Оглавление:
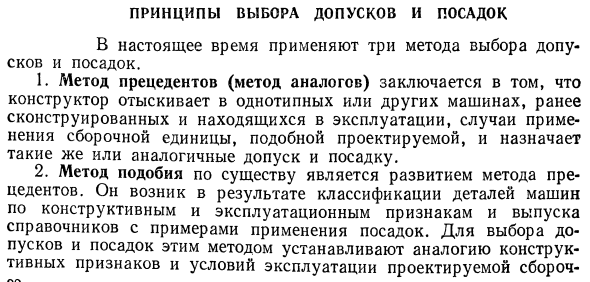
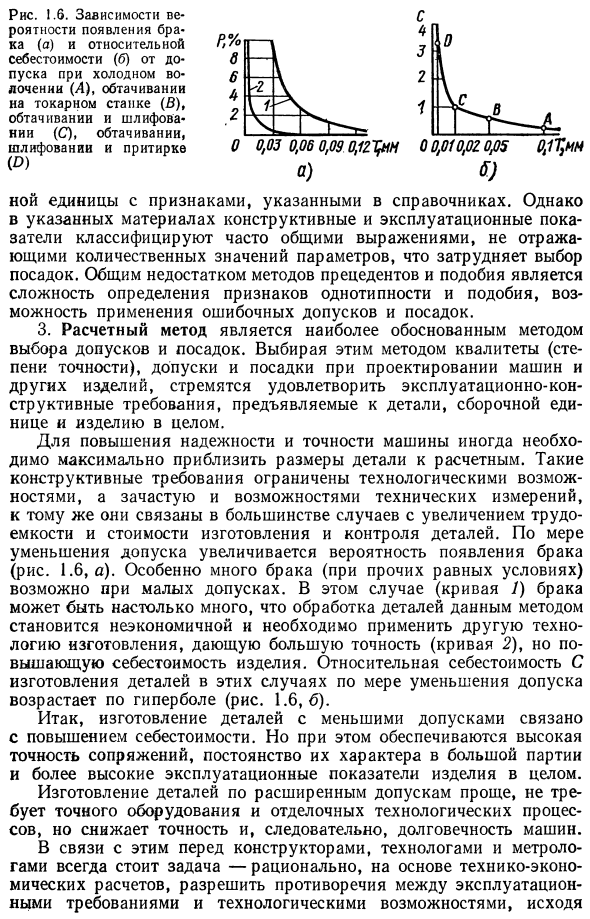
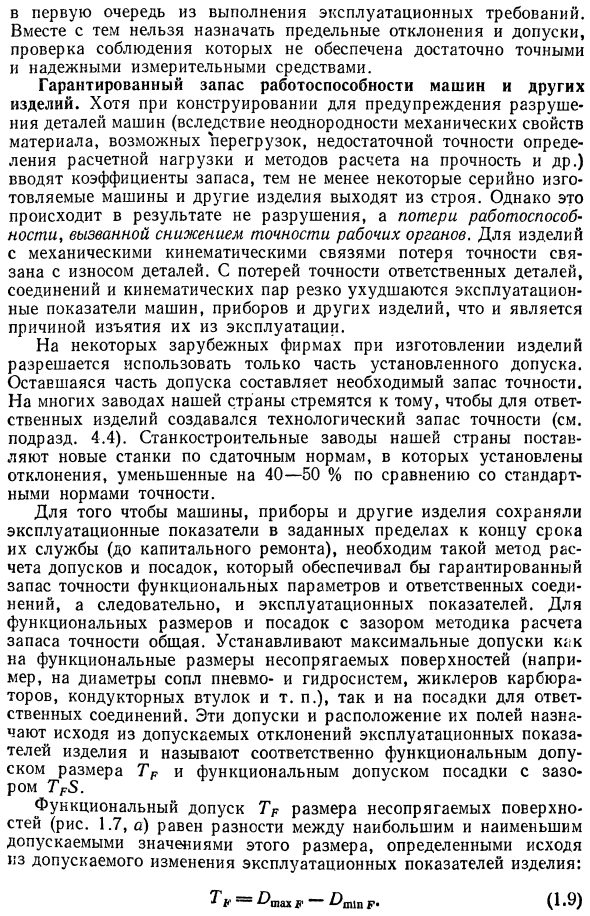
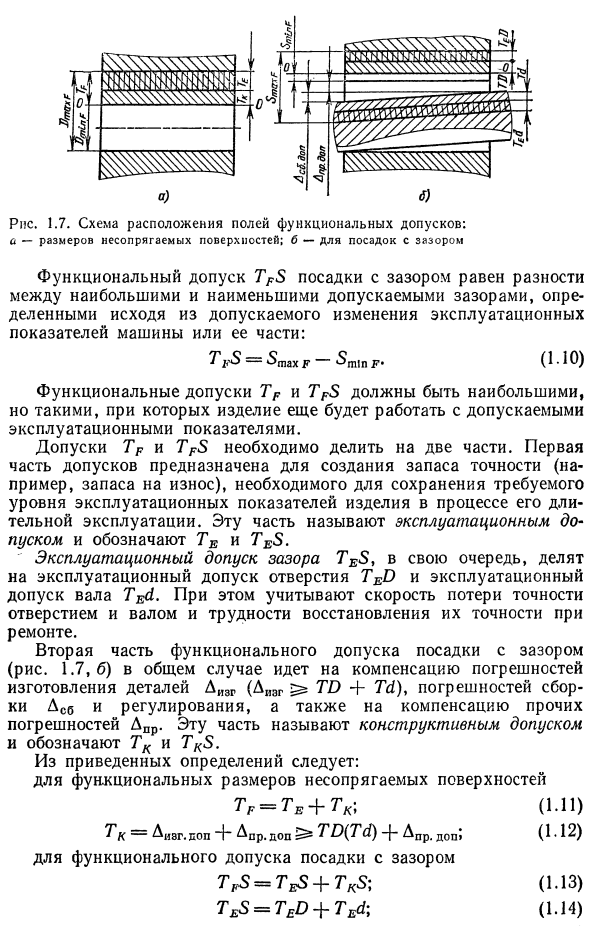
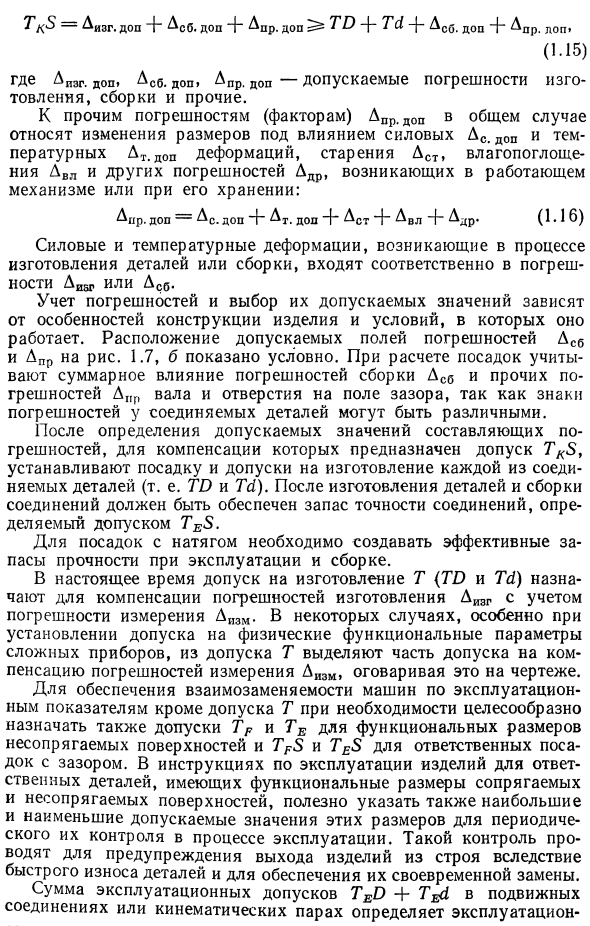
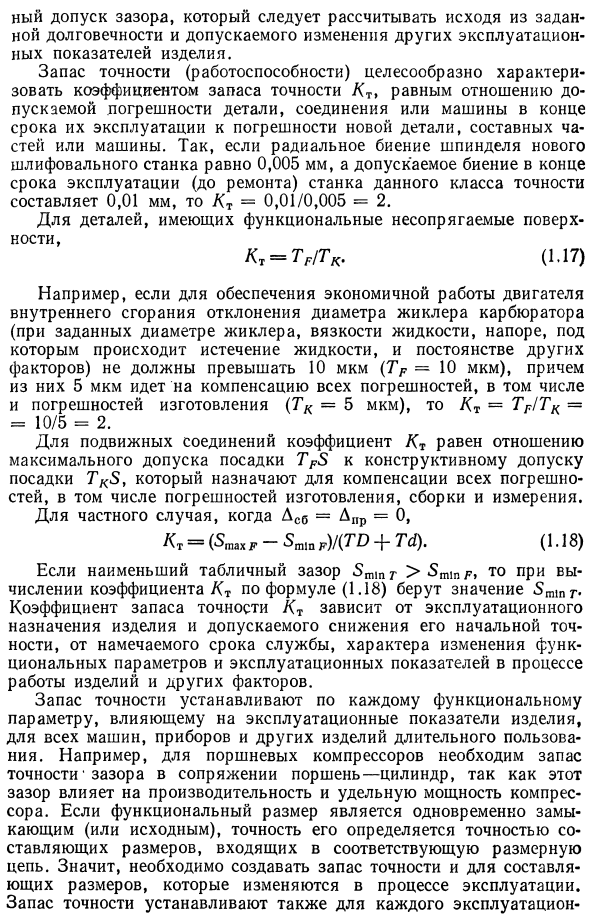
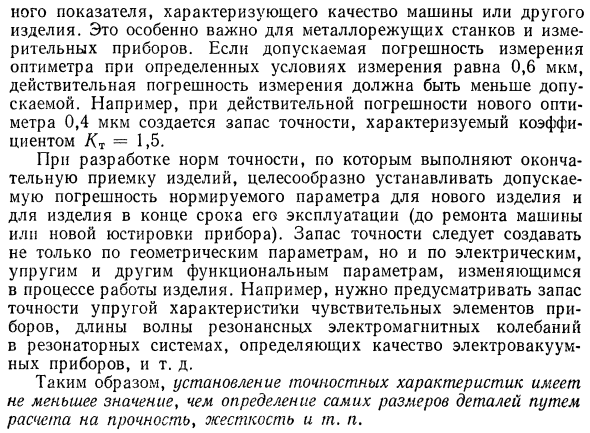

Принципы выбора допусков и посадок
- В настоящее время есть три способа выбора между терпимостью и посадкой. 1. Метод варианта использования (аналоговый метод) такой же или похожий, когда разработчик использует сборочную единицу, аналогичную той, которая была спроектирована на той же или другой машине, которая была спроектирована и эксплуатировалась так же или ранее Есть в факте назначения клиренс и посадка 2. Метод сходства — это, в основном, разработка метода варианта использования. Это стало результатом классификации механических частей по конструктивным и эксплуатационным характеристикам и публикации справочника, содержащего примеры посадки.
Чтобы выбрать допуски и посадку, этот метод устанавливает сходство проектной функции и условий эксплуатации проектируемой сборки. НИК. 1o Зависимость вероятности брака (o) и относительной стоимости (б) O 0,03 0,06 0,09 O, CT ^ IN 0 0,010,02 0,05 0,1T, MN Холодный запуск токарного станка (б), токарный и шлифовальный (С), токарный станок, шлифовка (O) обертка Единица с характеристиками, указанными в каталоге. Однако в этих материалах структурные и эксплуатационные показатели часто классифицируются по общим выражениям, которые не отражают количественные значения параметров, что затрудняет выбор посадок.
