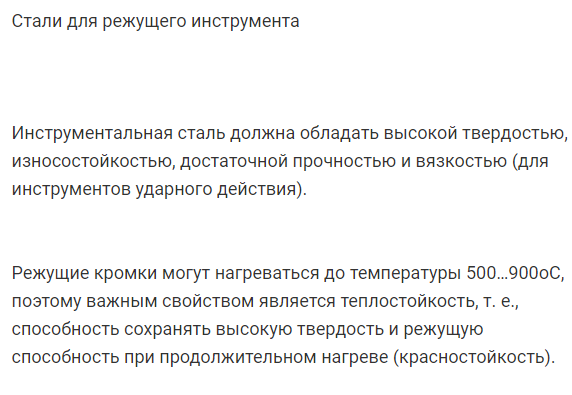
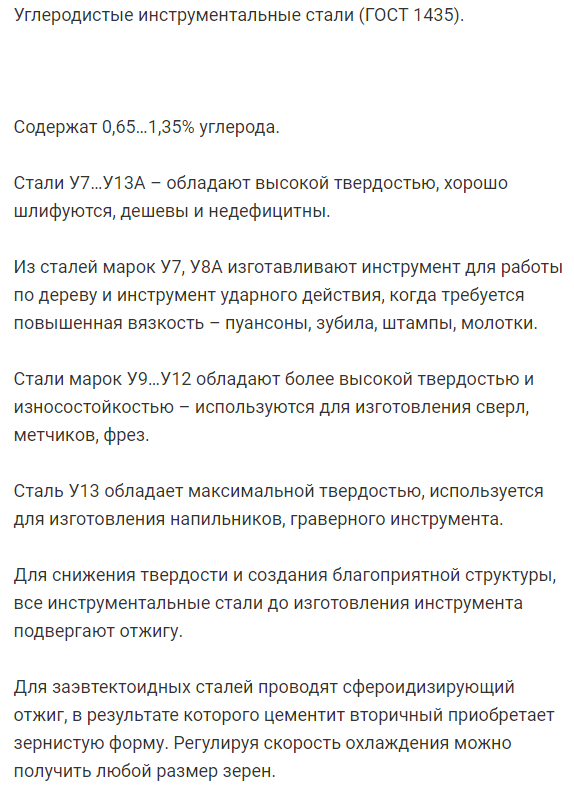
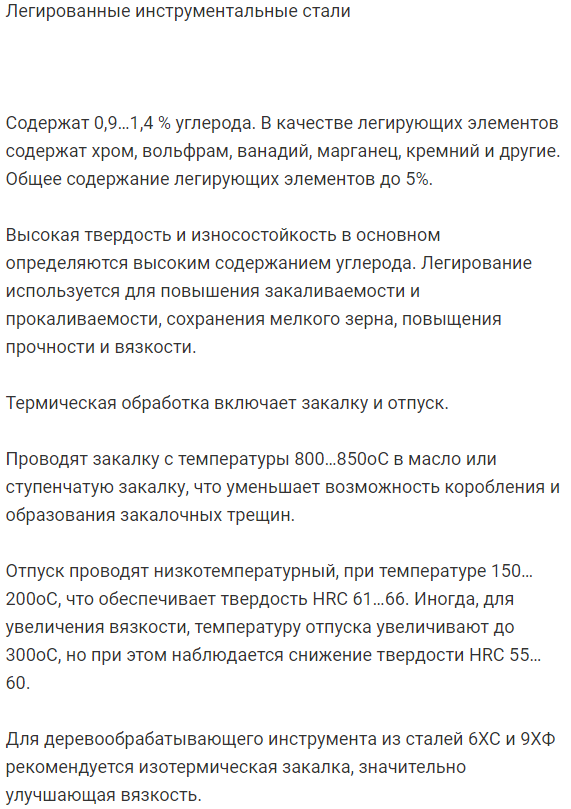
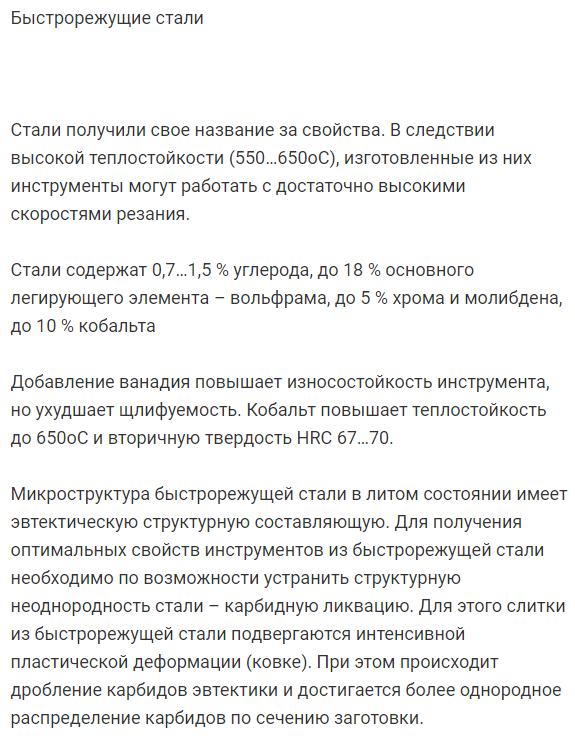
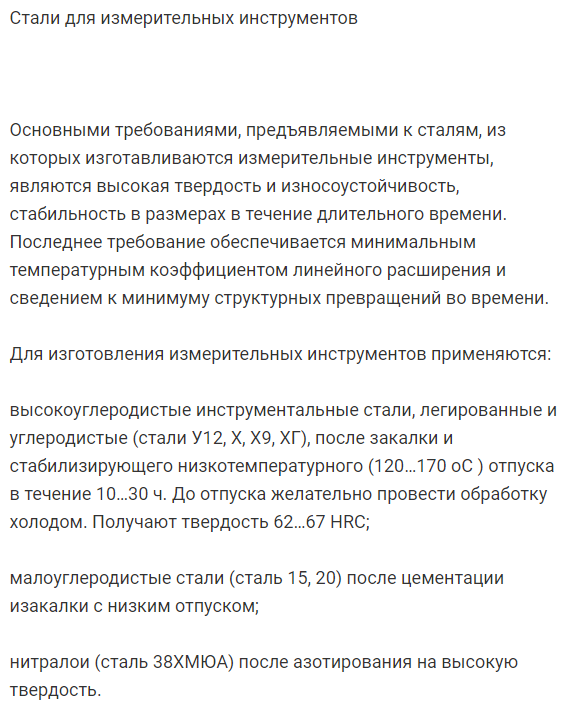
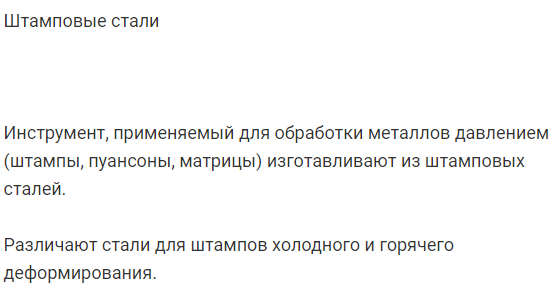
