Оглавление:
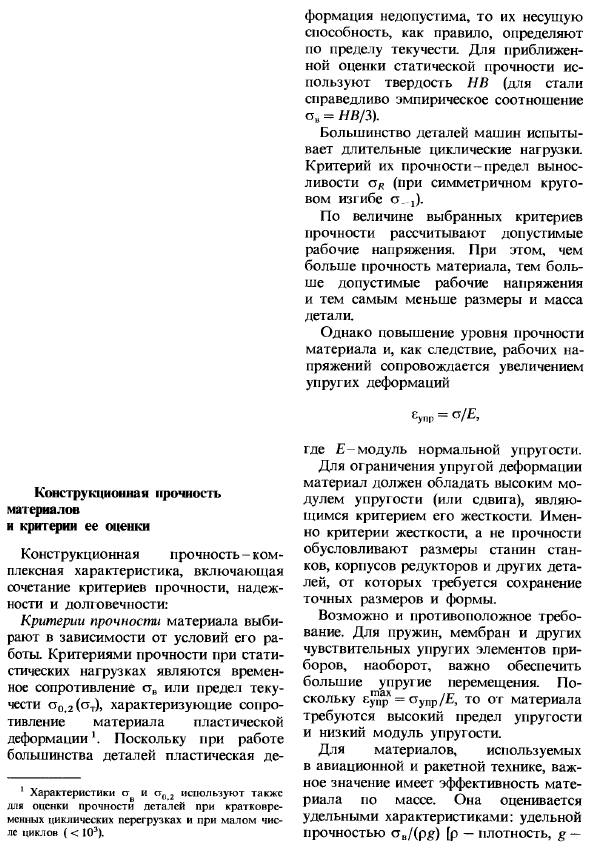
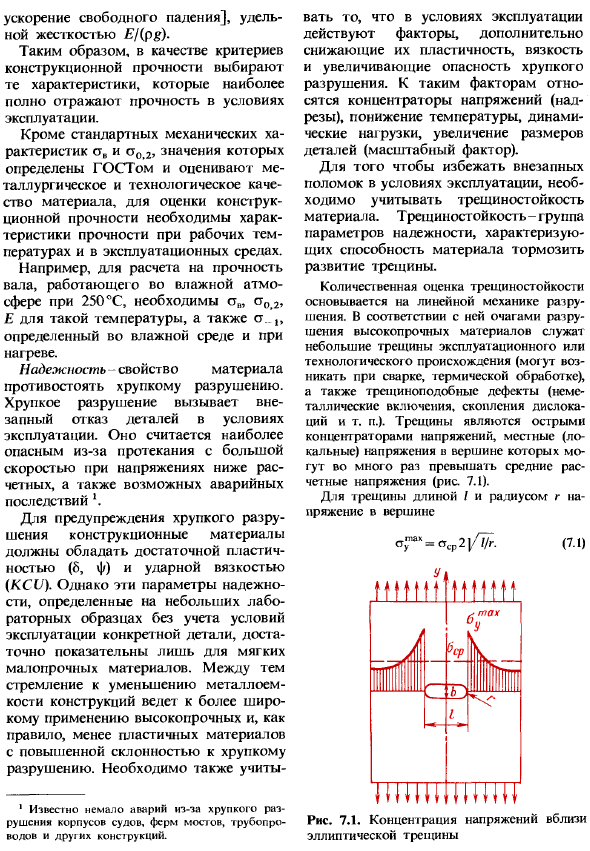
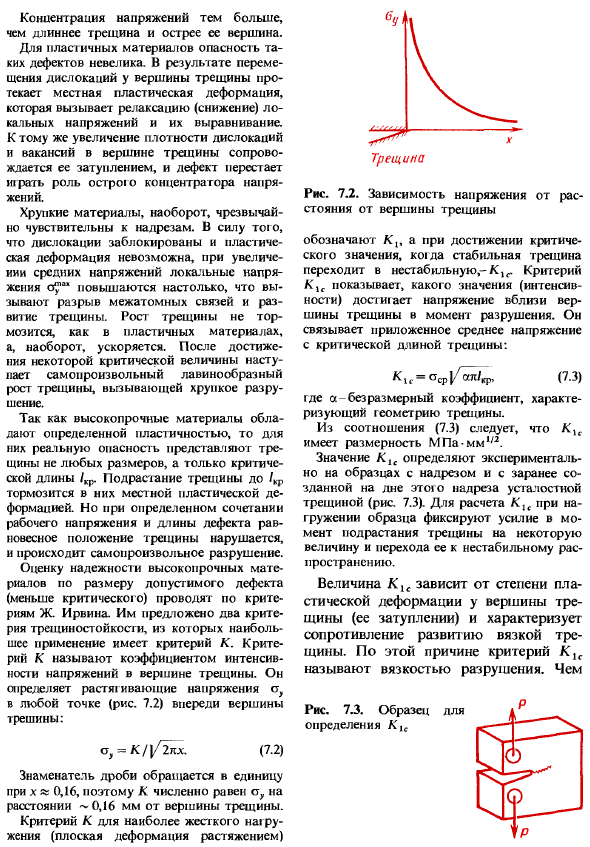
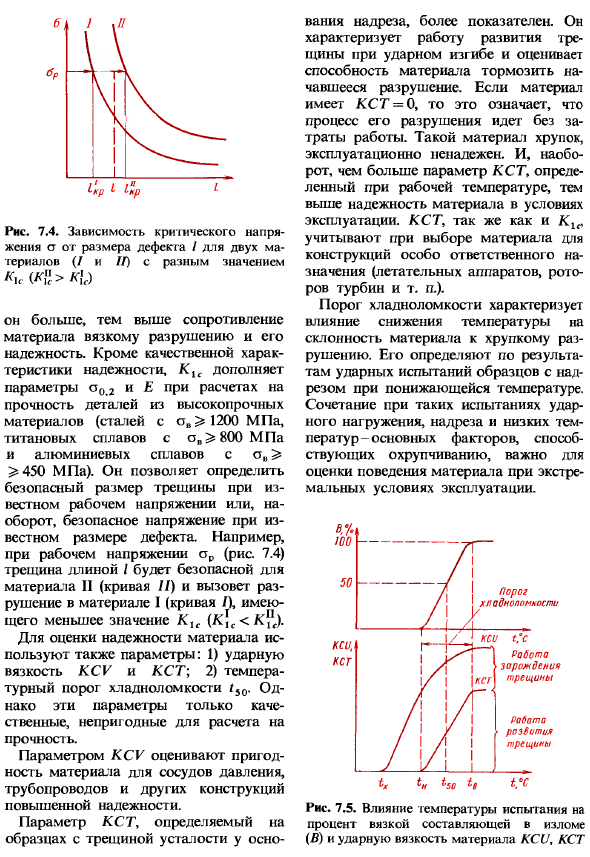
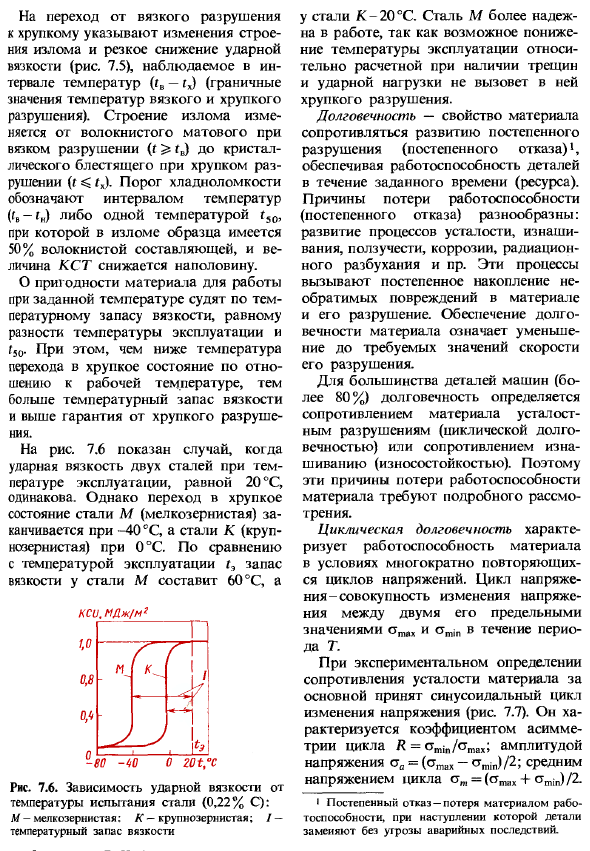
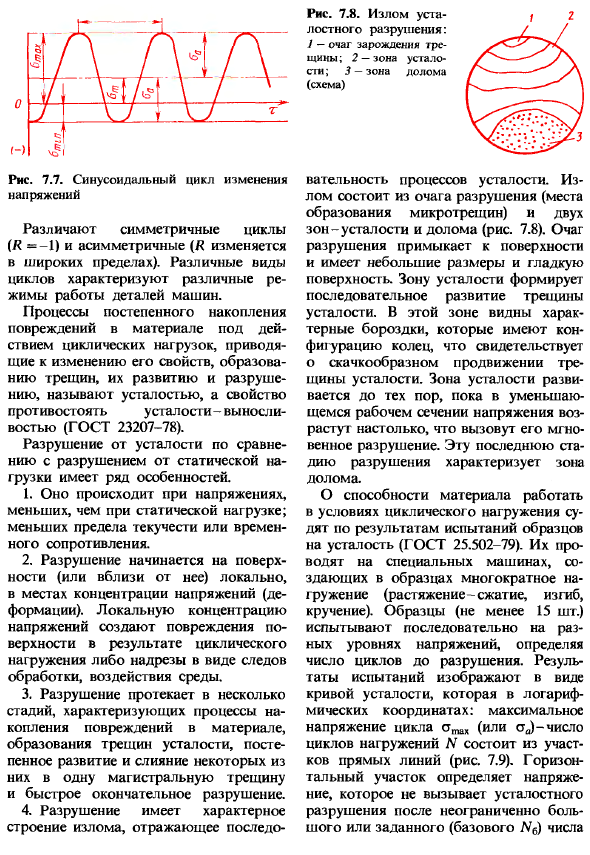
