Оглавление:
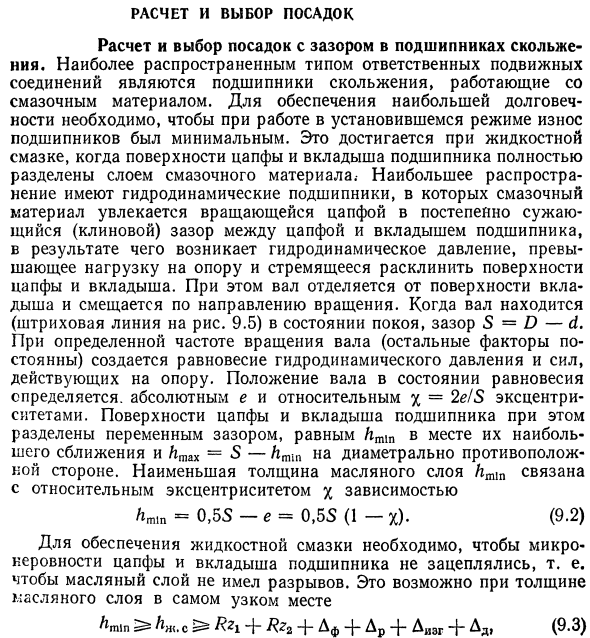
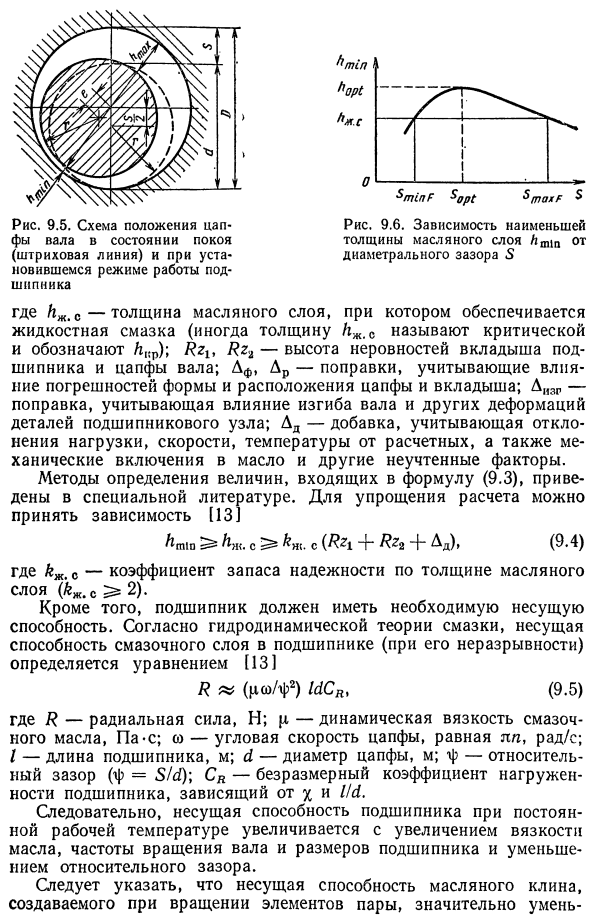
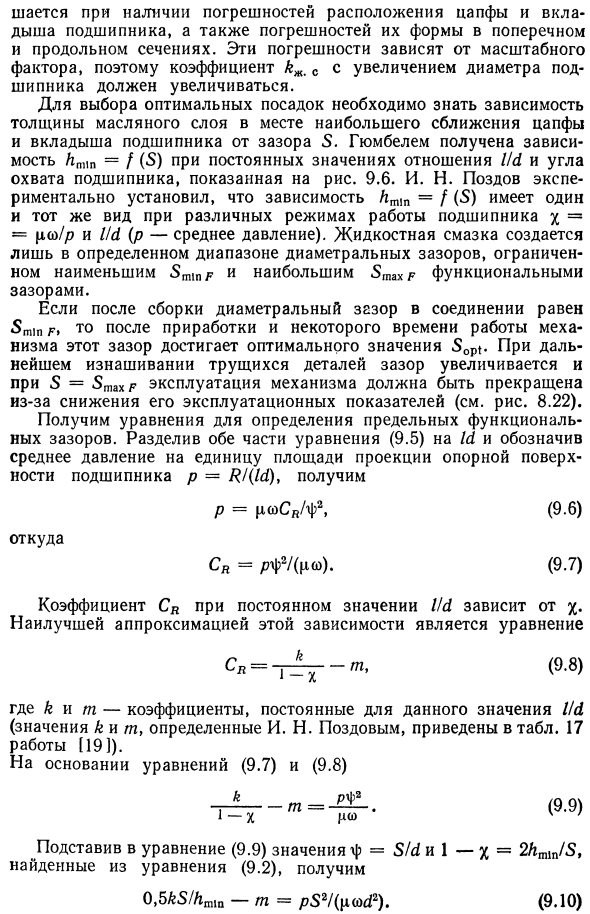
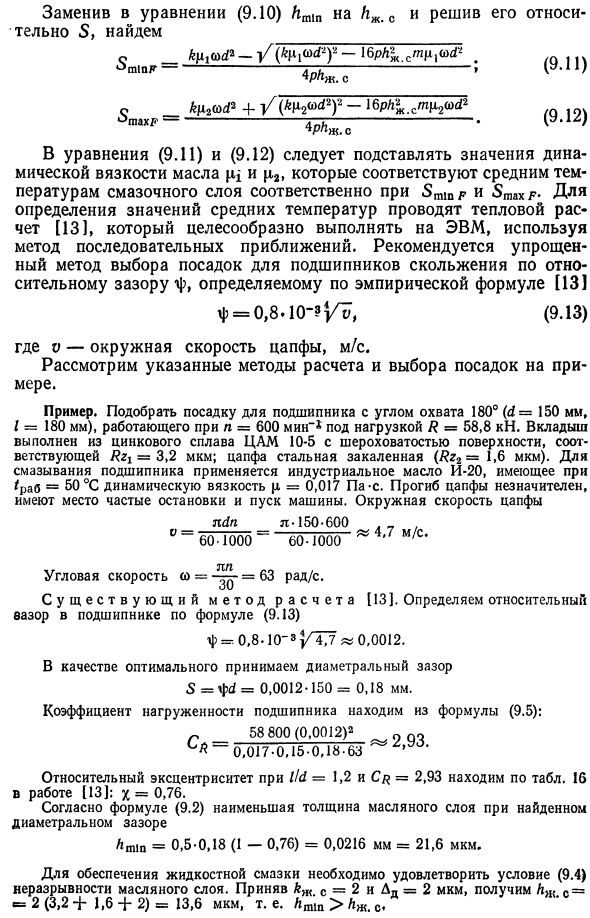
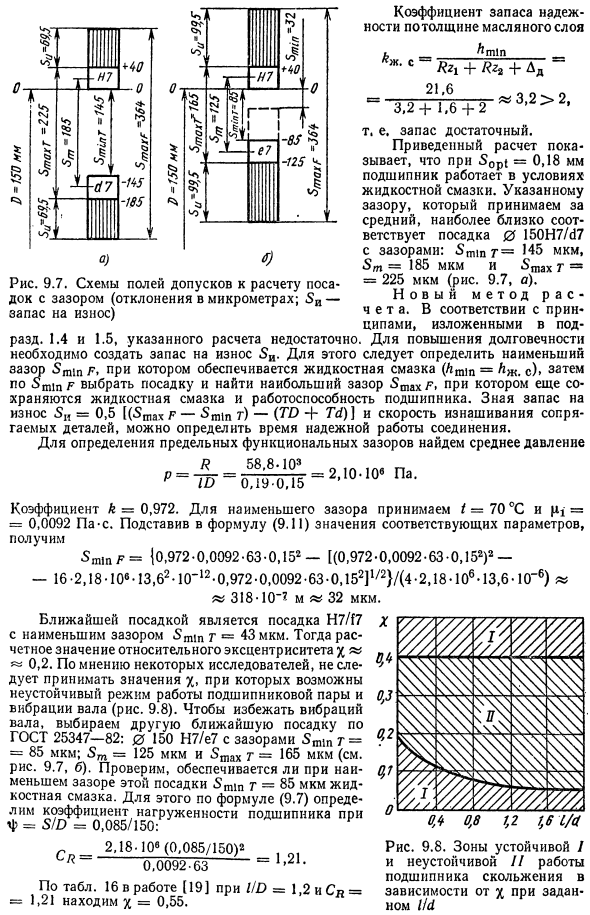
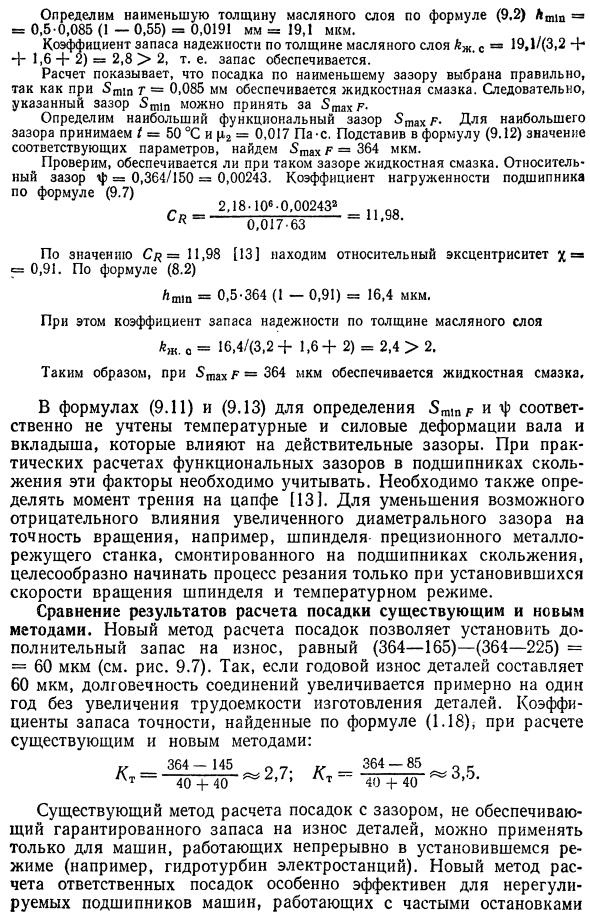
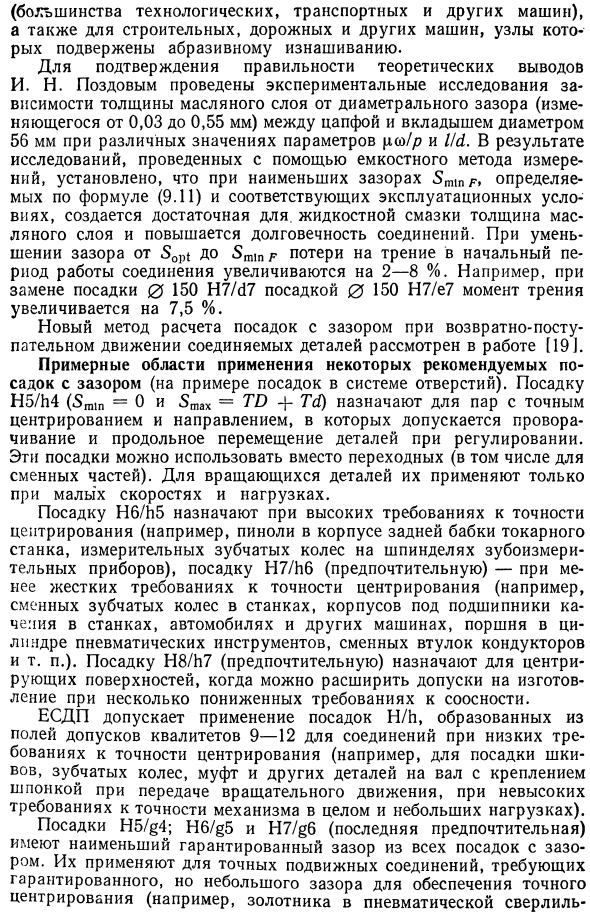
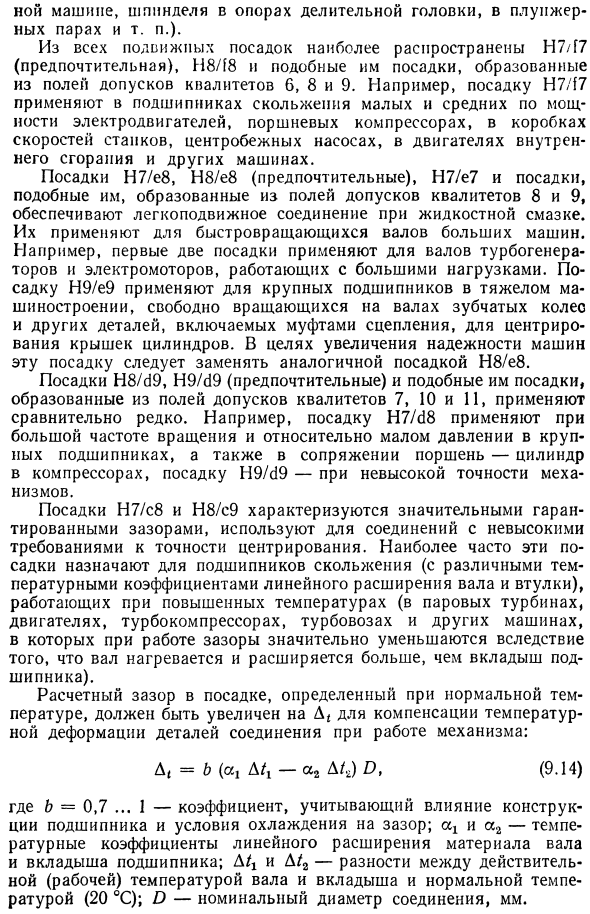
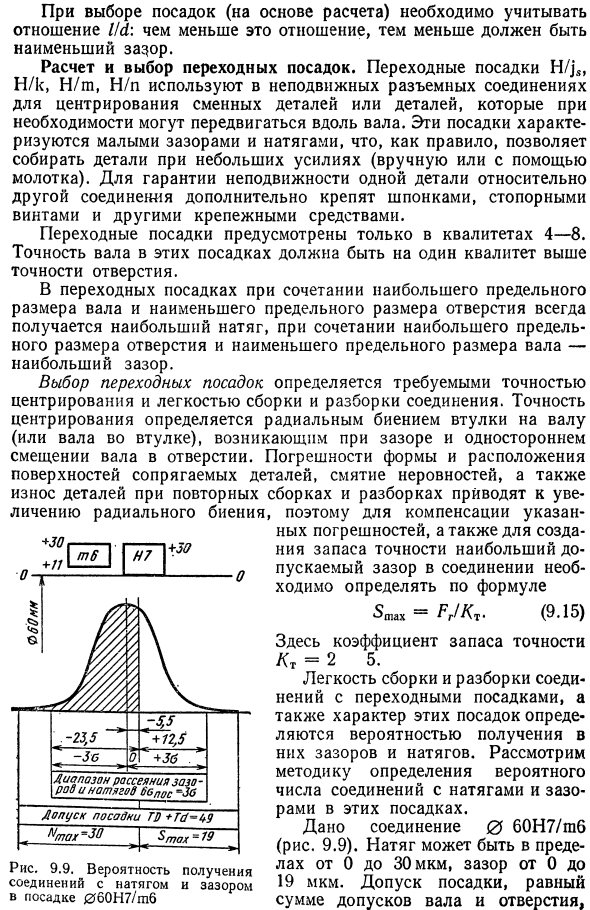
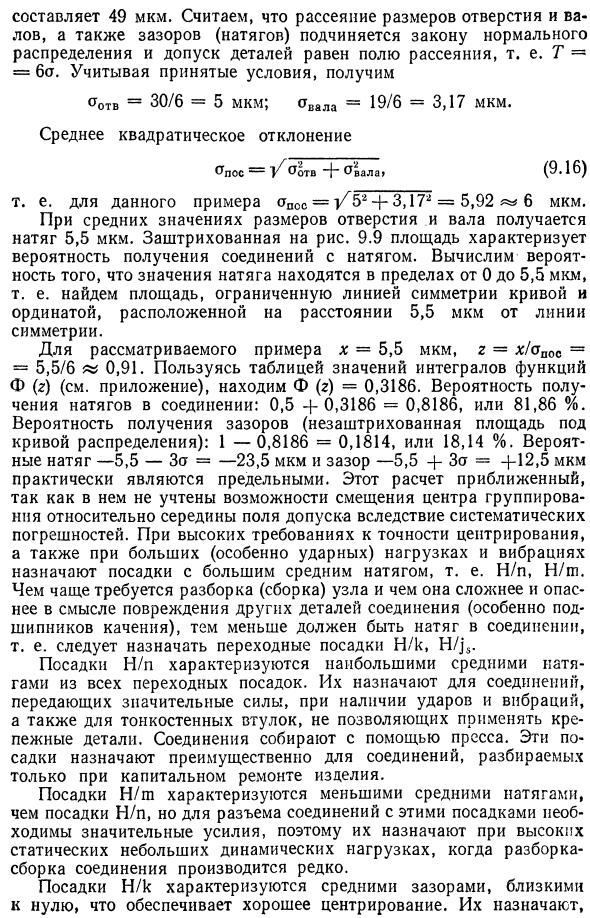
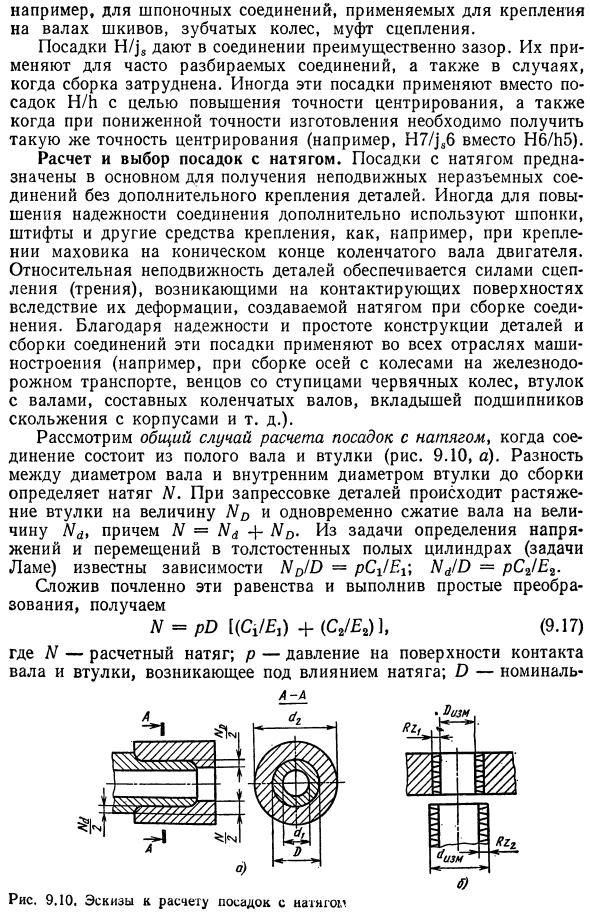
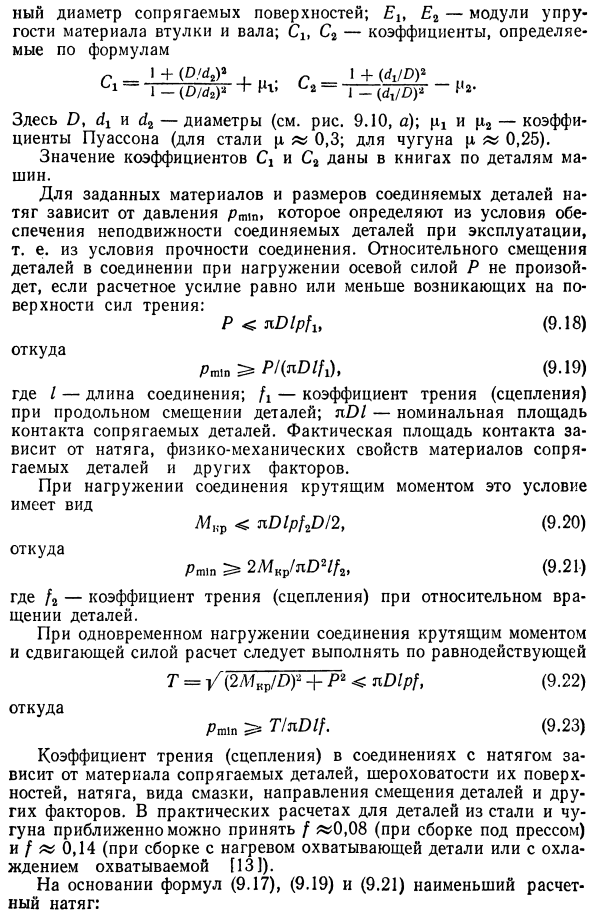
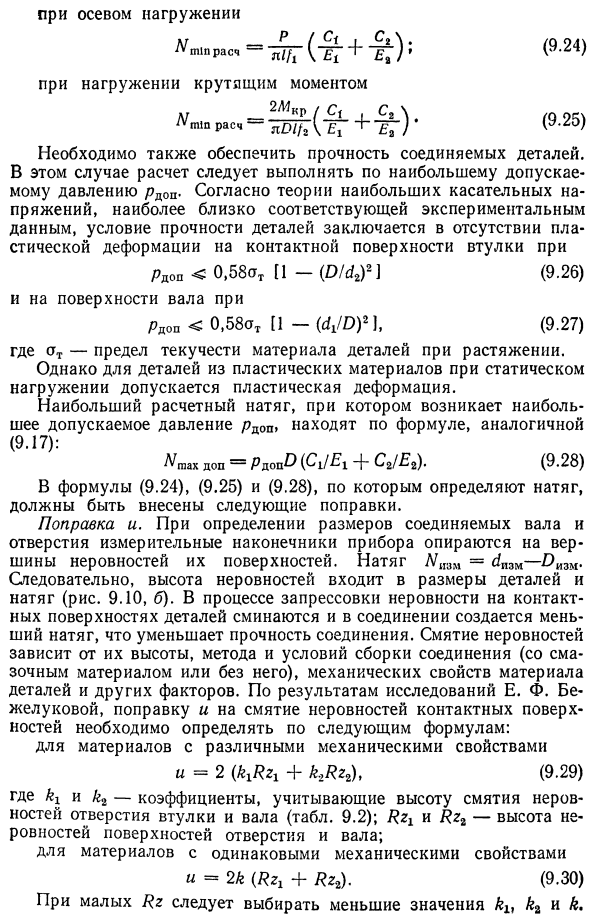
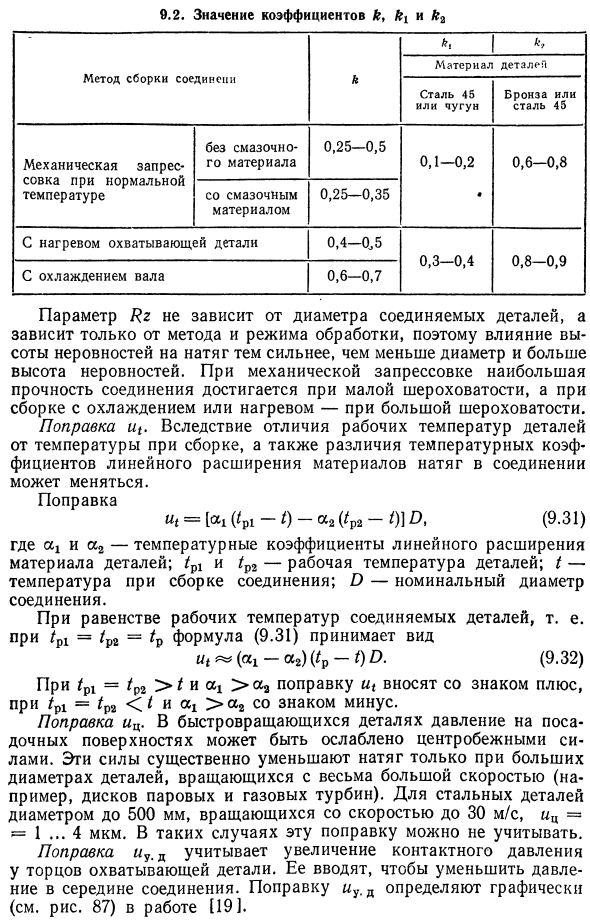
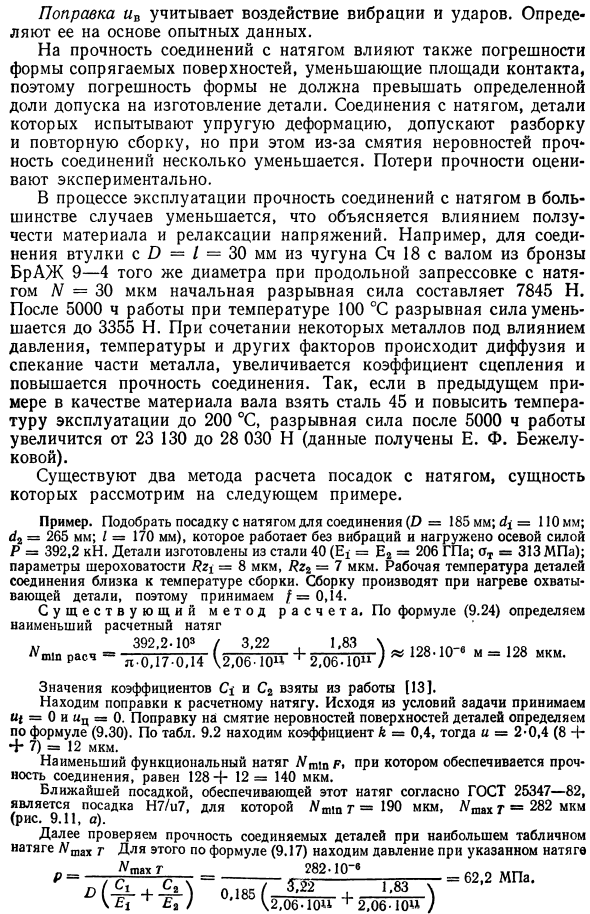
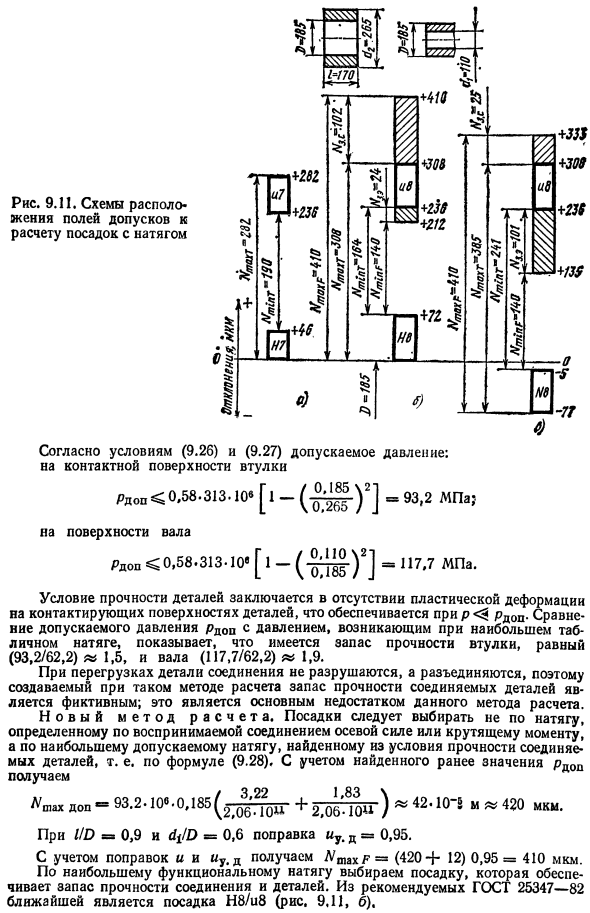
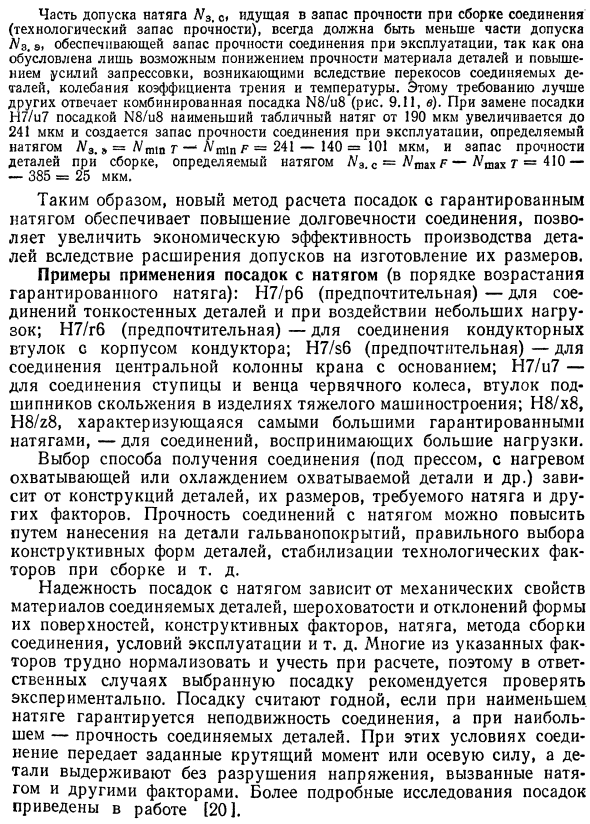

Расчет и выбор посадок
- Расчет и подбор посадочных мест с зазорами в подшипниках скольжения. Наиболее распространенный тип важного подвижного соединения — подшипник скольжения, работающий со смазкой. Для обеспечения максимальной долговечности износ подшипника должен быть сведен к минимуму