Оглавление:
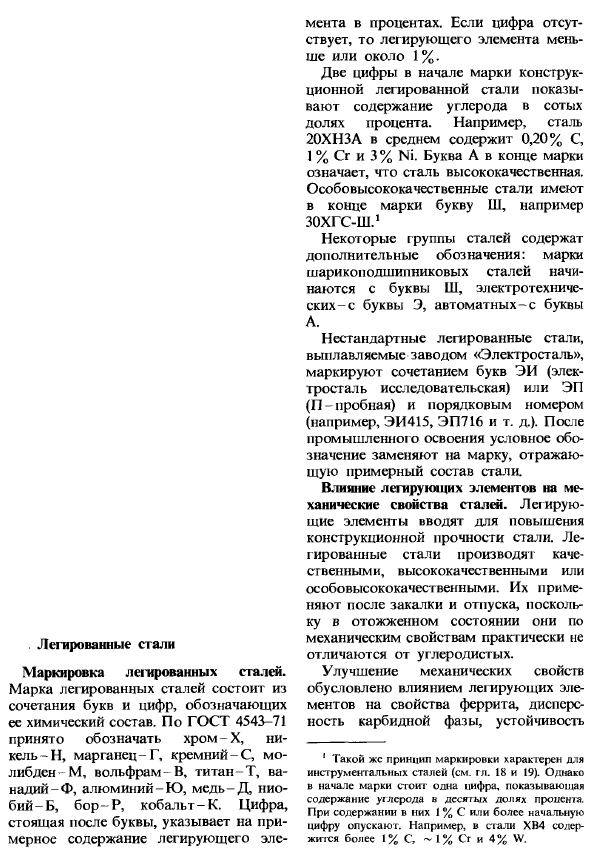
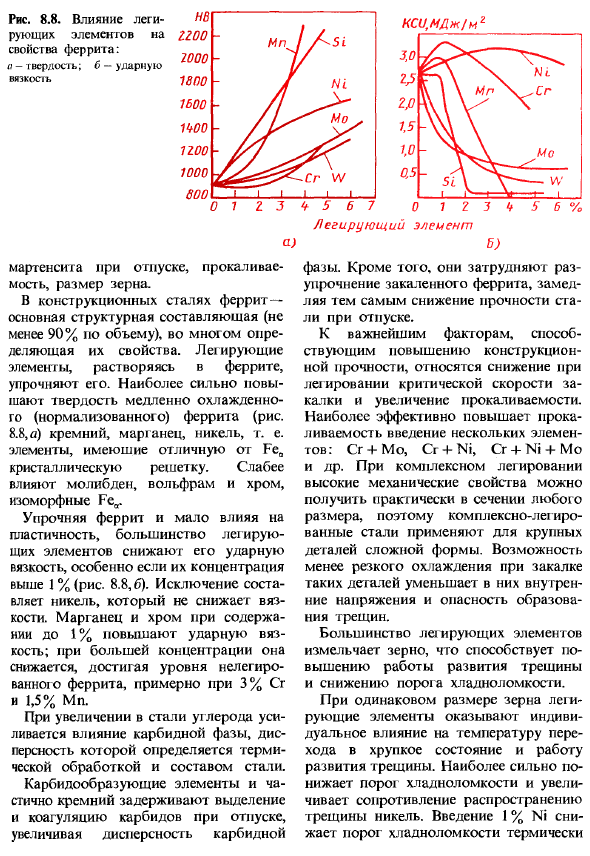
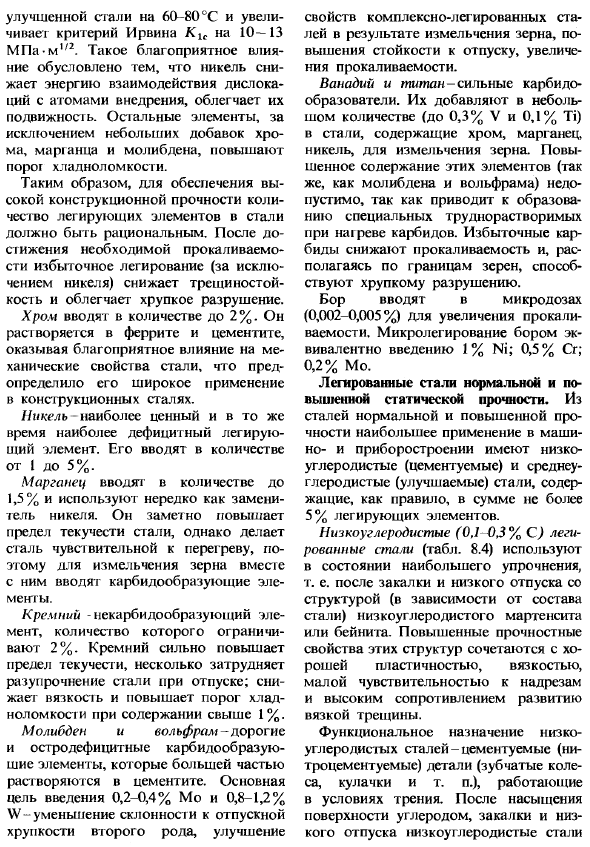
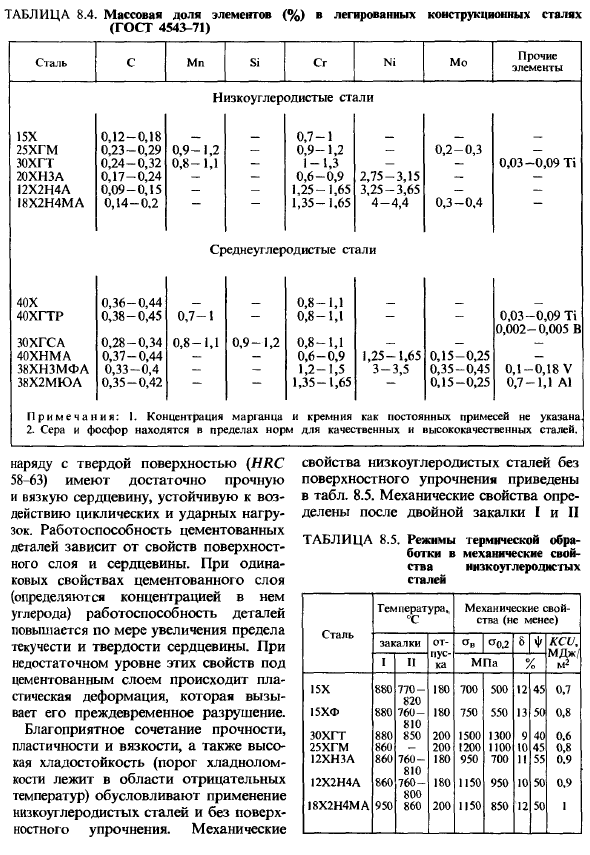
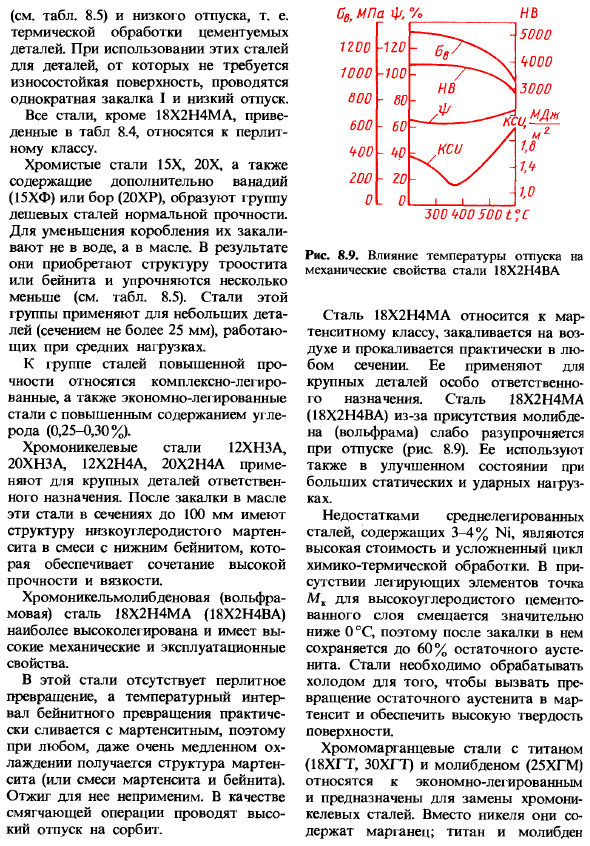
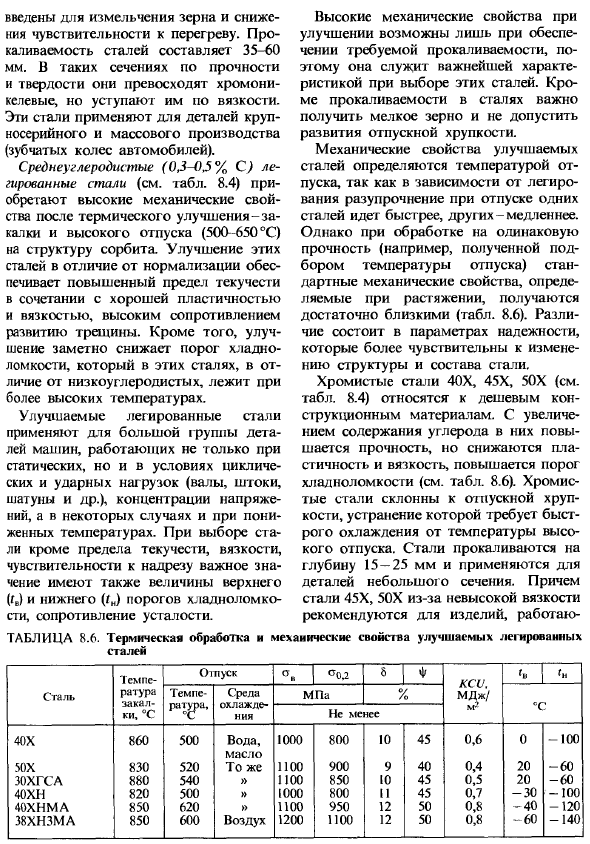
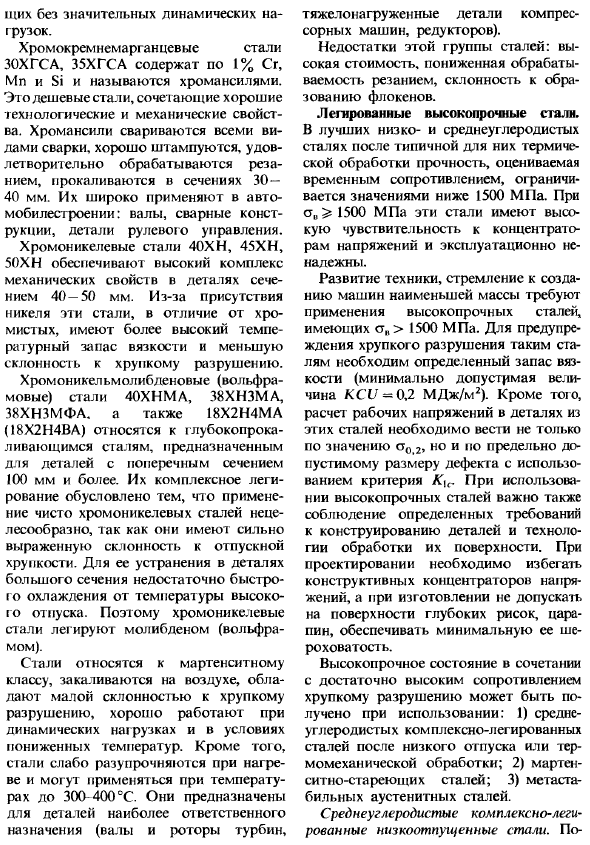
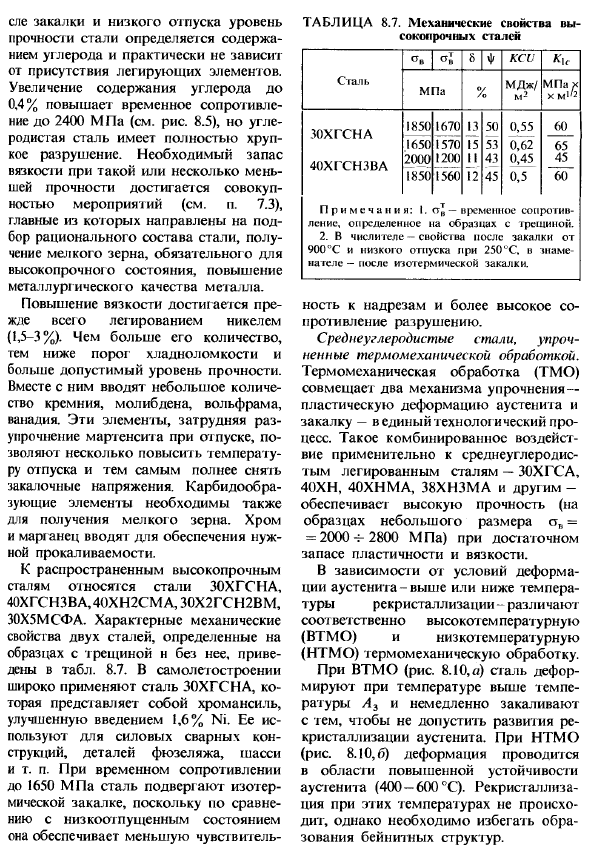
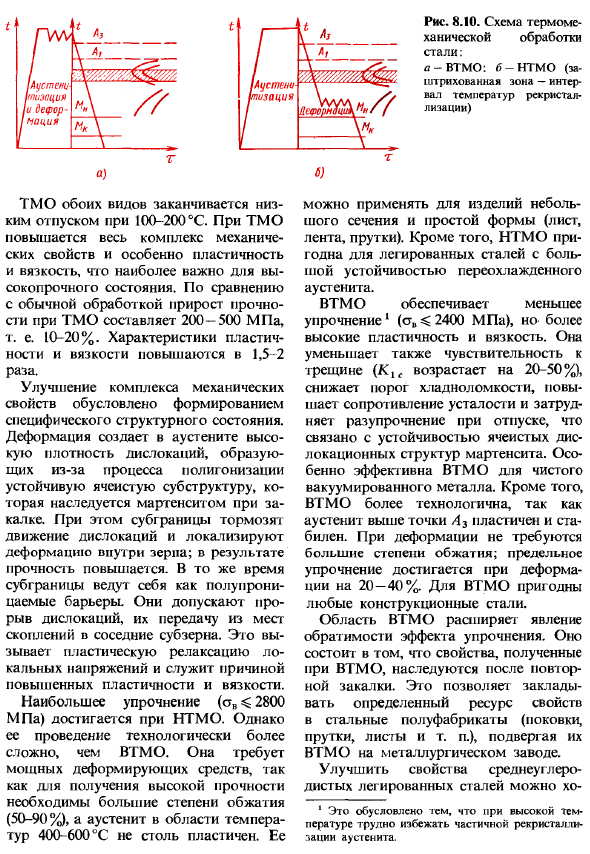
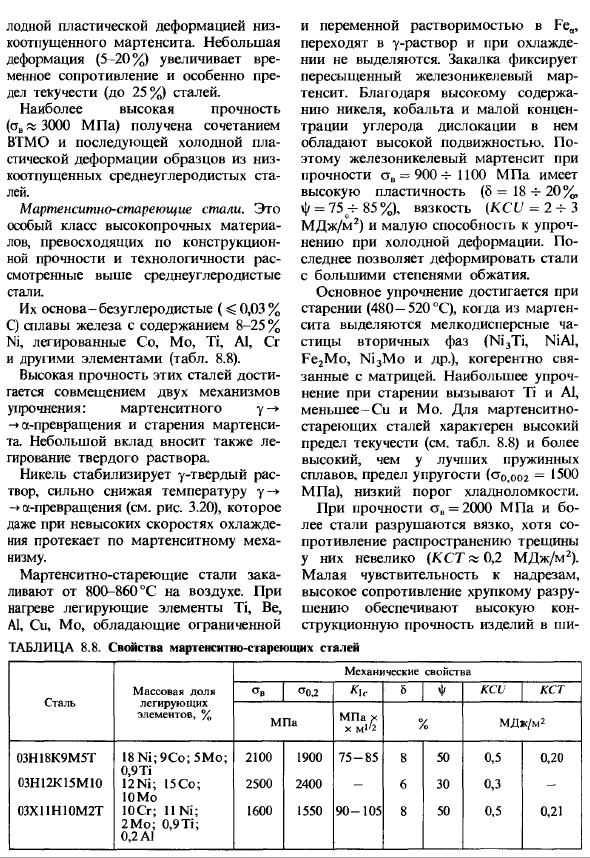
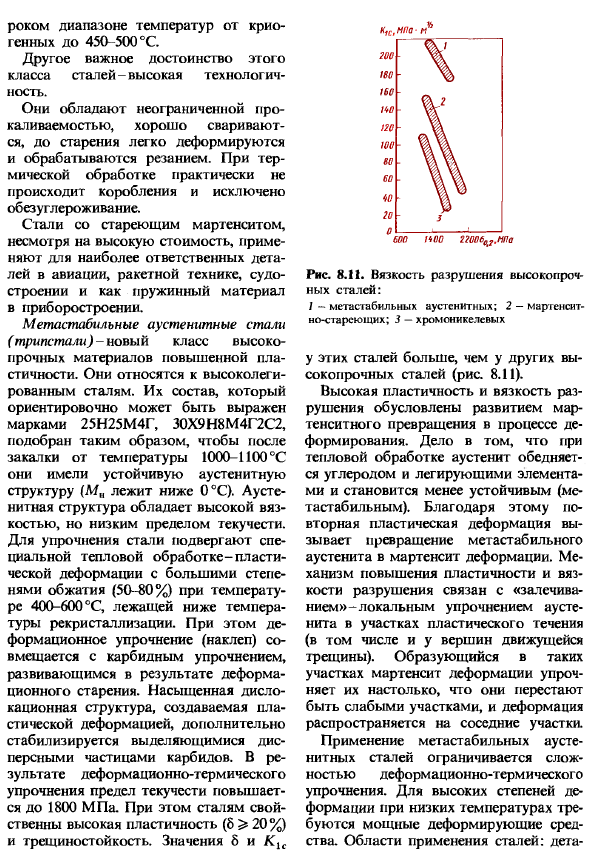
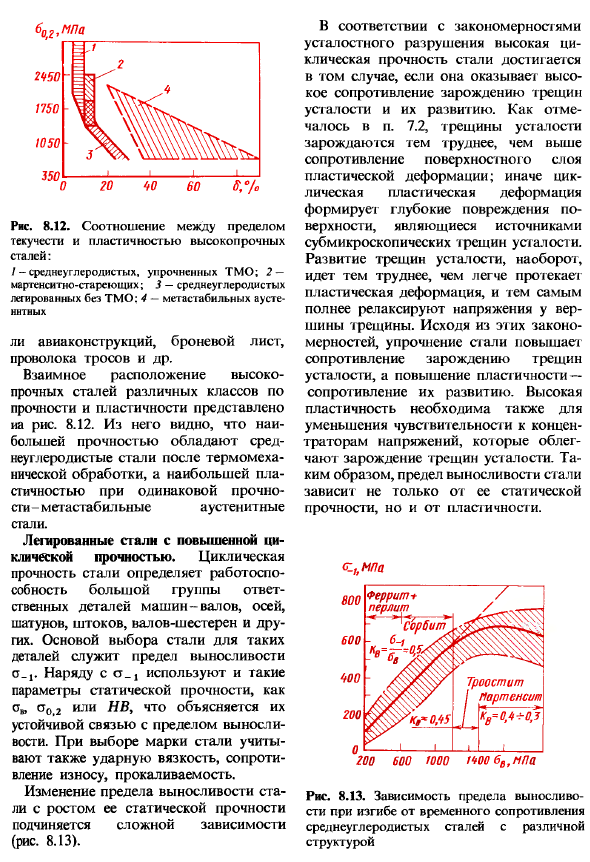
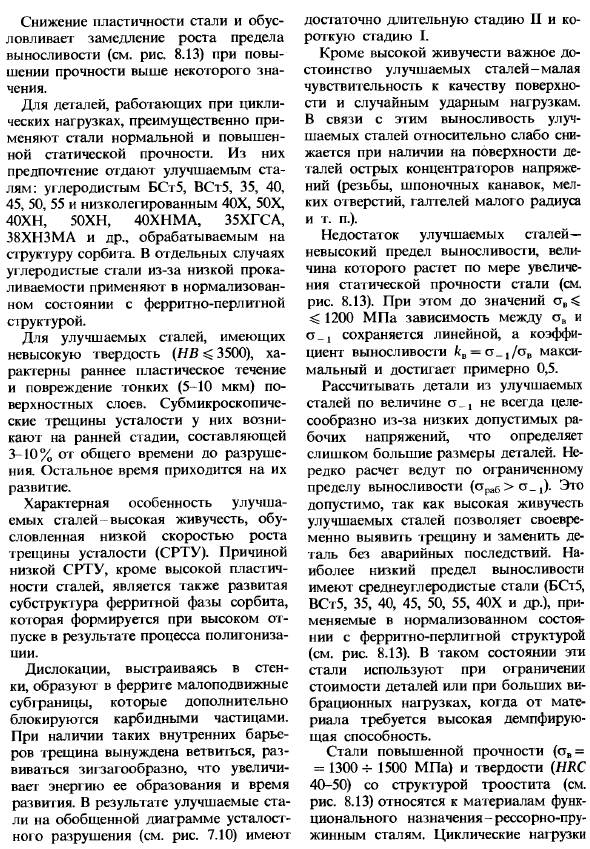
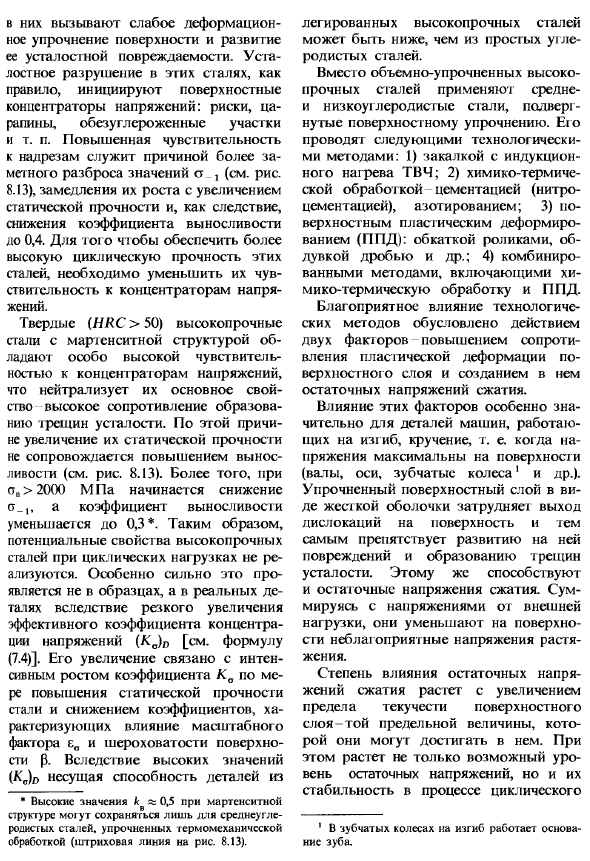
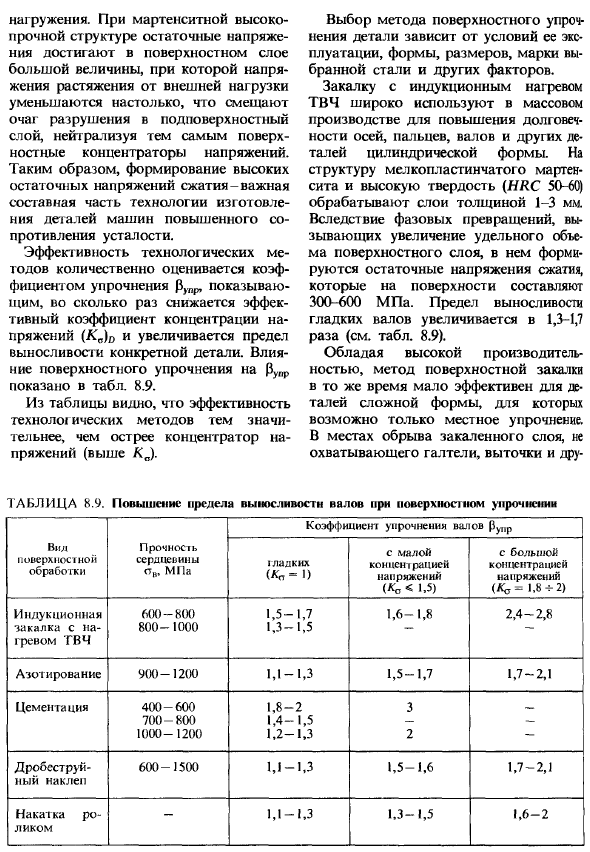
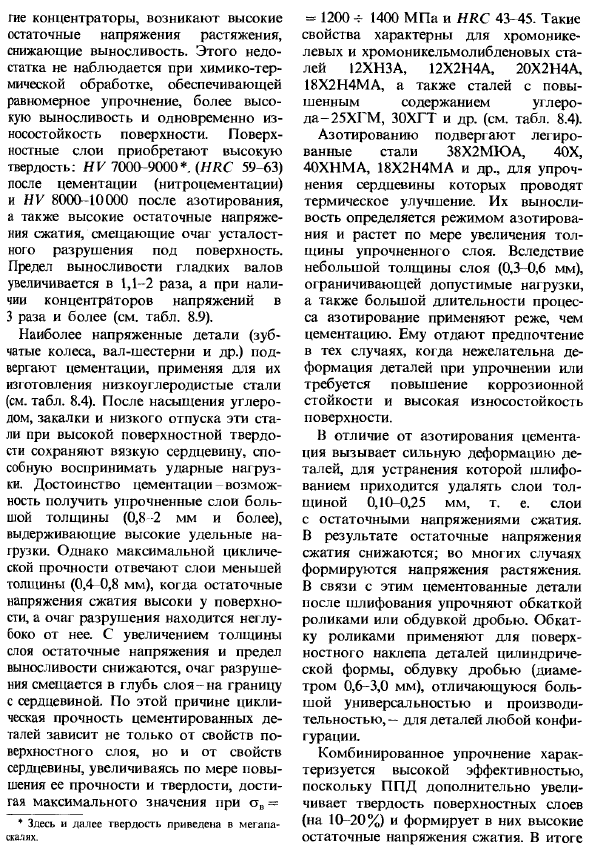
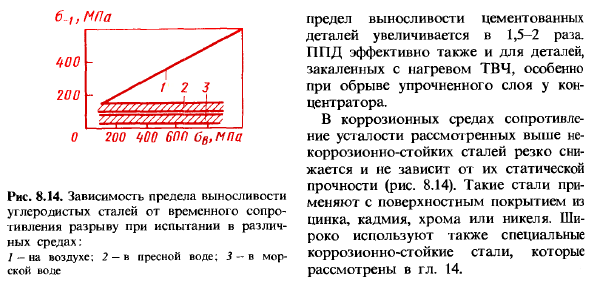

Легированные стали
- Задняя часть сплава Маркировка легированной стали. Марка легированной стали состоит из комбинации букв и цифр, которые указывают на химический состав ЕС. По ГОСТ 4543-71 принято показывать хром х, никель Н, марганец г, кремний с, молибден м, вольфрам Б, Титан Т, ванадий Ф, алюминий у, медь Д, ниобий Б, бор. — Р, кобальт к. цифры после букв указывают примерное содержание легирующих элементов
