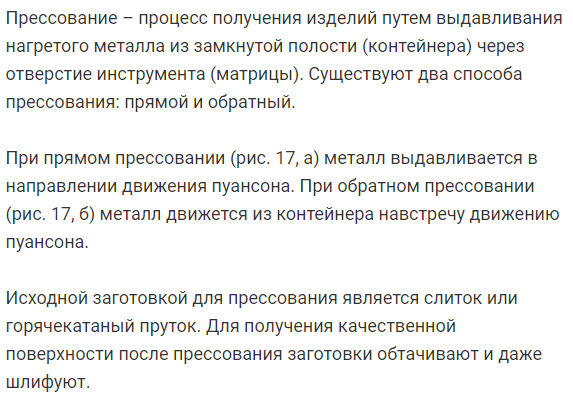

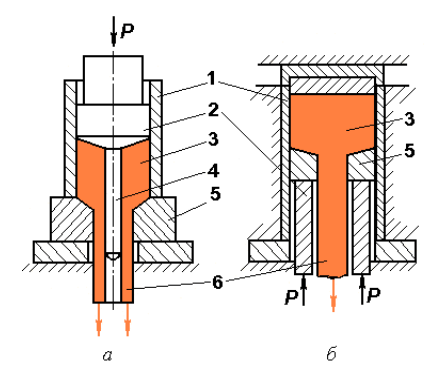


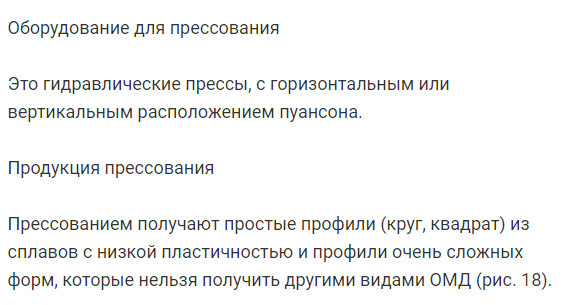
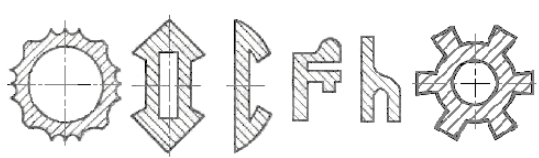
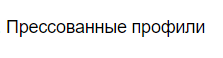
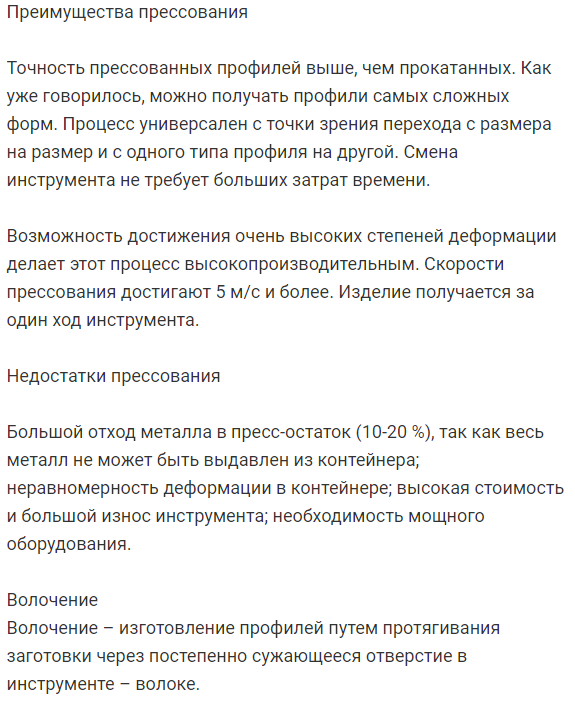
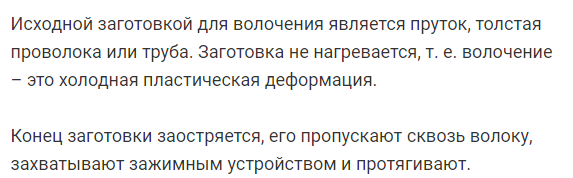