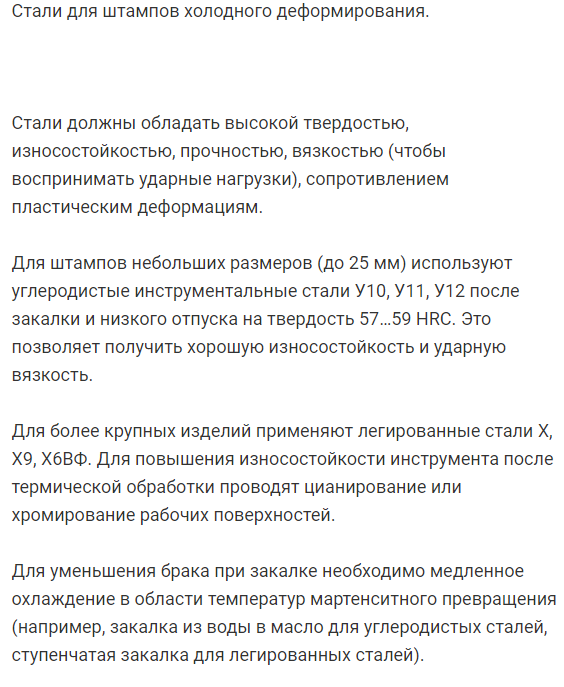
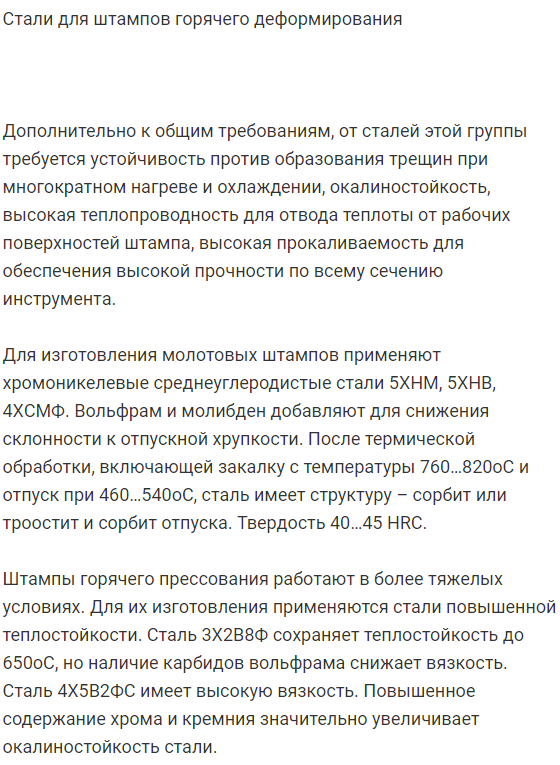
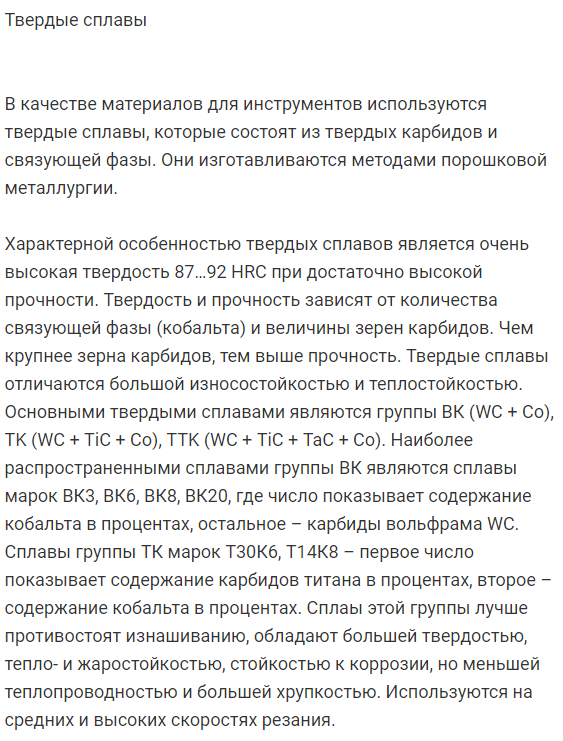
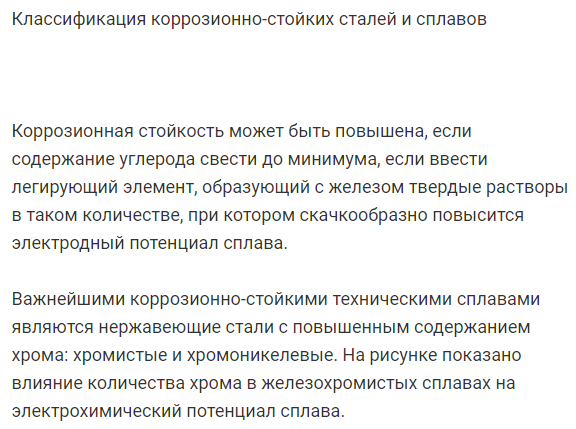
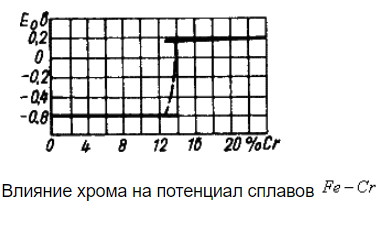
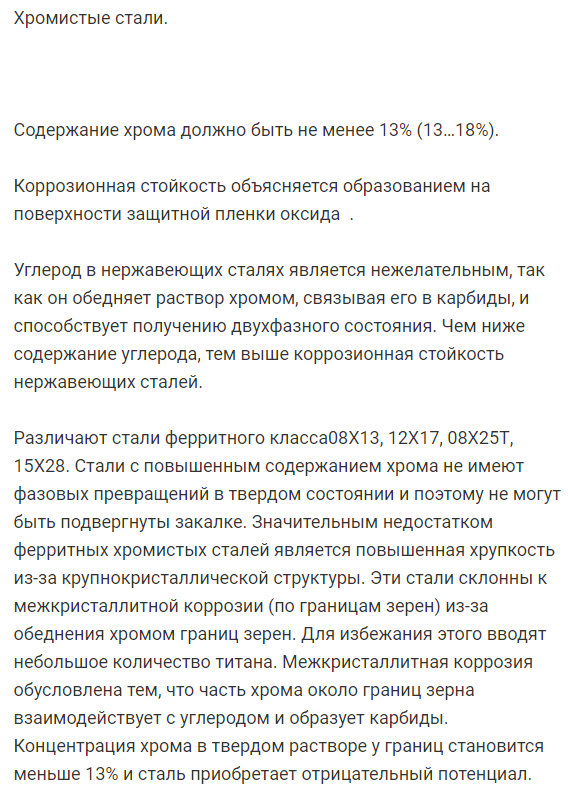
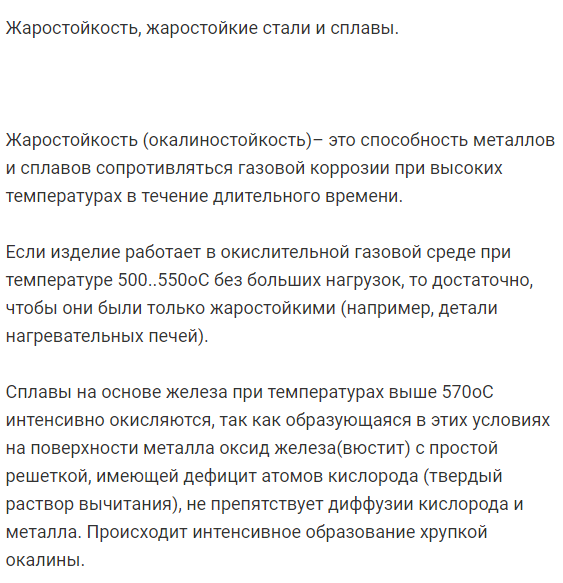
Сталь для режущих инструментов
Инструментальная сталь должна иметь высокую твердость, износостойкость, достаточную прочность и ударную вязкость (для ударных инструментов).
Поскольку режущая кромка может нагреваться до температуры от 500 до 900 ° C, термостойкость является важной характеристикой. Другими словами, это способность поддерживать высокую твердость и способность к резанию (устойчивость к красному цвету) при длительном нагревании.
Сталь инструментальная углеродистая (ГОСТ 1435).