Процент полицейских. Если нет рисунка, то легирующий элемент составляет менее 1% или около 1%. Первые 2 рисунка марок конструкционных легированных сталей показывают содержание углерода 100% за 1 минуту. Например, сталь 2охнза содержит в среднем 0,20% с, 1% Cr и 3% Ni. Буква А В конце марки означает, что Сталь имеет высокое качество. Имеет ли особо высококачественная сталь букву the в конце марки (например, 30HGS-Sh)?
Некоторые группы стали включают дополнительные названия. Людмила Фирмаль
Марка шарикоподшипниковой стали начинается с буквы begin, электротехническая — с буквы E, а автомат — с буквы A. Нестандартная легированная сталь, выплавляемая на заводе «Электросталь», имеет комбинацию букв EI (электротехническая сталь для исследований) или EP (II trial) и серийный номер (nanpHMq), EI415, EP716 и др. После промышленного освоения обозначение заменяется маркой, отражающей примерный класс стали. Влияние легирующих элементов на механические свойства стали. Легирующие элементы вводятся для повышения конструкционной прочности стали.
Производство легированной стали! Высокое качество, высокое качество или очень высокое качество. Их применяют после закалки и отпуска, поскольку в отожженном состоянии их механические свойства практически не отличаются от углеродных. Улучшение механических свойств обусловлено влиянием выщелачивающих элементов на свойства феррита, дисперсность карбидных фаз и стабильность. *Тот же принцип маркировки характерен и для инструментальной стали (см. главы 18 и 19).
- Но в начале марки были две цифры с содержанием углерода от 10 минут до 1 из 1 пропена. Если он содержит i% C или более, первая цифра опущена. Например, сталь XB4 содержит более 1% C, более 1% Cr и более 4% W. Мартенсит в закаленном, затвердетом, размере зерна. Рисунок 8.8.Влияние легирующих элементов на свойства феррита: о-твердость; б-ударная вязкость В конструкционной стали феррит является основным компонентом (менее 90% по объему), что во многом определяет его характеристики. Легирующие элементы, растворенные в феррите, упрочняются.
