Оглавление:
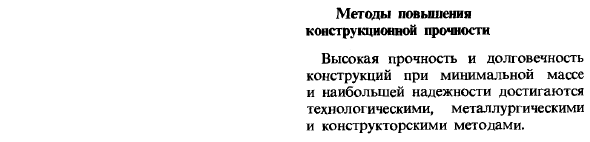
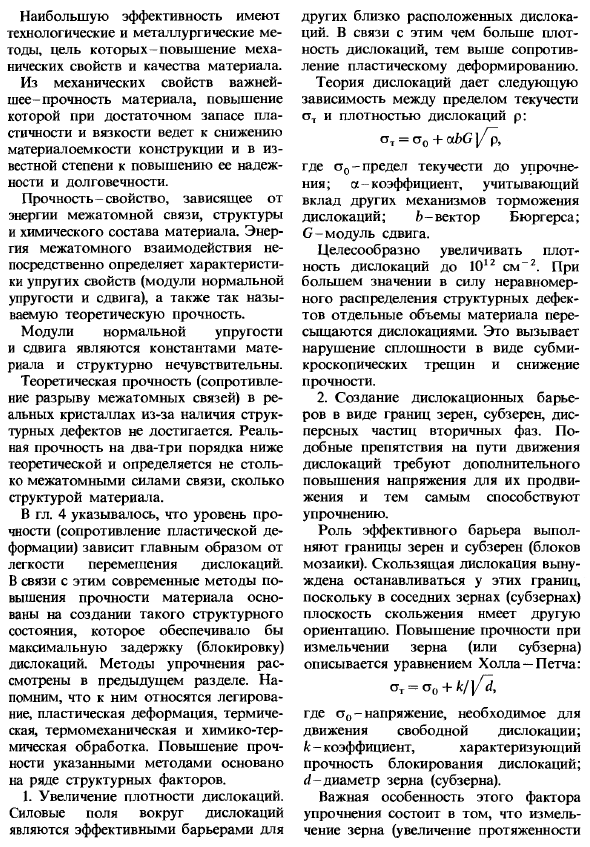
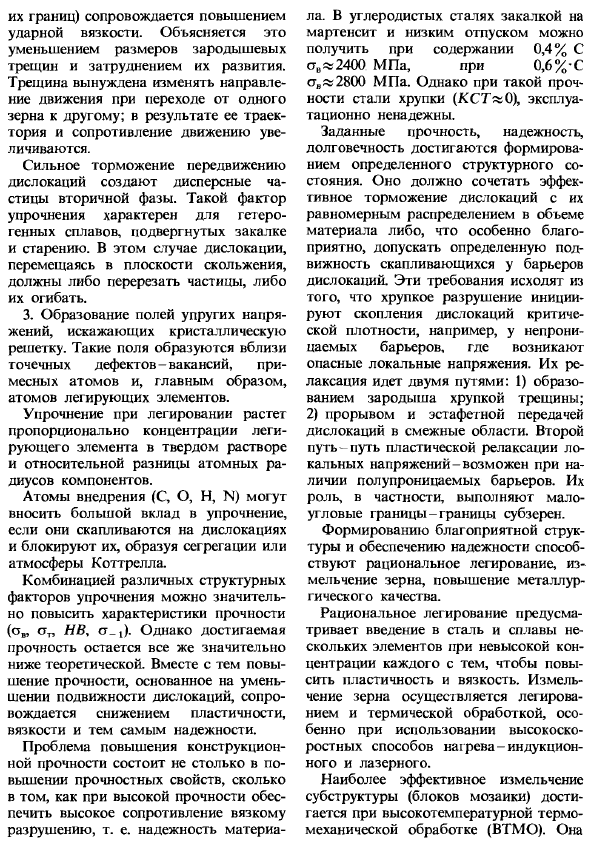
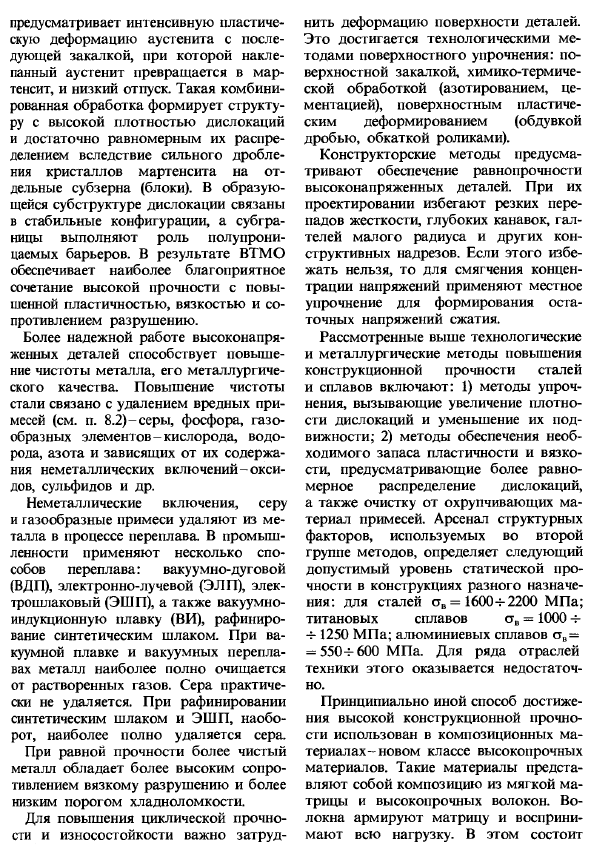
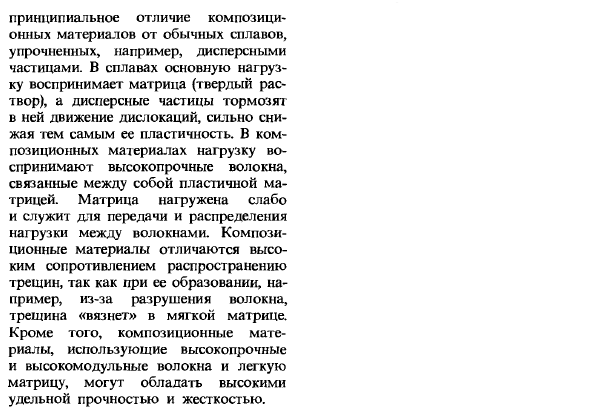

Методы повышения конструкционной прочности
- Как увеличить прочность конструкции Технические, металлургические и конструкторские приемы позволяют обеспечить высокую прочность и долговечность конструкций при минимальном весе и максимальной надежности. Наиболее эффективными являются технические и металлургические методы, целью которых является улучшение механических свойств и качества материала.
Из механических свойств наиболее важным является прочность материала, а увеличение материала с достаточным запасом пластичности и вязкости приводит к снижению материалоемкости конструкции, в некоторой степени к повышению ее надежности и долговечности. Прочность-это свойство, которое зависит от энергии связей между атомами, от структуры и химического состава материала. Энергия межатомного взаимодействия непосредственно определяет свойства их свойств
(обычный коэффициент упругости и сдвига) и так называемую теоретическую прочность. Людмила Фирмаль
Обычные модули упругости и сдвига являются константой материала и не являются структурно чувствительными. Теоретическая прочность реального кристалла за счет наличия структурных дефектов (устойчивость к разрушению межатомных связей) не