- Содержит от 0,65 до 1,35% углерода.
- Сталь U7 … U13A-Высокая твердость, хорошо полируется, недорого и без дефектов.
- Из марок стали U7 и U8A могут быть изготовлены деревянные и ударные инструменты, если необходимо увеличить вязкость: штампы, долота, пресс-формы, молотки.
- Стали марок от U9 до U12 имеют высокую твердость и износостойкость и используются при изготовлении сверл, метчиков и фрез.
- Сталь U13 имеет самую высокую твердость и используется для изготовления пилок и инструментов для гравировки.
Все инструментальные стали отжигают перед изготовлением инструмента, чтобы уменьшить твердость и создать благоприятную структуру.
В случае гиперэвтектоидной стали проводят сфероидизирующий отжиг, и в результате вторичный цементит становится зернистым. Все размеры частиц могут быть получены путем регулирования скорости охлаждения.
Финальная термообработка — закалка и отпуск
Гиперэвтектоидная сталь полностью отверждена, а гиперэвтектоидная сталь отверждена не полностью. Закаленная сталь или мартенсит, или мартенситно-карбидная структура.
Температура отпуска выбирается в зависимости от требуемой твердости инструмента.
Легированная инструментальная сталь
Содержит 0,9-1,4% углерода. Легирующие элементы включают хром, вольфрам, ванадий, марганец и кремний. Общее содержание легирующих элементов составляет до 5%.
Высокая твердость и износостойкость в основном определяются высоким содержанием углерода. Легирование используется для повышения прокаливаемости и прокаливаемости, удержания мелких частиц и увеличения прочности и вязкости.
Термическая обработка включает отверждение и отпуск.
Отверждение осуществляется от температуры 800-850 ° C до масла или ступенчатого отверждения. Это уменьшает вероятность коробления и растрескивания.
Отпуск проходит при низкой температуре 150-200 ° С, обеспечивая твердость HRC 61-66. Чтобы повысить вязкость, температуру отпуска можно повысить до 300 ° C, но в то же время наблюдается снижение твердости HRC 55 … 60.
Изотермическое упрочнение рекомендуется для деревообрабатывающих инструментов из стали 6ХС и 9ХФ. Это значительно улучшает вязкость.
- Повышенное содержание кремния (сталь 9ХС) способствует повышению прокаливаемости до 40 мм и повышению стабильности мартенсита при отпуске. Недостатками сталей, содержащих кремний, являются чувствительность к обезуглероживанию при термообработке, плохая обрабатываемость резанием и деформация из-за упрочнения феррита кремнием.
Быстрорежущая сталь
- Сталь получила название собственности. Благодаря высокой термостойкости (550-650 ° C) изготовленные из них инструменты могут работать при значительно более высоких скоростях резания.
- Сталь содержит 0,7-1,5% углерода, до 18% основных легирующих элементов — вольфрама, до 5% хрома и молибдена, до 10% кобальта
- Добавление ванадия увеличивает износостойкость инструмента, но ухудшает полировку. Кобальт повышает термостойкость до 650 ° С и повышает вторичную твердость HRC 67 … 70.
Микроструктура литой быстрорежущей стали имеет эвтектические структурные компоненты. Чтобы получить оптимальные свойства инструментов, изготовленных из быстрорежущей стали, необходимо устранить структурную неоднородность стали — если возможно, карбидную сегрегацию. По этой причине слитки из быстрорежущей стали подвергаются сильной пластической деформации (ковка). В этом случае эвтектический карбид измельчается и достигается более равномерное распределение карбида по поперечному сечению заготовки.