Твердость медленно охлаждаемых (нормализованных) ферритов (рис. 8.8, а) наиболее сильно повышается за счет кремния, марганца и никеля, то есть элементов с кристаллической решеткой, отличной от Her0. Молибден, вольфрам и хром в той же форме, что и Fca, слабее. Упрочняя феррит и оказывая незначительное влияние на пластичность,
большинство легирующих элементов снижают свою вязкость, особенно если их концентрация составляет более 1% (рис.8.8.6). Людмила Фирмаль
Исключение составляет никель, который не снижает вязкость. Марганец и хром с содержанием до 1% улучшают вязкость. Когда концентрация высока, она уменьшается, и когда Cr составляет около 3%, а Mp-1,5%, он достигает уровня легированного феррита. С увеличением содержания углеродистой стали увеличивается влияние карбидной фазы, а ее дисперсность определяется термической обработкой и составом стали. Карбидообразующие элементы и частичный кремний задерживают высвобождение и затвердевание карбида при отпуске и увеличивают дисперсность карбида Phase. In дополнение к нему.
Они затрудняют размягчение закаленных ферритов, тем самым замедляя ухудшение прочности стали при отпуске. К наиболее важным факторам, способствующим повышению прочности конструкции, относятся снижение скорости критического упрочнения легирования и увеличение твердения. Введение нескольких элементов, таких как Cr + Mo, Cr + Ni, Cr + Ni + Mo, наиболее эффективно улучшит прокаливаемость. Детали сложной формы. Возможность менее быстрого охлаждения при упрочнении таких деталей снижает риск возникновения внутренних напряжений и их растрескивания. Большинство легирующих элементов дробят частицы, что приводит к увеличению работы по инициированию
трещин и уменьшению холодной трещины nopoa™. Легированные элементы с одинаковым размером зерен оказывают индивидуальное влияние на температуру перехода и работу по распространению трещин в хрупкое состояние. Наиболее сильно снижается порог холодной хрупкости, что повышает устойчивость никеля к распространению трещин. Введение 1%Ni снижает порог
низкотемпературной хрупкости, прокаливаемость и размер зерен термического мартенсита при отпуске. Рисунок 8.8.Влияние легирующих элементов на свойства феррита: о-твердость; б-ударная вязкость В конструкционной стали феррит является основным компонентом (менее 90% по объему), что во многом определяет его характеристики. Легирующие элементы, растворенные в феррите, упрочняются. При отжиге (нормализации) твердость феррита возрастает наиболее сильно(рисунок 8.8, а) элемент с кристаллической решеткой, отличной от кремния, марганца, никеля или Her0. Молибден, вольфрам и хром в той же форме, что
и Fca, слабее. Упрочняя феррит и оказывая незначительное влияние на пластичность, большинство легирующих элементов снижают свою вязкость, особенно если их концентрация составляет более 1% (рис.8.8.6).Исключение составляет никель, который не снижает вязкость. Марганец и хром с содержанием до 1% улучшают вязкость. Когда концентрация высока, она уменьшается, и когда Cr составляет около 3%, а Mp-1,5%, он достигает уровня легированного феррита. С увеличением содержания углеродистой стали увеличивается влияние карбидной фазы, а ее дисперсность определяется
термической обработкой и составом стали. Карбидообразующие элементы и частичный кремний задерживают высвобождение и затвердевание карбида при отпуске и увеличивают дисперсность карбида Phase. In дополнение к нему. Они затрудняют размягчение закаленных ферритов, тем самым замедляя ухудшение прочности стали при отпуске. К наиболее важным факторам, способствующим повышению прочности конструкции, относятся снижение скорости критического упрочнения легирования и увеличение твердения. Введение нескольких элементов, таких как Cr + Mo, Cr + Ni, Cr + Ni + Mo, наиболее эффективно улучшит прокаливаемость. Детали
сложной формы. Возможность менее быстрого охлаждения при упрочнении таких деталей снижает риск возникновения внутренних напряжений и их растрескивания. Большинство легирующих элементов дробят частицы, что приводит к увеличению работы по инициированию трещин и уменьшению холодной трещины nopoa™. Легированные элементы с одинаковым размером зерен
оказывают индивидуальное влияние на температуру перехода и работу по распространению трещин в хрупкое состояние. Наиболее сильно снижается порог холодной хрупкости, что повышает устойчивость никеля к распространению трещин. Введение 1%Ni снижает порог холодной хрупкости термически вместе с твердой поверхностью (HRC 58 63), обладает достаточной прочностью и вязкостью сердцевины, выдерживает многократные нагрузки и ударные нагрузки. Производительность цементной части зависит от характеристик поверхностного слоя и сердцевины. При тех же
свойствах, что и цементный слой (определяется концентрацией углерода в нем), чем выше предел текучести и твердость сердцевины, тем лучше производительность детали. Недостаточный уровень этих свойств приводит к образованию пластической деформации под слоем цемента, что вызывает его преждевременное разрушение. Таблица 8.4.Массовая доля элементов из стали для конструкционных сплавов (% ) (ГОСТ 4543-71) Примечание: 1. концентрация mar (Anza и кремния как постоянной примеси не показана) 2.Сера и фосфор находятся в пределах высококачественной и качественной стали. Предпочтительное сочетание прочности, пластичности, вязкости и высокой холодостойкости (низкотемпературный порог разрушения находится в области отрицательной температуры) определяет применение низкоуглеродистой стали без поверхностного
упрочнения. Механический Характеристики низкоуглеродистой стали без поверхностного упрочнения приведены в таблице. 8.5.Механические свойства I и II после двойного отверждения Таблица 8.5.Режим термической обработки в механических свойствах низкоуглеродистой стали (См. таблицу 8.5) и низкотемпературный отпуск, то есть термическая обработка цементных деталей. При использовании этих сталей для деталей, не требующих износостойкой поверхности, выполняется однократное упрочнение и низкий отпуск. Все стали, кроме 18×2h4ma, перечислены в таблице 8.4 и относятся к классу перлитов. Хромистая
сталь, включая 15X, 20X и даже ванадий (15XF) или бор (20XR), обычно образует группу дешевых сталей strength. To уменьшают искривление, их гасят не водой, а с помощью oil. As в результате он приобретает структуру тростника или бейнита и становится несколько жестким (см. таблицу 8.5).Сталь этой группы применяется для мелких деталей (сечение не более 25 мм), которые работают при средних нагрузках. В группу высокопрочных сталей входят композитные и экономически легированные стали с высоким содержанием углерода (0,25-0,30%). Хромо-никелевая сталь 12хнза,
20ХНЗА, 12×2н4а, 20Х2Н4А используются для крупных важных деталей. После закалки маслом эти стали в сечениях до 100 мм имеют низкоуглеродистую мартенситную структуру в смеси с низким содержанием бейнита, обеспечивая сочетание высокой прочности и ударной вязкости. Хромоникелево-молибденовая (вольфрамовая) сталь 18Х2Н4МА (18Х2Н4ВА) является наиболее высоколегированной и обладает высокими механическими и эксплуатационными свойствами. В этой стали нет перлитного превращения, а температурный диапазон бейнитного превращения существенно
плавится с мартенситным превращением, поэтому даже при очень медленном охлаждении структура мартенситной (или мартенситно-бейнитной смеси) является obtained. No применяется отжиг. как смя Для основной операции, проведенные высокая-сорбит отпуска. Сталь 18Х2Х4МА относится к мартенситной системе, она твердеет на воздухе и затвердевает практически во всех sections. It особенно используется в течение большинства дней для важных целей. Присутствие молибдена (вольфрама) несколько смягчает 18X2H4MA(18X2H4VA) при отпуске (рис.8.9). он также используется
в улучшенных условиях больших статических и ударных нагрузок. 8-9. Влияние температуры отпуска на механические свойства стали 18Х2Н4ВА Недостатком среднелегированной стали, содержащей 3-4%Ni, является высокая стоимость и сложный цикл химического нагрева treatment. In наличие легирующих элементов, точки dth высокоуглеродистого цементного слоя хорошо перемешиваются при температуре менее 0°С, поэтому после закалки в нем сохраняется до 60% остаточного аустенита. Сталь необходимо обрабатывать при низких температурах для превращения остаточного аустенита в мартенсит и получения высокой поверхностной твердости.