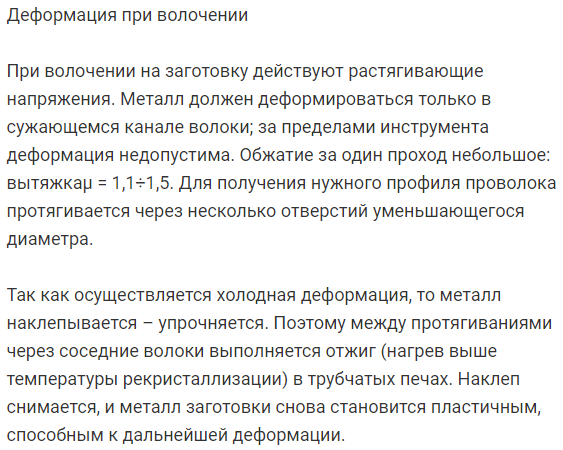
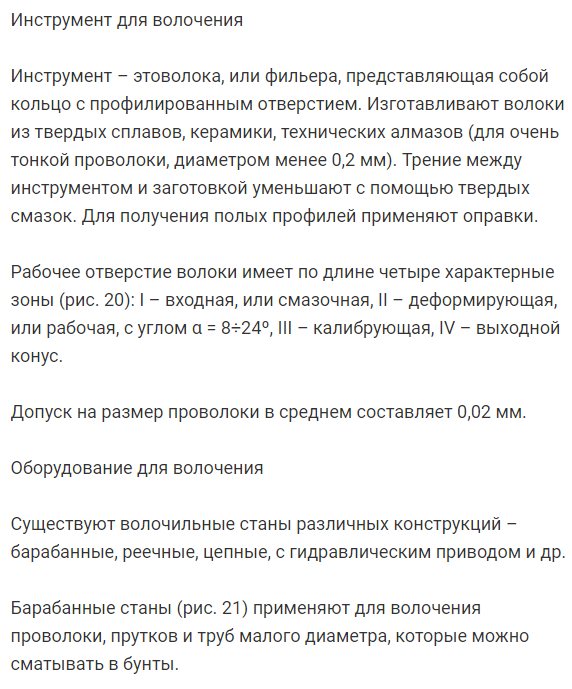
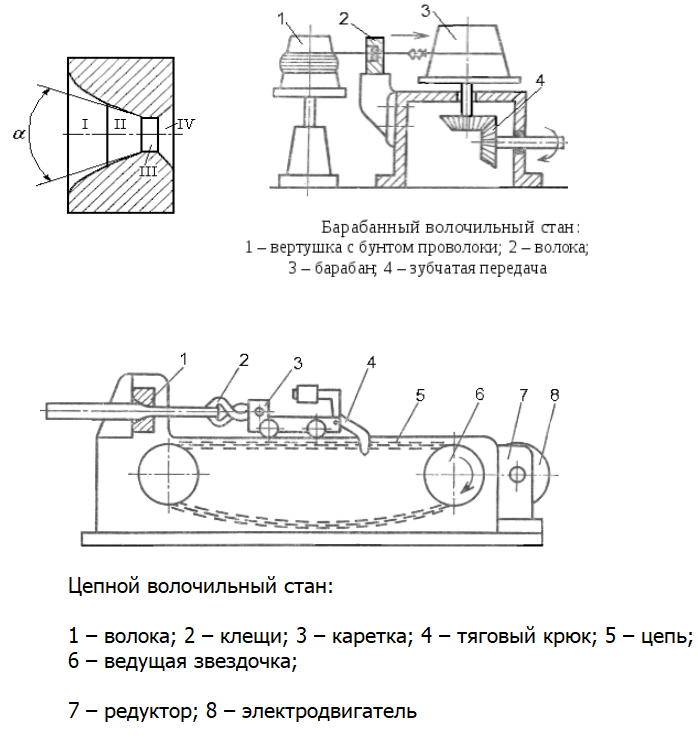
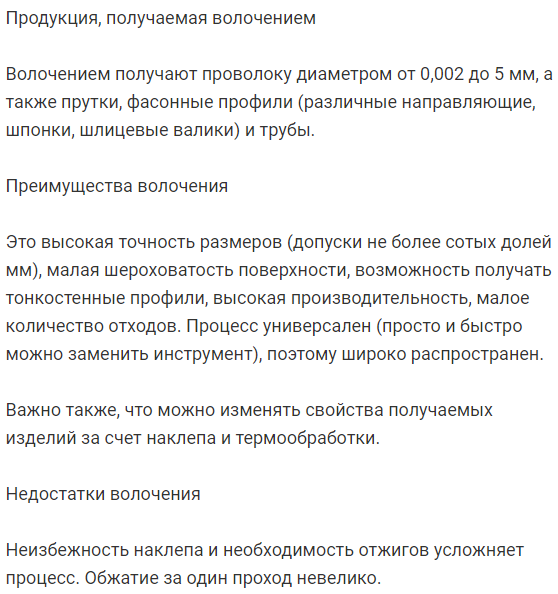


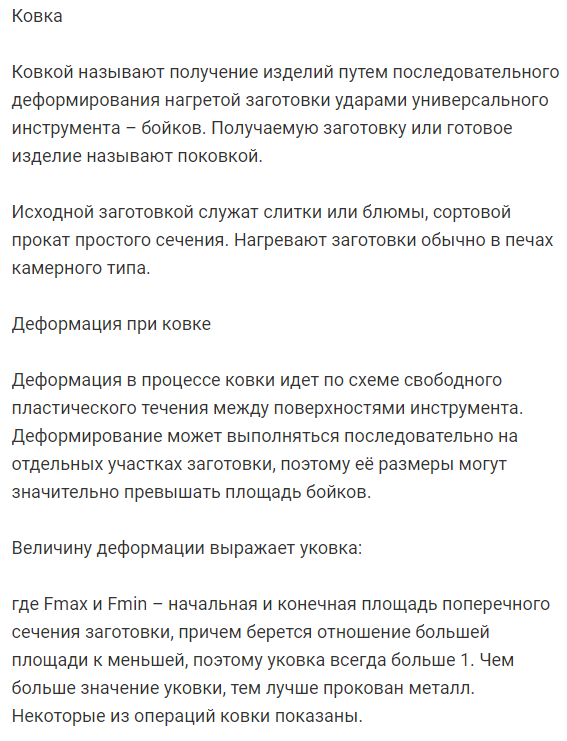
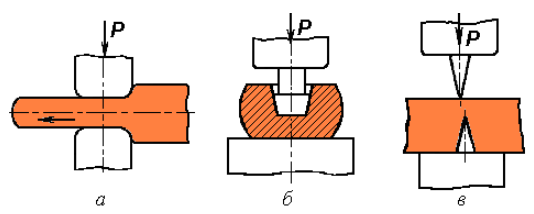
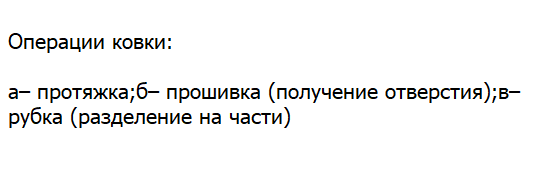
