Оглавление:
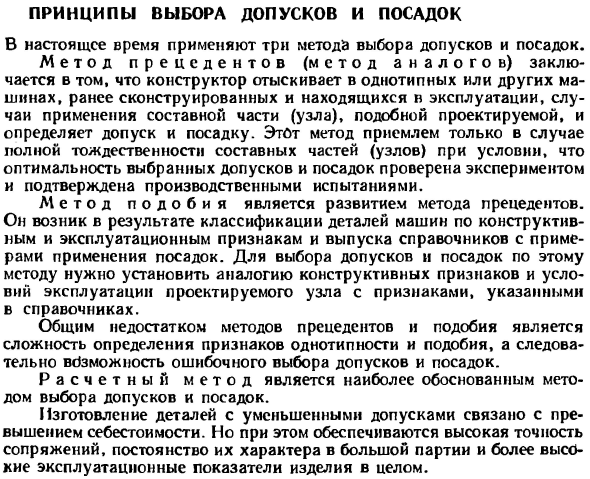
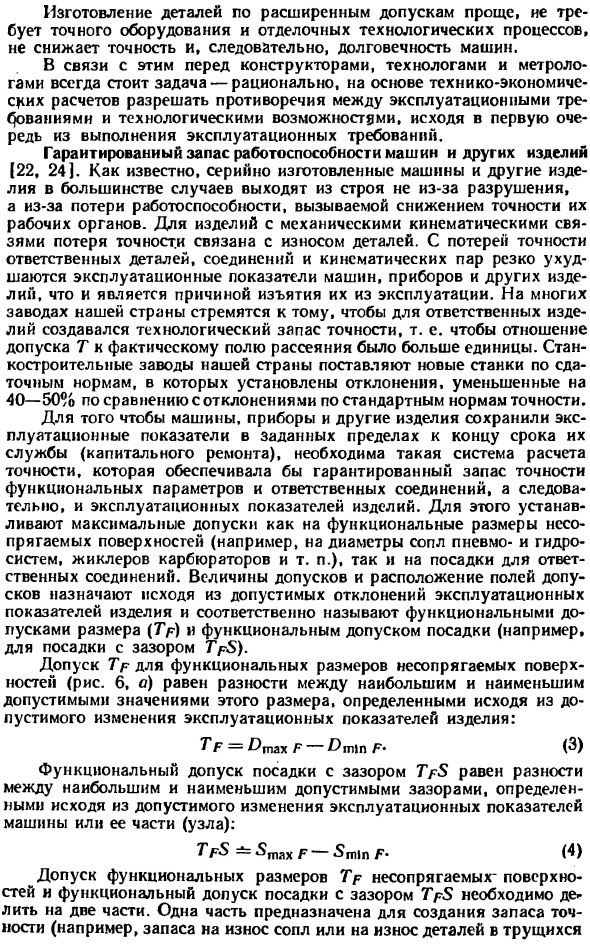
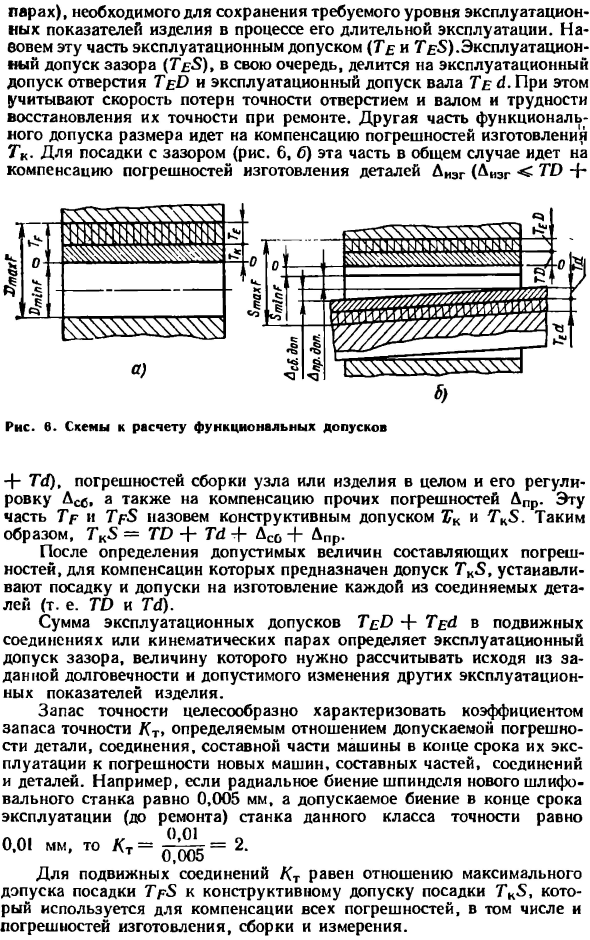
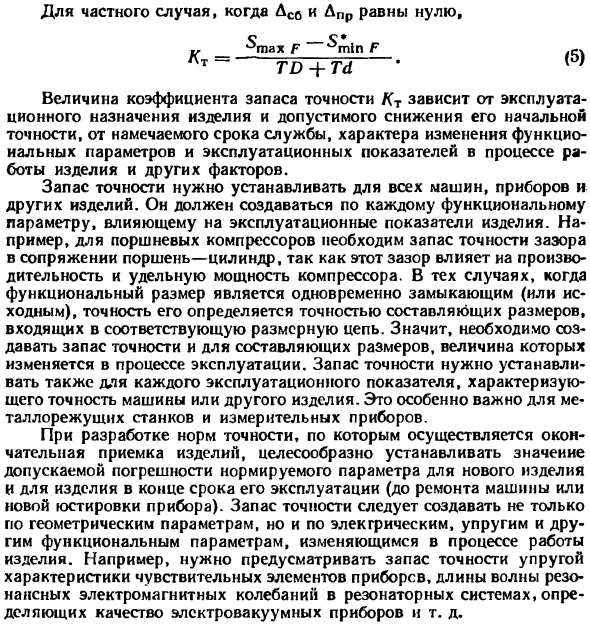

Принципы выбора допусков и посадок
- В настоящее время есть три способа выбора между терпимостью и посадкой. Метод варианта использования (аналоговый метод) позволяет разработчику искать использование компонентов (сборок), аналогичных тем, которые были сконструированы на том же типе или другой машине, которая была ранее спроектирована и работает, и определять допуски и посадку Состоит из того, что Этот метод приемлем только для полной идентификации компонентов (узлов), при условии, что выбранные допуски и оптимальность посадки проверяются экспериментами и подтверждаются производственными испытаниями.
Аналогичная модель — разработка методов использования. Это стало результатом классификации механических частей по конструктивным и эксплуатационным характеристикам и публикации справочника, содержащего примеры посадки. Для выбора допусков и посадок в соответствии с этим методом необходимо установить сходства в конструктивных функциях и условиях эксплуатации проектируемого агрегата, используя характеристики, приведенные в справочной информации.
Деление может продолжаться и дальше, но на самом деле оно должно было остановиться раньше на 254, так как длина круга измеряется в сантиметрах, а значение l округляется до трех цифр. Людмила Фирмаль
Общим недостатком метода прецедента и сходства является то, что трудно определить сходство и признаки сходства, а следовательно, возможность ошибки и неправильный выбор посадки. Метод расчета является наиболее разумным способом выбора допусков и посадок. Производство деталей с низкими допусками связано с перерасходом средств. Тем не менее, это обеспечивает высокоточное сопряжение, постоянство свойств в больших партиях и улучшение общих показателей производительности продукта.