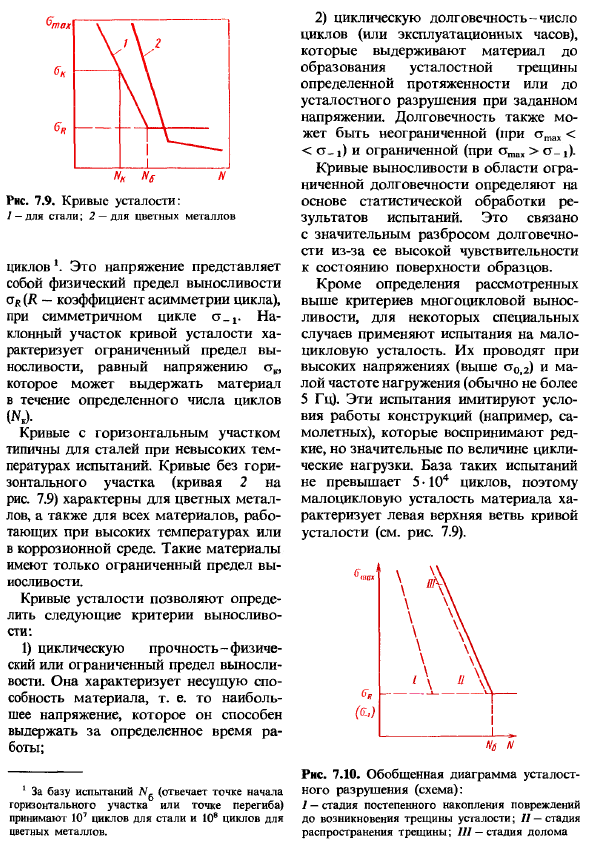
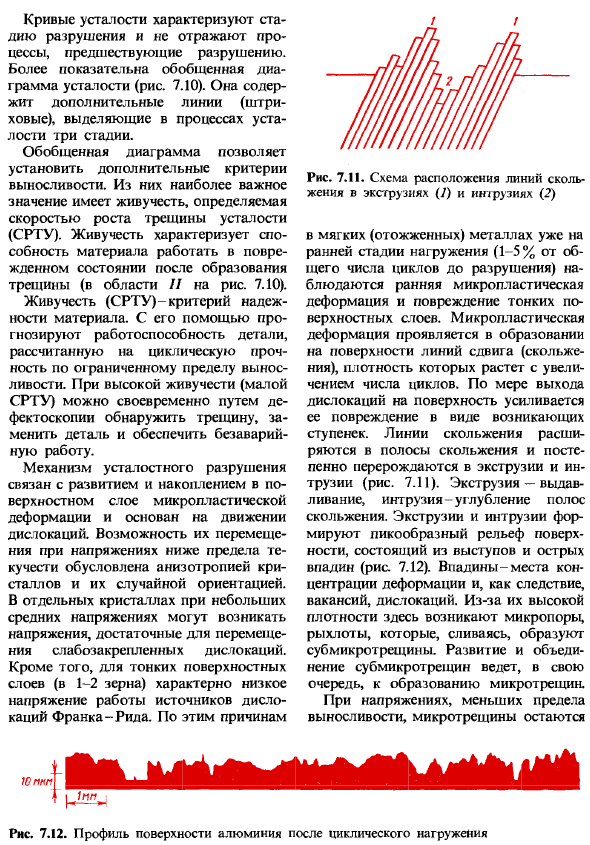
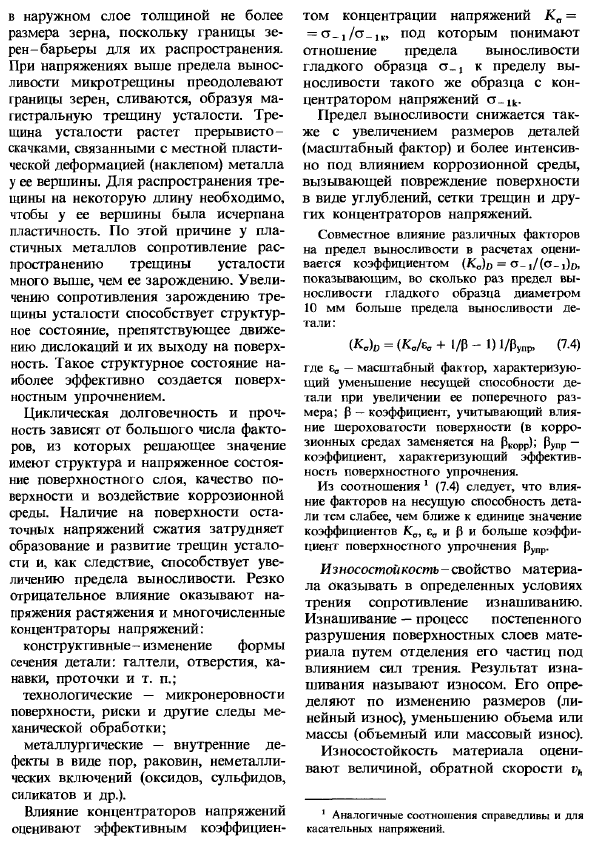
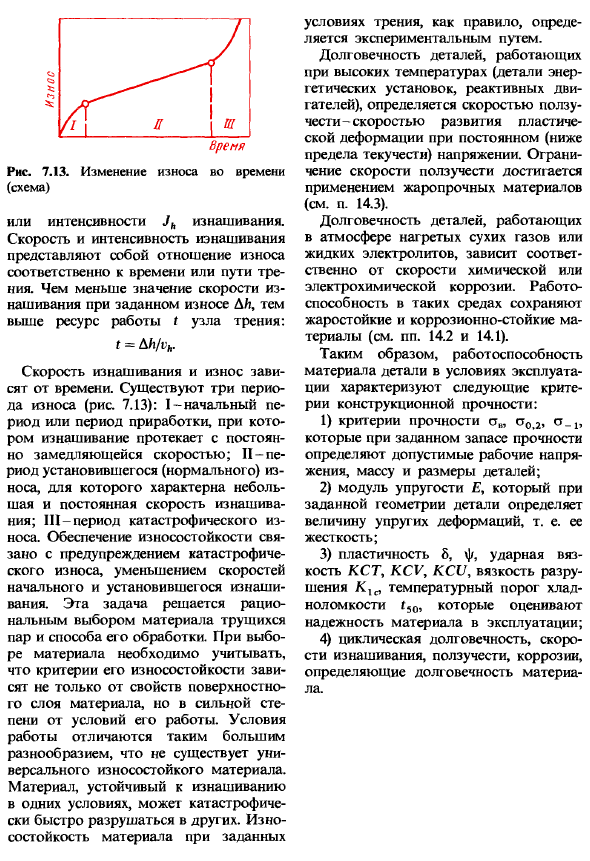

Конструкционная прочность материалов и критерии ее оценки
- Если пласт неприемлем, то их несущая способность, как правило, определяется пределом текучести. Для приблизительной оценки статической прочности используется твердость HB (для стали справедливо эмпирическое отношение= HB / 3). Большинство механических деталей длительное время подвергаются периодическим нагрузкам. Критерием их прочности является предел прочности (симметричный круговой изгиб о..). Допустимое рабочее напряжение рассчитывается по величине выбранной прочности criterion.
