Оглавление:
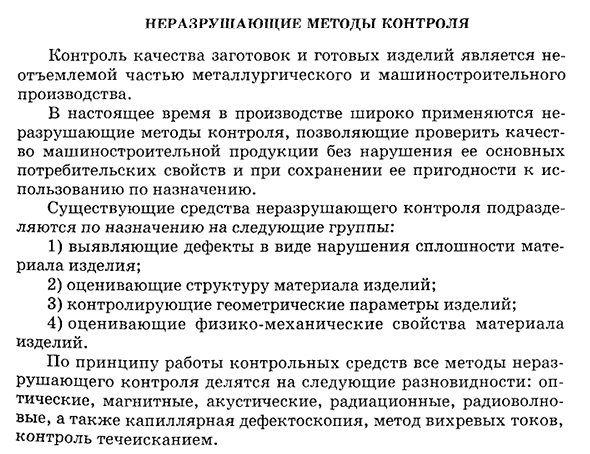
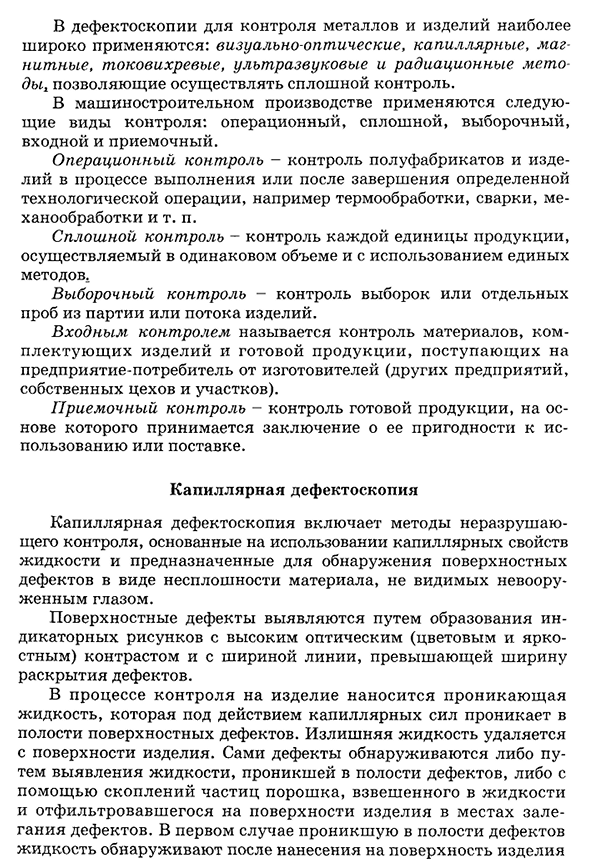
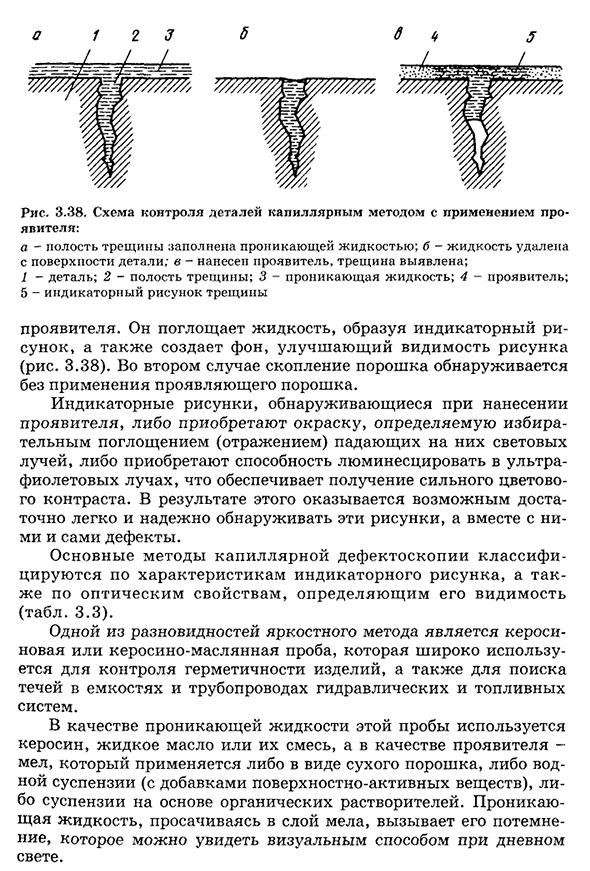
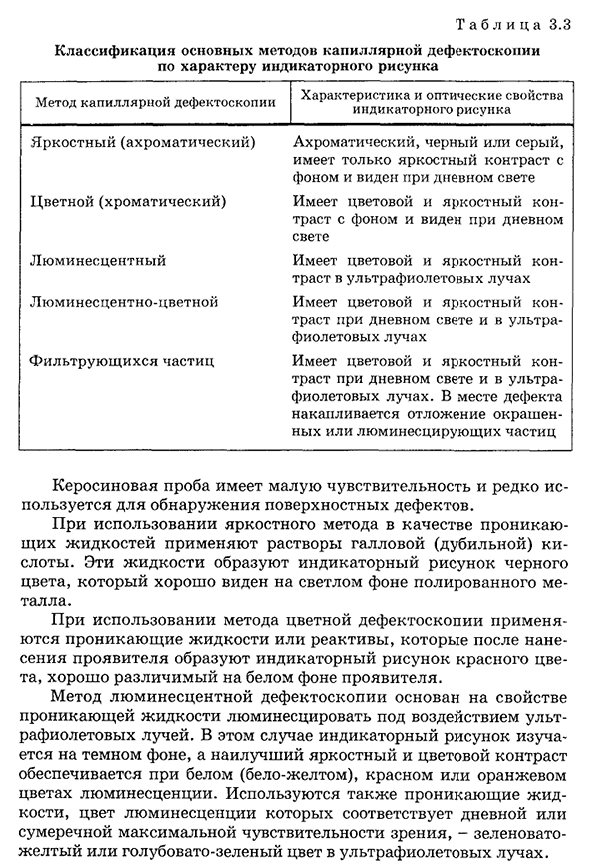
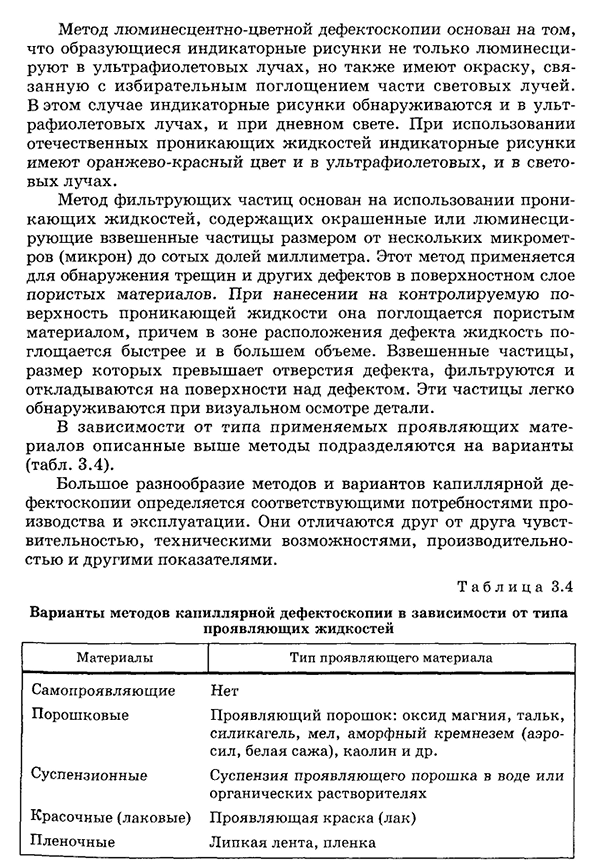
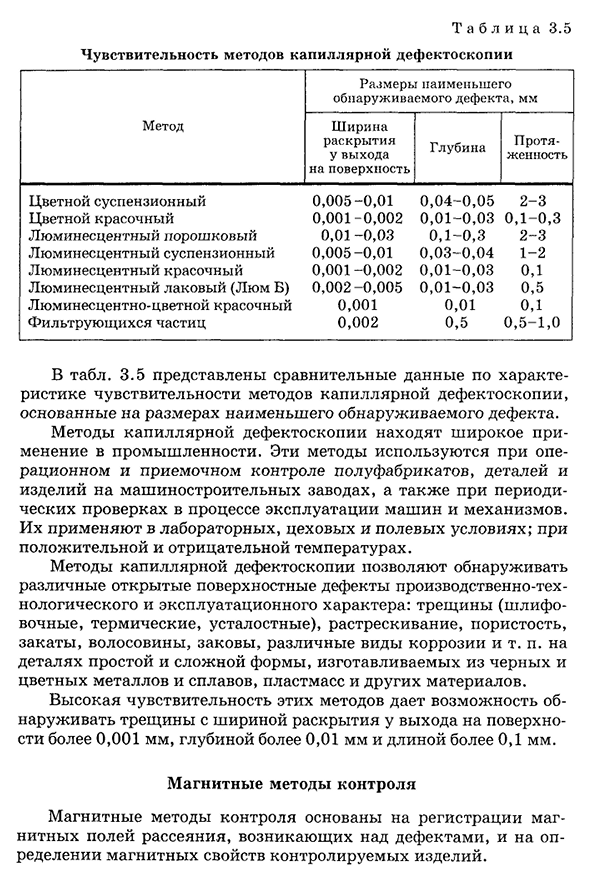
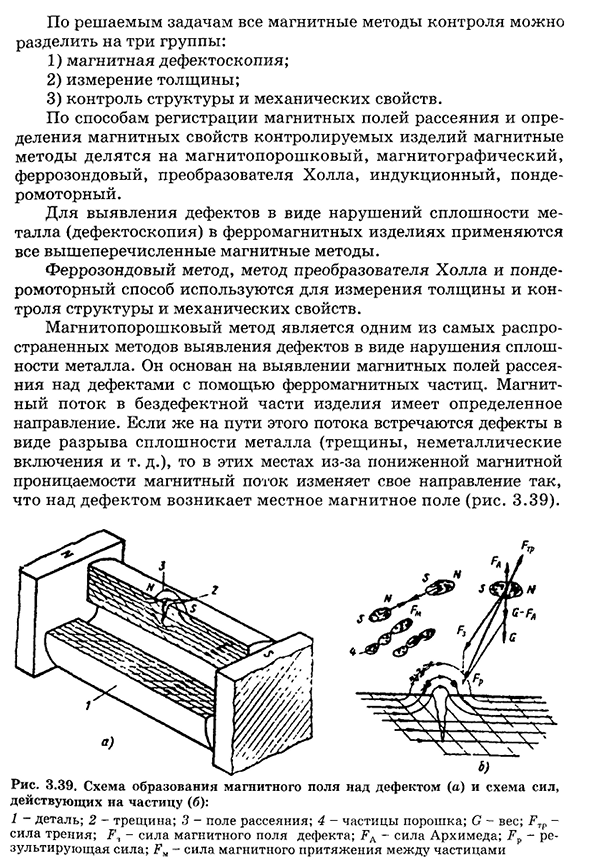
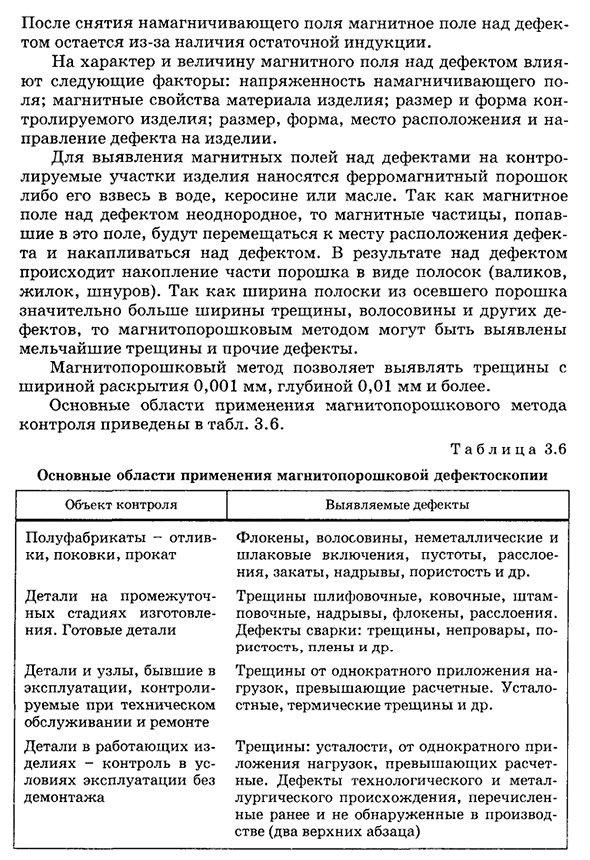
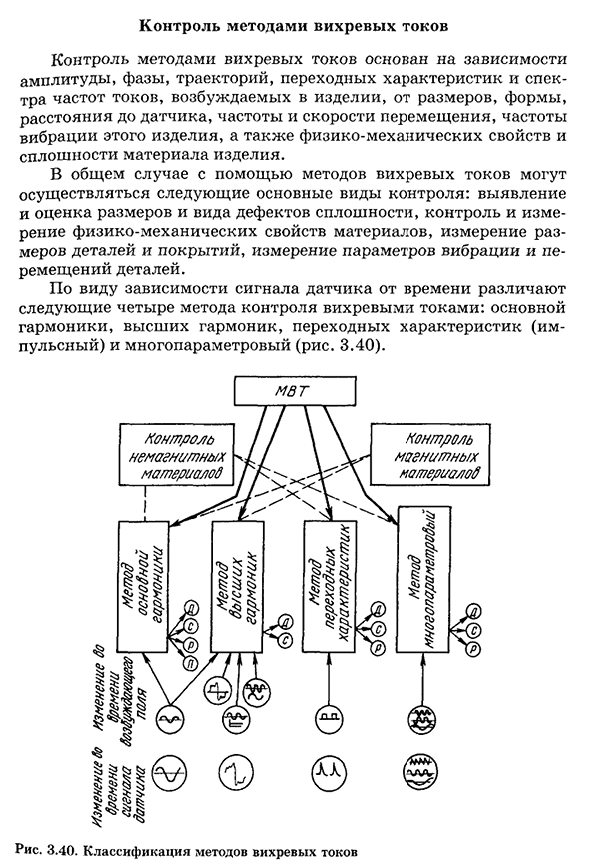
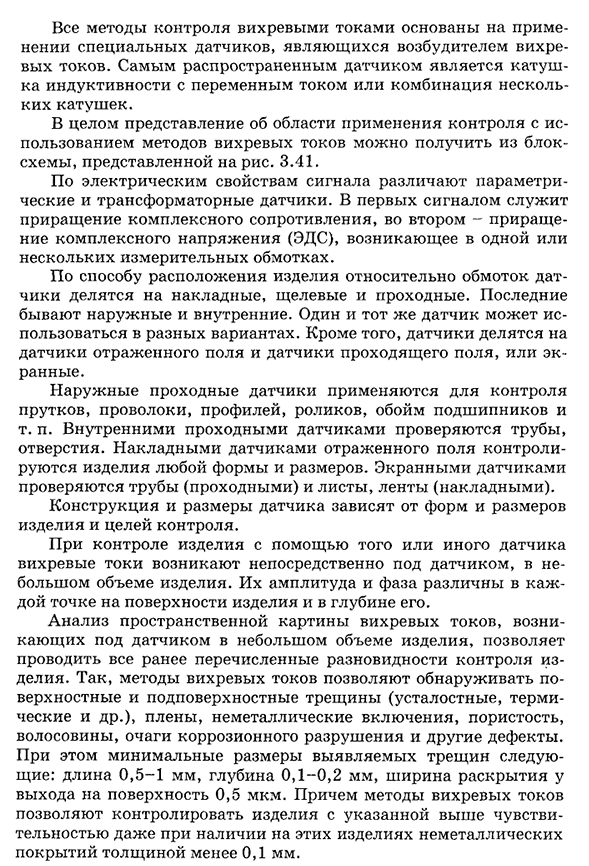
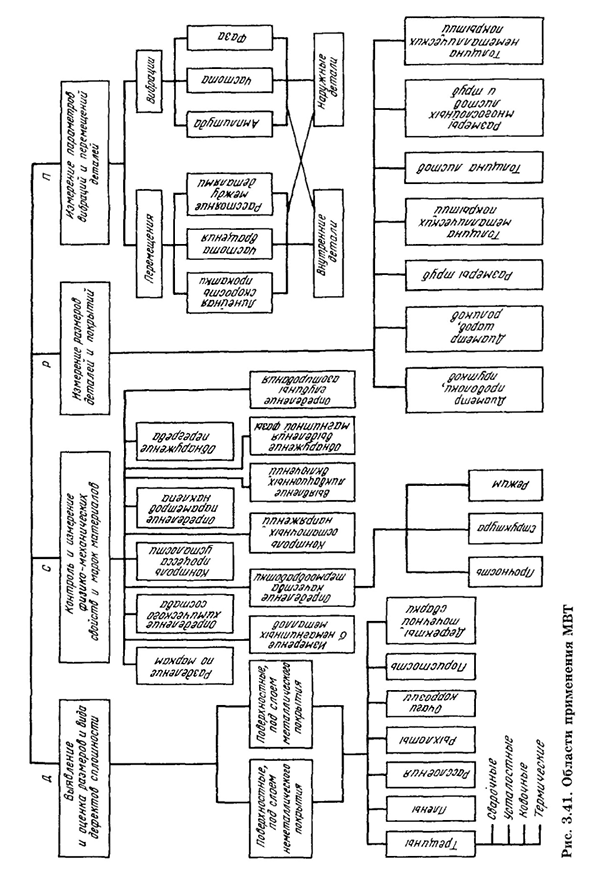
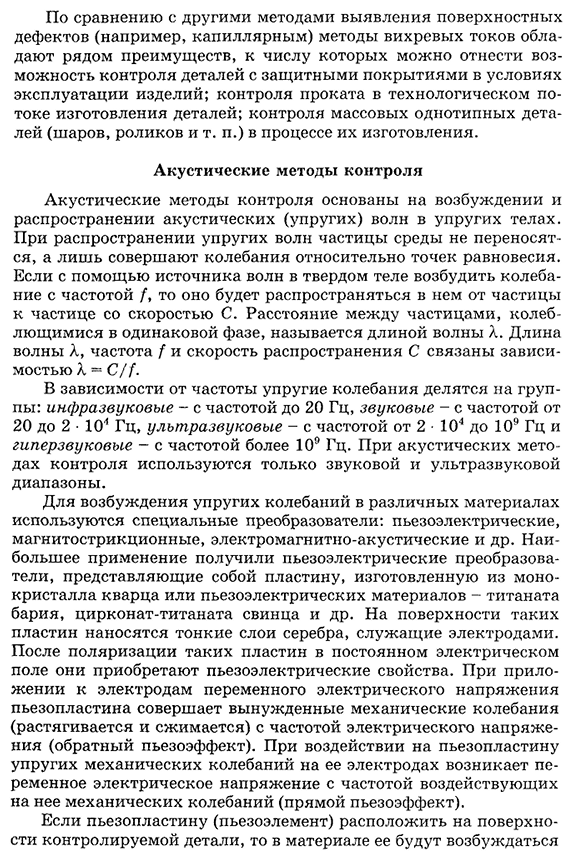
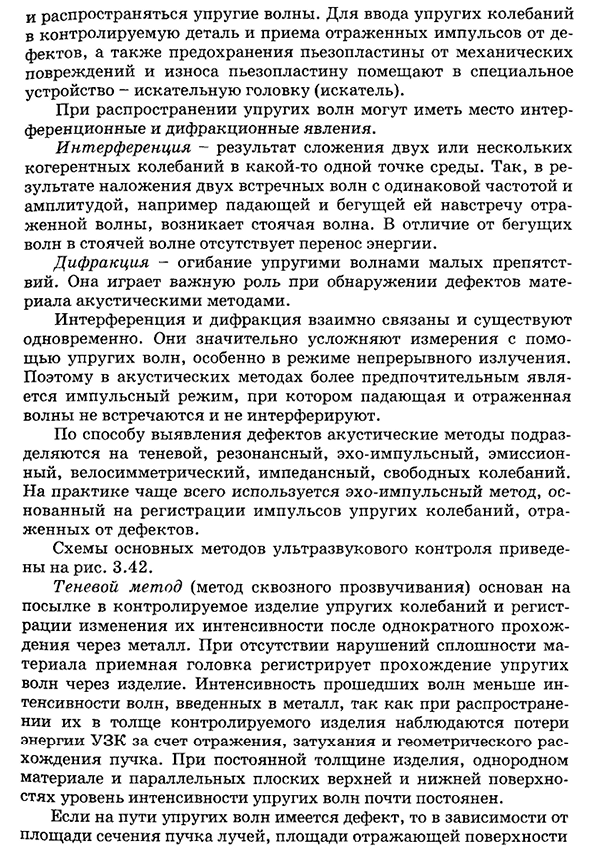
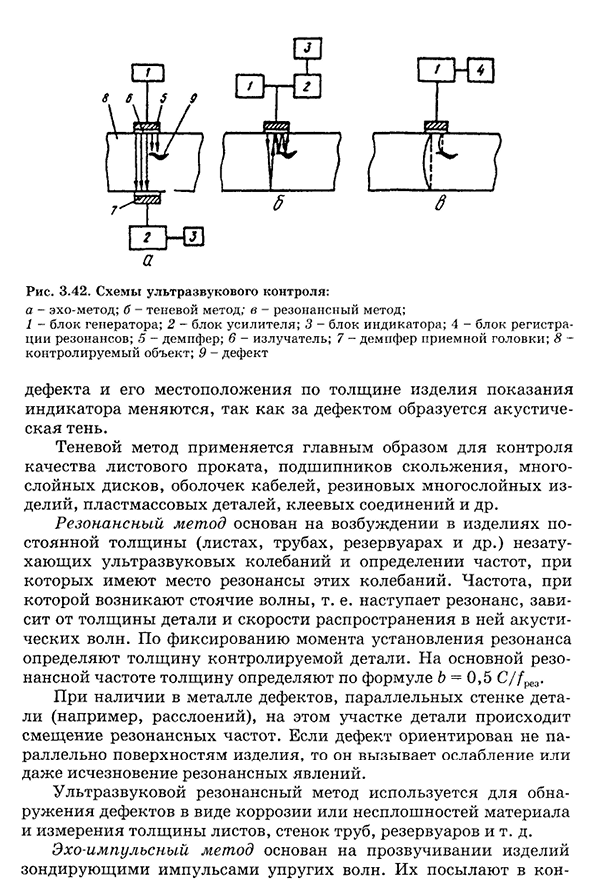
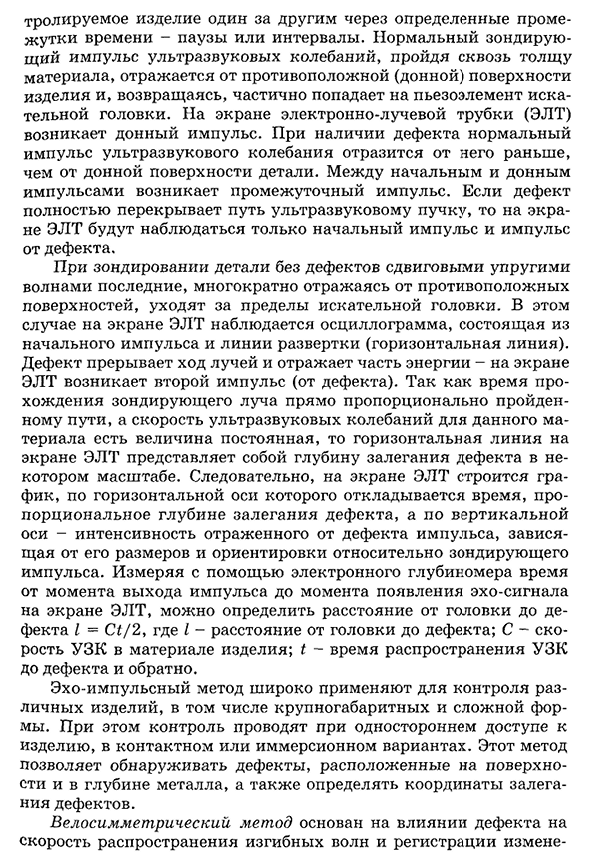
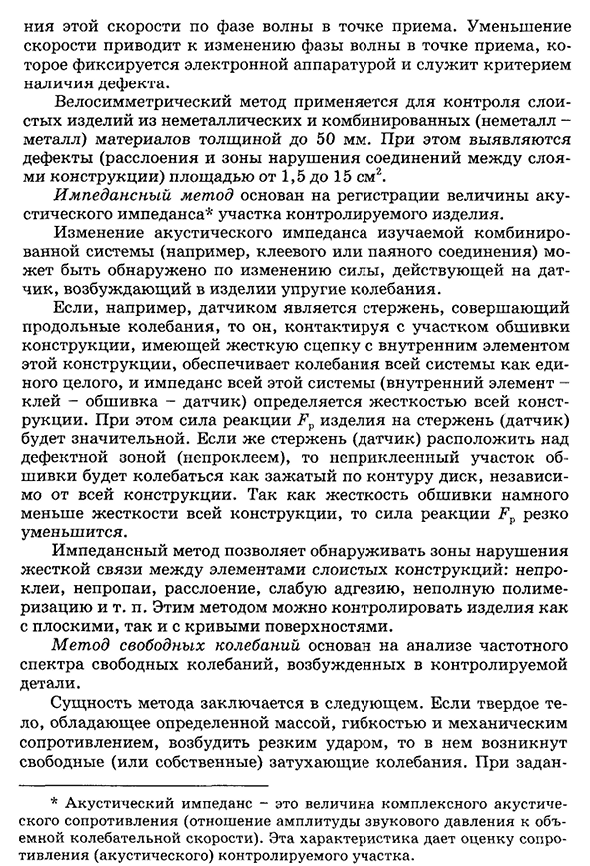
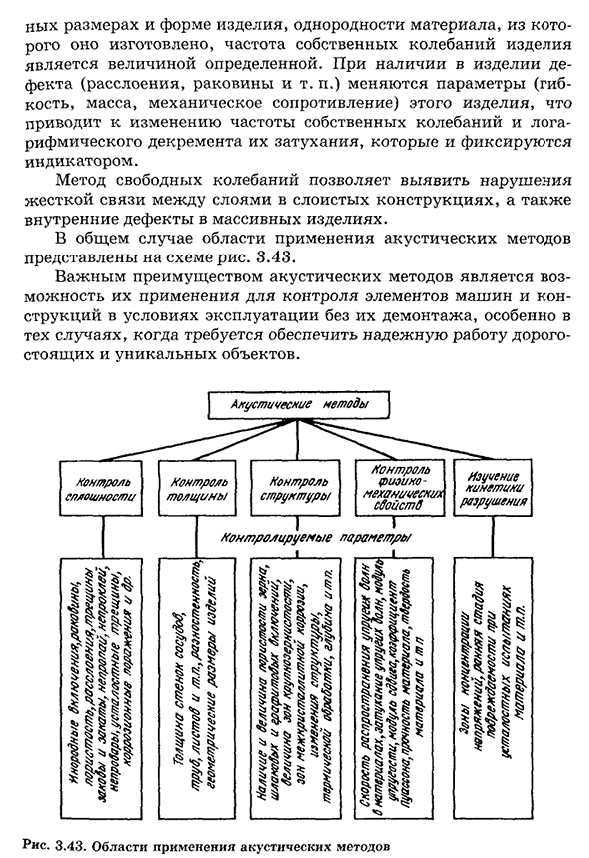
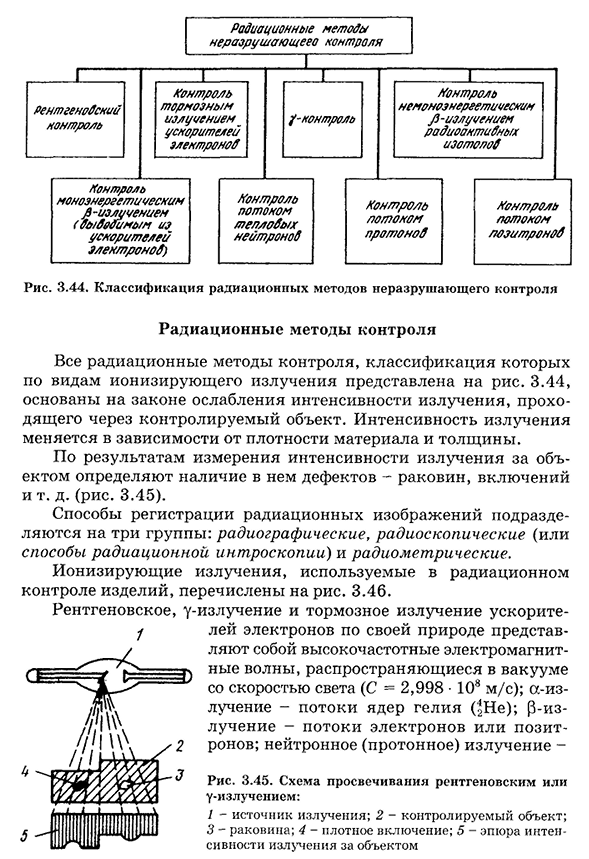
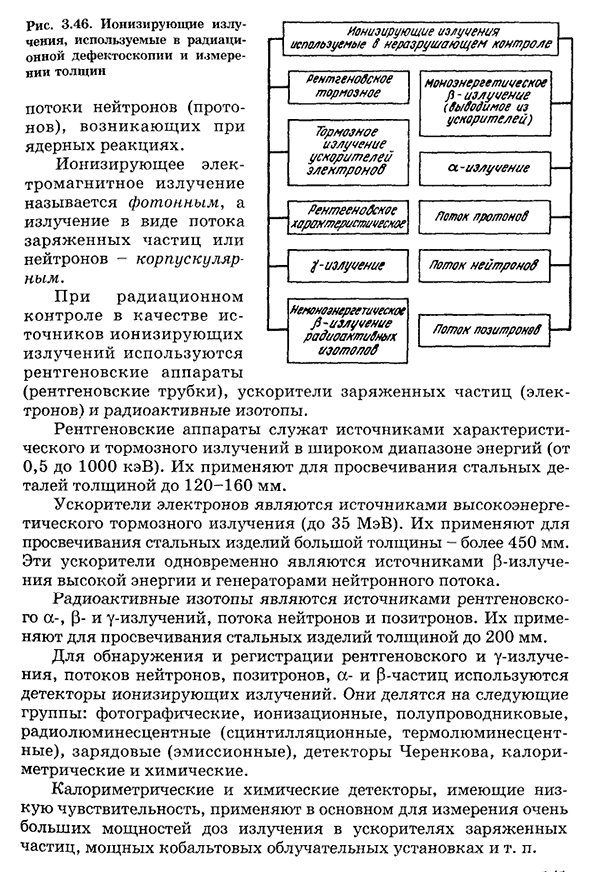
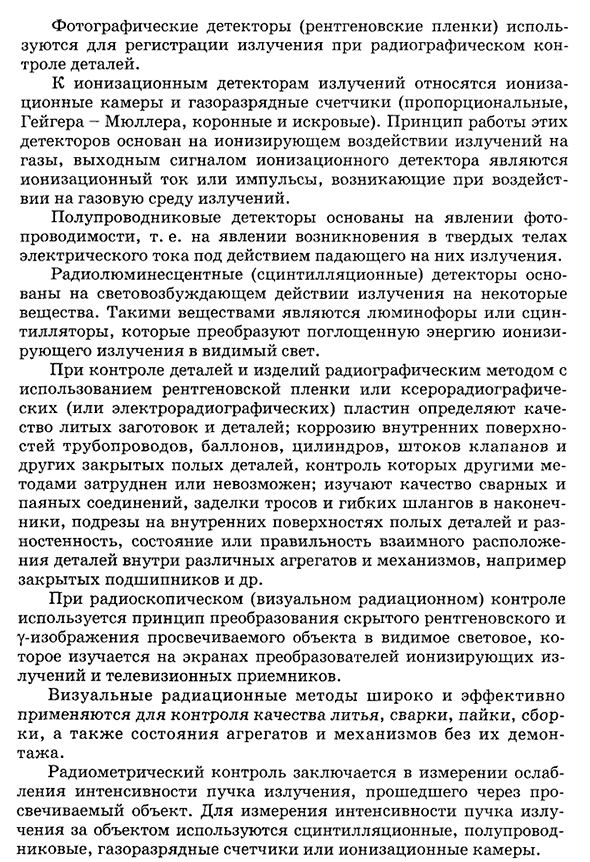
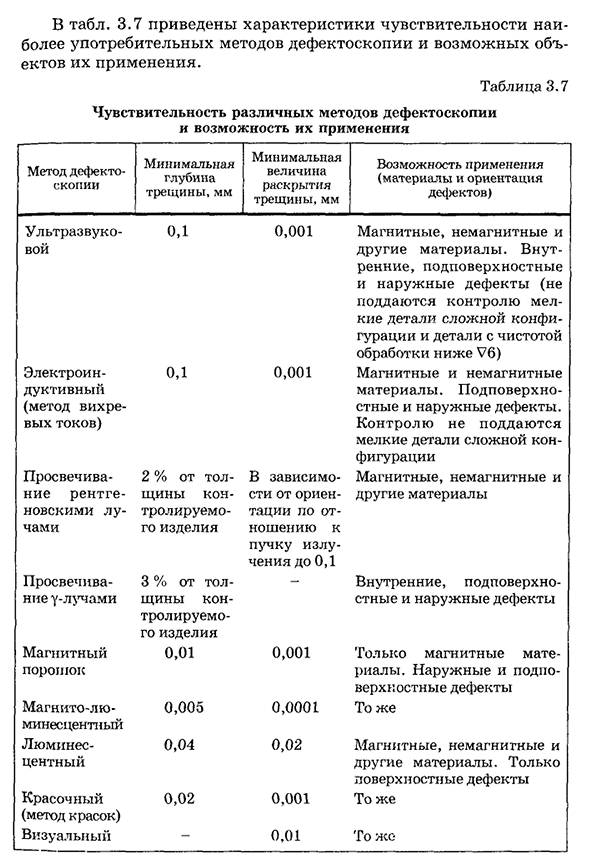

Неразрушающие методы контроля
- неразрушающий контроль Контроль качества заготовок и готовой продукции является неотъемлемой частью металлургического и машиностроительного производства. В настоящее время метод неразрушающего контроля широко применяется в области машиностроения, сохраняя при этом его пригодность к использованию по прямому назначению без нарушения его основных потребительских характеристик. Существующие методы неразрушающего контроля подразделяются на следующие группы по назначению: 1) выявление дефектов, таких как разрывы в материале изделий;2) оценка структуры материала изделий;3) оценка структуры изделий.
По принципу действия средств контроля все методы неразрушающего контроля подразделяются на оптические, магнитные, акустические, радиационные, радиоволновые, а также капиллярные дефектоскопы, вихретоковый метод, контроль обнаружения утечек. Дефектоскопия 123B для контроля металлов и изделий наиболее широко применяется: оптическая оптика, капиллярная, магнитная, вихретоковая, ультразвуковая и др., что позволяет осуществлять непрерывный контроль. В машиностроении применяются следующие виды управления: оперативное, непрерывное, избирательное, входное и приемное.
В процессе эксплуатации, контроля-выполнение полуфабрикатов или изделий после завершения определенных технологических операций, таких как термообработка, сварка, механическая обработка и др. Людмила Фирмаль
Непрерывный контроль-контроль каждой единицы продукции осуществляется в одном и том же объеме и с использованием одного и того же метода. Контроль проб-контроль проб или отдельных проб из партии или потока продукции. Входной контроль — это контроль материалов, комплектующих и готовой продукции, поступающей на предприятия-потребители от производителей (других компаний, собственных магазинов и площадок). Приемо-сдаточный контроль-это контроль готовой продукции, на основании которого будут сделаны выводы о пригодности к использованию или поставке. Обнаружение капиллярных дефектов включает неразрушающий контроль, основанный на использовании капиллярных свойств жидкости и обнаружении поверхностных дефектов в виде разрывов материала, которые не видны невооруженным глазом.
Дефекты поверхности выявляются путем формирования индикаторного рисунка с высоким оптическим (цветовым и яркостным) контрастом и шириной линии, превышающей ширину раскрытия дефекта. В процессе контроля на изделие наносят проникающую жидкость, которая под действием капиллярных сил проникает в полость поверхностного дефекта. Излишки жидкости удаляются с поверхности изделия. Сам дефект суспендируют в жидкости путем обнаружения жидкости, которая проникла в полость дефекта, или в том месте, где дефект возникает, и в первом случае порошок фильтруют на поверхность изделия, жидкость, которая проникла в полость дефекта, можно обнаружить после нанесения на поверхность изделия.
- 124A1 2 3Б У5 3.38 схема управления деталями проявителя с использованием капиллярного метода: — заполнить полость трещины проникающим раствором; б-удалить жидкость с поверхности детали; в-нанести проявляющую жидкость; в-удалить жидкость с поверхности детали. Он поглощает жидкость, образуя индикаторный паттерн, а также создает фон, который улучшает видимость паттерна (рис. 3.38). В последнем случае накопление порошка обнаруживается без использования проявляющего порошка. Индикаторный рисунок приобретает цвет, который определяется селективным поглощением (отражением) световых лучей, обнаруженных при нанесении проявителя или падающих на них, и в результате эти рисунки могут быть легко и надежно обнаружены, а сам дефект может быть легко обнаружен.
Основные методы капиллярной дефектоскопии классифицируются по характеристикам индикаторной картины, а также оптическим свойствам, определяющим ее видимость (таблица). 3.3). Одна из разновидностей метода яркости широко применяется для контроля герметичности изделия, а также для поиска утечек в баках и трубопроводах в гидравлических или топливных системах. В качестве проникающего раствора этого образца используют керосин, жидкое масло или его смесь, проникая в слой мела, применяемого в виде сухого порошка или водной суспензии (с добавками поверхностно-активных веществ), проникающая жидкость затемняет его и может быть видна визуально в дневное время. 125
Классификация основных методов обнаружения капиллярных дефектов по характеру индикаторной картины Т а б л и Ц А3. Людмила Фирмаль
Три Способ обнаружения капиллярных дефектов и оптических характеристик индикаторной картины Яркость (бесцветный) ахроматический цвет, черный или серый, имеет только контраст яркости с фоном, цвет дневного света (цвет цвета) имеет контраст цвета и яркости с фоном, цвет дневного света (цвет цвета) имеет контраст цвета и яркости с фоном. Люминесценция имеет контраст цвета и яркости ультрафиолетовая люминесценция имеет контраст цвета и яркости дневного света и ультрафиолета. На месте дефектов накапливаются отложения окрашенных или люминесцентных частиц Образцы керосина менее чувствительны и редко используются для обнаружения поверхностных дефектов. При использовании метода люминесценции в качестве осмотической жидкости применяют растворы галловой кислоты (и дубильной кислоты).
Эти жидкости образуют черный индикаторный узор, который хорошо виден на ярком фоне полированного металла. При использовании метода обнаружения цветовых дефектов используют осмотическую жидкость или реагент, после нанесения проявителя образующий красную индикаторную картину, и на белом фоне проявителя. Метод флуоресцентного тестирования основан на свойстве пропускать и излучать жидкость под воздействием ультрафиолетовых лучей. В этом случае индикаторная картина изучается на темном фоне, лучшая яркость и цветовой контраст обеспечивается белым (бело-желтым), красным или оранжевым излучающим цветом, также используется пропускаемая жидкость, а ее световой цвет соответствует максимальной чувствительности дневных сумерек или сумерек (зеленовато-желтый или сине-зеленый в ультрафиолете).
Метод флуоресцентного обнаружения дефекта цвета основан на том, что полученный индикаторный рисунок не только излучает свет в ультрафиолетовом диапазоне, но и имеет цвет, связанный с избирательным поглощением световых лучей. В этом случае индикаторная картина обнаруживается в ультрафиолетовом и дневном свете. При использовании бытовой проникающей жидкости индикаторные цифры оранжево-красные как с ультрафиолетовыми, так и со световыми лучами. Метод фильтрующих частиц основан на использовании перколяционной жидкости, содержащей окрашенные или люминесцентные взвешенные частицы размером от нескольких микрометров (микрон) до ста миллиметров, этот метод используется для обнаружения трещин и других дефектов в поверхностных слоях пористых материалов.
При нанесении на контролируемую поверхность проницаемой жидкости она поглощается пористым материалом, и в области расположения дефекта жидкость поглощается в большем объеме быстрее, чем дефектная пора, а крупные взвешенные частицы фильтруются и осаждаются на поверхности над дефектом. Эти частицы легко обнаруживаются при визуальном осмотре детали. В зависимости от типа используемого проявочного материала описанный выше способ основан на варианте(табл. 3.4). Большое разнообразие методов и вариантов обнаружения капиллярных дефектов определяется соответствующими потребностями производства и эксплуатации.
Они отличаются друг от друга чувствительностью, техническими возможностями, производительностью и другими показателями. Т А Б Л и Ц А3. 4 Вариации метода капиллярной дефектоскопии в зависимости от типа проявителя Материальный Самобалансирующийся порошок Суспензия красочная (лаковая) пленка Типа растущих материальных Отсутствие порошка роста: окись магния, тальк, гель кремнезема, мел, аморфный кремнезем (аэросил, белая сажа), каолин, ЕТК. Вода или органический растворитель рост порошок суспензия рост краска (лак) клейкая лента, пленка 127T a b l и C 3.5 чувствительность метода обнаружения капиллярных дефектов
Наименьший обнаруживаемый размер дефекта, мм Поверхностным ширина проема Глубина длина Цвет подвески 0,005-0,01 0,04-0,05 2-3 красочные цвета 0,001-0,002 0,01-0,03 0,1-0,3 флуоресцентный порошок 0,01 −0,03 0,1-0,3 2-3 люминесцентная подвеска 0,005-0,01 0,03-0,04 1-2 красочные флуоресцентные 0,001 −0,002 0,01-0,03 0,1 флуоресцентный лак (лум Б)0,002-0,005 0,01-0,03 0,5 флуоресцентные цвета красочные 0.001 0.01 0.1 фильтрации частиц 0,002 0,5 0,5-1,0 За столом. Приведены сравнительные данные по характеристикам чувствительности метода обнаружения капиллярных дефектов 3.5, основанные на наименьшем размере обнаруженного дефекта.
Метод обнаружения капиллярных дефектов широко используется в промышленности. Эти методы характеризуются детальным эксплуатационным и приемо-сдаточным контролем полуфабрикатов, машиностроительных заводов и изделий, а также периодическими проверками в процессе эксплуатации машин и механизмов. Они используются в лабораториях, цехах и полевых условиях; при положительных и отрицательных температурах. Метод капиллярного дефектоскопирования позволяет выявлять различные открытые поверхностные дефекты промышленного, технического и эксплуатационного характера: трещины (шлифовальные, термические, усталостные), трещины, пористость, простые, сложные по форме детали из черных и цветных металлов и сплавов, пластмасс и других материалов.
Высокая чувствительность этих методов позволяет обнаруживать трещины в ширине отверстий на поверхностных выходах более 0,001 мм, глубинах более 0,01 мм и длинах более 0,1 мм. Метод магнитного контроля метод магнитного контроля основан на регистрации магнитного поля рассеяния магнитного поля вследствие дефектов и определении магнитных свойств контролируемых изделий. 128F Согласно разрешенной проблеме, все магнитные методы контроля можно разделить в 3 группы: 1)магнитное обнаружение неисправностей;2)измерение толщины;3) управление структуры и механических свойств.
В соответствии с методом регистрации магнитного поля контролируемого продукта магнитные свойства рассеяния и определения, магнитный метод делится на магнитный порошок, магнитный, феррозонд, Датчик Холла, индукционный, пондермотор. Для выявления дефектов в виде нарушения сплошности металла (дефектоскопии) в ферромагнитных изделиях используются все вышеперечисленные магнитные методы. Толщину, структуру управления и механические свойства измеряли с помощью метода ферроплова, метода датчика Холла и метода двигателя Пондера. Метод магнитных частиц является одним из наиболее популярных методов обнаружения дефектов в виде нарушения сплошности металла.
Он основан на обнаружении магнитного рассеяния магнитного поля на дефектах с использованием ферромагнитных частиц. Магнитный поток в бездефектной части изделия имеет определенное направление. В середине этого потока, если имеются дефекты в виде разрывов металлов (трещины, неметаллические включения и др.).И в этих местах магнитная проницаемость уменьшается, так что магнитный поток меняет направление, так что локальное магнитное поле генерируется против дефекта(рис. 3.39). Рис. 3.39 схема формирования магнитного поля относительно дефекта (а) и схема действия силы на частицу (Б): 1-деталь; 2-трещина;3-поле рассеяния;4-частицы порошка; г-масса; F,,,, — сила трения;
F3-магнитное поле дефекта; FA-алкимент; 5-2 9 8 6 129 после удаления поля намагничивания магнитное поле над дефектом остается из — за наличия остаточной индукции. На характер и величину магнитного поля над дефектом влияют следующие факторы: сила намагничивания; магнитные свойства материала изделия; размер контролируемого изделия. Применитесь к контролируемой зоне продукта для того чтобы обнаружить дефекты, ферромагнитный порошок или подвес в воде, керосине или месторождении нефти. Поскольку магнитное поле над дефектом неоднородно, магнитные частицы, захваченные в этом поле, перемещаются в положение дефекта и накапливаются на дефекте.
В результате над дефектом происходит накопление порошка в виде полосок (валиков, жил, Шнуров). Ширина полосы от осевшего порошка намного больше ширины трещины, волосяного покрова и других дефектов, так что мельчайшие трещины и другие дефекты не покрываются методом магнитного порошка. Метод магнитных частиц позволяет выявить такие трещины, как ширина раскрытия 0,001 мм, глубина раскрытия 0,01 мм. Основные области применения метода управления магнитными частицами приведены в таблице. Это 3.6. Т А Б Л и Ц А3. 6 основных приложений для магнитной дефектоскопии Объект управления обнаруженными дефектами Полуфабрикаты-отливки, поковки, прокатные группы, волосовины, неметаллические и шлаковые включения, пустоты, пучки, закаты, разрывы, пористость и др.
Изготовление компонентов средней стадии. Готовая деталь Молоть, ломать, ковать, штемпелевать, стадо, пачка. Дефекты сварки: трещины проникновения, отсутствие пористости, Щепка и т. д. Контролируются в процессе технического обслуживания и ремонта детали узлов и агрегатов, находившиеся в эксплуатации, рабочие изделия-контроль в процессе эксплуатации без разборки Трещины от однократного приложения нагрузок, превышающих расчетные. Усталость, термические трещины и др. Трещины: усталость от однократного приложения нагрузки, превышающей расчетную. Дефект вышеупомянутого технического и металлургического происхождения, не обнаруженный в производстве(два абзаца выше) 130 Управление вихретоковым методом управление вихретоковым
методом используется для определения амплитуды, фазы и траектории накачиваемого в изделие тока, размера и формы переходных и частотных спектров.、 В общем случае вихретоковый метод используется для обнаружения и оценки размеров и типа непрерывных дефектов, для контроля и измерения физико-механических свойств материалов, для обнаружения и оценки компонентов и покрытий. По типу временной зависимости сигнала датчика различают основной гармонический, гармонический, переходный (импульсный) и многопараметрический(фиг. 3.40). Все методы вихретокового контроля основаны на использовании специального датчика, который является возбуждающим агентом вихревых токов.
Наиболее распространенным датчиком является индукционная катушка с переменным током или комбинация нескольких катушек. В общем случае представление о диапазоне регулирования вихретоковым методом можно получить из блок-схемы, представленной на рисунке. 3.41 В зависимости от электрических характеристик сигнала различают параметрические и трансформаторные датчики. В первом сигнале вторым является приращение комплексного сопротивления-приращение комплексного напряжения (ЭДС), которое возникает в одной или нескольких измеряемых обмотках. По способу размещения изделия относительно обмоток датчик делится на накладные, щелевые и сквозные. Последние бывают внешними и внутренними. Один и тот же датчик может использоваться по-разному. Кроме того, датчик разделен на датчик отраженного поля и датчик проходящего поля, или датчик экрана.
Штанга, профиль провода, кольцо подшипника ролика etc. внутренние датчики расхода, используемые для контроля внешнего микродатчика раствора, проверяются трубкой, отверстием. Надземный датчик для отражательных продуктов контроля поля любых формы и размера. Экранные датчики проверяют трубы (сквозные), листы, ленты(накладные провода). Конструкция и размеры датчика зависят от формы и размера изделия и цели его контроля. При контроле изделия с помощью датчика вихревые токи генерируются непосредственно под датчиком в небольшом количестве изделия. Их амплитуда и фаза различаются в каждой точке на поверхности изделия и в его глубине.
Анализируя пространственные закономерности вихревых токов, возникающих под датчиком в небольшом объеме изделия, можно осуществлять все ранее перечисленные виды управления изделием. Таким образом, вихретоковый метод позволяет выявлять поверхностные и подповерхностные трещины (усталостные, тепловые и др.).), Очаги захвата, неметаллические включения, пористость, волосяной покров, коррозионное разрушение и другие дефекты. При этом минимальные размеры обнаруженных трещин составляют 0,5-1 мм в длину, 0,1-0,2 мм в глубину, ширина отверстия на выходе на поверхность 0,5 мкм.
Кроме того, вихретоковый метод позволяет контролировать изделия с описанной выше чувствительностью даже при наличии неметаллических покрытий толщиной менее 0,1 мм. Тысяча, сто, двести, одиннадцать Рис. 3.41 области применения МВ по сравнению с другими методами обнаружения поверхностных дефектов (например, капиллярные трубки) методом вихретокового контроля защитного покрытия и деталей в процессе эксплуатации изделия)в процессе его изготовления. Акустический метод управления основан на возбуждении и распространении акустических (упругих) волн в упругом теле.
При распространении упругой волны частицы среды не смещаются и вибрируют только относительно точки равновесия. При использовании источника волн в твердом теле для возбуждения колебаний на частоте f он распространяется от частицы к частице со скоростью C до точки между частицами, колеблющимися в одной и той же фазе. В зависимости от частоты упругие колебания делятся на группы: инфразвуковые-частоты до 20 Гц, звуковые-20-2•104 Гц, ультразвуковая частота 2 * 104-109 Гц, Полярная частота выше 10 000 Гц. Акустический метод управления использует только диапазон звука и ультразвука.
Для возбуждения упругих колебаний различных материалов используются специальные преобразователи, такие как пьезоэлектрический, магнитный тр, электромагнитная акустика. Наиболее широко используемым пьезоэлектрическим преобразователем является пластина, выполненная из монокристалла кристалла или пьезоэлектрического материала, такого как титанат бария, титанат цирконата свинца. На поверхность такой пластины наносится тонкий слой серебра, который служит электродом. После поляризации таких пластин в постоянном электрическом поле они приобретают пьезоэлектрические свойства. Когда переменное электрическое напряжение приложено к электроду, пьезопластина произведет принудительную механическую вибрацию (растянутую и сжатую) с частотой электрического напряжения (обратный пьезоэффект).
При воздействии на пьезоэлектрическую пластину упругих механических колебаний на электроде возникает переменное напряжение с частотой действующих на него механических колебаний (прямой пьезоэффект). Когда пьезопластина (пьезоэлемент) помещается на поверхность контролируемой детали, упругая волна возбуждается и распространяется на материал 134. Для введения упругих колебаний в контролируемую деталь, получения импульсов, отраженных от дефекта, защиты пьезопластины от механических повреждений и износа необходимо использовать пьезопластину. При распространении упругих волн могут наблюдаться интерференционные и дифракционные явления. Интерференция-это результат сложения двух или более когерентных колебаний в одной точке среды.
Таким образом, в результате суперпозиции двух противоположных волн с одинаковой частотой и амплитудой, например, падающих и бегущих навстречу ей отраженных волн, возникает стоячая волна. В отличие от непрерывной волны, в стоячей волне отсутствует передача энергии. Дифракция-это изгиб небольшого препятствия упругой волной. Он играет важную роль в обнаружении дефектов материала акустическим методом. Интерференция и дифракция взаимосвязаны и существуют одновременно. Они значительно усложняют измерение упругими волнами, особенно в режиме непрерывного излучения. Поэтому в акустическом методе более предпочтителен импульсный режим, в котором падающая волна и отраженная волна не интерферируют.
По способу обнаружения дефектов акустический метод подразделяют на теневой, резонансный, Эхо-импульсный, радиационный, велосиметрический, импедансный, свободный вибрационный. На самом деле, наиболее часто используется Эхо-импульсный метод, основанный на регистрации импульса упругих колебаний, отраженных от дефекта. Схема основных методов ультразвукового исследования приведена на рисунке. 3.42 Теневой метод (через звуковой метод) основан на посылке упругой вибрации на контролируемое изделие, регистрируя изменение интенсивности после одного прохода через металл. При отсутствии нарушения непрерывности приемной головки материала она регистрирует прохождение упругих волн через изделие.
Интенсивность передаваемых волн зависит от толщины контролируемого изделия, при их распространении потери энергии обусловлены отражением, затуханием и расходимостью пучка, так что при определенной толщине золотого изделия, однородного материала и параллельной плоской верхней и нижней поверхности, уровень интенсивности упругой волны практически постоянен. В зависимости от площади поперечного сечения пучка, отражающей поверхности, при наличии дефектов на пути распространения упругой волны 135А Рис. 3.42 схема ультразвукового контроля: Эхо-метод; Б-теневой метод; в-резонансный метод;1 блок генератора; 2 блока усилителя; 3 блока индикатора; 4 блока регистрации резонанса;5 демпфера;6 излучателя; 7 приемного блока
Из дефектов по толщине изделия и его расположению показания индикатора изменяются, так как за дефектом образуется акустическая тень. Метод тени главным образом использован для проверки качества металлического листа, сползая подшипника, разнослоистого диска, оболочки кабеля, резиновых разнослоистых продуктов, пластичных частей, слипчивых соединений, etc. Резонансный метод основан на стимуляции непрерывной ультразвуковой вибрации изделия постоянной толщины (листа, трубки, бака и др.). Определение частоты, на которой возникает резонанс этих колебаний. Частота, с которой возникает стоячая волна, то есть резонанс, зависит от толщины детали и скорости распространения в ней звуковой волны. Толщина контролируемой детали определяется путем фиксации момента установления резонанса.
На основной резонансной частоте толщина определяется по формуле b=0,5 C/fve3. При наличии дефектов металла, параллельных стенке детали (например, пучка), в этой части детали происходит смещение резонансной частоты. Если дефект не ориентирован параллельно поверхности изделия, это вызывает ослабление или исчезновение явления резонанса. Ультразвуковой резонансный метод используется для обнаружения дефектов в виде коррозии или разрыва материалов и для измерения толщины листа, стенки трубы, резервуара и др. Эхо-импульсный метод основан на звуке изделия путем зондирования импульса упругой волны. Они отправляются в аферу- 136 продуктов контролируются один за другим с определенными интервалами-паузами или интервалами.
Обычный зондирующий импульс ультразвуковых колебаний, проходящий через толщину материала, отражается от (нижней) поверхности противоположной стороны изделия, а на задней частично поисковой головке пьезоэлемента появляется нижний импульс на экране электронно-лучевой трубки (ЭЛТ). При наличии дефектов нормальный импульс ультразвуковых колебаний отражается от него раньше, чем от нижней части детали. Промежуточные импульсы генерируются во время начального и нижнего импульсов. Если дефект полностью перекрывает путь ультразвукового луча, то на экране ЭЛТ наблюдаются только начальный импульс и импульс от дефекта. Этой скорости в волновой стадии точки приема.
Уменьшение скорости фиксируется электроникой, что приводит к изменению фазы волны в точке приема, которая служит ориентиром для наличия дефектов. Метод Велоциметрии применяется для контроля слоистых изделий из неметаллических и композиционных (металлических) материалов толщиной до 50 мм. дефекты (чешуйки) составляют от 1,5 до 15 см2 Метод импеданса основан на регистрации значения акустического импеданса контролируемой области изделия. * Акустическое сопротивление — это величина комплексного акустического сопротивления (отношение амплитуды звукового давления к скорости колебаний звукового давления). Эта характеристика дает оценку сопротивления (акустического) контролируемой фазы.
Изменение акустического импеданса исследуемых сложных систем (например, клеевых или паяных соединений) представляет собой изменение силы, действующей на датчик, возбуждающий упругие колебания изделия. Например, если датчик представляет собой стержень, который совершает продольные колебания, то он контактирует с внутренними элементами этой конструкции и кожной частью конструкции с жесткой связью, и в этом случае сила реакции изделия на стержень (датчик) f. p является значительной. Если стержень (датчик) расположен над дефектной зоной (неклеевой), как диск, закрепленный по контуру, то жесткость обшивки значительно меньше, чем у всей конструкции, поэтому противодействующая сила ФП резко снижается.
Импедансный метод позволяет выявлять участки нарушения жестких связей между элементами слоистой структуры, такие как неклеевые, неклеевые, шелушащиеся, слабая адгезия, неполная полимеризация. Этот способ позволяет управлять изделием как на плоских, так и на криволинейных поверхностях. Метод свободных колебаний основан на анализе частотного спектра свободных колебаний, возбуждаемых в контролируемой части. Суть метода заключается в следующем. Если твердое тело с определенной массой, гибкостью и механическим сопротивлением возбуждается резким ударом, то в нем возникает свободное (или собственное) демпфирующее колебание.
При установке- 138-это размер и форма изделия, однородность материала, из которого оно изготовлено, частота собственных колебаний изделия составляет определенную величину. Когда дефект продукта (пачка, раковина, etc.).) Изменяет параметры (гибкость, вес, механическое сопротивление) данного изделия, что приводит к изменению собственной частоты и логарифмическому затуханию регистрируемого индикатором затухания. Метод свободной вибрации позволяет выявить нарушения строгой связи между слоями в слоистой конструкции, а также внутренние дефекты крупногабаритного изделия. В целом, на рисунке показано применение акустического метода. 3.43
Важным преимуществом акустического метода является возможность выполнения механических и конструкционных работ без их демонтажа, особенно когда необходимо обеспечить надежную эксплуатацию дорогостоящих и уникальных объектов. Рис 3.43 область применения акустического метода 139). 3.44 классификация методов неразрушающего радиационного контроля Радиационные методы контроля все радиационные методы, контролирующие их классификацию по типу ионизирующего излучения, показаны на рисунке. 3.44, основанный на законе ослабления интенсивности излучения, проходящего через контролируемый объект. Интенсивность излучения изменяется в зависимости от плотности и толщины материала. По результатам измерения интенсивности излучения за объектом определяется наличие в нем дефектов-оболочек, включений и др. (Инжир. 3.45).
Метод регистрации радиационных изображений делится на три группы. Ионизирующее излучение, используемое в продуктах радиационного контроля, описано на рисунке. 3.46 Рентгеновское, y-образное и тормозное излучения ускорителя электронов по своим свойствам представляют собой высокочастотные электромагнитные волны, распространяющиеся в вакууме со скоростью света (с=2,998•108 м / с). — Рис. 3.45 схема передачи рентгеновского или u излучения:1-источник излучения; 2-контролируемый объект;3-оболочка; 4-герметичное включение;5-график интенсивности излучения за объектом 140-1 3.46 ионизирующее излучение, используемое для обнаружения и измерения радиационных дефектов Поток нейтронов (протонов), возникающий в результате ядерной реакции. Ионизирующее электромагнитное излучение называют фотонным, излучением в виде потока заряженных частиц или нейтронов-частиц. В радиационном контроле в качестве источников ионизирующего излучения используются рентгеновская аппаратура (рентгеновские трубки), ускорители и радиоактивные изотопы заряженных частиц (электронов).
Рентгеновский аппарат является источником характеристического и тормозного излучения в широком диапазоне энергий (от 0,5 до 1000 кэВ). Они использованы для передач толстых стальных компонентов до 120-160 mm. Ускоритель электронов является источником высокоэнергетического тормозного излучения (до 35 МэВ). Они применяются для грохочения стальных изделий большой толщины более 450 мм. Эти ускорители являются одновременно источниками высокоэнергетического излучения 0 и потоками нейтронов. Радиоизотопы являются источниками рентгеновского, р-и y-лучей, нейтронных потоков и позитронов. Они используются для скрининга толщиной стальных изделий до 200 мм. Детектор ионизирующего излучения используется для обнаружения и регистрации изменения рентгеновского излучения и излучения y, нейтронов, позитронов, а-и Р-частиц.
Они делятся на группы: фото -, ионизационные, полупроводниковые, радиопрозрачные (сцинтилляционные, термоэмиссионные), зарядовые (эмиссионные), Черенковские детекторы, калориметрические и химические. Низкочувствительные калориметрические и химические детекторы в основном используются для измерения очень высоких доз ускорителей заряженных частиц, мощных установок облучения кобальтом и др. Одна тысяча четыреста одиннадцать Фотодетекторы (рентгеновские пленки)используются для регистрации излучений при рентгенографических осмотрах компонентов. Детекторы ионизирующего излучения включают ионизирующую камеру и газоразрядный счетчик (пропорциональный, Гейгера Мюллера, короны, искры).
Принцип работы этих детекторов основан на ионизирующем воздействии излучения на газ, а выходной сигнал ионизационного детектора может быть определен при воздействии излучения на газовую среду. Полупроводниковый детектор основан на явлении фотопроводимости, то есть на явлении генерации электрического тока в твердом теле под действием падающего на него излучения. Радиационно-эмиссионный (сцинтилляционный) детектор основан на фотостимулирующем воздействии излучения на некоторые вещества. Такими веществами являются люминофор или сцинтилляторы, которые преобразуют поглощенную энергию ионизирующего излучения в видимый свет. Контроль литой детали и изделия с помощью рентгеновской пленки или ксерорадиографической (или электрорадиографической) пластины с использованием рентгенографических методов для определения
качества подготовки отливки и деталей; качество сварки и паяного соединения деталей, герметизация передней кромки кабеля и гибкого шланга, внутренняя подрезка внутренней поверхности и полой части. разница, близкая В радиоспектральном (зрительно-радиационном) контроле-скрытое изображение передаваемого объекта в видимом свете, которое было изучено на экране ионизирующего излучения и преобразователя телевизионного приемника, и изображение передаваемого объекта.
Метод визуального излучения широко и эффективно применяется при контроле качества состояния узлов и механизмов без литья, сварки, пайки, сборки, а также их демонтажа. Радиометрический контроль заключается в измерении ослабления интенсивности пучка излучения, прошедшего через передаваемый объект. Сцинтилляционные, полупроводниковые, газоразрядные измерители или ионизационные камеры используются для измерения интенсивности пучка излучения за объектом. 142б стол. 3.7 приведены характеристики чувствительности наиболее распространенных методов обнаружения дефектов и их применимых объектов.
Смотрите также:
Характеристика основных фаз в сплавах | Статические испытания на растяжение |
Структура сплавов | Специальные методы испытаний |