при работе в устойчивом состоянии. Это достигается с помощью жидкой смазки, когда поверхности цапфы и корпуса подшипника полностью разделены слоем смазки.
Наиболее популярными являются гидродинамические подшипники, где смазочный материал переносится вращающимся штифтом в постепенно сужающийся (клиновой) зазор между штифтом и оболочкой подшипника, который стремится заклинить штифт и поверхность подшипника за пределы нагрузки на подшипник. Это становится гидродинамическим давлением. В этом случае вал отделяется от поверхности вкладыша и движется в направлении вращения. Когда вал неподвижен (пунктирная линия на рис. 9.5), зазор 3 = O-L. При определенной частоте вращения вала (другие факторы остаются постоянными) создается баланс гидродинамического давления и силы, действующей на опору.
Комплект принадлежностей включает в себя блок во время маркировки, с торцевыми средствами и двумя типами держателей для фиксации блоков, используемых для проверочных и маркировочных работ. Людмила Фирмаль
Положение вала в равновесии определяется абсолютным e и относительным x = 2e 8 эксцентриситетом. Поверхность цапфы и оболочки подшипника, чередующиеся с зазором равна позицией сближения, которые разделены на противоположной стороне направления диаметра Lmax = 5-Lmnn. Минимальная толщина масляного слоя НТ1п связана с зависимостью относительного эксцентриситета Ltn = 0,55-е = 0,55 (1-х). (9.2) Для обеспечения жидкой смазки неровности штифтов и корпус подшипника не должны соприкасаться. Другими словами, необходимо предотвратить повреждение слоя масла. Это возможно в точке, где толщина масляного слоя является самой узкой. Lt ls.s R1 + Ha + Df 4-D + DI8G + Dd (9,3) Рисунок 9.5.
Диаграмма положения шейки вала в стационарном (пунктирная линия) и стационарном состоянии Где Ls.s — толщина масляного слоя, где происходит жидкая смазка (толщина Ls.o называется критической и обозначается как L p). DGG-Шероховатость вкладыша подшипника и шейки вала Df, Dp — коррекция с учетом влияния ошибок формы и положения цапфы и вставки 2. — коррекция с учетом влияния изгибов вала и других деформаций узлов вала DD-расчет Присадки, которые учитывают нагрузку, скорость, отклонения температуры от того, что было сделано, и механические включения в масле и другие неизвестные факторы. Как определить количество, содержащееся в уравнении (9.3), описано в специальной литературе.
Зависимости могут быть приняты для упрощения расчетов 13 yt10 L , s * f. c ( r, + Я2 + + д), (9.4) Где kzh, 0-коэффициент запаса толщины слоя масла (с с 2). Кроме того, подшипник должен иметь необходимую несущую способность. Согласно гидродинамической теории смазки, несущая способность (с непрерывностью) слоя смазки подшипника определяется по уравнению 13 . K (pCO 2) 1aСн, (9,5) Где -Радиальная сила, Н; р-динамическая вязкость смазки, Па-с; w-осевая угловая скорость, равная ПП, рад с; длина подшипника I, м; диаметр 4 цапф, м; f-относительный зазор (f = 5 4); Cn — безразмерный коэффициент нагрузки на подшипник, который зависит от x и 4.