At в то же время, чем больше прочность материала, тем меньше размеры и вес детали, потому что кромка больше допустимого рабочего напряжения. Однако повышение уровня прочности материала и возникающее в результате этого рабочее напряжение сопровождается увеличением упругой деформации Конструкционная прочность материалов и критерии их оценки Прочность конструкции-комплексные свойства, включающие сочетание критериев прочности, надежности и долговечности:
Нормы прочности материала подбираются в зависимости от условий его эксплуатации. Людмила Фирмаль
Стандартом прочности для статистических нагрузок является предел текучести c02 (s), который характеризует временное сопротивление напряжению, или сопротивление материала пластической деформации. В процессе эксплуатации большинство деталей, пластмасса Характеристики o и a (12) также используются для оценки прочности деталей с кратковременными периодическими перегрузками и несколькими циклами (<103). Где E-нормальный модуль упругости. Для ограничения упругой деформации необходим высокий модуль упругости (или сдвига), который является критерием жесткости материала.
Определение размеров станины станка, корпуса редуктора и других деталей, необходимых для поддержания правильных размеров и формы, является критерием жесткости, а не прочности. Возможно и обратное. Напротив, важно обеспечить большое упругое смещение в случае пружины устройства, мембраны и других чувствительных упругих элементов. = Pupr / E, поэтому материалу нужен высокий предел упругости и низкий модуль упругости.
- Для материалов, используемых в авиационной и ракетной технике, массовая эффективность материала составляет important. It оценивается по определенным характеристикам: удельная прочность aB /(pgj [p-плотность, G-ускорение свободного падения] и удельная жесткость Ej (pg). Таким образом, в качестве критерия прочности конструкции выбирается характеристика, наиболее полно отражающая ее прочность в условиях эксплуатации. Помимо стандартных механических свойств о0 и 2, их значения определяются ГОСТом, необходимо оценить металлургические и технические качества материала, его прочностные характеристики при температуре и в рабочей среде, оценить прочность конструкции.
Например, для расчета прочности вала, работающего во влажной среде 250°С, необходимо использовать такие температуры st, o2, E. Надежность свойств материалов, которые выдерживают хрупкое разрушение. Хрупкое разрушение приводит к внезапному выходу из строя детали при эксплуатации conditions. It считается наиболее опасным, из-за высокой скорости потока
ниже расчетного напряжения и возможной аварийной ситуации. Людмила Фирмаль
Для предотвращения хрупкого разрушения конструкционные материалы должны обладать достаточной пластичностью (b, f) и ударной вязкостью (CSG).Однако эти параметры надежности, которые определяются в небольших лабораторных образцах без учета условий эксплуатации конкретных деталей, достаточно показательны только для мягких, малопрочных материалов. С другой стороны, стремление снизить металлоемкость конструкций приводит к более широкому использованию менее пластичных материалов с повышенной склонностью к хрупкому разрушению, в целом с высокой strength.
It также необходимо учитывать 1. известно много аварий, связанных с хрупким разрушением стволов, мостовых ферм, трубопроводов и других конструкций. Следует отметить, что в условиях эксплуатации действуют факторы, дополнительно снижающие пластичность, вязкость и повышающие риск хрупкого разрушения. К таким факторам относятся концентраторы напряжений (насечки), снижение температуры, динамическая нагрузка, увеличение размеров детали (масштабный коэффициент). Чтобы избежать внезапного выхода из строя условий эксплуатации, необходимо учитывать трещиностойкость материала.
Трещиностойкость — это группа показателей надежности, характеризующих способность материала подавлять возникновение трещин. Количественное определение вязкости разрушения основано на линейной механике разрушения. Соответственно, очагом разрушения высокопрочных материалов являются мелкие трещины эксплуатационного или технологического происхождения (могут возникать при сварке, термообработке), а также дефекты типа трещин (неметаллические включения, скопление дислокаций и др.).).
Трещина представляет собой резкую концентрацию напряжений, и локальное (локальное) напряжение на вершине может быть во много раз больше среднего расчетного напряжения(рис.7.1). В случае трещины длины/и радиуса r, напряжение на вершине е Рисунок 7.1.Концентрация напряжений вблизи овальной трещины Чем больше концентрация напряжений, тем длиннее трещина, тем острее наконечник. Для пластиковых материалов риск возникновения таких дефектов составляет low. As в результате смещения дислокации на вершине трещины происходит локальная пластическая деформация, вызывающая локальную релаксацию напряжений (редукцию) и equalization.
