

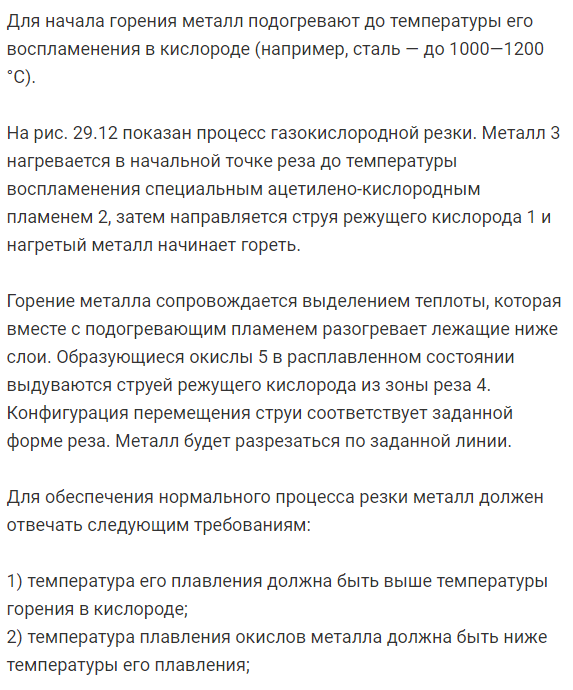
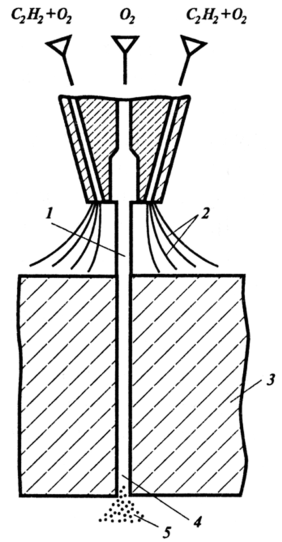
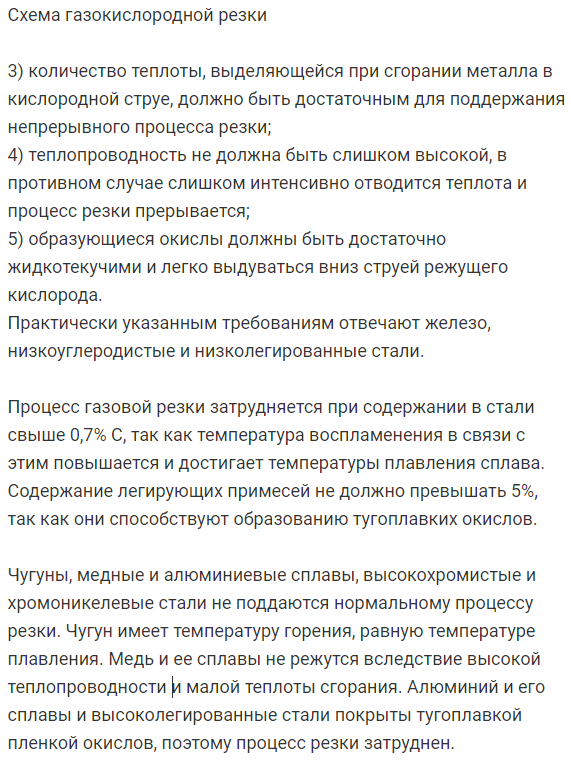
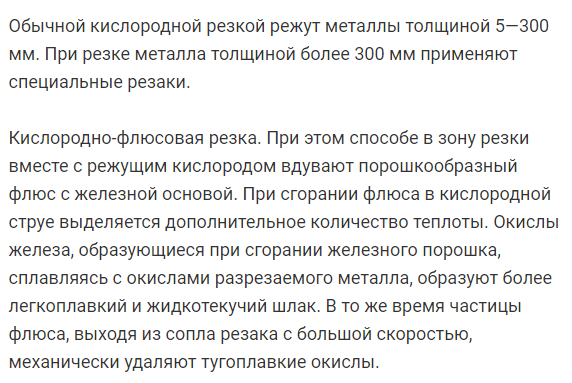
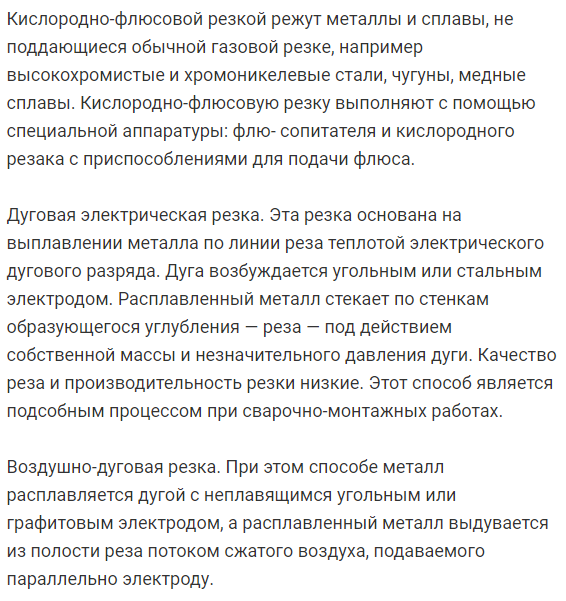
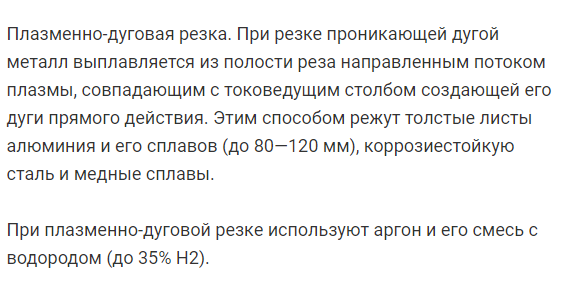
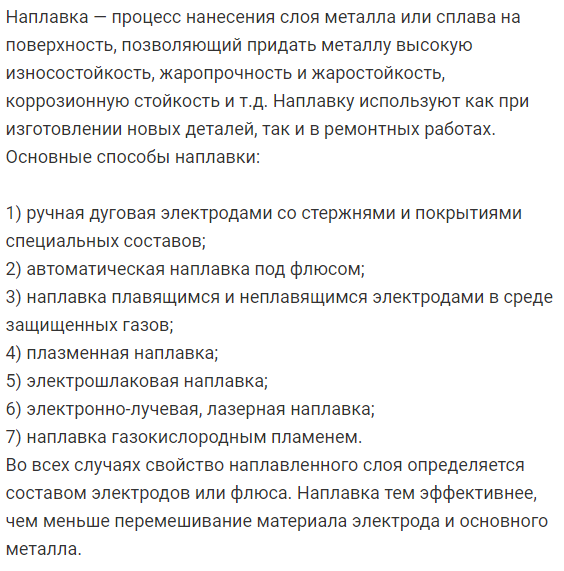
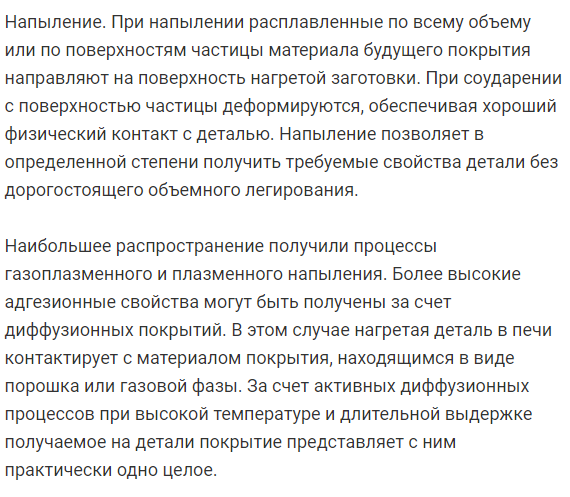
Резка металла. Во время процесса резки металл из режущей полости может быть удален термическим (плавление и протекание вдоль линии резки) и химическим (окисленный, оксид и шлак, которые также удаляются из режущей полости) способом. , Оба эти процесса могут происходить одновременно.
Термические и химические воздействия могут сочетаться с механическим воздействием газовых или порошковых струй, чтобы способствовать удалению жидких или размягченных продуктов из режущей полости.
Существует несколько методов резки, но наиболее распространенным в отрасли является резка кислородным топливом.
Кислородная резка. Этот метод включает термохимическую резку и состоит из сжигания металла с технически чистым потоком кислорода и удаления оксидов, образованных этим потоком. Когда железо горит кислородом, реакция выделяет значительное количество тепла
Чтобы начать горение, нагрейте металл в кислороде до температуры воспламенения (например, сталь от -1000 до 1200 ° С).
На рисунке показан процесс резки кислородного топлива. Металл 3 нагревается до температуры воспламенения с помощью специального ацетилен-кислородного пламени 2 в начале резки, направляется струя резки кислорода 1, и нагретый металл начинает гореть.
Сгорание металла включает выделение тепла, которое нагревает нижележащий слой с помощью нагревающего пламени. Полученный в результате расплавленный оксид 5 выдувается из области 4 резки потоком кислорода для резки. Конфигурация струйного движения соответствует заданной форме среза. Металл режется по заданной линии.
Чтобы обеспечить нормальный процесс резки, металл должен соответствовать следующим требованиям:
- 1) Температура его плавления должна быть выше, чем температура сгорания в кислороде.
- 2) Температура плавления оксида металла должна быть ниже.
Схема резки кислородного топлива
- 3) Количество тепла, выделяемое при сжигании металла в потоке кислорода, должно быть достаточным для поддержания непрерывного процесса резки.