достигается. Фактическая прочность на 2-3 порядка ниже теоретической величины и определяется не силой связи атома, а структурой материала. Было показано, что уровень вашей 4 прочности (устойчивость к пластической деформации) во многом зависит от легкости перемещения dislocations.
In в связи с этим новейшие методы повышения прочности материала основаны на создании такого структурного состояния, которое обеспечивает максимальную задержку (блокирование) дислокаций. Методы упрочнения описаны в предыдущем разделе. Напомним, что к ним относятся легирование, пластическая деформация, термическая, термомеханическая и химико-термическая обработка. Увеличение прочности этими методами основано на многих структурных факторах. 1.Увеличение плотности дислокаций. Силовое поле вокруг дислокации является эффективным барьером Другие близко расположенные dislocations.
- In в связи с этим, чем выше плотность дислокации, тем выше сопротивление пластической деформации. Теория дислокаций дает следующие зависимости между пределом текучести и плотностью дислокаций P. / / п、 Где o0 — предел текучести перед отверждением. а-коэффициент, учитывающий вклад других механизмов подавления дислокации. Гамбургер L вектор; 6 модуль сдвига. Рекомендуется увеличить четкость дислокации до 10 * 2 cm-2.At в большей степени, из-за неравномерного распределения структурных дефектов, отдельные объемы материала становятся перенасыщенными дислокациями.