In кроме того, дислокация вершины трещины и увеличение плотности вакансии сопровождаются затуплением, и дефект перестает играть роль острого концентратора напряжений. Напротив, хрупкий материал очень чувствителен к надрезу. При увеличении среднего напряжения дислокации блокируются, пластическая деформация становится невозможной, поэтому локальное напряжение становится очень большим, что вызывает разрушение межатомных связей и образование трещин. Рост трещин не будет таким медленным, как в пластических материалах, а наоборот будет ускоряться.
После достижения определенного критического значения, RTRGHT трещины, как естественная лавина, может произойти, вызывая хрупкое разрушение. В связи с тем, что высокопрочные материалы обладают определенной пластичностью, трещины любого размера, но только критической длины / cr, представляют для них реальную опасность. рост трещин to / cr подавляется их локальной пластической деформацией. Однако при определенном сочетании рабочего напряжения и длины дефекта равновесное положение трещины нарушается, и тогда происходит естественное разрушение.
J. В соответствии с критериями Ирвина проводится оценка надежности высокопрочных материалов по величине допустимых дефектов (менее критических).Он предложил 2 критерия трещиностойкости, из которых наиболее часто используется критерий К. Он определяет рост! Напряжение сдвига st, в любой точке вершины трещины(рис. 7.2).: о= к / | / 2хх (7.2) Так как знаменатель дроби преобразуется по X ss 0,16 в 1, то K численно равен Cyan на расстоянии около 0,16 мм от вершины трещины. Самые строгие стандарты усушки Хайпи к (плоская растяжимая деформация) Трещина Рисунок 7.2.
Зависимость напряжения от расстояния до вершины трещины Если критическое значение будет достигнуто, стабильная трещина становится неустойчивой ко-К Х(.Критерий KXc указывает на величину (прочность), которую напряжение достигает вблизи вершины трещины во время разрушения. Свяжите приложенное среднее напряжение с критической длиной трещины. ки = пср1 ′/ ас / 1Ф. (7.3) Где а-безразмерный коэффициент, характеризующий форму трещины. Из соотношения (7.3) следует, что размеры KXc составляют МПа-мм1 ′ 2. Величина Klt определяется экспериментально с образцом с выемкой и усталостной трещиной, предварительно созданной в нижней части выемки (рис.7.3).
В день расчета КЛТ при нагружении образца фиксируется Сила момента роста трещины в определенном количестве и переход к неустойчивому распространению. Величина K1e зависит от степени пластической деформации на вершине трещины (затупления) и характеризует сопротивление развитию вязких трещин. По этой причине критерий K1c называется вязкостью разрушения. Больше, чем Рисунок 7.3. Изображение i для определения Kte Рисунок 7.4.Зависимость критического напряжения c от размера дефекта / 2 материалов с различными значениями (/и II)!< (*1 * J>
A’L) Чем он больше, тем выше сопротивление материала вязкому разрушению и его прочность. reliability. In помимо качественных характеристик надежности, Kic дополняет параметры O 1200 и E при расчете прочности деталей, изготовленных из высокопрочных материалов(сталь o> 1200 МПа, титановый сплав o ^ 800 МПа, алюминиевый сплав o > 450 МПа).Можно определить безопасный размер трещины при известном рабочем напряжении или, наоборот, безопасное напряжение при известном размере дефекта.
Например, при рабочем напряжении op (рис.7.4) трещина длины/является безопасной для материала II (кривая//) и вызывает разрушение материала 1 (кривая I).Это связано с тем, что значение K1c мало(k {c a_.). Кривая выносливости для областей, где выносливость ограничена, определяется на основе статистической обработки результатов испытаний. Это связано с высокой чувствительностью образца к условиям поверхности, что значительно расширяет его долговечность. В дополнение к определению критериев многоцикловой долговечности, описанных выше, в некоторых особых случаях используются испытания на усталость с низким циклом.
Они выполняются при высоких напряжениях ( 2 и выше) и на низких частотах нагрузки (ns, обычно 5 Гц и выше).Эти испытания имитируют условия эксплуатации конструкций (например, самолетов), которые поглощают редкие, но значительные циклические нагрузки. Поскольку база такого испытания не превышает 5-104 циклов, то малоцикловая усталость материала характеризуется верхней левой ветвью кривой усталости (см. рис. 7.9). Рисунок 7. 10.Общая схема усталостного разрушения(рис.): 1-фаза накопления постепенного повреждения до возникновения усталостной трещины; / 7-фаза распространения трещины. /// — Стадия дромадеров Кривая усталости характеризует стадию разрушения, а ns отражает процесс, предшествующий разрушению.