- 4) Теплопроводность не должна быть слишком высокой. В противном случае тепло отводится чрезмерно, и процесс резки прерывается.
- 5) Образующийся оксид является достаточно текучим, и его необходимо легко сдувать потоком режущего кислорода.
- Большинству указанных требований отвечают железо, низкоуглеродистая и низколегированная сталь.
Температура воспламенения этого соединения увеличивается и достигает точки плавления сплава, поэтому, если содержание стали превышает 0,7% С, процесс газовой резки затрудняется. Содержание легирующих примесей должно способствовать образованию тугоплавких оксидов и не должно превышать 5%.
Чугунные, медные и алюминиевые сплавы, высокохромистые и хромоникелевые стали бесполезны для обычного процесса резки. Температура сгорания чугуна совпадает с температурой плавления. Медь и ее сплавы не режутся из-за высокой теплопроводности и низкой теплоты сгорания. Алюминий, его сплавы и высоколегированные стали покрыты тугоплавкой оксидной пленкой, что затрудняет процесс резки.
При обычной кислородной резке резался металл толщиной от 5 до 300 мм. Специальный резак используется при резке металла толщиной более 300 мм.
Резка кислородным потоком. В этом методе порошковый флюс на основе железа режет кислород и выдувается в зону резания. Когда поток горит потоком кислорода, генерируется дополнительное тепло. Оксид железа, образующийся при сжигании железного порошка, легируется оксидом металла, который должен быть разрезан, с образованием жидкого шлака с более высокой температурой плавления.
В то же время частицы флюса, выходящие из сопла горелки с высокой скоростью, механически удаляют тугоплавкий оксид.
Металлы и сплавы, которые не подходят для обычной газовой резки, такие как высокохромистая и никель-хромовая сталь, чугун и медные сплавы, режутся методом кислородной резки. Резка кислородным потоком осуществляется с помощью флюсового питателя с флюсовым питателем и специального устройства кислородного резака с флюсовым питателем.
Дуговая электрическая резка. Эта резка основана на выплавке металла вдоль линии резания из-за высокой температуры дугового разряда. Дуга возбуждается углеродным или стальным электродом. Расплавленный металл стекает по стенкам образовавшегося углубления под воздействием собственной массы и небольшого давления дуги. Качество резки и производительность резки низкие. Этот метод является вспомогательным процессом при сварочных и монтажных работах.
- Воздушно-дуговая резка. В этом способе металл плавится по дуге с нерасходуемым угольным или графитовым электродом, а расплавленный металл выдувается из режущей полости потоком сжатого воздуха, подаваемого параллельно электроду.
Плазменная дуговая резка. При резке сквозной дугой металл выплавляется из режущей полости под действием индуктивного потока плазмы и создает его на одной линии с токопроводящей дуговой колонной. Этот метод режет толстые листы алюминия и его сплавов (до 80-120 мм), коррозионно-стойкой стали и медных сплавов.
В плазменной резке используется смесь аргона и водорода (до 35% H2).
Отделка поверхности — процесс нанесения слоя металла или сплава на поверхность. Это дает металлу высокую износостойкость, термостойкость, термостойкость и коррозионную стойкость. Поверхностные покрытия используются как в производстве новых деталей, так и в ремонтных работах. Основные методы отделки поверхности:
- 1) Ручной дуговой электрод со специальным составом стержня и покрытием.
- 2) Автоматическая левитация под флюсом;
- 3) Плавать с расходуемыми и не расходуемыми электродами в среде защитного газа.
- 4) плазменная поверхность;
- 5) электрошлаковая левитация;
- 6) электронный луч, лазерная левитация;
- 7) Поднимитесь с кислородным пламенем.
Во всех случаях характеристики нанесенного слоя зависят от состава электрода или флюса. Обработка поверхности более эффективна при меньшем смешении материала электрода и основного материала.
Спрей. Во время распыления частицы будущего материала покрытия, которые расплавились по всему объему или поверхности, направляются на поверхность нагреваемой заготовки. При ударе о поверхность частицы деформируются и обеспечивают хороший физический контакт с деталью. Термический спрей может обеспечить необходимые свойства деталей без какого-либо дорогостоящего массового легирования.
- Наиболее широко используемые процессы — газоплазменное и плазменное напыление. Диффузионное покрытие обеспечивает более высокие адгезионные свойства. В этом случае нагретая часть в печи контактирует с материалом покрытия в виде порошковой или газовой фазы. Благодаря активному диффузионному процессу при высоких температурах и длительной выдержке, полученное покрытие на детали фактически интегрируется с ним.
Смотрите также:
Примеры решения задач по материаловедению
Производство бесшовных и сварных труб. | Физико-химические основы процесса резания. |
Ликвация и газы в литейных сплавах. | Механические основы процесса резания. |