Это приводит к разрывам в виде субмикронных трещин, что приводит к снижению прочности. 2.Создание дислокационных барьеров в виде границ зерен, субкритических и вторичных фазовых дисперсных частиц. Такое препятствие движению дислокаций требует дополнительного увеличения напряжений за счет их продвижения вперед, способствуя тем самым упрочнению. Роль эффективного барьера играют границы злаков и подзерен (мозаичные блоки).Дислокации скольжения вынуждены останавливаться на этих границах,
поскольку плоскости скольжения имеют различную ориентацию на соседних зернах (субконтиненте). Людмила Фирмаль
Увеличение прочности при измельчении частиц (или субзерен) описывается уравнением Холла-патча: ct = o0 + k / / d9 Где<y0-напряжение, необходимое для движения свободной дислокации. k-коэффициент, характеризующий интенсивность блокирующей дислокации. (/- Диаметр зерна (субграней). Важной особенностью этого упрочняющего фактора является то, что измельчение зерна(увеличение длины границы) сопровождается увеличением ударной вязкости. Эго объясняется уменьшением размеров трещин в зародыше и трудностями в их развитии.
Трещины вынуждены менять направление движения при переходе от одного зерна к другому. another. As в результате сопротивление его траектории и движению возрастает. Сильное торможение движения дислокаций создают дисперсные частицы вторичной фазы. Такие факторы упрочнения характерны для неоднородных сплавов, подвергнутых закалке и aging. In в этом случае дислокации, которые движутся в плоскости скольжения, должны разрезать частицы или согнуть частицы. 3.Образование упругого поля напряжений, искажающего кристаллическую решетку.
Такие поля формируются вблизи вакансий, примесных атомов и точечных дефектов, которые в основном являются атомами легирующих элементов. Упрочнение при легировании увеличивается пропорционально относительной разнице между концентрацией легирующих элементов в твердом растворе и атомным радиусом компонента. Интерстициальные атомы (C, O, H, N) могут существенно способствовать упрочнению, когда они накапливаются в дислокациях и блокируют их, образуя сегрегационную или Котрелловую атмосферу.
Сочетание различных структурных факторов упрочнения позволяет значительно повысить прочностные характеристики (s, HB, st_ ()).Однако достигнутая интенсивность значительно ниже теоретического значения. 。 Проблемы с улучшением дизайна Прочность-это способ обеспечения высокой стойкости к вязкому разрушению с высокой прочностью, то есть он не увеличивает прочностные характеристики так сильно, как надежность материала В углеродистой стали La мы получаем закалку и низкий отпуск мартенситом с содержанием 0,4% C st%2400 MPa и 0,6% * C. авл28оо МПа.
Однако при такой прочности сталь хрупка(KST%0) и не надежна в эксплуатации. Удельная прочность, надежность и долговечность достигаются за счет формирования специфической конструкции state. It необходимо сочетать эффективное торможение дислокаций с равномерным распределением в объеме материала. Также особенно предпочтительно допускать специфическую подвижность дислокаций, которые накапливаются в барьере.
Эти требования основаны на том, что, например, они являются непроницаемыми барьерами, в которых возникают опасные локальные напряжения, а начало хрупкого разрушения происходит за счет накопления дислокаций критической плотности. Расслабление их протекает в 2-х направлениях.1)образование хрупких трещин эмбриона. 2) прорыв дислокации и передача реле к смежным областям. Путь пластической релаксации локальных напряжений, 2-й способ, возможен при наличии полупроницаемого слоя barrier. In в частности, их роль играют границы малых углов, то есть границы подзерен.
Рациональное легирование, измельчение зерна и улучшение металлургического качества способствуют формированию хорошей структуры и обеспечивают надежность. Рациональное легирование предполагает введение нескольких элементов в сталь и сплавы при каждой низкой концентрации для повышения пластичности и ударной вязкости. Измельчение зерна осуществляется путем легирования и термообработки, особенно при использовании высокоскоростных методов нагрева, индукционного и лазерного.