Изготовление деталей с расширенными допусками проще, не требует точного оборудования или технических процессов отделки, не снижает точность и, следовательно, не снижает долговечность станка. В связи с этим проектировщики, инженеры и метрологи могут разумно разрешать конфликты между эксплуатационными требованиями и техническими возможностями, основываясь, главным образом, на технических и экономических расчетах, основанных, главным образом, на соблюдении эксплуатационных требований. Всегда сталкиваюсь с задачей сделать.
Гарантированная работоспособность машин и другой продукции 22, 24 . Как известно, в большинстве случаев станки серийного производства и другие изделия выходят из строя не из-за разрушения, а из-за того, что производительность ухудшается из-за сниженной точности обрабатываемой детали. Для изделий с механическим движением потеря точности связана с износом деталей. Потеря точности критических деталей, соединений и кинематических пар может значительно снизить производительность машин, устройств и других изделий. Вот почему он снят с эксплуатации.
Многие фабрики в Японии стремятся создать запасы критической точности для критически важных продуктов. Другими словами, допустимое отношение T к фактическому рассеянному полю превышает 1. Наш станкостроительный завод поставляет новые станки в соответствии с приемлемыми стандартами. С помощью этого критерия отклонение уменьшается на 40-50% по сравнению с отклонением в соответствии со стандартным стандартом точности.
Точность, которая обеспечивает станку, устройству и другим изделиям эксплуатационные параметры в критических пределах к концу их срока службы (капитального ремонта), функциональных параметров и критических соединений, таким образом гарантируя запасы точности производительности изделия Требуется система расчетов. По этой причине существуют максимальные допуски как на функциональные размеры нерасширяемой поверхности (например, диаметры сопел пневматической и гидравлической системы, форсунки карбюратора и т. Д.)