В результате, несущая способность подшипника при постоянной рабочей температуре увеличивается с увеличением вязкости масла, частоты вращения вала, размеров подшипника и уменьшением относительного зазора. Обратите внимание, что несущая способность масляного клина, создаваемого вращением сопряженных элементов, значительно снижается. Эту проблему можно устранить, если имеется ошибка в положении шейки и вкладыша подшипника, а также в форме поперечного сечения и вертикального сечения. Поскольку эти ошибки зависят от масштабного коэффициента, коэффициент kzh s увеличивается с увеличением диаметра подшипника.
Чтобы выбрать наилучшую посадку, необходимо знать зависимость толщины масляного слоя от зазора 5 в ближайшей точке цапфы и вкладыша подшипника. 9.6. И. Н. Поздовым экспериментально установлено, что зависимость ттщ (5) имеет одинаковый вид для разных режимов работы подшипника ыы и и 1 й (-среднее давление) , Жидкие смазки создаются только с определенным диапазоном зазоров по диаметру, ограниченным минимальным 5tf и максимальным 5tfr функциональным зазором.
После сборки диаметральный зазор соединения составляет 5 м pR, t После того, как механизм заработает после операции, когда этот зазор достигнет оптимального значения Zory, при дальнейшем износе фрикционной части зазор также будет 5 = Ztm Увеличение в Работа механизма должна быть остановлена, потому что он снижает производительность (см. Рисунок 8.22). Получите уравнение, определяющее ограниченный функциональный зазор. Уравнения, разделенные по обе стороны от го (9.5), проекция р = С (1-е) от опорной поверхности подшипника, что указывает среднее давление на единицу площади, p = r.hSya f2, (9,6) Откуда Cn = pf2 (p-
Коэффициент C с постоянным значением 1 th зависит от следующей формулы: Зв = -g4g-т, (9,8) Где k и t — постоянные коэффициенты для определенного значения Oi (значения китов, определенные И. Н. Поздовым, показаны в таблице 17 (191). На основании уравнений (9.7) и (9.8) Подставляя значение = 8-й и 1-% = 2Lt1n 5 в уравнение (9.9) и вычисляя из уравнения (9.2), 0,5×5 Lt1o-m = p32 (n2), (9,10) Подстановка е в формуле (9.10) и ясно 5 e k ^ aiR- (krp
В уравнениях (9.11) и (9.12) необходимо заменить значения кинематической вязкости масел u и u, соответствующие средним температурам смазочных слоев 5 gatR и 8 mpr, соответственно. Тепловой расчет выполняется для определения среднего значения температуры 131. Лучше всего это сделать на компьютере, используя метод последовательного приближения. Эмпирическая формула 131 f = 0,8,10- В упрощенном методе рекомендуется выбирать посадку подшипника скольжения в соответствии с относительным зазором f, определяемым <(9.13) Где V — скорость оси, м с. Рассмотрим эти методы расчета и варианты посадки в качестве примеров. Пример.
Выберите тот, который подходит для подшипников с углом охвата 180 ° (d = 150 мм, I = 180 мм), работающих при n = 600 мин. *. * Под нагрузкой I = 58,8 кН. 2g2 = 3,2 Совместим с закаленным стальным штифтом (2g2 = 1,6 мкм), смазывающим подшипник индустриальным маслом I-20, динамическая вязкость p = 0,017 Па с при ведомом = 50 ° C. Не часто останавливаться и заводить машину. ПЛП И-150-600, 0 60-1000 60-1000 I 4.7 S Угловая скорость
Определите относительный зазор подшипника в соответствии с уравнением (9.13). f = 0,8-10 4 0,0012. Возьмите зазор диаметра как оптимальный 5 = fi = 0,0012-150 = 0,18 мм. Коэффициент нагрузки на подшипник можно получить из уравнения (9.5): 58800 (0,0012) ~ 0,017-0,15-0,18-63 Относительный эксцентриситет при 1 4 = 1,2 и Cp = 2,93 приведен в таблице. 13 16: х = 0,76. Согласно уравнению (9.2) минимальная толщина слоя масла при зазоре найденного диаметра LSP = 0,5-0,18 (1-0,76) = 0,0216 мм = 21,6 мкм Чтобы обеспечить смазку жидкости, должно быть соблюдено условие непрерывности масляного слоя (9.4). Принимая ql c = 2 и Dn = 2 мкм, получаем Ls c = 2 (3,2 + 1,6 + 2) = 13,6 мкм, т. Е. Лш1о> Лж.
Фактором безопасности, безусловно, является толщина слоя масла Вышеприведенных расчетов достаточно, чтобы рассчитать, что при Op1 = 0,18 мм подшипник будет работать в условиях жидкой смазки. Указанный зазор принят за среднее значение и наиболее тесно коррелирует с 0150Н7 67 = 145 мкм, 5maxТ = ^ метод ras-. Согласно принципам, описанным в подразделе. В 1.4 и 1.5 указанного расчета недостаточно. Чтобы увеличить долговечность, нужно создать запас на износ 5I.
Для этого определите минимальный зазор 5t P d, при котором обеспечивается жидкая смазка (LS P = Lzh, с), выберите посадку в соответствии с Oscch d, а также максимальный уровень, при котором все еще сохраняются характеристики жидкой смазки и подшипника. Найти клиренс 5шаад. 8I = 0,5 (5max p-5t Pm) — (TO +) и скорость износа для определения предела износа Вы можете определить надежное время работы деталей и соединений.
Найти среднее давление, чтобы определить пределы функционального зазора Коэффициент k = 0,972. Для наименьшего зазора принять = 70 ° C и u = = 0,0092 Па-с. Подставляя значение параметра, соответствующего уравнению (9.11), 5ttd = 10,972 0,0092-63-0,152 — (0,972-0,0092-63-0,15a) g- -16-2.18-10 -13.6g-10 12-0.972-0.0092-63-0.152 1 2 (4-2.18-106-13.6-10 6) 318-10-1 m Нет 32 мкм. Минимальная толщина слоя масла определяется по уравнению (9.2). Лш п = = 0,5-0,085 (1-0,55) = 0,0191 мм = 19,1 мкм. 19,1 (3,2 + + 1,6 + 2) = 2,8> Коэффициент запаса толщины масляного слоя kzh равен 2, т. Е. Запасной предусмотрен.
Поскольку 5 м м = 0,085 мм обеспечивает жидкую смазку, расчет показывает, что посадка с минимальным зазором выбрана правильно. Следовательно, указанный разрыв 5tsc можно считать 5tehr. Определим максимальный функциональный разрыв 5шахр. При наибольшем зазоре I = 50 ° C, поиск = 0,017 Па-с. Подстановка соответствующего значения параметра в уравнение (9.12) дает 5piX e = 364 мкм. Убедитесь, что этот зазор обеспечивает зазор жидкости. Относительный зазор f = 0,364 150 = 0,00243. Коэффициент нагрузки на подшипник на основе уравнения (9.7) О 1P.POLCH2 Южная Каролина Значение 13 для Cs = 11,98 дает относительный эксцентриситет x = 0,91. Согласно формуле (8.2) > SHP = 0,5-364 (1-0,91) = 16,4 мкм.
Коэффициент запаса толщины масляного слоя * Wo = 16,4 (3,2 + 1,6 + 2) = 2,4> 2. Следовательно, обеспечивается 5 га хл = 364 микрон жидкой смазки. Уравнения (9.11) и (9.13), которые определяют Zr1pR и , не учитывают температуры вала и гильзы и деформации силы, которые влияют на фактический зазор, соответственно. Эти факторы должны учитываться при фактическом расчете функционального зазора подшипника скольжения. Также необходимо определить момент трения штифта 131.
Например, чтобы уменьшить негативное влияние увеличенного зазора в диаметре на точность вращения шпиндельных прецизионных металлорежущих станков, установленных на подшипниках скольжения, при установившейся скорости вращения шпинделя и температурных условиях Рекомендуется начинать только процесс резки. Сравнение результатов расчета посадки с существующими и новыми методами. С новым методом расчета посадки может быть установлен дополнительный запас износа, равный (364-165) — (364-225) = 60 мкм (см. Рисунок 9.7). Следовательно, если годовой износ детали составляет 60 мкм, долговечность соединения увеличится примерно на один год без увеличения сложности изготовления детали.