Наиболее эффективное измельчение субструктуры (мозаичного блока) осуществляется при высокотемпературной термомеханической обработке (ВТМО), которая обеспечивает сильную пластическую деформацию аустенита и последующее упрочнение, а заклепанный аустенит превращается в мартенсит и подвергается низкому отпуску. Такая композиционная обработка создает структуру с достаточно равномерным распределением за счет высокой плотности дислокаций и сильного расщепления мартенситных кристаллов на отдельные субзерна (блоки). в полученной субструктуре дислокации соединяются в устойчивую конфигурацию, а субграница служит полупроницаемой barrier.
As в результате HTMO предлагает наиболее предпочтительное сочетание высокой прочности и пластичности, ударной вязкости и повышенной стойкости к разрушению. Более надежная работа высоконапряженных компонентов способствует повышению чистоты металла и металлургического качества. Повышение чистоты стали связано с удалением вредных примесей (см. раздел 8.2)-серы, фосфора, газообразных элементов-кислорода, водорода, азота, а также неметаллических включений-оксидов, сульфидов и др. в зависимости от их содержания.
В процессе переплава из металла удаляются неметаллические включения, сера и газообразные примеси process. In в промышленности используется несколько методов переплава, таких как вакуумная дуга (VDP), электронно-лучевой (EB), электрошлаковый (ESR), вакуумно-индуцированное растворение (VI) и очистка синтетическим шлаком. При вакуумном и вакуумном переплаве металлы наиболее тщательно очищаются от растворенных газов. Сера практически не удаляется. Напротив, при очистке синтетическим шлаком и СОЭ сера практически полностью удаляется.
Если прочность одинакова, то чем чище металл, тем выше его сопротивление вязкому разрушению и тем ниже порог низкотемпературной хрупкости. Важно увеличить повторную прочность и износостойкость. Винтовая деформация на поверхности детали. Это достигается техническими методами поверхностного упрочнения: поверхностным упрочнением, химико-термической обработкой(азотирование, цементирование), поверхностным пластическим деформированием (дробеструйная обработка, прокатка роликами).
Метод проектирования обеспечивает равную прочность при высоких напряжениях компонентов. При их проектировании исключаются резкие изменения жесткости, глубокие канавки, скругления малого радиуса и другие конструктивные разрезы. Если этого нельзя избежать, то для ослабления концентраций напряжений и формирования остаточных сжимающих напряжений используется локальное упрочнение. К вышеуказанным техническим и металлургическим способам повышения конструкционной прочности стали и сплавов относятся: 1) способ упрочнения, вызывающий увеличение плотности дислокации и снижение ее подвижности. 2) способ обеспечения необходимого запаса пластичности и вязкости, обеспечивающий более равномерное распределение дислокаций и очистку материала от примесей охрупчивания.
Арсенал конструктивных факторов, используемых во 2-й группе методов, определяет следующий допустимый уровень статической прочности конструкции различного назначения. Для стали о = 16004-2200 МПа; титанового сплава ов = 1000-4-1250 МПа; алюминиевого сплава СТН — = 5504-600 МПа. Для многих отраслей промышленности этого недостаточно. Радикально разные методы Использованный для того чтобы достигнуть высокой прочности конструкции, используемой в композиционных материалах, которые новый класс высокопрочных материалов. Таким материалом является композиция из мягкой матрицы и высокопрочных волокон. Волокна укрепляют матрицу и поглощают всю нагрузку.
В этом заключается принципиальное отличие композита от обычного сплава, который, например, упрочняется дисперсным particles. In сплавов, Матрица (твердый раствор) поглощает основную нагрузку, но дисперсные частицы подавляют движение дислокаций в ней, значительно уменьшая ее ductility. In композиционные материалы, нагрузка распознается высокопрочными волокнами, соединенными между собой пластиковой матрицей.
Матричная нагрузка является легкой, передающей и рассеивающей нагрузку между волокнами. Композиционные материалы, например, характеризуются высокой устойчивостью к распространению трещин, поскольку при образовании вследствие разрушения волокон трещины»прилипают» к мягким matrices. In кроме того, композиционные материалы с высокопрочными и высокомодульными волокнами и легкими штампами могут обладать высокой удельной прочностью и жесткостью.
Смотрите также:
Материаловедение — решение задач с примерами
Классификация конструкционных материалов | Общие требования, предъявляемые к конструкционным материалам |
Классификация конструкционных сталей | Конструкционная прочность материалов и критерии ее оценки |