Оглавление:
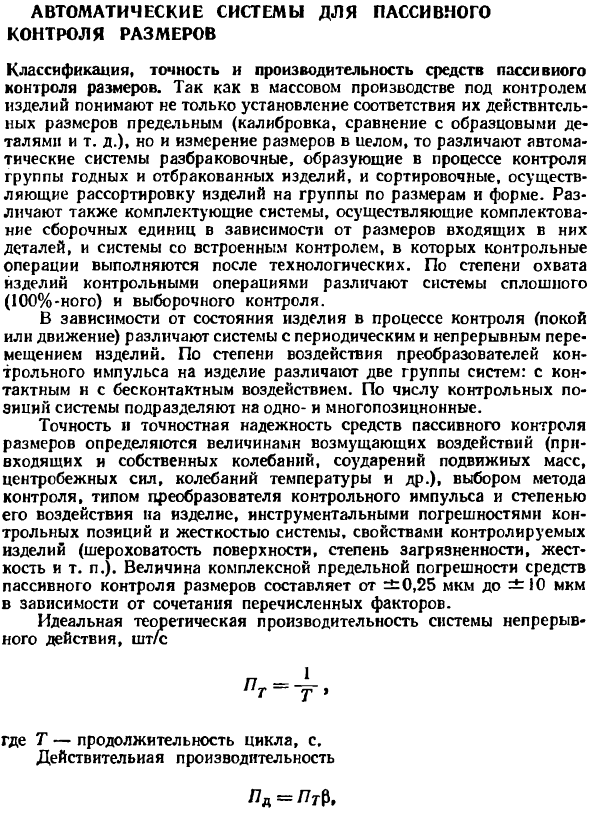
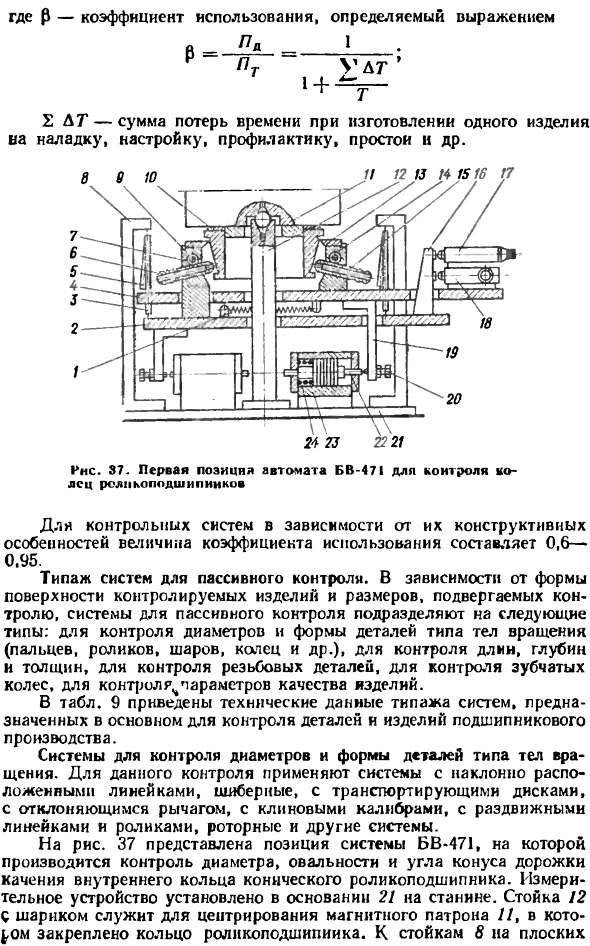
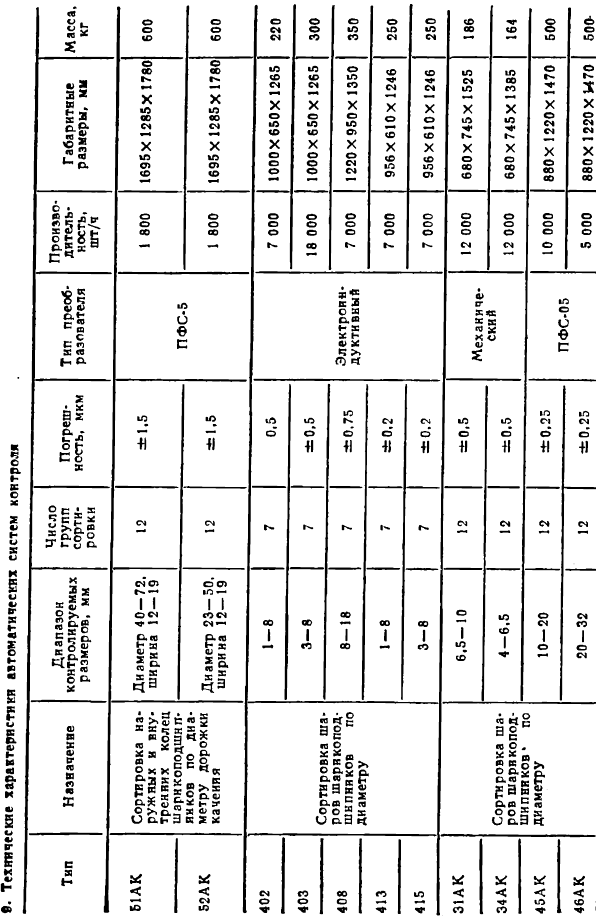
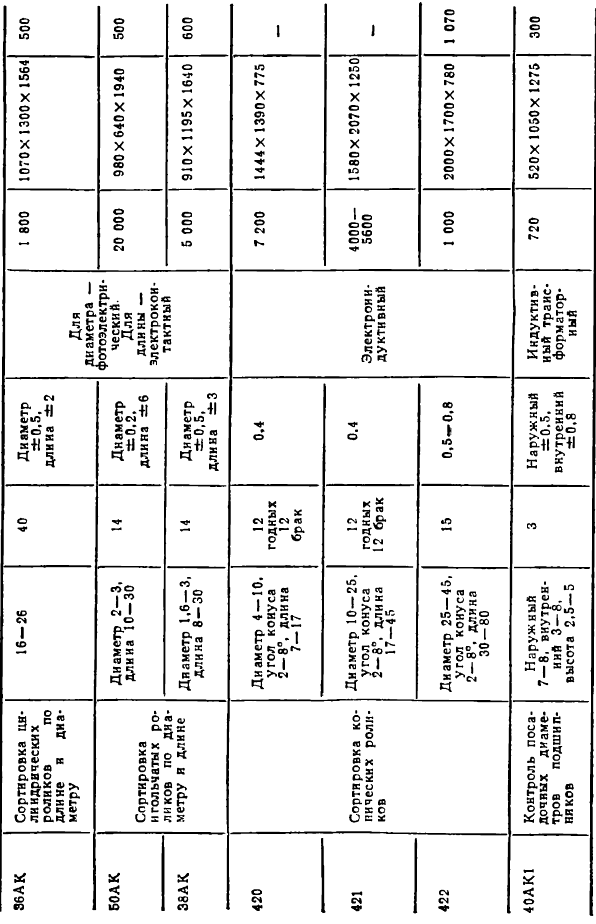
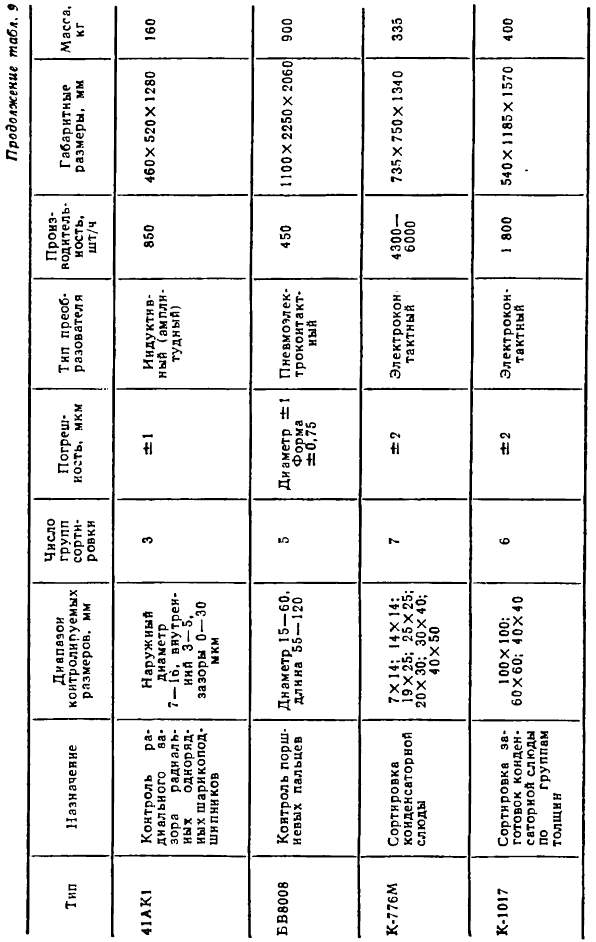
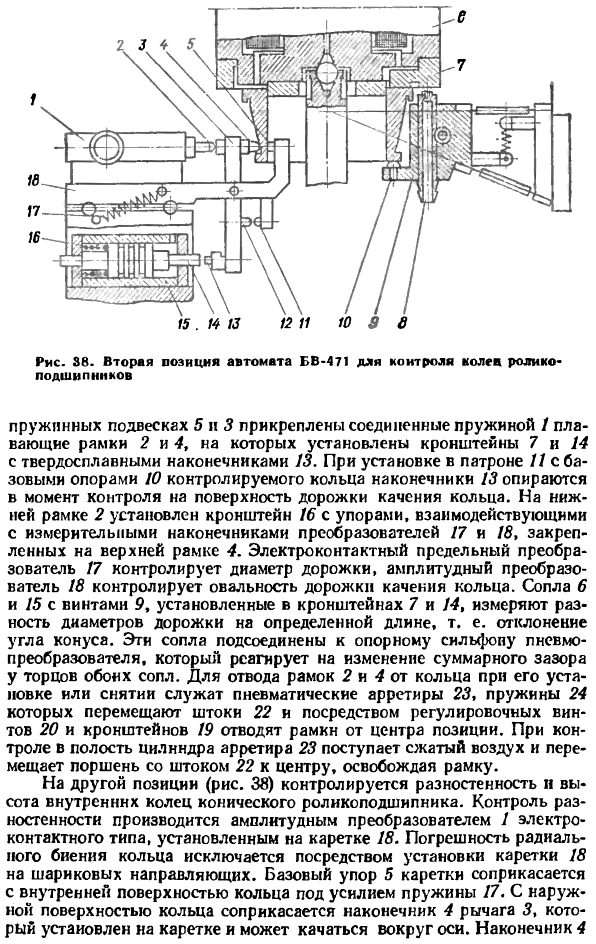
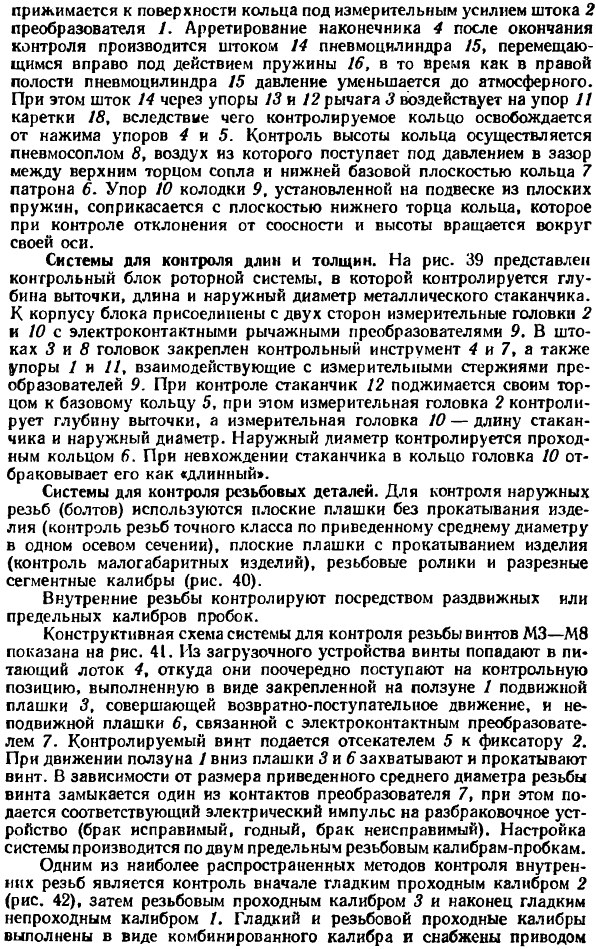
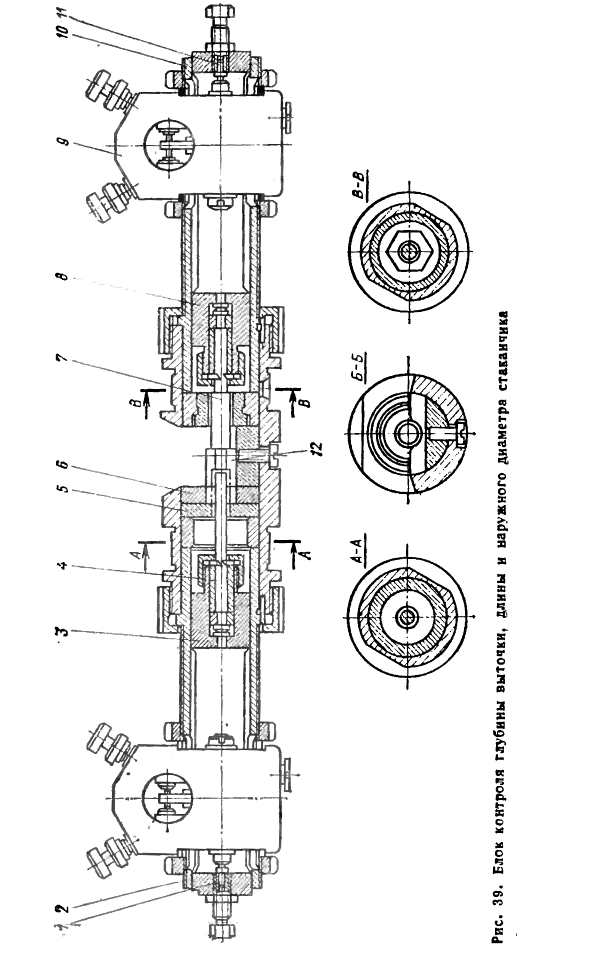
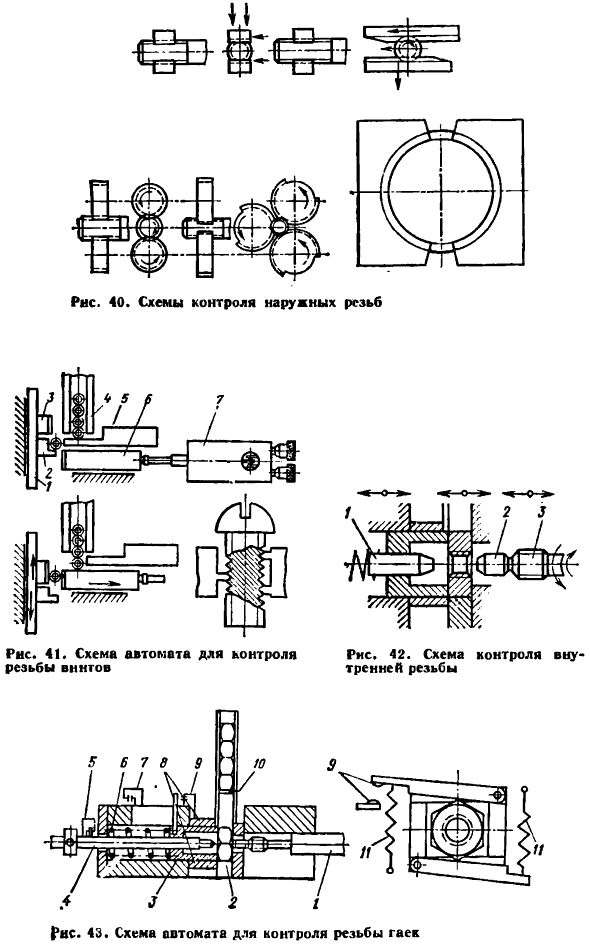
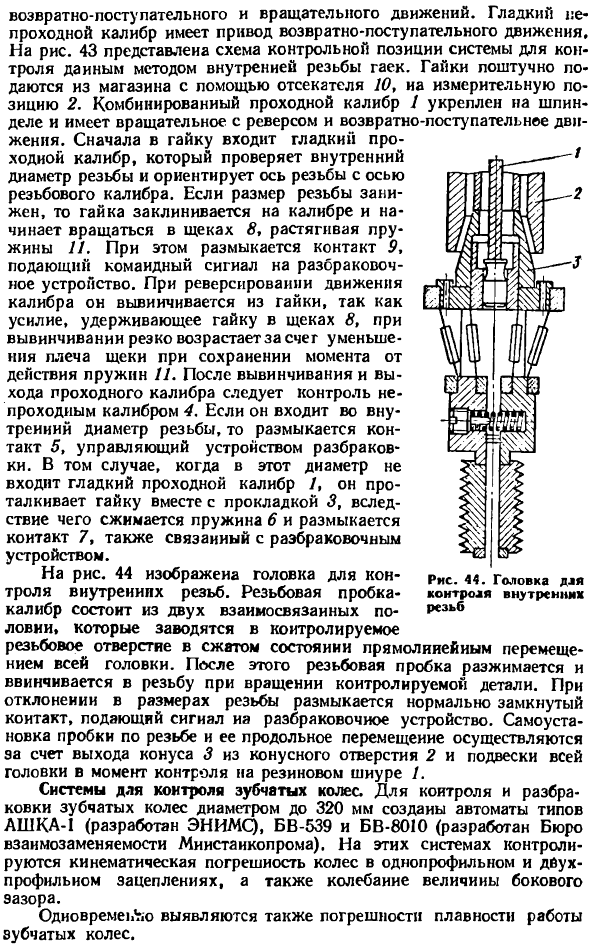
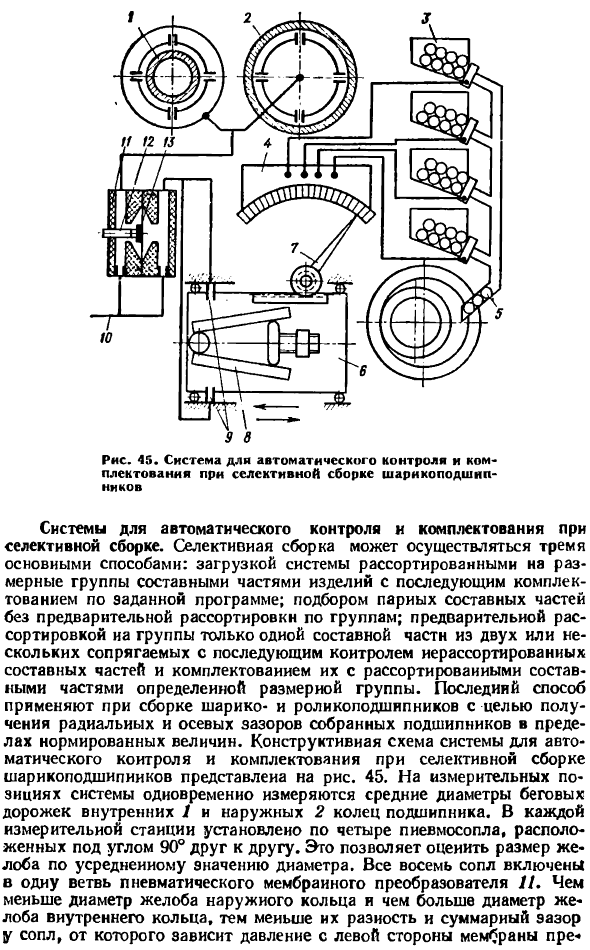
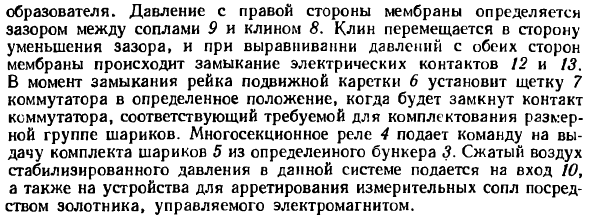

Автоматические системы для пассивного контроля размеров
- Классификация, точность и эффективность пассивного размерного контроля. В массовом производстве под контролем продукта скребок не только знает, что фактический размер соответствует ограничениям (калибровка, сравнение с деталями модели и т. Д.), Но также измеряет габаритные размеры. Автоматические системы различаются и образуют соответствующие группы в процессе контроля, отбраковывают продукты и классифицируют продукты по группам в соответствии с их размером и формой.
Другие системы имеют отличительные компоненты, которые дополняют сборочную единицу в зависимости от размера участвующих частей, и встроенные элементы управления, где операции управления выполняются после технических. Степень охвата продукта контрольной операцией различает системы непрерывного (100%) и избирательного контроля. В зависимости от состояния продукта (стационарного или движущегося) в процессе управления различают системы с периодическим и непрерывным перемещением продукта. Различают две группы систем в зависимости от степени влияния преобразователя импульсов управления на изделие.
Часто термины формируются из слов, которые имеют много значений в общем языке, давая значение термина. Людмила Фирмаль
Контактная работа и бесконтактная работа. В зависимости от количества позиций управления, система может быть разделена на одну позицию и несколько позиций. Точность и точность мер пассивного контроля размера зависит от значений влияния возмущения (входящие и естественные колебания, столкновения движущейся массы, центробежные силы, колебания температуры и т. Д.), Выбора метода управления, типов преобразователя импульсного управления и изделий.
Степень влияния зависит от погрешности контрольного оборудования, положения и жесткости системы, контролируемых свойств продукта (шероховатость поверхности, степень загрязнения, жесткость и т. Д.). Значения комплексной предельной погрешности для мер пассивного контроля размера составляют ± 0, от 25 до -10 мкм, в зависимости от комбинации вышеуказанных факторов. Идеальная теоретическая производительность непрерывной системы, шт с P1 1 T Где T период s цикла. Фактическая производительность р Где 0 — коэффициент использования, определяемый по формуле.
Лд 1 Ким УДТ 1+ т 2 AT-количество времени, потраченного на изготовление одного изделия для ввода в эксплуатацию, настройки, обслуживания, простоя и т. Д. Для систем управления значения использования варьируются от 0,6 до 0,95, в зависимости от проектной функции. Тип системы для пассивного контроля. В зависимости от формы поверхности контролируемого продукта и размера контролируемого продукта, пассивные системы управления подразделяются на следующие типы: для контроля диаметра и формы таких частей, как вращающиеся тела (пальцы, ролики, шарики, кольца и т. д.
Контроль длины, глубины, толщины, контроль резьбовых деталей, контроль зубчатой передачи, контроль параметров качества продукции. В таблице. На рисунке 9 показаны технические данные типа системы, в основном предназначенной для контроля деталей и изделий в производстве подшипников. Система, которая контролирует диаметр и форму деталей, таких как вращающиеся тела. Для этого управления используются такие системы, как наклонная линейка, задвижка, передаточный диск, отклоняющий рычаг, клиновой датчик, скользящая линейка и ролик, а также поворотный.
На фиг. 37 показано положение системы BV-471, где управляют диаметром, эллиптичностью и углом конуса дорожки качения внутреннего кольца конического роликового подшипника. Измерительное устройство установлено на основании 21 на кровати. Шарики подставки 120 служат для центрирования магнитного картриджа 11, на котором закреплено кольцо роликового подшипника. Квартира на стойке 8 Технические характеристики автоматической системы ко Так называемый резервный диапазон контролируемой р свки B1AK 52AK Наружное кольцо и внутренний диаметр кольца выбора 40-72.
Ширина 12-19 12. 86 A K Сортировка цилиндрических роликов по длине и диаметру 16-26 40 Диаметр иглы БОЛК, диаметр сортировки 2-3. Длина 10-30 14 1.6-3 диаметр, длина от 8-30 14 до 38 м и длина Сортировка 420 корор, диаметр 4-10. Угол конуса 2 ~ 8 °. Длина 7-17 12 12 Брак 421 диаметр 10-25. 2-8 °. Длина 17-45 12 подходит 12 брака 422 диаметр 25-45. Угол конуса 2-8 °. Длина 30-80 15 40АК1 контрольная позиция-наружная 7-8. Внутренняя 3-8.
Высота 2,5—5 3 ± 0,5 в диаметре. Для диаметра -1800 1070X 1300X 1564 500 Длина диаметра ± 6 шахмат. 20000 980X640X 1940 500 для электро хода ± 0,5 в диаметре. Длина ± 3 5000 910X 1195X1640 600 0,4 дедуктивный 7,200 1444X 1390X775- 0,4 4000—5600 1580X2070X1250- 0,5—0,8 1 000 2000X 1700X780 1 070 Снаружи ± 0,5.
Индуктивный индукционный трансформатор Контролируемый диапазон резервирования типа PEuggP Управление наружными 7 ~ 16 радиальными шарикоподшипниками с одним каналом типа ААА 41АК1. Внутренний 3-5, разрыв 0-30 3 -1 BV8008 поршневой палец управления диаметром 15-60. Длина 55-120 5 Диаметр ± 1 ±: ( .75 Сортировка конденсатора K-776M слюда 7X14: 14X14: 19X25; 25X25; 20X30; 30X40; 40X50 7 ± 1 Классификация заготовок конвейера по группе K-1017 100X 100: 60X60; 40X40 6 ± 2 Продолжение таблицы. Тип драйвера-конвертер.
Габаритные размеры, мм вес, Iductive-hard) 850 460X520X1280 160 Пневмозлек-trocoitact-450 1100X2250X2060 900 Электронный 4300—6000 735 X 750X 1340 335 Электрические контакты 1800 540X 1185X 1570 400 Пружинные подвески 5 и 3 имеют пружинные соединения плавающие рамы 2 и 4, а кронштейны 7 и 14 имеют твердосплавные наконечники 13. При установке на картридж 11 с опорой 10 основания контролируемого кольца наконечник 13 опирается на поверхность дорожки качения кольца в момент управления.
Нижняя рама 2 имеет кронштейн 16 с упорами, который взаимодействует с измерительными наконечниками преобразователей 17 и 18, установленных на верхней раме 4. Датчик 17 ограничения электрических контактов управляет диаметром дорожки, а датчик 18 амплитуды управляет эллиптической формой траектории кольца. Сопла 6 и 15 с винтами 9, установленными на кронштейнах 7 и 14, измеряют разницу в диаметре гусеницы по определенной длине, то есть отклонение угла конуса.