Точность запаса находится в уравнении (1.18), при расчете существующих и новых методов: 364-145 40 + 40 ~ 2 7 Существующий метод расчета посадок с зазорами, которые не обеспечивают гарантированного запаса на частичный износ, может использоваться только для машин, которые работают непрерывно в устойчивом состоянии (например, турбины электростанции). Новый метод расчета критических посадок особенно эффективен для нерегулируемых подшипников на часто останавливаемых машинах. Для большинства технологий, транспорта и другой техники, а также строительной, дорожной и другой техники эти детали подвержены износу. Я подтверждаю обоснованность теоретического заключения. Н.
Поздоф провел экспериментальное исследование зависимости толщины нефтяного слоя от различных параметров ts p и зазора диаметра между цапфой IL и вкладышем диаметром 56 мм (изменен с 0,03 до 0,55 мм). Это было Исследования, проведенные с использованием емкостных измерений, показали, что минимальный зазор 5t1pL, определенный по уравнению (9.11), и соответствующие рабочие условия являются достаточными. Улучшенная толщина слоя жидкой смазки и долговечность швов. Уменьшенный зазор с ZoR Начальные потери на трение в комбинированном режиме увеличиваются на 2-8% до 5 тонн. Например, замена посадки 0 150 N7 D7 на посадку 0 150 N7 e7 увеличивает момент трения на 7,5%.
Новый способ расчета зияющих посадок при возвратно-поступательном соединении деталей (191. Рекомендуемое совместное покрытие с зазорами (приблизительная посадка лунок). Посадка Н5 И4 (5шш = 0 и Зпмх = ТО + Т б ) Назначается паре с точным центрированием и ориентацией, что позволяет регулировать вращение и продольное перемещение детали. Эти посадочные площадки могут использоваться вместо переходных посадочных площадок (включая сменные части). Для вращающихся деталей он используется только на низких скоростях и при низких нагрузках.
Посадка H6 L5, высокие требования к точности центрирования (например, штифт для задней бабки токарного станка, измерение передачи шпинделя измерительного механизма), посадка H7 L6 (рекомендуется) — строгие требования к точности центровки (замена) Возможно) и т. Д. Предназначены для зубчатых колес машин, корпусов подшипников качения машин, автомобилей и других машин, поршней цилиндров пневматических инструментов, сменных втулок проводников и т. Д.). Посадка H8 J7 (рекомендуется) указывается для центрирования поверхности, если требования к выравниванию можно немного уменьшить для увеличения производственных допусков.
ESDP использует соединения H L, сформированные из 9-12 полей допусков, соединения с низкими требованиями к точности центровки (например, шкивы, зубчатые колеса, муфты с фиксированными ключами при передаче вращательного движения, А при креплении других частей к валу) можно использовать весь механизм точности и требования к малой нагрузке). Посадки H5 §4; H6 §5 и H7 §6 (последняя рекомендованная) гарантируют минимальный зазор между всеми посадками с зазором. Они используются для точных подвижных соединений, которые гарантируют точное центрирование, но требуют небольших зазоров (например, катушки с пневматическим сверлом) Станок, шпиндель, шпиндельная пара и т. Д.).
Из всех мобильных посадок наиболее распространенными являются H7 17 (рекомендуется), H8 18 и аналогичные посадочные площадки, сформированные из квалификационных 6, 8 и 9 полей допуска. Например, посадка H7 17 используется в электродвигателях малой и средней мощности, поршневых подшипниках скольжения, таких как компрессоры, механические коробки передач, центробежные насосы, двигатели внутреннего сгорания. Посадка из H7 e8, H8 e8 (рекомендуется), H7 e7 и аналогичных посадок, поля допусков квалификации 8 и 9 обеспечивают жидкую смазку и легко перемещаемые соединения. Используется для высокоскоростных вращающихся валов больших машин.
Например, первые две посадочные площадки используются для турбогенераторов и валов электродвигателей, работающих под большими нагрузками. Посадка H9 e9 используется для больших подшипников в тяжелой технике и центрирует крышку цилиндра, свободно вращая вал шестерни и другие детали, содержащиеся в сцеплении. Для повышения надежности машины эту посадку следует заменить на аналогичную посадку на H8 e8. Подобные приземления, сформированные из посадок H8 89, H9 <19 (рекомендуется) и полей допуска 7, 10 и 11, используются относительно редко.
Например, посадка Н7 88 используется на высоких скоростях и относительно низких давлениях в больших подшипниках, а посадка Н9 <19 — механизмы низкой точности в фитингах поршневых цилиндров компрессора. Посадки N7 s8 и H8 s9 характеризуются важным гарантийным зазором, используемым для соединений с низкими требованиями к точности центра. В большинстве случаев эти фитинги предназначены для подшипников скольжения, которые работают при высоких температурах (различные температурные коэффициенты для линейного расширения вала и втулки) (для паровых турбин, двигателей, турбокомпрессоров, турбовозов и валов).
На других машинах, где зазор при движении значительно уменьшается) он будет нагреваться и расширяться больше, чем вкладыш подшипника). Расчетный посадочный клиренс, определенный при нормальной температуре, должен быть увеличен на D (чтобы компенсировать температурные искажения соединительных деталей при работе механизма: (9,14) Где b = 0,7 … 1 — коэффициент, учитывающий влияние конструкции подшипника и условий охлаждения на зазор. а и а2 — температурные коэффициенты линейного расширения материала вала и вкладыша подшипника. Разница между фактической (рабочей) температурой и нормальной температурой (20 ° C) D , а также D 2-вал и вкладыш. Номинальный диаметр О-соединения, мм.
Переходные фитинги N N c, N gp, N p используются в фиксированных разъемных соединениях для центрирования сменных деталей или деталей, которые могут перемещаться вдоль вала по мере необходимости Эти посадочные площадки характеризуются небольшими зазорами и жесткостью, что, в принципе, позволяет собирать детали вручную (вручную или с помощью молотка), чтобы одна часть не двигалась относительно другого соединения. Для этого закрепите его при помощи дюбелей, крепежных винтов или других крепежных средств. Переходные посадки предлагаются только в 4-8 классах.
Точность этих посадочных валов должна быть на одно качество выше точности отверстий. В переходной посадке максимальный размер помех всегда является комбинацией максимального предельного размера вала и минимального предельного размера отверстия, а максимальный размер отверстия и минимальный предельный размер вала являются комбинацией максимального зазора. Выбор промежуточной посадки зависит от требуемой точности центрирования, а также от простоты сборки и разборки соединения. Точность центровки определяется радиальным отклонением втулки вала (или вала внутри втулки). Это происходит, когда в отверстии происходит зазор вала и одностороннее смещение.
Ошибки формы поверхности и положения сопряженных деталей, неровности и износ деталей при повторной сборке и разборке приводят к увеличению радиального биения. Поэтому, чтобы исправить эти ошибки и создать запас точности, необходимо определить максимально допустимый разрыв в формуле Zshah = P, Kt. (9.15) где запас точности равен KT = 22. Легкость, с которой соединения могут быть собраны и разобраны с использованием переходных фитингов, и характер этих посадочных площадок определяются возможностью зазора и помех. Рассмотрим методологию определения количества стыков, которые могут иметь помехи и клиренс на этих посадках. Приведено соединение 060Н7 т6 (рис. 9.9).
- Помехи колеблются от 0 до ZOкмкм, а зазор составляет от 0 до 19 микрон. Допуск на посадку равен сумме допусков на вал и отверстие, .U. 06ON7 t6 ° M не вероятность -23,5 -55 -Zs +30. ^ ро ^ и интерференция 49 мкм. Размеры отверстий и стержней, а также рассеяние (интерференция) следуют закону нормального распределения, и допуск компонента считается равным полю рассеяния, T = 6a. Учитывая принятые условия, aotv = 30 6 = 5 мкм; Avala = 19 6 = 3,17 мкм. Стандартное отклонение aaos = <4d.