Хромохромистые стали, содержащие Титан (18ХГТ, ЗОХГТ) и молибден (25хгм), являются экономически легированными для замены хромоникелевых сталей. Вместо никеля он содержит марганец. Титан и молибден вводятся для измельчения зерен и снижения их чувствительности к перегреву. Термостойкость стали составляет 35-60 mm. In такие секции, он имеет лучшую прочность и твердость, чем хромовый никель, но он уступает! По вязкости. Эти стали используются для крупносерийных и серийных деталей (автомобильных редукторов). Среднеуглеродистая (0,3-0,5% с) легированная сталь (см. табл. 8.4) приобретает высокие механические свойства после закалки структуры сорбита и термического улучшения высокой температуры (500-650°С). в отличие от нормализации, эти улучшения стали обеспечивают хорошую
пластичность и вязкость, увеличение предела текучести в сочетании с высокой устойчивостью к cracking. In кроме того, это улучшение значительно снижает низкотемпературный порог хрупкости при высоких температурах, в отличие от низкоуглеродистых сталей в этих сталях. Улучшенные легированные стали используются для больших групп механических компонентов, которые работают не только в статических, но и в повторяющихся нагрузках и ударных нагрузках (таких как валы, стержни и шатуны), концентрациях напряжений, а в некоторых случаях даже при низких temperatures. In кроме
предела текучести, вязкости и чувствительности к надрезам, при выборе стали также важны значения порога хрупкости при низких температурах и сопротивления усталости верхнего (ge) и нижнего (/n) уровней. Улучшенные высокие механические свойства возможны только в том случае, если обеспечивается необходимое прокаливание™.Наиболее важные характеристики при выборе этих steels. In помимо прокаливаемости стали, важно получать мелкие зерна и предотвращать возникновение отпускной хрупкости. В зависимости от легирования, размягчение при отпуске одних виселиц происходит быстрее, а других медленнее, поэтому
механические свойства стали, подлежащей улучшению, определяются температурой отпуска. Однако при обработке с одинаковой прочностью (например, полученной выбором температуры отпуска) стандартные механические свойства, определяемые натяжением, будут очень близки (табл.8.6).Разница заключается в параметре надежности, который более чувствителен к изменениям структуры и состава стали. Хромистая сталь 40Х, 45х, 50х (см. таблицу 8.4) является недорогим конструкционным материалом. С увеличением содержания в них углерода прочность
увеличивается, но пластичность и вязкость уменьшаются, а порог холодной хрупкости увеличивается(см. таблицу 8.6).Хромистая сталь имеет тенденцию к смягчению хрупкости, и ее удаление требует быстрого охлаждения от высоких температур. Сталь обжигают на глубину 15-25 мм и используют для деталей с небольшим диаметром. cross-section. In кроме того, для изделий, работающих без больших динамических нагрузок, рекомендуется сталь 45х, 50х из-за низкой вязкости. Хром-марганцевой стали ZOKHGSA, 35ХГСА, содержащего 1% хрома, марганца, кремния, соответственно, называется chromansil. Это недорогие стали, которые сочетают в себе
отличные технические и механические свойства. Хромсил сваривается всеми видами сварных швов, хорошо упрочняется, хорошо обрабатывается резанием и прокаливается в сечениях 30-40 мм. Они широко применяются в автомобильной промышленности: валы, сварные конструкции, детали рулевого управления. Хромо-никелевые стали 40ХН, 45ХН и 50ХН обладают широким диапазоном механических свойств при просеивании 40-50 мм. Благодаря наличию никеля эти стали, в отличие от хромовых сталей, имеют высокую температуру вязкости и низкую склонность к хрупкому разрушению. Хромоникелево-молибденовая (вольфрамовая) сталь 40ХНМА, 38ХН3МА, 38ХНЗМФА. И 18Х2Н4МА(18Х2Н4ВА)является поперечным сечением более 100 мм в части высокой прочности сталей. Их сложное легирование обусловлено тем, что применение чистой
хромоникелевой стали нецелесообразно, так как она имеет ярко выраженную тенденцию к облегчению fragility. It недостаточно снять его с большой поперечной деталью Для основной операции, проведенные высокая-сорбит отпуска. Сталь 18Х2Х4МА относится к мартенситной системе, она твердеет на воздухе и затвердевает практически во всех sections. It особенно используется в течение большинства дней для важных целей. Присутствие молибдена (вольфрама) несколько смягчает 18X2H4MA(18X2H4VA) при отпуске (рис.8.9). он также используется в улучшенных условиях больших статических и ударных нагрузок. 8-9. Влияние температуры отпуска
на механические свойства стали 18Х2Н4ВА Недостатком среднелегированной стали, содержащей 3-4%Ni, является высокая стоимость и сложный цикл химического нагрева treatment. In наличие легирующих элементов, точки dth высокоуглеродистого цементного слоя хорошо перемешиваются при температуре менее 0°С, поэтому после закалки в нем сохраняется до 60% остаточного аустенита. Сталь необходимо обрабатывать при низких температурах для превращения остаточного аустенита в мартенсит и получения высокой поверхностной твердости. Хромохромистые стали,
содержащие Титан (18ХГТ, ЗОХГТ) и молибден (25хгм), являются экономически легированными для замены хромоникелевых сталей. Вместо никеля он содержит марганец. Титан и молибден вводятся для измельчения зерен и снижения их чувствительности к перегреву. Термостойкость стали составляет 35-60 mm. In такие секции, он имеет лучшую прочность и твердость, чем хромовый никель, но он уступает! По вязкости. Эти стали используются для крупносерийных и серийных деталей (автомобильных редукторов). Среднеуглеродистая (0,3-0,5% с) легированная сталь (см. табл. 8.4) приобретает высокие механические свойства после закалки
структуры сорбита и термического улучшения высокой температуры (500-650°С). в отличие от нормализации, эти улучшения стали обеспечивают хорошую пластичность и вязкость, увеличение предела текучести в сочетании с высокой устойчивостью к cracking. In кроме того, это улучшение значительно снижает низкотемпературный порог хрупкости при высоких температурах, в отличие от низкоуглеродистых сталей в этих сталях. Улучшенные легированные стали используются для больших групп механических компонентов, которые работают не только в статических,
но и в повторяющихся нагрузках и ударных нагрузках (таких как валы, стержни и шатуны), концентрациях напряжений, а в некоторых случаях даже при низких temperatures. In кроме предела текучести, вязкости и чувствительности к надрезам, при выборе стали также важны значения порога хрупкости при низких температурах и сопротивления усталости верхнего (ge) и нижнего (/n) уровней. Улучшенные высокие механические свойства возможны только в том случае, если обеспечивается необходимое прокаливание™.Наиболее важные характеристики при выборе этих steels. In помимо прокаливаемости стали, важно получать мелкие
зерна и предотвращать возникновение отпускной хрупкости. В зависимости от легирования, размягчение при отпуске одних виселиц происходит быстрее, а других медленнее, поэтому механические свойства стали, подлежащей улучшению, определяются температурой отпуска. Однако при обработке с одинаковой прочностью (например, полученной выбором температуры отпуска) стандартные механические свойства, определяемые натяжением, будут очень близки (табл.8.6).Разница заключается в параметре надежности, который более чувствителен к изменениям структуры и состава стали. Хромистая сталь 40Х, 45х,
50х (см. таблицу 8.4) является недорогим конструкционным материалом. С увеличением содержания в них углерода прочность увеличивается, но пластичность и вязкость уменьшаются, а порог холодной хрупкости увеличивается(см. таблицу 8.6).Хромистая сталь имеет тенденцию к смягчению хрупкости, и ее удаление требует быстрого охлаждения от высоких температур. Сталь обжигают на глубину 15-25 мм и используют для деталей с небольшим диаметром. cross-section. In кроме того, для изделий, работающих без больших динамических нагрузок, рекомендуется сталь 45х, 50х из-за
низкой вязкости. Хром-марганцевой стали ZOKHGSA, 35ХГСА, содержащего 1% хрома, марганца, кремния, соответственно, называется chromansil. Это недорогие стали, которые сочетают в себе отличные технические и механические свойства. Хромсил сваривается всеми видами сварных швов, хорошо упрочняется, хорошо обрабатывается резанием и прокаливается в сечениях 30-40 мм. Они широко применяются в автомобильной промышленности: валы, сварные конструкции, детали рулевого управления. Хромо-никелевые стали 40ХН, 45ХН и 50ХН обладают широким диапазоном механических свойств при просеивании 40-50 мм. Благодаря наличию
никеля эти стали, в отличие от хромовых сталей, имеют высокую температуру вязкости и низкую склонность к хрупкому разрушению. Хромоникелево-молибденовая (вольфрамовая) сталь 40ХНМА, 38ХН3МА, 38ХНЗМФА. И 18Х2Н4МА(18Х2Н4ВА)является поперечным сечением более 100 мм в части высокой прочности сталей. Их сложное легирование обусловлено тем, что применение чистой хромоникелевой стали нецелесообразно, так как она имеет ярко выраженную тенденцию к облегчению fragility. It недостаточно снять
его с большой поперечной деталью Для основной операции, проведенные высокая-сорбит отпуска. Сталь 18Х2Х4МА относится к мартенситной системе, она твердеет на воздухе и затвердевает практически во всех sections. It особенно используется в течение большинства дней для важных целей. Присутствие молибдена (вольфрама) несколько смягчает 18X2H4MA(18X2H4VA) при отпуске (рис.8.9). он также используется в улучшенных условиях больших статических и ударных нагрузок. 8-9. Влияние температуры отпуска на механические свойства стали 18Х2Н4ВА Недостатком среднелегированной стали, содержащей 3-4%Ni, является высокая стоимость и сложный цикл химического нагрева treatment. In наличие легирующих элементов, точки dth высокоуглеродистого цементного слоя хорошо перемешиваются при температуре менее
0°С, поэтому после закалки в нем сохраняется до 60% остаточного аустенита. Сталь необходимо обрабатывать при низких температурах для превращения остаточного аустенита в мартенсит и получения высокой поверхностной твердости. Хромохромистые стали, содержащие Титан (18ХГТ, ЗОХГТ) и молибден (25хгм), являются экономически легированными для замены хромоникелевых сталей. Вместо никеля он содержит марганец. Титан и молибден вводятся для измельчения зерен и снижения их чувствительности к перегреву. Термостойкость стали составляет 35-60 mm. In такие секции, он имеет лучшую прочность и твердость, чем хромовый никель,