Качество продукции оценивают показателями качества продукции — количественными характеристиками основных свойств продукции. Людмила Фирмаль
Общие недостатки предыдущих методов и методов сходства заключаются в том, что трудно определить сходство и признаки сходства, а также возможность использования ложных допусков и посадок. 3. Метод расчета является наиболее разумным способом выбора допусков и посадки. Разрабатывая эту квалификацию (точность), допуск и метод посадки при проектировании машин и других изделий, мы стремимся удовлетворить эксплуатационные и конструктивные требования к деталям, сборочным единицам и целым изделиям.
Для повышения надежности и точности станка может потребоваться максимально увеличить размеры детали до расчетных размеров. Эти требования к дизайну ограничены техническими возможностями и часто связаны с повышенной сложностью производства и контролем затрат в большинстве случаев, в дополнение к техническим возможностям измерения. Чем меньше допуск, тем больше вероятность его дефекта (рис. 1.6, а). Возможны многие браки (автобус Cetellis Paris), особенно с небольшими допусками.
В этом случае (кривая 1) может быть так много дефектов, что обработка деталей этим методом становится неэкономичной, и необходимо применять другую технологию изготовления, которая повышает точность (кривая 2) ) Но стоимость товара возрастет. Относительная стоимость изготовления деталей в этих случаях увеличивается вдоль гиперболы по мере уменьшения допусков (рисунок 1.6.6). Поэтому производство деталей с низкими допусками связано с повышенными затратами.
Тем не менее, это обеспечивает высокоточное сопряжение, постоянство свойств в больших партиях и улучшение общих показателей производительности продукта. Легче изготавливать детали на основе расширенных допусков и не требует точного оборудования или технологических процессов отделки, но это снижает точность и, следовательно, долговечность станка. В связи с этим перед проектировщиками, инженерами и метрологами всегда стоит задача разрешения конфликтов между требованиями бизнеса и техническими возможностями на основе технико-экономических расчетов. В основном от выполнения эксплуатационных требований. В то же время, максимальное отклонение и допуск не могут быть назначены.
Проверка соответствия не обеспечивает достаточно точный и надежный метод измерения. Гарантирует работоспособность станков и другой продукции. При проектировании для предотвращения разрушения механических частей (из-за неоднородности механических свойств материала, возможности перегрузки, отсутствия точности определения расчетной нагрузки, метода расчета прочности и т. Д.) Вводится коэффициент безопасности. Однако некоторые коммерческие машины и другие продукты по-прежнему выходят из строя. Однако это происходит не в результате разрушения, а как потеря производительности, вызванная потерей точности заготовки. Для изделий с механическим движением потеря точности связана с износом деталей.
Потеря точности критических деталей, соединений и кинематических пар может значительно снизить производительность машин, устройств и других изделий. Вот почему он снят с эксплуатации. Некоторые иностранные компании допускают только некоторые допуски, используемые для производства продукта. Оставшийся допуск — это требуемый запас точности. Многие фабрики в Японии стремятся обеспечить запас технической точности для критически важных продуктов (см. Подраздел 4.4). Наш станкостроительный завод поставляет новые станки в соответствии с приемлемыми стандартами. В этом стандарте отклонение уменьшается на 40-50% по сравнению со стандартным стандартом точности.
Чтобы машины, устройства и другие изделия могли поддерживать эксплуатационные характеристики в указанных пределах к концу срока их службы (до капитального ремонта), требуется способ расчета допусков и посадок. Это гарантирует точность параметров функции и важных соединений. Показатель эффективности. Для соединений с функциональными размерами и зазорами процедура расчета запаса точности является обычной. Максимальные допуски устанавливаются как для функциональных размеров поверхности, не связанной с сопряжением (например, диаметры сопел для пневматических и гидравлических систем, сопел карбюраторов, проводящих втулок и т. Д.), Так и фитингов для критических соединений.
Эти допуски и их полевые положения назначаются на основе допусков индекса производительности продукта и называются функциональными допусками посадки с функциональным допуском размера TP и зазором TP8 соответственно. Функциональный допуск TP размера не сопрягаемой поверхности (рис. 1.7, а) равен разнице между максимальным и минимальным допустимыми значениями для этого размера и определяется на основе допустимого изменения эксплуатационных характеристик изделия. Г = Ош1, -Рш1пр.