Более понятен общий вид усталости (рис. 7.10). он содержит дополнительные линии (пунктирные линии), которые выделяют 3 стадии процесса усталости. Обобщенная схема позволяет задать дополнительные критерии долговечности. Из них наиболее важной является жизнеспособность, которая определяется скоростью роста усталостных трещин (сигу).Жизнеспособность характеризует способность материала функционировать в поврежденном состоянии после образования трещин (площадь / I на рисунке 7.10).
Живучесть (СРТУ) — критерий надежности материала. С его помощью рассчитана работоспособность детали и рассчитана на многократное превышение пределов прочности при ограниченном пределе выносливости. Высокая живучесть (низкая СРТУ) позволяет своевременно выявлять трещины с помощью дефектоскопии и замены деталей для обеспечения безаварийной работы. Механизм усталостного разрушения связан с возникновением и накоплением микропластической деформации поверхностного слоя и основан на движении дислокаций. Возможность перемещать их в условиях стресса Ниже предел текучести из-за анизотропии кристалла и случайной direction.
In отдельные кристаллы, небольшое среднее напряжение может произвести достаточное напряжение, чтобы переместить слабо внедренный dislocation. In кроме того, тонкий поверхностный слой (1-2 зерна) характеризуется низким напряжением работы источника дислокаций Франка-Рида. По указанным причинам Рисунок 7.11.Выталкивающая (2) и вталкивающая (2) Схема линии скольжения В мягких (обожженных) металлах ранняя микропластическая деформация и повреждение тонкого поверхностного слоя наблюдаются уже на начальной стадии нагружения (1-5% от общего числа циклов до разрушения).
Микропластическая деформация проявляется в образовании на поверхности линий сдвига (скольжения), плотность которых увеличивается с увеличением числа циклов. Когда дислокация достигает поверхности, происходит все повреждение в ступенчатой форме. Линия скольжения расширяется до полосы скольжения, постепенно вырождаясь в вытеснение и вторжение (рис. 7.11).Вытолкнуть-выталкивать, полосы скольжения углубление проникновения. Выдавливание и проникновение формируют горноподобный рельеф поверхности, состоящий из выступов и острых впадин (рис. 7.12).Депрессия-это место, где концентрируется напряжение, приводящее к вакансиям и дислокациям.
Из-за их высокой плотности здесь возникают микропоры и разрыхление, и они сливаются, образуя субмикрокрески. Развитие и интеграция суб-микротрещин приводит к образованию микротрещин. При напряжениях ниже предела выносливости, микротрещины остаются Рисунок 7.12.Поверхностный профиль алюминия после периодического нагружения во внешнем слое имеет толщину меньшую, чем размер частиц, поскольку границы зерен являются барьером для их distribution.
At напряжения выше предела усталости, микротрещины преодолевают границы зерен и плавятся, образуя крупные усталостные трещины. Усталостные кабели растут с перебоями, возникает скачок, связанный с локальной пластической деформацией (упрочнением) металла при его apex. In для того чтобы трещина растянулась до определенной длины, необходимо, чтобы ее пластичность исчерпалась на пике. Из-за этого в пластичных металлах сопротивление распространению усталостных трещин значительно выше, чем при их зарождении.
Повышению устойчивости к зарождению усталостных трещин способствует структурное состояние, которое препятствует перемещению дислокаций и дислокаций к поверхности. Такое структурное состояние наиболее эффективно создается поверхностным упрочнением. Повторная долговечность и прочность зависят от ряда факторов, таких как структура и напряженное состояние поверхностного слоя, качество поверхности и критическая важность воздействия агрессивных сред.
Наличие остаточных сжимающих напряжений на поверхности затрудняет образование и прогрессирование усталостных трещин, что приводит к увеличению пределов выносливости. Растягивающее напряжение и многочисленные устройства концентрации напряжений имеют резко отрицательный эффект. Структура-изменение формы сечения детали: скругление, отверстие, ПАЗ, канавка и др. Технология-микрошероховатость поверхности, риск и другие следы механической обработки. Металлургия-внутренние дефекты в виде пор, оболочек, неметаллических включений (оксидов, сульфидов, силикатов и др.). Влияние концентратора напряжений оценивается по эффективному коэффициенту Концентрация напряжений Kn = a_1 / o_1k. это означает отношение предела выносливости к пределу гладкого образца.