но он уступает! По вязкости. Эти стали используются для крупносерийных и серийных деталей (автомобильных редукторов). Среднеуглеродистая (0,3-0,5% с) легированная сталь (см. табл. 8.4) приобретает высокие механические свойства после закалки структуры сорбита и термического улучшения высокой температуры (500-650°С). в отличие от нормализации, эти улучшения стали обеспечивают хорошую пластичность и вязкость, увеличение предела текучести в сочетании с высокой устойчивостью к cracking. In кроме того, это улучшение значительно снижает низкотемпературный порог хрупкости при высоких температурах, в отличие от низкоуглеродистых сталей в этих сталях. Улучшенные легированные стали используются для больших групп механических компонентов, которые работают не только в статических,
но и в повторяющихся нагрузках и ударных нагрузках (таких как валы, стержни и шатуны), концентрациях напряжений, а в некоторых случаях даже при низких temperatures. In кроме предела текучести, вязкости и чувствительности к надрезам, при выборе стали также важны значения порога хрупкости при низких температурах и сопротивления усталости верхнего (ge) и нижнего (/n) уровней. Улучшенные высокие механические свойства возможны только в том случае, если обеспечивается необходимое прокаливание™.Наиболее важные характеристики при выборе этих steels. In помимо прокаливаемости стали, важно получать мелкие
зерна и предотвращать возникновение отпускной хрупкости. В зависимости от легирования, размягчение при отпуске одних виселиц происходит быстрее, а других медленнее, поэтому механические свойства стали, подлежащей улучшению, определяются температурой отпуска. Однако при обработке с одинаковой прочностью (например, полученной выбором температуры отпуска) стандартные механические свойства, определяемые натяжением, будут очень близки (табл.8.6).Разница заключается в параметре надежности, который более чувствителен
к изменениям структуры и состава стали. Хромистая сталь 40Х, 45х, 50х (см. таблицу 8.4) является недорогим конструкционным материалом. С увеличением содержания в них углерода прочность увеличивается, но пластичность и вязкость уменьшаются, а порог холодной хрупкости увеличивается(см. таблицу 8.6).Хромистая сталь имеет тенденцию к смягчению хрупкости, и ее удаление требует
быстрого охлаждения от высоких температур. Сталь обжигают на глубину 15-25 мм и используют для деталей с небольшим диаметром. cross-section. In кроме того, для изделий, работающих без больших динамических нагрузок, рекомендуется сталь 45х, 50х из-за низкой вязкости. Хром-марганцевой стали ZOKHGSA, 35ХГСА, содержащего 1% хрома, марганца, кремния, соответственно, называется chromansil. Это недорогие стали, которые сочетают в себе отличные технические и механические свойства. Хромсил
сваривается всеми видами сварных швов, хорошо упрочняется, хорошо обрабатывается резанием и прокаливается в сечениях 30-40 мм. Они широко применяются в автомобильной промышленности: валы, сварные конструкции, детали рулевого управления. Хромо-никелевые стали 40ХН, 45ХН и 50ХН обладают широким диапазоном механических свойств при просеивании 40-50 мм. Благодаря наличию никеля эти стали, в отличие от хромовых сталей, имеют высокую температуру вязкости и низкую склонность к хрупкому разрушению. Хромоникелево-молибденовая (вольфрамовая) сталь 40ХНМА,
38ХН3МА, 38ХНЗМФА. И 18Х2Н4МА(18Х2Н4ВА)является поперечным сечением более 100 мм в части высокой прочности сталей. Их сложное легирование обусловлено тем, что применение чистой хромоникелевой стали нецелесообразно, так как она имеет ярко выраженную тенденцию к облегчению fragility. It недостаточно снять его с большой поперечной деталью Для основной операции, проведенные высокая-сорбит отпуска. Сталь 18Х2Х4МА относится к мартенситной системе, она твердеет на воздухе и затвердевает практически во всех sections. It особенно используется в течение большинства дней для важных целей. Присутствие молибдена
(вольфрама) несколько смягчает 18X2H4MA(18X2H4VA) при отпуске (рис.8.9). он также используется в улучшенных условиях больших статических и ударных нагрузок. 8-9. Влияние температуры отпуска на механические свойства стали 18Х2Н4ВА Недостатком среднелегированной стали, содержащей 3-4%Ni, является высокая стоимость и сложный цикл химического нагрева treatment. In наличие легирующих элементов, точки dth высокоуглеродистого цементного слоя хорошо перемешиваются при температуре менее 0°С, поэтому после закалки в нем сохраняется до 60% остаточного
аустенита. Сталь необходимо обрабатывать при низких температурах для превращения остаточного аустенита в мартенсит и получения высокой поверхностной твердости. Хромохромистые стали, содержащие Титан (18ХГТ, ЗОХГТ) и молибден (25хгм), являются экономически легированными для замены хромоникелевых сталей. Вместо никеля он содержит марганец. Титан и молибден вводятся для измельчения зерен и снижения их чувствительности к перегреву. Термостойкость стали составляет 35-60 mm. In такие секции, он имеет лучшую прочность и твердость, чем хромовый никель, но он уступает! По вязкости. Эти стали используются для
крупносерийных и серийных деталей (автомобильных редукторов). Среднеуглеродистая (0,3-0,5% с) легированная сталь (см. табл. 8.4) приобретает высокие механические свойства после закалки структуры сорбита и термического улучшения высокой температуры (500-650°С). в отличие от нормализации, эти улучшения стали обеспечивают хорошую пластичность и вязкость, увеличение предела текучести в сочетании с высокой устойчивостью к cracking. In кроме того, это улучшение значительно снижает низкотемпературный порог хрупкости при высоких температурах, в отличие от низкоуглеродистых сталей в этих сталях. Улучшенные легированные стали используются для больших групп механических компонентов, которые работают не только в статических, но и в повторяющихся нагрузках и ударных нагрузках (таких как
валы, стержни и шатуны), концентрациях напряжений, а в некоторых случаях даже при низких temperatures. In кроме предела текучести, вязкости и чувствительности к надрезам, при выборе стали также важны значения порога хрупкости при низких температурах и сопротивления усталости верхнего (ge) и нижнего (/n) уровней. Улучшенные высокие механические свойства возможны только в том случае, если обеспечивается необходимое прокаливание™.Наиболее важные характеристики при выборе этих steels. In помимо прокаливаемости стали, важно получать мелкие зерна и предотвращать возникновение отпускной хрупкости. В зависимости от легирования, размягчение при отпуске одних виселиц происходит быстрее, а других медленнее, поэтому механические свойства стали, подлежащей улучшению,
определяются температурой отпуска. Однако при обработке с одинаковой прочностью (например, полученной выбором температуры отпуска) стандартные механические свойства, определяемые натяжением, будут очень близки (табл.8.6).Разница заключается в параметре надежности, который более чувствителен к изменениям структуры и состава стали. Хромистая сталь 40Х, 45х, 50х (см. таблицу 8.4) является недорогим конструкционным материалом. С увеличением содержания в них углерода прочность увеличивается, но пластичность и вязкость уменьшаются, а порог холодной хрупкости увеличивается(см. таблицу 8.6).Хромистая сталь
имеет тенденцию к смягчению хрупкости, и ее удаление требует быстрого охлаждения от высоких температур. Сталь обжигают на глубину 15-25 мм и используют для деталей с небольшим диаметром. cross-section. In кроме того, для изделий, работающих без больших динамических нагрузок, рекомендуется сталь 45х, 50х из-за низкой вязкости. Хром-марганцевой стали ZOKHGSA, 35ХГСА, содержащего 1% хрома, марганца, кремния, соответственно, называется chromansil. Это недорогие стали, которые сочетают в себе отличные технические и механические свойства. Хромсил
сваривается всеми видами сварных швов, хорошо упрочняется, хорошо обрабатывается резанием и прокаливается в сечениях 30-40 мм. Они широко применяются в автомобильной промышленности: валы, сварные конструкции, детали рулевого управления. Хромо-никелевые стали 40ХН, 45ХН и 50ХН обладают широким диапазоном механических свойств при просеивании 40-50 мм. Благодаря наличию никеля эти стали, в отличие от хромовых сталей, имеют высокую температуру вязкости и низкую склонность к хрупкому разрушению. Хромоникелево-молибденовая (вольфрамовая) сталь 40ХНМА, 38ХН3МА, 38ХНЗМФА. И 18Х2Н4МА(18Х2Н4ВА)является поперечным
сечением более 100 мм в части высокой прочности сталей. Их сложное легирование обусловлено тем, что применение чистой хромоникелевой стали нецелесообразно, так как она имеет ярко выраженную тенденцию к облегчению fragility. It недостаточно снять его с большой поперечной деталью Или ниже, чем температура рекристаллизации, она различает соответствующую высокотемпературную (HTMO) и низкотемпературную (NTMO) термомеханическую обработку. Используя ВТМО (рис. 8.10, а), Сагар деформируется при более высокой температуре, чем А3, и быстро
гасится гемом, чтобы предотвратить возникновение рекристаллизации аустенита. В НТМО (рис. 8.10.6) деформация происходит в области повышенной аустенитной стабильности (400-600°с).Хотя рекристаллизация не происходит при этих температурах, следует избегать образования бейнитных структур. Оба типа ТМЦ заканчиваются низкотемпературным отпуском при 100-200°С. Когда ТМТ увеличивает все диапазоны механических свойств, особенно пластичность и вязкость, это наиболее важно для его высоких условий прочности. По сравнению с обычной обработкой увеличение прочности при ТМТ составляет 200-500 МПа, то есть 10-20%.Свойства
пластичности и вязкости увеличиваются в 1,5-2 раза. один) Рисунок 8. 10.Схема термомеханической обработки стали: а-HTMO: б-НТМО зоны рекристаллизации (заштрихованная диапазон температур) Шесть) Улучшение комплекса механических свойств происходит за счет формирования определенного структурного состояния. Деформация аустенита приводит к образованию дислокаций высокой плотности, а многослойный процесс формирует стабильную субструктуру аустенита. cell. It наследуется мартенситом во время quenching. In в этом случае субграница замедляет движение дислокации и локализует деформацию внутри дислокации. grain.