После этого отжиг проводят при температуре 860-900оС. Структура отожженной быстрорежущей стали — мелкий пербит и карбид сорбита, небольшие эвтектоиды и более крупные первичные продукты. Количество карбида составляет около 25%. Сталь с такой структурой хорошо обрабатывается. Подавляющее большинство легирующих элементов находятся в карбидной фазе. Чтобы получить оптимальные свойства стали с готовым инструментом, необходимо обеспечить максимальное насыщение мартенсита легирующими элементами при термообработке. Сталь для измерительных инструментов
Основными требованиями к сталям, из которых состоит измерительное оборудование, являются высокая твердость и износостойкость, а также долговременная стабильность размеров. Последнее требование обеспечивается минимальным температурным коэффициентом линейного расширения и минимизацией структурного превращения во времени.
Для изготовления измерительных инструментов используются:
Высокоуглеродистая инструментальная сталь, легированная и углеродистая (сталь U12, X, X9, HG), после низкотемпературного (120-170 ° С) отпуска и стабилизации в течение 10-30 часов. Рекомендуется проводить холодную обработку перед закалкой. Получите твердость 62-67 HRC.
- Цемент и мягкая сталь после низкотемпературного отверждения (Сталь 15, 20).
- Нитралой (сталь 38ХМЮА) после азотирования для получения высокой твердости.
- Штамп стальной
Инструменты, используемые для формовки металла (штамп, штамп, штамп), изготовлены из штампованной стали.
Есть стали для холодной и горячей деформации.
Сталь для холодной штамповки.
Сталь должна иметь высокую твердость, износостойкость, прочность, ударную вязкость (поглощать ударные нагрузки) и устойчивость к пластической деформации.
Для штампов небольшого размера (до 25 мм) используйте углеродистую сталь U10, U11, U12, чтобы получить твердость 57-59 HRC после закалки. Это обеспечивает хорошую износостойкость и ударную вязкость.
Для крупных изделий используются легированные стали X, X9 и X6VF. Для повышения износостойкости инструмента после термообработки рабочая поверхность цианируется или хромируется.
Чтобы уменьшить разрушение при разрушении, необходимо медленно остывать в интервале температур мартенситного превращения (например, закалка от воды до масла для углеродистой стали и ступенчатое закалка для легированной стали).
Когда ударная сила применяется к перфоратору, используется сталь с высокой вязкостью (сталь 4ХС4, 5ХНМ). Это достигается за счет снижения содержания углерода, введения легирующих элементов и соответствующей термообработки. После закалки проводят высокотемпературный отпуск при температуре 480-580 ° C и получают твердость 38-45 HRC.
Сталь горячей деформации
В дополнение к общим требованиям, эта группа сталей обладает стойкостью к растрескиванию при многократном нагреве и охлаждении, стойкостью к окалине, высокой теплопроводностью для отвода тепла с рабочей поверхности штампа, высокой по поперечному сечению инструмента. Высокая прочность требуется для обеспечения прочности.
Для изготовления молотковых штампов используется углеродистая сталь 5ХНМ, 5ХНБ и 4ХСМФ. Вольфрам и молибден добавляются, чтобы уменьшить тенденцию к подавлению хрупкости. После термической обработки, включая закалку при температуре 760-820 ° C и отпуск при 460-540 ° C, сталь приобретает отпущенную структуру из сорбита или троостита и сорбита. Твердость 40 … 45 HRC.
Штампы с горячей штамповкой работают в более жестких условиях. Для изготовления используется сталь с высокой термостойкостью. Сталь 3Х2В8Ф сохраняет термостойкость до 650 ° С, но ее вязкость уменьшается из-за присутствия карбида вольфрама. Сталь 4Х5В2ФС обладает высокой вязкостью. По мере увеличения содержания хрома и кремния стойкость к окалину стали значительно улучшается.
Твердый сплав
Твердый сплав используется в качестве материала инструмента. Твердые сплавы состоят из твердого карбида и связующей фазы. Они сделаны методом порошковой металлургии.