Описание поля функционального допуска: Функциональный допуск приземления TP8 с зазором равен разнице между максимальным и минимально допустимым зазором, который определяется на основе допустимого изменения рабочих характеристик машины или ее частей. (1.10) Функциональные допуски TP и TP8 должны быть максимальными, но продукт работает с приемлемыми показателями производительности. Допуски TP и TP8 должны быть разделены на две части. Первая часть допуска предназначена для создания необходимого запаса точности (например, запаса износа) для поддержания требуемого уровня производительности продукта во время длительной эксплуатации.
Эта часть называется эксплуатационным допуском и называется TE и TE8. Далее, допуск срабатывания зазора TE8 делится на допуск срабатывания отверстия TEE и допуск срабатывания вала TrA. В то же время учитывается скорость, с которой теряется точность отверстия и вала, а также трудность восстановления точности во время ремонта. Вторая часть функционального допуска на посадку с зазорами в общем случае (рис. 1.7.6) — это погрешность изготовления детали (Dieg TO + TA), Дсв и ошибка нормативной сборки, а также Дпр. Используется для исправления других ошибок. Эта часть называется конструктивной терпимостью и называется Tk и Tk8.
- Из приведенного выше определения. Для функциональных размеров не сопряженных поверхностей TP = TE + TK-, (1.11) Tk = DIM..EOP + DOP.Pop TO (Ty) + Dpr. Добавлено; (1.12) Функциональная посадка с зазором Tp5 = Te8 + Tx8; (1,13) Te8 = TeO + TeA (1,14) TKZ = Диаз. ext + vir In + dpr doi затем + ta + de6. Ext + DPR провисания (1-15) Где Дизг Добавьте к этому. Ace. Добавьте к этому. Допп изготовление-сборка, сборка и другие допуски.
Другие ошибки (факторы) в общем случае Dpr.dop содержат изменение размера под влиянием мощности Ds. Дополнительная и температурная деформации Dt.dop, старение Dst, влагопоглощение Dvl и другие ошибки Ddr возникают при работе механизма или его хранении. DPR добавлено = Ds. ext + Dt.
Так как в большинстве случаев деления шкал устройств для измерения длин или углов бывают равномерными, то указывается не чувствительность, а только цена деления. Людмила Фирмаль
Силовые и температурные деформации, возникающие в процессе изготовления детали или сборки, включены в Ошибка 2 или Деб Описание ошибок и выбор их допусков зависит от возможностей дизайна продукта и условий, в которых он работает. Поля допусков Дс6 и Дпр на рисунке, местоположения 1.7 и b отображаются условно. При расчете посадок учитывается совокупное влияние ошибок сборки ДСП и других ошибок вала и отверстий на поле зазора, поскольку признаки ошибок подключенных деталей могут быть разными.
Для компенсации, для которой предназначены допуски Tk8, после определения допусков на погрешности компонентов устанавливаются производственные соответствия и допуски для каждой соединенной детали (TO и Ta). После изготовления детали и сборки соединения необходимо обеспечить запас точности для соединения, который определяется допуском Te8. Чтобы обеспечить надежную посадку, необходимо создать эффективный запас прочности при эксплуатации и сборке. В настоящее время производственные допуски T (TO и Ta) назначаются для компенсации производственных ошибок Dizg с учетом ошибок измерения DIZm, в некоторых случаях, особенно для параметров физических функций сложных устройств.
При установлении допусков часть допусков для исправления погрешности измерения Dazm присваивается из допуска T, который указан на чертеже. Для обеспечения совместимости машины с точки зрения производительности, помимо допусков T, присвойте допуски TR и TB функциональным размерам нематируемых поверхностей, а также TP8 и TE8 для критических соединений с зазорами. Рекомендуется назначить Инструкции по эксплуатации продукта для критических деталей с функциональными размерами сопрягаемой и нематериальной поверхности также могут указывать максимальные и минимальные допустимые значения этих размеров для регулярного контроля во время работы. Это помогает.