As в результате, интенсивность increases. At в то же время субграница действует как полупроницаемый барьер. Они позволяют осуществить прорыв дислокаций, переход от узла кластера к соседним подзернам. Это уменьшает местное напряжение и увеличивает пластичность и вязкость. Максимальное упрочнение (ab <2800 МПа) достигается с помощью НТМО. Однако его реализация более технически сложна, чем BIMO. To для получения высокой прочности требуется большая степень сжатия (50-90%), а аустенит в диапазоне температур 400-600°с
не очень пластичен, поэтому требует сильного деформирующего агента. Ее. Его можно использовать для изделий простых форм (листы, ленты, прутки) с небольшим поперечным сечением. НТМО также подходит для переохлажденной аустенитных сталей с высокой стабильностью. HTMO имеет более низкую степень отверждения (1 ° C®» <2400 МПа), но более высокую пластичность и viscosity. It также снижает трещиностойкость (К1е увеличивается на 20-50%), снижает низкотемпературный порог хрупкости, повышает усталостную стойкость и затрудняет размягчение при отпуске. HTMO особенно эффективен для чистого вакуума metal. In кроме того, HTMO является
более технологичным, потому что аустенит является более пластичным и стабильным, чем наконечник. Большое уплотнение не требуется для деформации. Окончательное упрочнение достигается за счет 20-40% деформации. Вся структурная сталь соответствующа для VTMO. Область HTMO расширяет явление обратимости отверждения effect. It заключается в том, что свойства, приобретенные HTMO, наследуются после повторного усиления. Это позволяет размещать определенные активы в стальных полуфабрикатах (поковки, прутки, листы и др.) и подвергают их воздействию НТМО на металлургических заводах. Свойства
среднеуглеродистой легированной стали、 1 это связано с тем, что частичной перекристаллизации аустенита трудно избежать при высоких температурах. Низкий отпуск мартенситной лодочной пластической деформации. При незначительной деформации (5-20%) прочность стали на растяжение увеличивается, в частности, предел текучести (до 25%). Наибольшая прочность (%3000 МПа) была получена при совмещении БиМО и последующей холодной пластической деформации образцов из низкопрочной среднеуглеродистой стали. Марта стала старекпекцией steel. It это
особый класс высокопрочных материалов, который обладает лучшей прочностью конструкции и технологичностью, чем вышеупомянутая промежуточная углеродистая сталь. Их основой является безуглеродистый (<0,03% с) сплав железа с содержанием Ni 8-25%, в котором легированы Co, Mo, Ti, Al, Cr и другие элементы (табл.8.8). Высокая прочность этих сталей достигается сочетанием 2-х механизмов упрочнения. Мартенсит — «Мартенситная метаморфоза и aging. It также немного способствует легированию твердый раствор. Никель стабилизирует твердый раствор γ и значительно снижает температуру превращения γ→α (см. рис. 3.20). он протекает
по мартенситному механизму даже при низких скоростях охлаждения. Марая сталь твердеет от 800°C к 860 ° C в воздухе. При нагревании легирующие элементы Ti, Be, A! КР, МО、 Кроме того, переменная растворимость платы передается в раствор y, который менее заметен при охлаждении. Закалка корректирует перенасыщенный железоникелевый мартенсит. Благодаря большому содержанию никеля, кобальта и низкой концентрации углерода, дислокации в нем обладают высокой подвижностью. Таким образом, железоникелевый мартенсит прочности o = 900 4-1100 МПа обладает высокой пластичностью (5 = 18 4-20%, f = 75 4-85%), вязкостью (KCU = 2
+ 3 МДЖ / м2) и низкой Смогите быть затвердето во время холодной деформации. Последнее позволяет деформировать сталь с большим коэффициентом восстановления. Основные затвердевания достигаются при старении (480-520°С)и мелкодисперсных частицах вторичных фаз (Ni3Ti, Niial, Fe2Mo, Ni3Mo и др.) соединены с матрицей и когерентно отделены от мартенсита. Наибольшее упрочнение при старении происходит за счет Ti и A1, Cu и Mo меньше. Характеристики Марая стали более высокая прочность выхода (см.
таблицу 8.8) и более высокий предел упругости(см. ко. КТГ — ^ 00 МПа) и низким порогом хладноломкости. Если прочность больше чем 2000 MPa, то сталь сломает вязкостное (KST% 0.2 MJ / m2), хотя сопротивление к распространению отказа мало. Низкая чувствительность к надрезам, высокая устойчивость к хрупкому разрушению придают изделию Ши высокую прочность конструкции Таблица 8.8.Характеристики Марая стали Диапазон температур горных пород от криогенных до 450-500°C Еще одним важным преимуществом стали этого класса является передовая технология. 1.
Они имеют неограниченные жаропрочностью, хорошей свариваемостью и легко деформируются и обрабатываются резанием до старения. При термообработке коробление происходит редко, а обезуглероживание исключается. Сталь, в том числе и состаренный мартенсит, несмотря на свою высокую стоимость, используется в важнейших компонентах авиационной, ракетной техники, судостроения, а также в качестве пружинного материала для изготовления музыкальных инструментов. Метастабильный аустенитный штамп (штатив) — это новый класс высокопрочных
материалов с улучшенной пластичностью. Они относятся к высоколегированной стали. Класс 25Н25М4Г,30Х9Н8М4Г2С2 в самое грубое, что может представлять свои композиции, составляет от 1000 до 1100°C при температуре закалки после стабильной аустенитной структуры с выбранным (Ми составляет 0°C менее).Аустенитная структура имеет высокую вязкость, но низкий предел текучести. Для упрочнения сталь подвергается специальной термической обработке-пластической деформации с высокой сжимаемостью (50-80%) при температуре 400-600 ° С ниже рекристаллизации temperature. In в этом случае деформационное упрочнение (закалка) сочетается
с твердосплавным упрочнением, которое происходит в результате деформационного старения. Насыщенная дислокационная структура, образованная пластической деформацией, дополнительно стабилизируется осажденным дисперсным карбидом particles. As в результате деформационного упрочнения предел текучести повышается до 1800 MPa. At в то же время сталь характеризуется высокой пластичностью (6> 20%) и устойчивостью к растрескиванию. Значения B и kic Эти стали больше, чем другие высокопрочные стали (рис.8.11). Рис. 8.11.Трещиностойкость высокопрочной стали: 1-метастабильный аустенит; 2-Маллинг; 3-никель-хром Высокая
пластичность и вязкость разрушения обусловлены развитием мартенситных превращений в процессе деформации. Дело в том, что при термообработке аустенит обедняется углеродом и легирующими элементами, что снижает его стабильность (метастабильность).По этой причине повторная пластическая деформация превращает метастабильный аустенит в деформированный мартенсит. Механизмы, повышающие пластичность и вязкость разрушения, связаны с «заживлением» локального упрочнения аустенита в области пластического течения (включая вершину движущихся
трещин).Деформация мартенсита, образующегося в таких областях, уже не является слабой областью, потому что она очень сильно их усиливает, и деформация распространяется на соседние области Применение метастабильных аустенитных сталей ограничено сложностью деформационного упрочнения. Высокая степень деформации при низких температурах требует сильного деформирующего агента. Ассортимент стали: детская Конструкция воздушных судн, броневой лист, веревочка провода и так далее. Рис. 8.12.Соотношение предела текучести и пластичности высокопрочной стали: срсднсарбонных, закаленных ТМТ; 2 — мартенсит мусиан; 3-среднеуглеродистый легированный без ТМТ: 4-метастабильный аустенит На рисунке показаны относительные положения высокопрочных сталей различных классов по прочности
и пластичности. 8.12.It можно видеть, что среднеуглеродистая сталь обладает наибольшей прочностью после термомеханической обработки, и можно видеть метастабильную аустенитную сталь такой же прочности. Вы также можете использовать его в качестве шаблона для вашего сайта. Легированная сталь с улучшенной прочностью цикла. Повторная прочность стали определяет производительность большой группы важных компонентов, таких как механические валы, оси, шатуны, стержни и зубчатые валы. Основой выбора стали для таких деталей является предел выносливости o_P. наряду с a_ используются также параметры
статической прочности, такие как o0> 2 или HB. Это объясняется устойчивой связью с пределом выносливости. При выборе марки стали также учитываются ударная вязкость, износостойкость и прокаливаемость. Изменение предела выносливости стали с увеличением статической прочности следует сложной зависимости(рисунок 。 8.13). В соответствии с законом усталостного разрушения, высокая циклическая прочность стали достигается, если она проявляет высокую устойчивость к зарождению усталостных трещин и их development. As отмеченные в разделе 7.2, зародыши
усталостных трещин, чем выше сопротивление изнашиваемого слоя пластической деформации, тем сложнее он становится. В противном случае периодическая пластическая деформация приведет к образованию глубоких поверхностных повреждений, которые вызовут очень малую усталостную трещину. С другой стороны, возникновение усталостных трещин становится более трудным, так как пластическая деформация становится легче, и геммы более полно снимают напряжение вершины трещины. Исходя из этих закономерностей, упрочнение платков повышает устойчивость к зарождению усталостных трещин, а увеличение пластичности повышает их устойчивость к их развитию. Высокая пластичность также необходима для снижения чувствительности к концентрация
м напряжений, что способствует возникновению усталостных трещин. Поэтому предел прочности стали зависит не только от ее статистической прочности, но и от ее пластичности. < LhMna зоопарк 600 гав, гав, 6В, ННА Рис. 8.13.Зависимость предела прочности при изгибе от временного сопротивления среднеуглеродистой стали с различными конструкциями При снижении пластичности стали рост предела усталости замедляется (см. рис. 8.13), а прочность выше определенного значения возрастает. Для деталей, работающих при многократных нагрузках, обычно используют сталь с повышенной
статической прочностью. Среди них предпочтение отдается углеродистой стали BSt5, VSt5, 35, 40, 45, 50, 55 и улучшенная сталь с низкими узлами! 40Х, 50Х, 40XH, 50ХН, 40XHMA, 35HGCA、 38XH3MA и соавт. Лечение сорбитом structure. In в некоторых случаях используется углеродистая сталь с нормализованной ферритно-перлитной структурой из-за ее низкой закалочности. Улучшенная сталь низкой твердости (HB <3500) характеризуется ранним пластическим течением и повреждением тонкого (5-10 мкм) поверхностного слоя. Их субмикронные усталостные трещины возникают на ранних стадиях и составляют 3-10% от общего времени разрушения. Остальное время уходит на разработку. Особенностью
стали, которая была улучшена, является ее высокая жизнеспособность из-за низкой скорости роста усталостных трещин (SRTU).помимо высокой пластичности стали, причиной низкой SRTU является также развитая субструктура сорбитовой ферритной фазы, которая образуется при высоких температурах отпуска в результате полигонального процесса. Дислокации, выстилающие стенки, образуют в феррите инертный феррит и далее блокируются частицами карбида. При таком внутреннем барьере трещины вынуждены разветвляться, развиваться в зигзаги, что увеличивает энергию и время развития их formation. As в результате улучшенная
сталь в обобщенной диаграмме усталостного разрушения (см. Рисунок 7.10) имеет вид、 Достаточно длительный этап 11 и короткого этапа я Помимо высокой живучести, важным преимуществом усовершенствованного изделия является низкое качество поверхности и чувствительность к случайному удару loads. In в связи с этим долговечность улучшенной стали относительно слабо снижается при наличии резкой концентрации напряжений на поверхности детали (винтовые резьбы, шпоночные канавки, мелкие отверстия, скругления малого радиуса и др.). Недостатком
улучшаемой стали является ее низкий предел прочности. Это предельное значение возрастает с увеличением статической прочности стали(см. рис. 8.13). в то же время до значения an<1200 МПа зависимость между и o_ сохраняется линейным образом, а коэффициент выносливости Av = o_j / oB достигает максимума около 0,5. Не всегда рекомендуется рассчитывать деталь из улучшенной стали размера с, так как допустимые рабочие напряжения невелики, а размеры детали слишком велики. Часто расчеты выполняются в соответствии с ограничением пределов выносливости (Oj»g> ^ — i) —
это допустимо. Это связано с высокой живучестью улучшенной стали, что позволяет выявлять трещины и заменять детали, не приводя к аварийным ситуациям. Среднеуглеродистая сталь (BST5, BST), используемая в нормализованном состоянии в ферритно-перлитной структуре 5、35、40、45、50、55、40х и др.) будет иметь самый низкий предел усталости (см. рис. 8.13). в этом состоянии эти стали используются с высокими вибрационными нагрузками при ограничении стоимости детали или когда материал требует высокой демпфирующей способности. Сталь с повышенной прочностью (s = 1300-e-1500 МПа) и твердостью (HRC 40-50) с тростниковой структурой
(см. рис.8.13) является функциональным материалом, пружинной сталью. Их многократные нагрузки вызывают слабое деформационное упрочнение поверхности и возникновение усталостных повреждений. Усталостное разрушение этих сталей обычно инициируется устройством концентрации поверхностных напряжений. Риск, царапины, зона обезуглероживания и так далее. Силы, и, как следствие, снижение коэффициента выносливости до 0.4.To увеличьте прочность цикла этих сталей, чувствительность
к концентрации напряжений необходимо уменьшить. У меня мартенситная структура твердая (HRC> 50) высокопрочная сталь! Особенно высока чувствительность к концентраторам напряжений, нейтрализующим высокую устойчивость к усталостному растрескиванию, что является его главным свойством. По этой причине увеличение статической прочности не сопровождается увеличением выносливости (см. рис. 8.13). кроме того, уменьшение o_i начинается при N> 2 (xx) МПа, а коэффициент выносливости уменьшается до 0,3*.Таким образом, реализуются потенциальные свойства высокопрочных сталей при циклических НС нагрузках. Это не совсем образец, а эффективный коэффициент концентрации напряжений (Ko) 0 [справочная формула (7.4)].Его увеличение связано
с тем, что по мере увеличения статической прочности стали коэффициент со интенсивно возрастает, а коэффициент характеризует влияние масштабного коэффициента ω и шероховатости поверхности P. By высокое значение (KC) D、 Высокопрочная сталь, которая легируется, может быть ниже, чем простая углеродистая сталь. Вместо высокопрочной стали применяют средне-и низкоуглеродистые стали, подвергнутые поверхностному упрочнению. Используй его! Следующие технические способы: 1) тушение индукционным нагревом током высокой частоты. 2)химико-термическая обработка цементация (мягкое азотирование), азотирования; 3) поверхностным пластическим деформированием (ППД): прокатка роликом, удар в удар, и т. д. 4) химическая термическая обработка и составной метод включая PPD. Положительный эффект технического способа обусловлен действием
2 факторов: повышением сопротивления пластической деформации поверхностного слоя и образованием в нем остаточных сжимающих напряжений. Влияние этих факторов особенно важно для деталей, работающих на станках, которые имеют максимум изгиба, скручивания, то есть напряжения на поверхности (вал, ось, шестерня 1 и др.).Упрочненные поверхностные стойки в виде твердой оболочки затрудняют выход дислокаций на поверхность, тем самым предотвращая развитие поверхностных повреждений и образование усталостных трещин. Сжатие Octacquick также способствует этому. Если напряжение от внешней нагрузки взять вместе, то напряжение растяжения на поверхности уменьшается. Степень влияния остаточных сжимающих напряжений возрастает с увеличением
предела текучести поверхностного слоя. Это конечное значение, которое может быть достигнуто в поверхности layer. At при этом возможный уровень остаточных напряжений не только возрастает, но и повышает периодическую устойчивость. * Высокое значение k = 0,5 в мартенситной ткани может быть сохранено только в среднеуглеродистой стали, закаленной термической обработкой (пунктирная линия на рис.8.13). 1 в зубчатом колесе корень зуба изогнут. Loading. In высокопрочная структура мартенсита, когда остаточное напряжение поверхностного слоя достигает большого
значения, напряжение растяжения от внешней нагрузки значительно уменьшено, фокус трещиноватости двигает к подповерхностному слою, и поверхностная часть концентрации напряжений нейтрализована. Поэтому формирование высоких остаточных напряжений сжатия является важным элементом в технологии изготовления деталей машин с повышенной усталостной стойкостью. Эффективность технического метода количественно определяется коэффициентом упрочнения, который показывает, во сколько раз уменьшается эффективный коэффициент концентрации напряжений (КС) D и увеличивается предел выносливости отдельных деталей. Р) / таблица показывает влияние поверхностного упрочнения на 1р. 8.9. В таблице показана эффективность техноло! Чем больше число методов, тем резче концентрация напряжений (выше Ko). Выбор
способа поверхностного упрочнения детали зависит от условий ее эксплуатации, формы, размеров, марки выбранной стали и других факторов. Индукционный нагрев HFC широко используется в массовом производстве для повышения долговечности осей, пальцев, валов и других цилиндрических деталей. Слой толщиной 1-3 мм обработан с тонкой пластинчатой мартенситной структурой и высокой твердостью (HRC 50-60).За счет фазового перехода, который вызывает увеличение удельного объема поверхностного слоя, на поверхностном слое образуется остаточное сжимающее
напряжение, а на поверхности оно составляет 300-600 МПа. Предел выносливости гладких валов увеличивается в 1,3-1,7 раза(см. таблицу 8.9). Высокая производительность и в то же время метод поверхностного упрочнения менее эффективен для деталей сложной формы, которые могут быть упрочнены только локально. Где слой отверждения не распространяется на филе, подрезы и т. д. Его 8,9.Повышенная прочность вала при поверхностном упрочнении Типы поверхностного покрытия 1 прочность ядра ПВ、 Концентраторы имеют высокие остаточные напряжения растяжения, которые снижают долговечность. Этот недостаток не обнаруживается при химико-термической обработке и обеспечивает равномерное
упрочнение, более высокую прочность и износостойкость поверхности. Твердость поверхностного слоя выше: HV 7000 9000♦. (HRC 59-63) постцементируя (обуглероживая азотирование) и NU 8000 10000 после азотирования, так же, как высоким остаточным сжимающим напряжением, заменяют фокус трещиноватости усталости подповерхностной поверхности. Предел выносливости гладкого вала увеличивается в 1,1-2 раза, а при наличии устройства концентрации напряжений-более чем в 3 раза(см. таблицу 8.9). Наиболее напряженные детали (например, шестерни и валы шестерен) обрабатываются затиркой с использованием низкоуглеродистой стали для изготовления (см. таблицу 8.4).После
насыщения углеродом, закалки и низкого отпуска эти стали сохраняют вязкую сердцевину, которая может поглощать ударные нагрузки с высокой поверхностной твердостью. Преимущество цементации заключается в том, что можно получить толстый упрочненный слой (не менее 0,8-2 мм), толщина которого выдерживает высокие удельные нагрузки. Однако если остаточное сжимающее напряжение на поверхности велико, а очаг разрушения находится на ее стороне, то более тонкий слой (0,4-0,8 мм) соответствует максимальному периодическому strength. As толщина
слоя увеличивается, остаточные напряжения и предел выносливости уменьшаются, а очаг разрушения перемещается вглубь слоя и к границе с ядром. По этой причине повторная прочность соединительной детали зависит не только от характеристик поверхностного слоя, но и от характеристик сердечника, которые увеличиваются за счет увеличения его прочности и твердости, достигая максимального значения при o / 5=. ♦Твердость ниже обозначается мегапаскалей. = 1200 4-1400 МПа и HRC 43-45.Такими свойствами являются свойства хромоникелевой и хромоникелево-молибденовой стали 12хнза, 12×2н4а, 20Х2Н4А, 18Х2Н4МА, а также
высокое содержание углерода в стали (25ХГМ, ЗОХГТ и др.) (см. таблицу 8.4). Легированная сталь 38Х2МЮА, 40хнма, 40ХНМА, 18Х2Н4МА и другие азотируются для улучшения сердечника, где выполняется термическое улучшение. Их долговечность определяется площадью азотирования, которая увеличивается с увеличением толщины упрочненного слоя. Толщина слоя для ограничения допустимой нагрузки невелика (O. Z-O. 6 мм), а также из-за большой продолжительности процесса азотирование применяется не чаще, чем цементация. Если деформация детали при упрочнении нежелательна, или если она требует повышения коррозионной
стойкости и высокой износостойкости поверхности, ему отдадут предпочтение. В отличие от азотирования, цементация вызывает серьезную деформацию детали, устраняя шлифование, что требует удаления слоя толщиной 0,10-0,25 мм, то есть слоя с остаточным сжимающим действием stress. As в результате остаточное напряжение сжатия составляет reduced. In много случаев, растяжимое усилие formed. In в связи с этим цементные детали после шлифования упрочняют прокаткой роликом или дробеструйной обработкой. Roll-in применяется для поверхностного упрочнения цилиндрических деталей, дробеструйной обработки дробью (диаметр 0,6-3,0 мм), которая характеризуется отличной универсальностью и производительностью деталей любой конфигурации.
Композиционное упрочнение характеризуется высокой эффективностью, поскольку ППД дополнительно повышает твердость поверхностного слоя (на 10-20%) и формирует высокие остаточные напряжения сжатия. Окончательно Предел выносливости суставной части увеличивается в 1,5-2 раза. PPD также эффективен для деталей, которые затвердели из-за нагрева токами высокой частоты, особенно если слой, затвердевший концентратором, поврежден.
Рис. 8.14.Зависимость пределов выносливости углеродистой стали от переходного предела прочности при испытаниях в различных средах: 1-в воздухе. 2 — в пресной воде; 3-в морской воде В коррозионной среде, сопротивление усталости выше нержавеющей стали значительно уменьшается и не зависит от статической прочности (рис. 8.14).Такая сталь используется в поверхностном покрытии цинка, кадмия, хрома или никеля. Специальная коррозионностойкая сталь. 14.
Смотрите также:
Материаловедение — решение задач с примерами
Стали с улучшенной обрабатываемостью резанием | Влияние углерода и постоянных примесей на свойства стали |
Стали с высокой технологической пластичностью и свариваемостью | Углеродистые стали |