То есть в этом примере apoo = y5a4 3,172 = 5,92 i 6 мкм. При среднем отверстии и размере вала достигается интерференционная посадка 5,5 микрон. Заштрихованная область 9,9 на рисунке характеризует вероятность получения мешающих соединений. Вычисляет вероятность того, что значение помехи находится в диапазоне от 0 до 5,5 мкм. Другими словами, найдите область, окруженную симметричной линией кривой. о, и ордината, на расстоянии 5,5 микрон от линии симметрии. В рассматриваемом примере x = 5,5 мкм, g = x apos = = 5,5 6 0,91. Использование таблицы значений интеграции функций (a) (см.
Измерение относительного угла поворота проверяемого и модельного колес осуществляется в приборах комплексного однопрофильного контроля. Людмила Фирмаль
Приложение), (r) = 0,3186 Найти вероятность получения помех на соединении: 0,5 4-0,3186 = 0,8186 или 81,86% Вероятность разрыва (свободное пространство под кривой распределения): 1-0,8186 = 0,1814, т. Е. 18,14%. Это 5,5-Za = 23,5 мкм, а зазор 5,5 4 Za = 4 12,5 мкм, и этот расчет сгруппирован по центру поля допуска из-за систематических ошибок. Приблизительно потому, что центр не учитывает возможность смещения из-за высоких требований к точности центрирования и больших (особенно ударных) нагрузок и вибраций, посадка определяется большими средними помехами, т.е.
Сборка часто требует разборки (сборки) и других частей соединения (особенно прокатки) Если более сложные и опасные в том смысле, что повреждение принимающий), плотность меньше, необходимое для подключения. То есть, он должен назначить переходное сопрягаемой N C, то N 5. Посадка н д характеризуется наибольшим средним уровнем помех от всех переходных посадок. Они предназначены для соединений, которые передают большие усилия при наличии ударов и вибраций, а также для тонкостенных втулок, которые не позволяют использовать крепежные элементы. Состав собирается с помощью пресса.
Эти насаждения предназначены в первую очередь для соединений, которые разлагаются только во время ремонта продукта. Посадка н т характеризуется более низкой средней герметичностью, чем посадка н п, но для разрыва связи с этими посадками требуется значительное усилие. Поэтому, когда разборка соединений выполняется редко, это указывается для высоких статических и малых динамических нагрузок. Посадка н д характеризуется средним зазором, близким к нулю, что обеспечивает хорошее центрирование. Они назначены. Например, для шарнирных соединений используются для установки шкивов, зубчатых колес и сцеплений на валах. Посадка N 8 дает в основном совместный клиренс.
Рабочие места, которые часто разбираются Используется для установки или когда сборка затруднена. Иногда эти приземления используются вместо посадок N N для повышения точности центрирования. Кроме того, если вы снижаете точность изготовления, вам необходимо получить такую же точность центрирования (например, H7 a6 вместо H6 H5). Расчет и отбор помех.
Посадка с натягом в первую очередь предназначена для создания фиксированного постоянного соединения без необходимости дополнительной фиксации деталей. Для повышения надежности соединения могут дополнительно использоваться дюбели, штифты и другие крепежные средства, например, когда маховик прикреплен к коническому концу коленчатого вала двигателя. Относительная неподвижность деталей обеспечивается силой сцепления (трением), возникающей на поверхности контакта из-за деформации, вызванной посадкой с натягом во время сборки соединения.
Из-за надежности и простоты конструкции деталей и сборки соединений эти площадки используются во всех отраслях машиностроения (например, оси с колесами, коронки со ступицами червячных колес, втулки с валами, Составной коленчатый вал, вкладыш подшипника с подшипником и т. Д.). д. ). Рассмотрим общий случай расчета посадки с натягом, когда соединение состоит из полого вала и втулки (рис. 9.10, а). Разница между диаметром вала и внутренним диаметром втулки перед сборкой определяет интерференцию N. Когда деталь вдавливается, втулка растягивается на определенную величину, и в то же время вал сжимается на величину N4, N = N4 + N0.
Зависимость A ^ o P = pC ^ E ^, = pCr1Eg известна из задачи определения напряжения и смещения толстостенного полого цилиндра (проблема Хромого). Если вы добавите эти уравнения для каждого члена и выполните простое преобразование: N = pB (C ^ Eu) + (C ± E2) , (9.17) N — рассчитанная помеха. p — давление на поверхности контакта между валом и втулкой, вызванное помехами. О- номинальная <9 Рисунок 9.10. Эскиз для расчета посадки с натягом Диаметр сопрягаемой поверхности; E и Eg — модуль упругости муфты и материала вала. C1, Cg-коэффициент, определяемый по уравнению д 1 + 04 оп I + (R.
Коэффициенты Пуассона ( 0.3 для стали и 0.25 для чугуна). Коэффициенты C и Ca являются Для размера детали, соединяемой с данным материалом, интерференция зависит от давления rt n. Это определяется неподвижным состоянием деталей, соединенных во время работы, то есть прочностью соединения. Если расчетная сила меньше, чем сила трения, создаваемая на поверхности, относительное смещение соединительных деталей при приложении нагрузки с осевой силой P не произойдет. P > P (ny1 ^, (9.19) Где я длина связи. D — коэффициент трения (сила сцепления) с продольным смещением детали. pi1 — номинальная площадь контакта сопрягаемой части.
На практике площадь контакта зависит от посадки с натягом, физических и механических свойств материала сопрягаемой детали и других факторов. Когда крутящий момент приложен к соединению, это состояние будет иметь вид Mkr 2Mcr 10%, (9,21) Где г — коэффициент трения (сцепления) с относительным вращением детали. Для одновременной нагрузки соединений с крутящим моментом и усилиями сдвига, расчет должен быть выполнен с результатами T = f (2L1vr P) a + P2 nE1r , (9.22) Откуда Рппп> Т1яОЦ.
Коэффициент трения (прочность сцепления) зажимного соединения зависит от материала сопрягаемой детали, шероховатости поверхности, посадки с натягом, типа смазки, направления смещения детали и других факторов. В реальных расчетах для деталей, изготовленных из стали и чугуна, приблизительно 0,0 0,08 (при сборке под прессом) и 0,1 0,14 (при нагреве с помощью части крышки или охлаждаемой части с крышкой) 13 ) возможно. Расчетная минимальная посадка по помехам основана на уравнениях (9.17), (9.19) и (9.21): Под осевой нагрузкой LGtShras, (9,24) При подаче крутящего момента <9 23> Также необходимо обеспечить прочность соединяемых деталей.
В этом случае расчет должен выполняться при максимально допустимом давлении rDOP. В соответствии с теорией наибольшего касательного напряжения, наиболее близкой к экспериментальным данным, условие прочности детали составляет 1- (O d2) 2 (9,26) и rdp <0,58, и на контактной поверхности втулки отсутствует пластическая деформация. это. На поверхности вала rdoa <0,58 ат 1 — (^ O) 2 , (9,27) at — предел текучести материала компонента при растяжении. Тем не менее, пластическая деформация допускается для деталей, изготовленных из пластика при статической нагрузке.
Максимальная расчетная герметичность, при которой создается максимально допустимое давление p 0P, может быть рассчитана по уравнению (9.17). Pop = RdO (ZD + Cr Er). (9,28) Следующие модификации должны быть сделаны в уравнениях (9.24), (9.25) и (9.28), которые определяют подгонку помех: С исправлениями. При определении размеров соединяемого вала и отверстия измерительный наконечник прибора опирается на неровности верхней поверхности. Preload — Oism. Поэтому высота неровностей включена в размеры детали и помехи (рис. 9.10, б).
В процессе запрессовки неровности контактной поверхности деталей измельчаются, адгезия соединительной части уменьшается, а прочность соединительной части уменьшается. Сглаживание неровностей зависит от его высоты, способа соединения и условий сборки (со смазкой или без), механических свойств материала детали и других факторов. По результатам исследований Е.Ф. Бежелуковой, коррекция и дробление шероховатости контактной поверхности должны определяться по следующей формуле: Для материалов с различными механическими свойствами u = 2 (k ^ + k2Kr), (9,29) Здесь кг и кг — коэффициенты, учитывающие высоту шлифования втулки и шероховатости отверстия вала (таблица 9.2).
Высота шероховатости поверхности отверстия и вала. Для материалов с одинаковыми механическими свойствами u = 2k (Kr1 + Pr *). (9,30) Если n мало, вам нужно выбрать маленькие значения для k1, k2 и k. 9.2. Значения коэффициентов k, k1 и ka Чем сильнее мешающие ячеистые неровности, тем меньше диаметр неровности и тем выше высота неровности.