Такой контроль выполняется для предотвращения выхода изделия из строя из-за быстрого износа деталей и для обеспечения своевременной замены. Сумма допусков движения TEO + T и 1 подвижного соединения или кинематической пары определяет движение Минимальный допуск на просвет рассчитывается на основе указанной долговечности и других допусков производительности продукта. Рекомендуется охарактеризовать запас точности (работоспособность) с коэффициентом точности Kt, равным отношению допусков по истечении срока службы детали, соединения или станка к ошибкам новой детали, компонента или станка.
Поэтому, если новый шлифовальный станок имеет радиальное биение 0,005 мм и допустимое биение этого класса точности станка (до ремонта) составляет 0,01 мм, то Kt = 0,01 0,005 = 2. Для деталей с функциональными не сопряженными поверхностями, Kt = TP Tk. (1,17) Например, чтобы обеспечить экономичную работу двигателя внутреннего сгорания, отклонение диаметра сопла карбюратора (удельный диаметр сопла, вязкость жидкости, давление потока жидкости и другие факторы инвариантности) не должно превышать 10 мкм1ТП = 10 мкм. Если нет, 5 мкм исправляет все ошибки, включая производственную ошибку (Tk-5 мкм), и Kt-TP1TK = 10 5 = 2.
Для подвижных соединений коэффициент Kt равен отношению максимального допуска на посадку TP8 и конструктивного допуска на посадку Tk8 и предназначен для исправления всех ошибок, включая ошибки изготовления, сборки и измерения. Дс6 = Дпр = 0 особый случай Km = (5gamR-5t1oK) (TO + TH).
Когда минимальный зазор в таблице составляет 5m nr 5m nR, при расчете коэффициента Km с помощью уравнения (1.18) значение m запасного коэффициента Kt предназначено для уменьшения цели эксплуатации и начальной точности изделия. Зависит от срока службы изделия, характера изменений функциональных параметров и эксплуатационных показателей при эксплуатации изделия и других факторов. Предел точности устанавливается для каждого функционального параметра, который влияет на эксплуатационные характеристики продукта для всех машин, устройств и других долговечных продуктов. Например, поршневой компрессор имеет интерфейс поршень цилиндр. Запас точности 1 для очистки лица требуется.
Этот зазор влияет на производительность и удельную мощность компрессора. Если размер элемента является закрытым (или начальным) в то же время, его точность определяется точностью составляющих размеров в соответствующей размерной цепочке. Это означает, что вам нужно создать запас точности для размера компонента, который изменяется во время работы. Запас точности также устанавливается для каждой операции: Ny показатель, характеризующий качество техники или другой продукции. Это особенно важно для станков и измерительной техники. Если погрешность измерения допуска Оптимометра при определенных условиях измерения составляет 0,6 мкм, фактическая погрешность измерения должна быть меньше допуска.
Например, если фактическая погрешность нового оптиметра составляет 0,4 мкм, создается запас точности, характеризуемый коэффициентом Kt = 1,5. При разработке стандартов точности для окончательного утверждения продуктов важно установить нормированные допуски параметров в конце срока службы новых продуктов и продуктов (перед ремонтом машины или настройкой нового устройства). мы рекомендуем. Пределы точности должны создаваться не только геометрическими параметрами, но также электрическими, упругими и другими функциональными параметрами, которые изменяются во время работы изделия.
Например, необходимо обеспечить запас точности, такой как упругие свойства чувствительных элементов устройства и длина волны резонансной электромагнитной волны резонаторной системы, которая определяет качество электрического вакуумного устройства. Поэтому определение точностных характеристик так же важно, как и определение размеров самой детали путем расчета прочности, жесткости и т.
Смотрите также:
Принцип выбора типов и параметров рычажных передач | Показатели уровня стандартизации и унификации изделий |
Приборы с индуктивными преобразователями | Единая система стандартов приборостроения (ЕССП) |