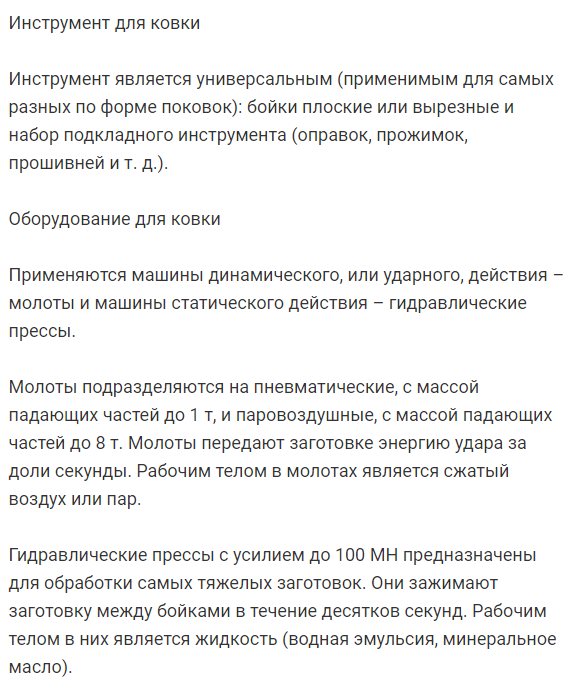
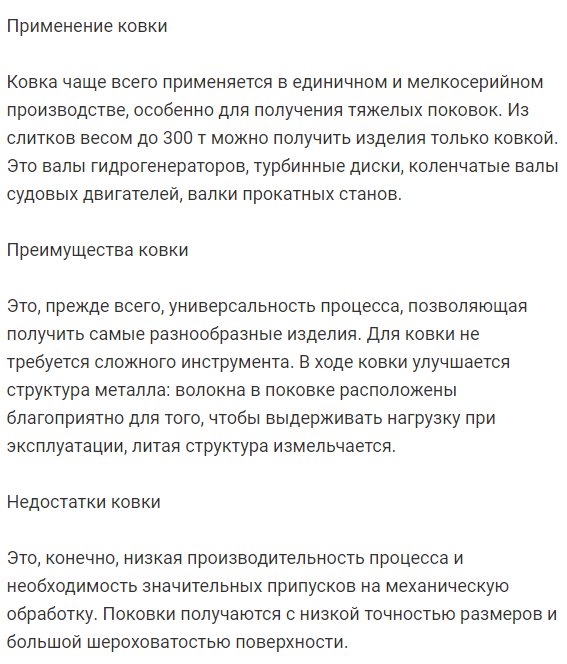
Прессование — это процесс получения продукта путем выдавливания нагретого металла из замкнутой полости (контейнера) через отверстие в инструменте (матрице). Существует два способа нажатия: прямой и обратный.