В механическом прессе максимальная прочность соединения достигается при небольшой шероховатости, а при сборке с охлаждением или нагревом — при большой шероховатости. Коррекция и (. Совместные помехи могут различаться из-за различий в температуре сборки и рабочей температуры компонентов, а также различий в температурном коэффициенте линейного расширения материала. коррекция <= 1 (<Р1-О- в ( рв-010. (9.31) Где SC и Oz — температурные коэффициенты линейного расширения материала компонента. 0с а п -Частота использования, I — температура при сборке соединения. O — номинальный диаметр соединения.
Если рабочие температуры соединяемых деталей равны, то есть p1 = p2 = p, уравнение (9.31) принимает вид u ( x-a2) KR-0 O. (9.32) Если p1 = pz> 1 и 1> , модификация u начинается со знака плюс, а 0> 1 = p> a8 начинается со знака минус. Для деталей с быстрым корректирующим движением давление на посадочную поверхность может быть уменьшено центробежной силой. Эти силы значительно уменьшают посадку с натягом только для деталей большого диаметра, которые вращаются с очень высокой скоростью (например, диски паровой и газовой турбины). Для стальных деталей диаметром до 500 мм вращайте со скоростью до 30 м с, ui = 1 … 4 мкм. В таких случаях это исправление может не учитываться.
Поправки u7, q учитывают увеличение контактного давления на конце охватывающей части. Введено для понижения давления в центре сустава. Поправка u7a определяется графически в 19 (см. Рис. 87). Компенсация ивы учитывает влияние вибрации и ударов. Определяется на основе экспериментальных данных. На прочность посадки с натягом также влияет ошибка формы сопряженных поверхностей, которая уменьшает площадь контакта, поэтому ошибка формы не должна превышать определенный процент от допуска на изготовление детали.
Натяжение соединения допускает некоторую разборку и повторную сборку, потому что часть его подвергается упругой деформации, но в то же время прочность соединения несколько уменьшается из-за нерегулярного разрушения. Потеря прочности оценивается экспериментально. Во время работы прочность зажимного соединения часто уменьшается под воздействием ползучести материала и релаксации напряжений. Например, если бронзовый вал BRAZH 9-4 того же диаметра, что и гильза O = I = 30 мм из чугуна Sch 18, монтируется вертикально с натягом N = 30 мкм, начальная прочность на разрыв составляет 7845 Н. После 5000 часов работы при температуре 100 ° С прочность на разрыв падает до 3355 Н.
Когда некоторые металлы объединяются под воздействием давления, температуры и других факторов, некоторые металлы диффундируют и спекаются, увеличивая коэффициент адгезии и увеличивая прочность сцепления. Следовательно, если в качестве материала вала в предыдущем примере используется сталь 45 и рабочая температура повышается до 200 ° C, прочность на излом после 5000 часов работы увеличивается с 23 130 до 28 030 Н (получено Е. Ф. Бежелуковой данные). Существует два способа вычисления подгонки помех, и его суть рассматривается в следующем примере. Пример.
Выберите посадку с натягом (O = 185 мм; 110 мм; <12 = 265 мм; I = 170 мм), которая работает без вибрации и нагружена осевым усилием P = 392,2 кН. Детали изготовлены из стали 40 (E; = E = 206 ГПа; от = 313 МПа); параметры шероховатости = 8 мкм, Кгг = 7 мкм. Рабочая температура соединения близка к температуре сборки. Сборка нагревает часть крышки Принимает = 0,14, потому что выполняется. Существование по формуле (9.24) Расчетный минимум Ату Значения коэффициентов St и C2 взяты из (13). Найти рассчитанную коррекцию помех.
Исходя из условия задачи, возьмем u = 0 и u = 0. Поправка на шероховатость поверхности детали определяется по уравнению (9.30). Согласно таблице, найти коэффициент 9,2 k = 0,4, тогда u = 2-0,4 (8 + 7) = 12 мкм. Минимальная функциональная плотность L nNpG, которая гарантирует прочность сцепления, составляет 128 + 12 = 140 мкм. Ближайшие посадочные площадки, которые обеспечивают эти помехи в соответствии с ГОСТ 25347 82, — это посадочные площадки с m = 190 мкм, мм, m = 282 мкм (Рисунок 9.11, а). Далее, проверьте части, которые соединяются с самой большой таблицей Давление при указанных помехах получается из уравнения (9.17).
Майнинг S 0,58-313,10 1 — (- ^ Ц-) 2 93,2 МПа; На поверхности вала Rdop <0,58,313-10 < 1- = I7 7 МП- Условием прочности детали является отсутствие пластической деформации на контактной поверхности детали. Это гарантируется при p <3 rdop. Сравнение допустимого давления RDOP и давления, создаваемого при максимальном затягивании стола, запас прочности муфты равен (93.2 62.2) I 1.5, вал (117.7 62.2) 1,9. В случае перегрузки детали подключения не сбрасываются, а отключаются.
Следовательно, запас прочности соединительных деталей, созданных этим методом расчета, является фиктивным. Это главный недостаток этого метода расчета. Новый метод расчета. Посадка — это осевая сила, воспринимаемая суставом. Его следует выбирать не по помехам, определяемым крутящим моментом, а по требованиям к прочности деталей, подлежащих соединению, то есть максимально допустимым помехам, определяемым по уравнению (9.28). Аккаунт найден- .. Мы получаем Acney Rod а ^ 0 = 0,6 поправка у, С учетом поправки y.d. 1UpPP = (420 + 12) 0,95 = 410 мкм. В соответствии с максимальными функциональными помехами выберите подходящую, обеспечивающую запас прочности для соединений и компонентов.
Из рекомендуемых ГОСТ 25347-82 наиболее близким является посадка H8 i8 (рис. 9.11, б). Часть допуска на герметичность L13, с. Переход в зону безопасности (техническую зону безопасности) при сборке соединения всегда должен быть меньше, чем часть допуска L3.3. Это вызвано только увеличением силы прижима, вызванной снижением прочности материала деталей и искажением соединяемых деталей, что обеспечивает безопасный диапазон соединений при работе. Коэффициент трения и колебания температуры. Это требование лучше всего выполняется при комбинированной посадке N8 118 (рис. 9.11, в).
Замена посадок N7 i7 посадками N8 i8 увеличивает минимальные помехи пластины с 190 мкм до 241 мкм, создавая коэффициент безопасности соединения, определяемый плотностью L13 во время работы. = Mtut- t1nR = 241-140 = 101 мкм Nac-Ntcr-L t> 1t = 410 385 = 25 деталей в сборке, определяемых по герметичности. Следовательно, новый метод расчета посадки с гарантированной помехой может повысить долговечность соединения и увеличить производственные допуски на размеры, чтобы повысить экономическую эффективность производства деталей.
Примеры применения для посадки с натягом (гарантированный порядок посадки с натяжением): Н7 р6 (рекомендуется) — при соединении тонких деталей и воздействии малых нагрузок; H7 g6 (рекомендуется) — вводные проводники и проводники Для подключения основного блока. Для H7 h6 (рекомендуется) — Соединение между центральной колонной крана и основанием. Н7 и7-Для соединения червячных ступиц и коронок изделий тяжелой промышленности, втулок подшипников скольжения. H8 x8, H8 28 с максимальным гарантированным уровнем помех для соединений с большой нагрузкой.
Выбор метода изготовления компаунда (например, под прессом, нагрев или охлаждение детали крышки) зависит от таких факторов, как конструкция детали, размеры и необходимые помехи. Прочность зажимного соединения может быть увеличена путем гальванизации деталей, выбора соответствующих конструктивных деталей и стабилизации технических факторов во время сборки. Надежность посадки с натягом зависит от механических свойств материала соединяемых деталей, шероховатости и отклонения поверхности, конструктивных факторов, помех, метода сборки соединений и условий эксплуатации. Рекомендуется, чтобы выбранная посадка была проверена экспериментально.
Посадка считается подходящей, если герметичность соединения обеспечивается при минимальном затягивании, а прочность соединяемых деталей гарантируется при максимальном затягивании. В этих условиях соединение передает заданный крутящий момент или осевую силу, что позволяет детали выдерживать без разрушения напряжения, вызванного помехами или другими факторами.
Смотрите также: