Оглавление:
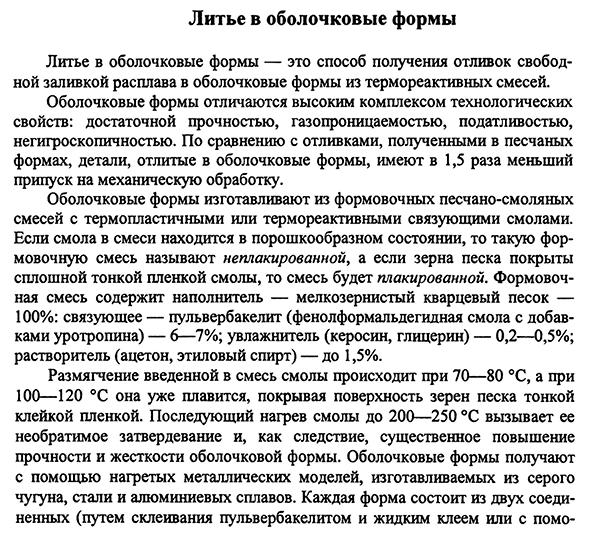
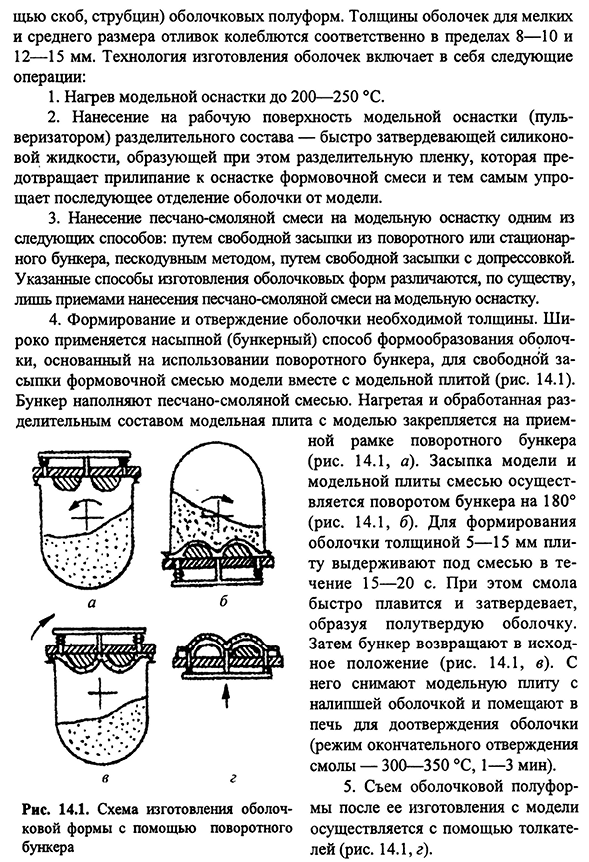
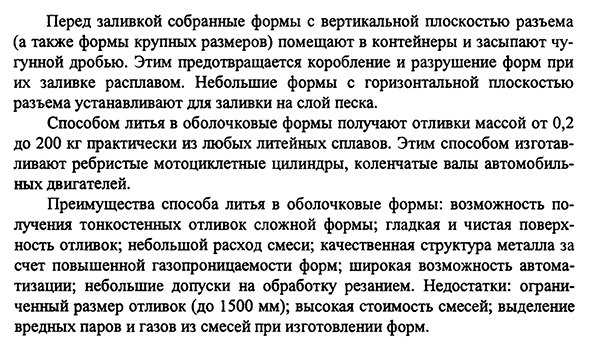

Литье в оболочковые формы
Литье в оболочковые формы Оболочечное литье-это способ изготовления отливок из термореактивных смесей путем свободного заливания в оболочечную форму. Оболочечная форма характеризуется комплексом высоких технических характеристик: достаточной прочностью, газопроницаемостью, гибкостью, негигроскопичностью.
По сравнению с отливками, полученными в песчаных формах, детали, отлитые в оболочковых формах, имеют в 1,5 раза больше места для обработки. Оболочковая форма изготавливается из смеси формовочных песчаных смол с термопластичной или термореактивной связующей смолой. Если смола в смеси находится в порошковом состоянии, то такую формовочную смесь называют непокрытой смесью, а если частицы песка покрыты сплошной тонкой пленкой смолы, то смесь 100%: связующее-пульдбакелит
(добавка уротропина и фенолформальдегидной смолы)-6-7%; (керосин, глицерин) −0,5%; (ацетонитрил, этилацетат и др.). Людмила Фирмаль
спирта) до 1,5%. Размягчение смолы, вводимой в смесь, происходит при 70-80 ° С, а при 100-120 ° С она уже плавится, покрывая поверхность песчинок тонкой клейкой пленкой.
Последующий нагрев смолы до 200-250°С приводит к ее необратимому затвердеванию, что приводит к значительному повышению прочности и жесткости оболочки формы.
- Прессформа шелухи произведена используя нагретую модель металла сделанную из серого литого железа, стали и алюминиевого сплава. Каждая форма состоит из двух соединенных (посредством присоединения микронизации и жидкого клея или с помощью- 325sch (скобы, зажимы) оболочка-полуформа
. Толщина оболочки для мелких и средних отливок колеблется в пределах 8-10 и 12-15 мм соответственно. Технология изготовления оболочки включает в себя следующие операции: 1. 200-250°C. 2 к прибору модели топления. Модельная оснастка (распылительная) нанесение на рабочую поверхность разделительного состава-быстро затвердевает силиконовая жидкость,
образует разделительную пленку, предотвращает прилипание оснастки к формовочной смеси и 3. Людмила Фирмаль
Применение песчано-смоляной смеси к любому из следующих способов модельной оснастки: путем свободной засыпки из роторного или стационарного бункера, пескоструйной обработки и пескоструйной обработки может быть достигнуто. Эти способы изготовления оболочковой формы, по существу, отличаются только способом нанесения песчано-смоляной смеси на модельную оснастку. 4. Формирование и упрочнение оболочки необходимой толщины. Широко используемый способ формирования объемной(бункерной) оболочки основан на использовании роторных бункеров, модельных плит (рис. 14.1).
Смесь песка и смолы. Конфигурация изоляции с моделью нагрета и обработана модельным вариантом зафиксированным к приему Рис 14.1. Способ изготовления оболочечной формы вращающимся бункером Рама роторного бункера (рис. 14.1, а). Заливка смеси в модельную и модельную плиты осуществляется с помощью бункера 180°(рис. 14.1, б). Чтобы сформировать оболочку толщиной 5-15 мм, подержите пластину под смесью 15-20 секунд. После этого бункер вернется в исходное положение фиг. 14.1, б). Затем снимают модельную плиту со штабельной крышкой и помещают ее в печь для удвоения крышки(окончательный режим отверждения смолы-300-350°с, 1-3 минуты). 5.
Удаление оболочки половины формы после изготовления из модели осуществляется с помощью толкателя (рис. 14.1, г). 326 перед заливкой собранную форму на вертикальную поверхность соединителя (а также в форму большого размера) помещают в емкость и заливают чугунной дробью. Это предотвращает деформацию и разрушение формы, когда она заполнена сплавлением. Небольшую форму с горизонтальной плоскостью соединителя устанавливают для заливки в слой песка. Методом литья в оболочковые формы является взвешивание отливок массой от 0,2 до 200 кг практически из всех литых сплавов. По этому методу цилиндр ребристого велосипеда является коленчатым валом двигателя автомобиля.
Преимущества способа литья в оболочковые формы: возможность получения тонкостенной отливки сложной формы; гладкая и чистая поверхность отливки; низкий расход смеси; низкая газопроницаемость формы минусы: ограниченный размер отливки (до 1500мм); высокая стоимость смеси; выделение вредных паров и газов из смеси при производстве литейных форм.
Смотрите также:
Литье под низким давлением | Ликвация и газы в литейных сплавах |
Литье вакуумным всасыванием | Технологические основы литейного производства |