При прямом нажатии (рис. 17, а) металл выдавливается в направлении движения пуансона. При обратном нажатии (рис. 17, б) металл перемещается из контейнера в направлении движения пуансона.
Первая заготовка пресса — это слиток или горячекатаный пруток. Заготовка полируется и полируется для получения высококачественной поверхности после прессования.
Нагревание происходит в индукционных установках или печах с солевыми ваннами. Цветные металлы прессуются без нагрева.
Нажмите прямой (а) и обратный (б):
1 контейнер. 2-удар, 3-заготовка, 4-игла, 5-матрица, 6-профиль
Пресс деформации
При нажатии реализуется комплексная неоднородная схема сжатия без растягивающего напряжения. Следовательно, можно прессовать даже сталь и сплавы с низкой пластичностью, такие как инструменты.
- Даже хрупкие материалы, такие как мрамор и чугун, могут быть спрессованы. Следовательно, прессование может обрабатывать материалы, которые не могут быть деформированы другими методами из-за их низкой пластичности.
Коэффициент экструзии µ при прессовании может достигать 30-50.
Пресс инструмент
- Инструментами являются контейнеры, пуансоны, штампы и иглы (для полых профилей). Полученный профиль продукта определяется формой отверстий матрицы. Профильное отверстие с иглой. Условия работы инструмента очень сложные: большое контактное давление, износ, нагрев до 800-1200 ° C. Изготовлен из высококачественной инструментальной стали и жаропрочного сплава.
Для уменьшения трения используются твердые смазочные материалы: графит, порошок никеля и меди, дисульфид молибдена.
Прессовое оборудование
- Это гидравлические прессы с горизонтальным или вертикальным расположением пуансонов.
Пресс продукты
- Прессование дает вам простой профиль (круглый, квадратный) из сплава с низкой пластичностью и очень сложный профиль, который невозможен для других типов OMD (Рисунок 18).
Преимущества прессы
- Точность экструдированного профиля выше, чем у прокатки. Как уже упоминалось, вы можете получить наиболее сложную форму профиля. Этот процесс универсален с точки зрения перехода от размера к размеру и от одного типа профиля к другому. Смена инструмента занимает меньше времени.
Этот процесс очень продуктивен, потому что могут быть достигнуты очень продвинутые деформации. Скорость пресса достигает более 5 м / с. Продукт приобретается одним движением инструмента.
Недостатки прессы
Большие отходы металла (10-20%) в остатке пресса, потому что не весь металл может быть выдавлен из контейнера. Неравномерная деформация контейнера, высокая стоимость и высокий износ инструмента. Потребность в мощном оборудовании.
Нарисуйте профиль, потянув заготовку из постепенно сужающегося отверстия в инструменте.
Первый пробел на чертеже — это полоса, толстая линия или труба. Заготовка не нагревается. Другими словами, рисунок — это холодная пластическая деформация.
Заострите край заготовки, дайте волю пройти, захватите зажимным устройством и потяните.
- При вытягивании на заготовку действует растягивающее напряжение. Металл должен деформироваться только в узком канале матрицы. Деформация вне инструмента не допускается. Сжатие за один проход мало и экстрактор µ = 1,1 ÷ 1,5. Чтобы получить нужный профиль, протяните провод через несколько отверстий уменьшающегося диаметра.
Из-за холодной деформации металл залипает и затвердевает. Следовательно, отжиг (нагрев выше температуры рекристаллизации) выполняется в трубчатой печи при вытягивании через смежную головку. Твердость удаляется, и металл детали снова становится пластичным и может быть далее деформирован.
