшим количеством C подходит для сглаживания. Это связано с тем, что он снижает скорость диффузии ИИ. Большинство легирующих элементов замедляют процесс наложения и уменьшают глубину слоя. Твердый раствор AI, содержащийся в соединениях Fe и FeAL, поступает в слой оксида алюминия.
Поверхность может состоять из хрупкой зоны Fe3Al pntermetallides или смеси Fe2Al6 и G’ea13. Диффузионный отжиг при 1000°C в течение 1-4 часов устраняет уязвимость. О И И и о е Обработка кремния-это процесс, посредством которого поверхностный слой стали Si насыщается. Кремни-обработанный слой имеет высокую стойкость к действию кислот, сопротивление жары до 850°C, и сопротивление износа. Поэтому рекомендуется применять силицирование для деталей, которые действуют на истирание в жестких условиях. Силицирование проводят в газовой и твердой средах (хотя и не очень часто). Газовой силикатизации осуществляется при 950-1050 ° C в SiCl4 пара.
После окончания процесса детали охлаждают в духовке до 500-400 ° C, после чего их охлаждают воздухом. Процесс силицирования газа протекает очень интенсивно. Поэтому для получения глубины 1 мм время выдержки при 1050°с не превышает 2 часов Обработанный кремнием слой поверхности имеет концентрацию 14% Si и представляет собой твердый раствор a-Ge Si. Это скучно. Процесс борирования заключается в насыщении поверхностного слоя стали B, повышении твердости, износостойкости и коррозионной стойкости в жестких условиях эксплуатации.
Борирование проводят в твердых, жидких и газообразных средах. Для твердых боратов используется состав B4C 50%, Al2O3 49%, NH4C1 1%.Этот процесс протекает при 900-1000°С в течение 10-20 часов, а глубина слоя составляет 0,15-0,20 мм. Na.2B4O? Электролиз (жидкость) в растворе Бора помещают в среднюю часть (катод).Графитовый стержень выполняет функцию анода. Борирование проводят при температуре 950-1000С в течение 4 часов, а глубина слоя достигает 0,15-0,30 мм. Для газа boronation1(Н2Вв-lн2) или (bcl8 hh2) J процесс проходит при температуре 800-1100С в течение 0,5-6 часов.
Глубина слоя оксида бора достигает 0,035-0,20 мм. Кроме того, соединение бора применяют в вакууме, при нагревании высокочастотных частиц и др. Структура и строение слоя соединения бора показаны на диаграмме состояния Fe-B(рис. 10.20).Первоначально бор y — (a) насыщают твердым раствором Fe с образованием боратного аустенита (915°C или выше) и феррита (915°C или ниже).При достижении предела насыщения твердого раствора происходит образование тетрагонального L-борида (9%B).При превышении этой концентрации в ромбической решетке е-фазы образуются бориды железа(16% B).
В низколегированных и среднелегированных сталях слои Бора состоят из боридов FeB (поверхностных) и Fe2B (более глубоких областей). в аустенитных легированных сталях слой Бора имеет глубину 0,02-0,06 mm. In добавление к высокой твердости, слой Бора имеет превосходную коррозионную устойчивость. По мере увеличения времени выдержки и температуры насыщения глубина слоя оксида бора увеличивается(рис. 10.21). по мере увеличения содержания С в стали глубина слоя Бора уменьшается. W и Mo важны, но Ni, Co и Mn мало влияют на Бор. Рисунок 10 20.
Диаграмма состояния системы Fe-B Около 2 10 20 т, ч Рисунок 10. зависимость глубины 21 слоя от продолжительности и температуры восстановления Бора (ME E. Blanoner et al.) При диффузионной металлизации сталь может насыщаться другими металлами. Именно поэтому применяется насыщение поверхности стали Be (belis). бериллированный слой характеризуется высокой твердостью и высокой теплопроводностью resistance. In добавление, титрование (Ti), цинкование(Zn), ниобий (Nb), молибден (Mo), ванадий (U), вольфрам (W), цирконизация (Zr) и др. известны.
Сложные свойства диффузионного слоя можно получить путем объединения стали с 2 или более металлизаторами (например, Cr и A1, Cr и W) и насыщения их.
Смотрите также:
Поверхностный наклеп | Термомеханическая обработка |
Общая характеристика влияния легирующих элементов | Поверхностная закалка |