Оглавление:
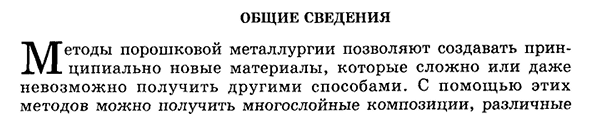
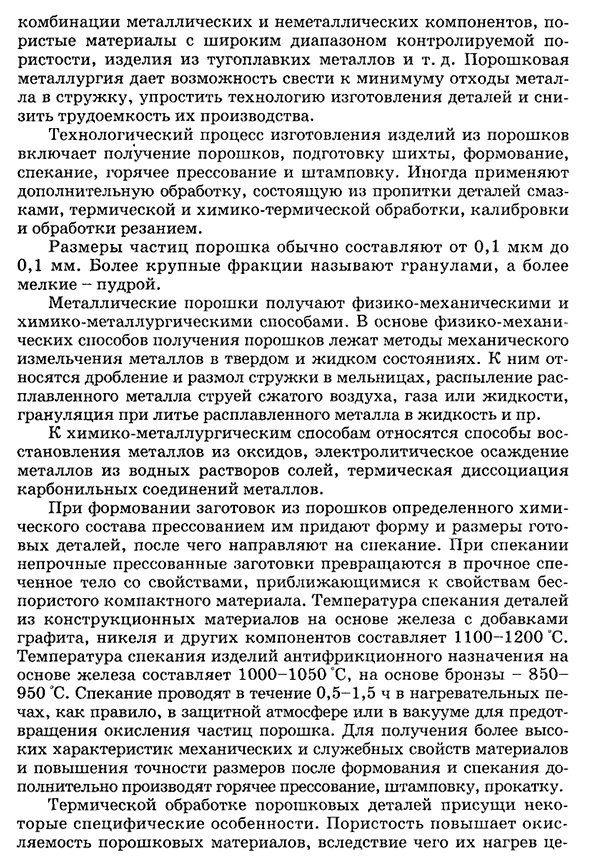
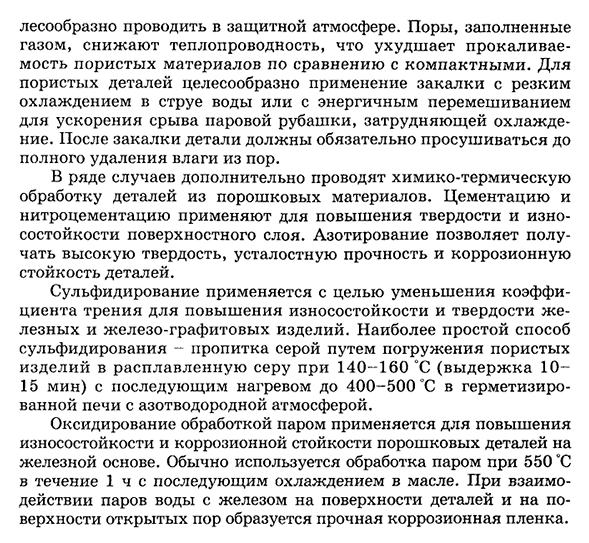

Порошковые материалы общие сведения
- Порошковые материалы общая информация Метод порошковой металлургии позволяет создать принципиально новый материал, который трудно или невозможно получить другими способами. С помощью этих методов могут быть получены различные многослойные композиции Сочетание 487 изделий из металлических и неметаллических компонентов, пористых материалов с широким спектром контролируемых пористых, тугоплавких металлов и др
. Порошковая металлургия сводит к минимуму отходы металла на стружку, упрощает технологию изготовления деталей и позволяет снизить трудоемкость производства. Технологический процесс изготовления изделий из порошка включает получение порошка, подготовку к заполнению, формование, спекание, горячее прессование и штамповку. В некоторых случаях применяется дополнительная обработка, которая
заключается в пропитке деталей смазкой, термической и химической обработке, калибровке и обработке резанием. Людмила Фирмаль
Размер частиц порошка обычно составляет от 0,1 мкм до 0,1 мкм. Металлические порошки получают физико-механическими и химико-металлургическими методами. В основе физико-механического способа получения порошка лежит метод механического измельчения металлов в твердом и жидком состоянии.
К ним относятся измельчение и измельчение стружки в мельнице, распыление расплавленного металла сжатым воздухом, струями газа или жидкости, гранулирование при заливке расплавленного металла в жидкость и др. Химико-металлургические методы включают: метод восстановления металлов из оксидов, электролитическое осаждение металлов из водных растворов солей, термическую диссоциацию карбонильных соединений металлов.
- Когда заготовки формируются из порошков с определенным химическим составом прессом, им придается форма и размер готовой детали, а затем они подаются в процесс спекания, пористый компакт становится близким к твердому спеченному телу, свойства которого перерождаются в хрупкую прессованную заготовку. Температура спекания деталей из конструкционных материалов на основе железа с добавками графита, никеля и других компонентов составляет 1100-1200 ° С.
Температура спекания антифрикционных изделий на основе железа, бронзы-1000-1050℃、850-9,950℃спекание производится в течение 0,5-1,5 часов в нагревательной печи, как правило, в защитной атмосфере, окруженной воздухом или в вакууме, чтобы получить характеристики механических и сервисных материалов для улучшения свойств оригинала после точного формования и спекания, мы также производим тепловой Пресс, пресс-обработку. Термическая обработка порошковых деталей имеет определенные характеристики. Пористость увеличивает окисляемость
порошкового материала, так что нагревание- Защиту 488l рекомендуется проводить в атмосферных условиях. Людмила Фирмаль
Поры, заполненные газами, имеют меньшую теплопроводность, что ухудшает потребность в пористых материалах по сравнению с прокливным компактом. В случае пористых компонентов детали должны быть неизбежно высушены до полного удаления воды из пор после отверждения, чтобы ускорить разложение паровой рубашки, что затрудняет охлаждение, используя закалку при закалке или интенсивное перемешивание в струе воды. В ряде случаев проводится дополнительная химико-термическая обработка деталей из порошкового материала.
Цементация и нитрификация используются для повышения твердости и износостойкости поверхностного слоя. Азотирование позволяет получить высокую твердость, усталостную прочность и коррозионную стойкость деталей. Сульфид используется для снижения коэффициента трения для повышения износостойкости и твердости чугуна и железо-графитовых изделий. Наиболее простым способом сульфидирования является образование сульфидов путем погружения пористого продукта в расплав серы при 140-160 ° с (выдержка 10-15 мин) и нагревания его до 400-500 ° с в закрытой печи с азотно-водородной атмосферой.
Паровое окисление используется для повышения износостойкости и коррозионной стойкости порошковых компонентов на основе железа. Обычно используется паровая обработка при 550°C в течение 1 часа с последующим охлаждением масла. При взаимодействии водяного пара с железом на поверхности деталей и на поверхности открытых пор образуется сильная коррозионная пленка.
Смотрите также:
Конструкционные материалы | Особенности термообработки литейных сталей |
Антифрикционные материалы (гост 26802-86) | Особенности применения литейных сталей |