Эти сопла соединены с эталонным сильфоном пневматического преобразователя, который реагирует на изменения общего зазора на концах обоих сопел. Чтобы снять рамы 2 и 4 с кольца, используйте пневматический разрядник 23 при установке или снятии кольца. Пружина 24 перемещает шток 22 и использует регулировочный винт 20 и кронштейн 19 для перемещения рамы от центра положения. Во время управления сжатый воздух поступает в полость цилиндра разрядника 23 и движется вокруг поршня со штоком 22, чтобы освободить раму. В другом положении.
Регулируется разница и высота внутреннего кольца конического роликового подшипника. Управление разницей осуществляется с помощью амплитудного преобразователя 1 электрического контакта, прикрепленного к каретке 18. Ошибки радиального биения в кольце устраняются путем прикрепления каретки 18 к шариковой направляющей. Упор 5 основания каретки находится в контакте с внутренней поверхностью кольца силой пружины 17. Наконечник 4 рычага 3, прикрепленный к рычагу, прикреплен к каретке, может качаться вокруг оси и находится в контакте с внешней поверхностью кольца.
- Преобразователь шток 2 прижимается к поверхности кольца измерительной силой. Блокировка наконечника 4 после окончания управления осуществляется штоком 14 пневматического цилиндра 15 и перемещается вправо под действием пружины 16, а в правой полости пневматического цилиндра 15 давление падает до атмосферного давления. В этом случае шток 14, проходящий через упоры 13 и 12 рычага 3, воздействует на упор 11 каретки 18, так что кольцо управления освобождается от толкания упоров 4 и 5.
Высота кольца контролируется пневматическим соплом 8, от пневматического сопла 8 до верха сопла и нижнего дна кольца 7 картриджа 6. Упор 10 блока 9, установленный на плоской пружинной подвеске, контактирует с плоскостью на нижнем конце кольца. Плоскость в нижней части кольца вращается вокруг своей оси при управлении выравниванием и отклонением от высоты. Система, которая контролирует длину и толщину. На фиг.39 показан блок управления роторной системы, в котором регулируется глубина канавки, длина и внешний диаметр металлического стакана.
В качестве примера можно привести точное определение момента времени, основанное на астрономических наблюдениях и измерениях. Людмила Фирмаль
Две измерительные головки 2-10 соединены с корпусом блока с обеих сторон электрическими контактными датчиками 9. Средства управления 4 и 7 закреплены на стержнях 3 и 8 головки. Также зафиксированы упоры 1 и 11, которые взаимодействуют с измерительным стержнем преобразователя 9. Нажмите на чашку 12 во время теста. Измерительная головка 2 контролирует глубину канавки, а измерительная головка 10 контролирует длину чашки и наружный диаметр. Наружный диаметр контролируется проходным кольцом 6. Если чашка не помещается в кольцо, головка 10 отклонит его как длинный .
Система управления винтовыми компонентами. Для контроля внешней резьбы (болта) используйте плоскую головку без раскатывания продукта (точный класс винтового управления в соответствии со средним диаметром, указанным в одной секции вала), Управление), используя резьбовые ролики и датчики с разрезными сегментами (Рисунок 40). Внутренняя резьба контролируется скользящей или ограничительной пробкой. На рисунке 1 показана структура системы управления резьбой винтов M3-M8. 41.
Винты входят в подающий лоток 4 из загрузочного лотка и оттуда поочередно в положение управления в виде возвратно-поступательной подвижной пластины 3, прикрепленной к ползунку 1, и неподвижной пластины 6, соединенной с датчиком 7 электрических контактов. он достигнет. Когда ползунок 5 перемещается вниз, матрицы 3 и 6 захватывают винт и вращаются. В зависимости от размера уменьшенного среднего диаметра резьбы один из контактов преобразователя 7 замыкается, и на устройство разборки подается соответствующий электрический импульс (плохо, хорошо, плохо).
Система настроена в соответствии с двумя концевыми резьбовыми манометрами. Одним из наиболее распространенных способов контроля внутренней резьбы является проверка сначала с помощью калибра 2 с гладким отверстием (рис. 42), затем с помощью калибра 3 с резьбой и, наконец, с помощью калибра 1 с гладким отверстием. Гладкий резьбовой калибр выполнен в форме комбинированного калибра и оснащен приводом Рисунок 39. Блок управления глубиной канавки, длиной чашки и наружным диаметром Рисунок 40. Схема управления внешним потоком Для контроля Рисунок 42: Схема управления резьбой B1 Рисунок 41.