Твердый сплав характеризуется очень высокой твердостью от 87 до 92 HRC и достаточной прочностью. Твердость и прочность зависят от количества связующей фазы (кобальта) и размера частиц карбида. Чем больше частицы карбида, тем выше прочность. Твердые сплавы характеризуются высокой износостойкостью и жаростойкостью. Основными твердыми сплавами являются ВК (WC + Co), ТК (WC + TiC + Co), ТТК (WC + TiC + TaC + Co). Наиболее распространенными сплавами в группе ВК являются сплавы ВК3, ВК6, ВК8 и ВК20. Цифры указывают процентное содержание кобальта, а остальное — карбид вольфрама WC. TK Group, сплавы T30K6, T14K8 — первое число указывает на содержание карбида титана в процентах, а второе указывает на содержание кобальта в процентах. Эта группа сплавов обладает высокой износостойкостью и превосходной твердостью, жаростойкостью, жаростойкостью и коррозионной стойкостью, но низкой теплопроводностью и высокой хрупкостью. Используется для средних и высоких скоростей резания.
Сплавы, содержащие небольшое количество кобальта, улучшают твердость и износостойкость, но используются для чистовой токарной обработки (VK3, T30K4), поскольку их прочность минимизирована. Классификация коррозионно-стойких сталей и сплавов
- Минимизируя содержание углерода и вводя легирующие элементы, можно повысить коррозионную стойкость при формировании твердых растворов с количеством железа, в котором электродный потенциал сплава постепенно увеличивается.
Наиболее важным коррозионно-стойким промышленным сплавом является нержавеющая сталь с высоким содержанием хрома и хромоникеля. На этом рисунке показано влияние количества хрома в железо-хромовом сплаве на электрохимический потенциал сплава.
Хромированная сталь
Содержание хрома должно быть не менее 13% (13-18%).
Коррозионная стойкость объясняется образованием защитной оксидной пленки на поверхности.
Углерод из нержавеющей стали нежелателен, поскольку он истощает раствор хромом, связывается с карбидами и способствует двухфазному состоянию. Чем ниже содержание углерода, тем выше коррозионная стойкость нержавеющей стали.
Различают стали ферритового класса 08Х13, 12Х17, 08Х25Т, 15Х28. Стали с высоким содержанием хрома не могут быть закалены, потому что они не подвергаются фазовому превращению в твердом состоянии. Существенным недостатком ферритной хромистой стали является то, что она более хрупкая из-за своей грубой кристаллической структуры. Эти стали подвержены межкристаллитной коррозии (вдоль межзеренных границ) из-за истощения межзеренных границ хромом. Чтобы избежать этого, вводится небольшое количество титана. Межкристаллитная коррозия связана с тем, что часть хрома вблизи границы зерен взаимодействует с углеродом с образованием карбидов. Концентрация хрома в твердом растворе на границе будет менее 13%, и сталь приобретет отрицательный потенциал.
Из-за тенденции к росту зерен ферритные стали требуют строгих условий сварки и централизованного охлаждения сварного шва. Недостатком является охрупчивание при нагревании в интервале температур 450-500 ° С.
Ферритная сталь используется при изготовлении оборудования для азотно-кислотных заводов (резервуары, трубы).
Жаростойкая, жаропрочная сталь и сплавы.
Термостойкость (стойкость к образованию накипи) — это способность металлов и сплавов выдерживать газовую коррозию при высоких температурах в течение длительных периодов времени.
- Если продукты работают в атмосфере окислительного газа при температуре 500,50 ° С без больших нагрузок, они являются достаточными с термостойкостью (например, часть печи).
Сплавы на основе железа сильно окисляются при температуре выше 570 ° С. Это связано с тем, что оксид железа (вюстит) образуется на поверхности металла с простой решеткой (вычитаемый твердый раствор), в которой отсутствуют атомы кислорода в этих условиях, поэтому диффузия кислорода и металла не затрудняется. , Происходит бурное образование хрупкой чешуи.
Смотрите также:
Примеры решения задач по материаловедению
Основные этапы технологического процесса пайки. | Центробежное литье. |
Методы контроля качества сварных и паяных соединений. | Факторы, определяющие продолжительность затвердевания отливок. |