Усталость одного и того же образца с использованием концентратора напряжений o-C. Предел прочности уменьшается более интенсивно под воздействием агрессивной среды, вместе с увеличением размеров детали (масштабного фактора), что вызывает повреждение поверхности в виде углублений, трещин в сети и других концентраций напряжений. Совокупное влияние различных факторов на предел выносливости при расчете оценивается коэффициентом (Ko)= = a ->)©.Это указывает на то, во сколько раз предел прочности гладкого геометрического диаметра 10 мм превышает предел прочности детали. (Ke) c =(Ko / Ee + l / p-1) l / pynp, (7.4) где масштабный коэффициент горы характеризуется уменьшением несущей способности детали с увеличением поперечного размера.
Коэффициент, учитывающий влияние Р-шероховатости поверхности (в агрессивной среде она заменяется Rcorr); Р> pr-коэффициент, характеризующий эффективность поверхностного упрочнения. Из соотношения (7.4) видно, что чем ближе значения коэффициентов q и p К 1 и чем больше коэффициент поверхностного упрочнения P> pr, тем меньше влияние факторов на несущую способность детали. Износостойкость-свойства материалов, которые проявляют износостойкость при определенных условиях трения.
Износ-это процесс, при котором поверхностный слой материала постепенно разрушается путем отделения частиц под действием трения. Результат износа называется Wear. It определяется изменением размеров (линейный износ), уменьшением объема или массы (объемный или массовый износ). Износостойкость материала оценивается по обратной скорости vh 1 аналогичное соотношение Это справедливо для тангенциального напряжения. Рис. 7.13.Изменение износа с течением времени(рисунок)
Или носить силу Jh. Скорость износа и прочность-это отношение износа ко времени или пути трения соответственно. Величина скорости изнашивания для конкретного изнашиваемого элемента меньше, чем больше срок службы узла трения. Т= ды /л. Скорость изнашивания и износа зависит от времени. Существует 3 периода износа (рис. 7.13).I-акклиматизационный период, в котором износ происходит в начальный период или по нарастающей ставке. II-период устойчивого развития (обычно) wear. It характеризуется малой и постоянной скоростью износа. III-катастрофический период амортизации.
Обеспечение износостойкости связано с предотвращением катастрофического износа и снижением скорости изнашивания в исходном и установившемся состоянии. Эта задача решается разумным выбором материалов для трущейся пары и способа их обработки. При выборе материала, следует иметь в виду, что критерии износостойкости во многом зависят не только от характеристик поверхностного слоя материала, но и от условий его эксплуатации.
Условия труда настолько разнообразны, что универсального износостойкого материала не существует. Материалы, которые выдерживают износ при определенных условиях, могут разрушаться катастрофически и быстро в других условиях. Износостойкость некоторых материалов Обычно условия трения определяются экспериментально. Долговечность деталей (силовых установок, деталей реактивных двигателей), работающих при высоких температурах, определяется падением пластической деформации при ползучести пластин, постоянными (меньше предела текучести) напряжениями.
Скорость ползучести ограничена применением термостойких материалов (см. раздел 14.3). Долговечность детали, работающей в атмосфере нагретого сухого газа или жидкого электролита, зависит от скорости химической или электрохимической коррозии соответственно. Эксплуатационные характеристики в такой среде поддерживаются термостойкими и коррозионно-стойкими материалами (см. пункты 14.2 и 14.1).
Таким образом, эксплуатационные характеристики материала детали в условиях эксплуатации характеризуются следующими критериями прочности конструкции: 1) Ссылка прочности ОК, о0> 2,a_x. It определяет допустимое рабочее напряжение, массу детали и ее размеры для заданного запаса прочности. 2) модуль упругости Е. Это определяет величину упругой деформации, то есть ее жесткость, для заданной формы детали. 3) пластичность b, f, ударная вязкость KST, KCV, KCU, вязкость разрушения K)s, порог температуры холодного охрупчивания 150.Оцените надежность материала в процессе эксплуатации. 4) определение повторной долговечности, скорости износа, ползучести, коррозии, долговечности материала.
Смотрите также:
Материаловедение — решение задач с примерами
Методы повышения конструкционной прочности | Диффузионное насыщение сплавов металлами и неметаллами |
Классификация конструкционных материалов | Общие требования, предъявляемые к конструкционным материалам |