Этот инструмент представляет собой Etobolock или die, кольцо с профилированным отверстием. Плашки изготовлены из твердых сплавов, керамики и промышленных алмазов (для очень тонких проволок диаметром менее 0,2 мм). Трение между инструментом и заготовкой уменьшается с помощью твердой смазки. Оправка используется для получения полого профиля.
- В длине рабочего отверстия в матрице имеются четыре отдельные зоны (рис. 20). I-вход или смазка, II-деформация или механическая обработка, угол α = 8 ÷ 24º, III-калибровка, IV-выходной конус.
Средний допуск на размер проволоки составляет 0,02 мм.
Существуют чертежные фабрики различных конструкций, такие как барабаны, стойки, цепи и гидравлические приводы.
Барабанные мельницы (рис. 21) используются для извлечения проводов, стержней и труб малого диаметра, которые могут быть намотаны в ходе беспорядков.
Мельницы с несколькими волочильными барабанами могут содержать до 20 барабанов. Между ними — матрица и печь для отжига. Скорость проволоки
Сжатый продукт
Чертеж рисует проволоку диаметром от 0,002 до 5 мм и стержень, литьевой профиль (различные направляющие, ключи, шлицевые ролики) и трубы.
Преимущества нанесения
- Это высокая точность размеров (допуск менее 1/100 мм), небольшая шероховатость поверхности, возможность получения тонкого профиля, высокая производительность и небольшое количество отходов. Поскольку этот процесс универсален (инструменты можно легко и быстро менять), он широко распространен.
Также важно иметь возможность изменять свойства получаемого продукта путем отверждения и термообработки.
минус недостаток
- Неизбежное отверждение и необходимость отжига усложняют процесс. За один проход происходит небольшое сжатие.
ковочный
- Кузнечное производство называется получением изделия путем непрерывной деформации нагретой заготовки, ударяя ударником, универсальным инструментом. Полученная заготовка или готовое изделие называется ковкой.
Слиток или Блум, длинный продукт с простым разделом служит в качестве первого препарата. Заготовки обычно нагревают в камерной печи.
Ковка деформации
Деформация в процессе ковки происходит по схеме свободного пластического потока между поверхностями инструмента. Поскольку деформация может выполняться непрерывно на отдельных участках заготовки, ее размеры могут значительно превышать площадь бойка.
Величина деформации представлена чернением.
Здесь Fmax и Fmin — начальная и конечная площади поперечного сечения заготовки, и принимается соотношение большего и меньшего, поэтому ковка всегда больше 1. Чем выше значение ковки, тем лучше ковка металла. Некоторые из ковочных работ показаны.
Инструменты для ковки
Этот инструмент универсален (применим для поковок различной формы). Плоские или режущие фиксаторы и набор инструментов для станины (оправка, обжим, стежок и т. Д.).
Кузнечное оборудование
- Используется молоток или статическая машина, гидравлический пресс, динамическая или ударная машина.
Молот делится на давление воздуха с массой падающей части до 1 тонны и паровой воздух с массой падающей части до 8 тонн. Рабочая жидкость молотка — сжатый воздух или пар.
Гидравлические прессы с усилием до 100 МН предназначены для обработки самых тяжелых деталей. Они держат работу между нападающими в течение десятков секунд. Их рабочая жидкость жидкая (водная эмульсия, минеральное масло).
Ковка чаще всего используется при производстве отдельных и мелкосерийных изделий, особенно при тяжелой ковке. Из слитков весом до 300 тонн продукты можно получить только ковкой. Это вал гидрогенизатора, диск турбины, коленчатый вал судового двигателя и валок прокатного стана.
Преимущества ковки
- Это, прежде всего, универсальность процесса и широкий спектр продуктов. Ковка не требует сложных инструментов. Во время ковки металлическая структура улучшается. Волокна ковки правильно расположены, чтобы выдерживать нагрузку во время работы, а литая конструкция разрушается.
Недостатки ковки
- Это, конечно, означает, что производительность процесса низкая, а обработка требует значительного запаса. Кованые изделия получают с низкой точностью размеров и высокой шероховатостью поверхности.
Смотрите также:
Примеры решения задач по материаловедению
Монокристаллическое литье. | Пайка конструкционных сталей. |
Листовая штамповка. | Характерные особенности свариваемости стали. |