- Так и на критические места соединения. Поскольку значение допуска и положение поля допуска назначаются на основе отклонения индекса производительности продукта, они называются функциональным допуском размера (Tr) и функциональным допуском соответствия (например, соответствие с зазором Tr5). Допуск функционального размера Tp не сопрягаемой поверхности (рис. 6, o) равен разнице между максимальным и минимальным допустимыми значениями для этого размера и определяется на основе допустимого изменения эксплуатационных характеристик изделия.
Функциональный допуск для посадки в зазоре Tr8 равен разнице между максимальным и минимально допустимым зазором, который определяется на основе допустимого изменения рабочих характеристик машины или ее частей (узлов). — max max P — m n p. (4) Допуск функционального размера Tr для несопряженной * поверхности и функциональный допуск посадок с зазором Tr8 должен быть разделен на две части. Одна деталь предназначена для создания запаса точности (например, запас износа детали из-за износа сопла и трения) Pair), необходимого для поддержания требуемого уровня производительности продукта при длительной эксплуатации.
Свойство измерительной насадки заключается в том, что она служит для улучшения состояния измерения без непосредственного изменения диапазона измерений. Людмила Фирмаль
Эта часть называется эксплуатационным допуском (Te и Te5). Эксплуатационный допуск ( 7e) подразделяется на допуск на эксплуатацию скважины 7eO и допуск на эксплуатацию вала Te L. На ремонте. Другой частью функционального допуска к размеру является исправление ошибки изготовления T. При посадке с зазором (рис. 6, б) в общем случае эта деталь используется для компенсации производственных ошибок деталей LIeg (Lmzg TO + + 74), ошибка Dpr при сборке устройства или всего изделия и его настройке и др. Исправление ошибок. Эта часть Tp и 7p5 называется конструктивным допуском Tk и Tk5.
Следовательно, 7K5-TO + 74 + Dso + Dpr- Для компенсации, для которой предназначен допуск 7K5, производственные допуски и допуски для каждой подключенной детали устанавливаются (т. Е. 70 и 74) после определения допусков на ошибки компонентов. Общий рабочий допуск 7eO + 7e4 подвижного соединения или кинематической пары определяет рабочий допуск зазора. Значение зазора следует рассчитывать исходя из указанной долговечности и допустимых изменений других рабочих параметров изделия. Рекомендуется характеризовать запас точности с помощью коэффициента точности Kt, который определяется отношением допусков детали, соединения и срока службы детали машины к новой машине, детали, соединению и погрешности детали.
Например, новый шлифовальный станок имеет биение шпинделя 0,005 мм в радиальном направлении. Для подвижных соединений CT равен отношению максимального допуска на посадку Tr5 и конструктивного допуска на посадку 7K5 и используется для исправления всех ошибок, таких как ошибки изготовления, сборки и измерения. (5) В особом случае, когда Dsb и Dpr равны нулю, 5max G ~ 5m1n P 1 ~ th + m Величина коэффициента безопасности Kt зависит от цели эксплуатации и начальных допусков изделия, предполагаемого срока службы, характера изменений функциональных параметров и рабочих показателей во время эксплуатации изделия и других факторов. Точность должна быть установлена для всех машин, устройств и других продуктов.
Вы должны создать каждый функциональный параметр, который влияет на производительность продукта. Например, поршневые компрессоры требуют запаса точности в зазоре интерфейса поршень-цилиндр. Это связано с тем, что этот зазор влияет на производительность и удельную мощность компрессора. Если размер элемента является закрытым (или начальным) в то же время, его точность определяется точностью составляющих размеров в соответствующей размерной цепочке. Это означает, что вам нужно создать поле для точности размера компонента, которая изменяется во время работы.
Запас точности также должен быть установлен для каждого индикатора движения, который характеризует точность станка или другого продукта. Это особенно важно для станков и измерительной техники. Установление нормированных значений допусков параметров в конце нового продукта и в конце срока службы продукта (до ремонта машины или настройки нового устройства) при разработке стандарта точности, при котором происходит окончательная приемка продукта.
Пределы точности должны создаваться не только геометрическими параметрами, но также электрическими, упругими и другими функциональными параметрами, которые изменяются во время работы изделия. Например, необходимо обеспечить запас точности, такой как упругие свойства чувствительных элементов устройства и длина волны резонансной электромагнитной волны резонаторной системы, которая определяет качество электрического вакуумного устройства.
Смотрите также:
Решение задач по метрологии с примерами