Схема машины Рисунок 44. Головка для контроля внутренней резьбы Возвратно-вращательное движение. Гладкий датчик Пепа имеет возвратно-поступательный привод. На фиг.43 показан вид положения управления системой для управления внутренним винтом гайки этим способом. Гайки подаются по одному из магазина в положение измерения 2 с помощью резака 10. Составной проходной датчик 1 установлен на шпинделе и выполняет вращательное движение в обратном и возвратно-поступательном движениях.
Сначала в гайку входит калибр с гладким отверстием, который проверяет внутренний диаметр резьбы и направляет ось резьбы к оси резьбы. Если размер винта занижен, гайка заклинивает в манометре и начинает вращаться на щеке 8, чтобы растянуть пружину 11. В это же время контакт 9 размыкается, давая сигнал команды неисправному устройству. Чтобы изменить направление движения калибра, выверните винт из гайки. Это связано с внезапным увеличением силы, удерживающей гайку на щеке 8 при отвинчивании из-за уменьшенного плеча щеки, при сохранении момента от действия пружины 11.
Разомкните контакт 5, который управляет отклоняющим устройством, после того, как он окажется внутри внутреннего диаметра резьбы. Если калибр 1 с гладким отверстием не соответствует этому диаметру, он толкает гайку вместе с прокладкой 3, так что пружина 6 сжимается и размыкается контакт 7, который также соединен с устройством для разборки. Рисунок 44 контролирует внутреннюю резьбу Показывает голову для просмотра.
Резьбовой манометр состоит из двух соединенных между собой половинок. Будет в контролируемом состоянии Сжатые отверстия для винтов из-за линейного перемещения всей головки. Затем резьбовая пробка выдвигается и ввинчивается в винт, пока контролируемая часть вращается. Если есть отклонение в размере салазок, нормально замкнутый контакт размыкается, давая сигнал неисправному устройству. Выход конуса 3 из конического отверстия 2 и подвеска всей головки при управлении резиновым шнуром 1 осуществляют самовыравниванием заглушки по резьбе и ее продольным движением.
Системы управления зубчатыми колесами Автоматы типа ASHKA-1 (разработанные ENIMS), BV-539 и BV-8010 (разработанные Miistaikoprom exchange) были созданы для управления и сортировки зубчатых колес диаметром до 320 мм. непосредственно ниже. Эти системы контролируют кинематические погрешности однопрофильных и двухпрофильных зубчатых колес и изменения бокового зазора. В то же время обнаруживаются ошибки в плавном движении зубчатых колес.
Система автоматического управления и автоматического сбора данных с выборочной сборкой шариковых подшипников Система автоматического управления и комплектации при выборочной сборке. Выборочная сборка может быть выполнена тремя основными способами. Компоненты продукта сортируются по группам размеров, загружаются в систему, а затем выбираются в соответствии с заданной программой. Вы можете выбрать парные компоненты без предварительной их классификации.
Предварительная сортировка групп только из двух или более отдельных компонентов, сопряжение с контролем последующих несортируемых компонентов и выбор их с отсортированными компонентами определенной группы размеров. Последний метод используется в сборках шариковых и роликовых подшипников для получения радиального и осевого зазора в собранных подшипниках в пределах нормированных значений. На рисунке показана структура системы автоматического управления и автоматического сбора при выборочной сборке шарикоподшипников. 45.
В точке измерения системы средний диаметр беговой дорожки двух внутренних наружных опорных колец измеряется одновременно. Четыре измерительных сопла установлены на каждой измерительной станции и расположены под углом 90 градусов друг к другу. Это позволяет оценить размер канавки по среднему диаметру. Все восемь сопел содержатся в одной ветви воздушного пленочного преобразователя 11. Чем меньше диаметр канавки во внешнем кольце и чем больше диаметр канавки во внутреннем кольце, тем меньше разница между соплами и общим зазором сопла, тем больше зависит давление на левой стороне мембраны.
Педагоги. Клин движется в направлении уменьшения зазора, и когда давление на обеих сторонах мембраны равно, электрические контакты 12 и 13 замыкаются. Положение при переключении щетки 7 переключателя контакта замыкается, когда подвижная каретка 6 рельса закрыта. Соответствует группе размеров шара, необходимой для завершения. Многосекционное реле 4 выдает команду на выдачу набора шариков 5 из определенного бункера 3.
Смотрите также:
Решение задач по метрологии с примерами