Оглавление:
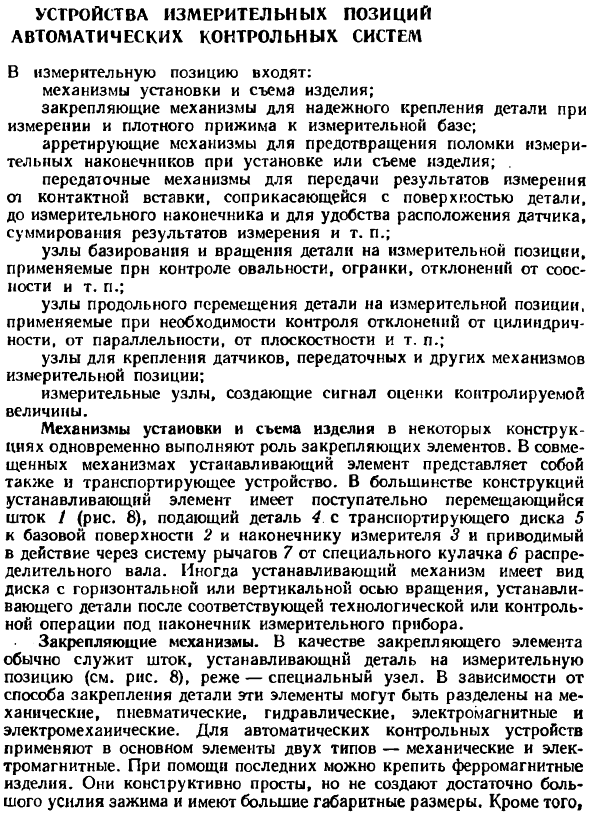
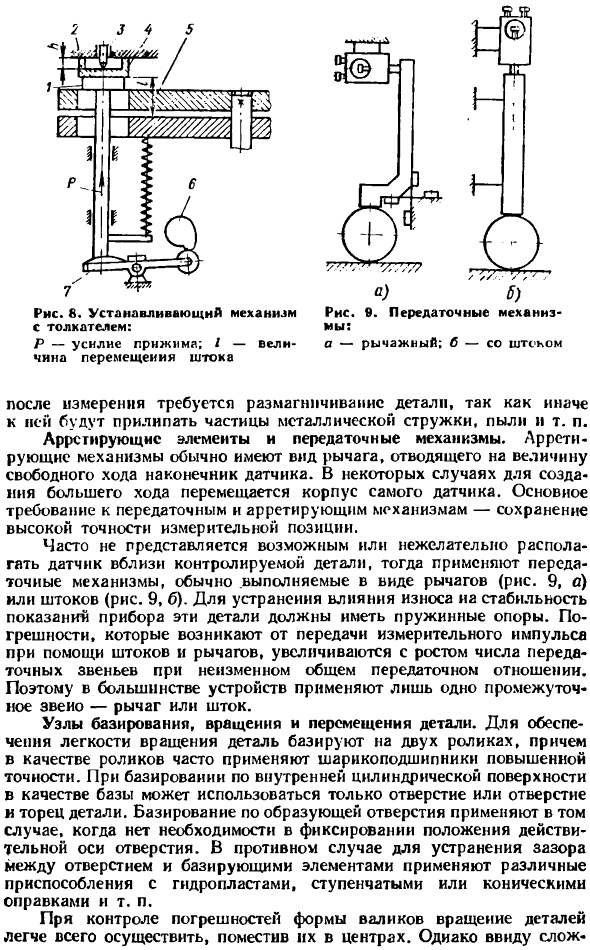
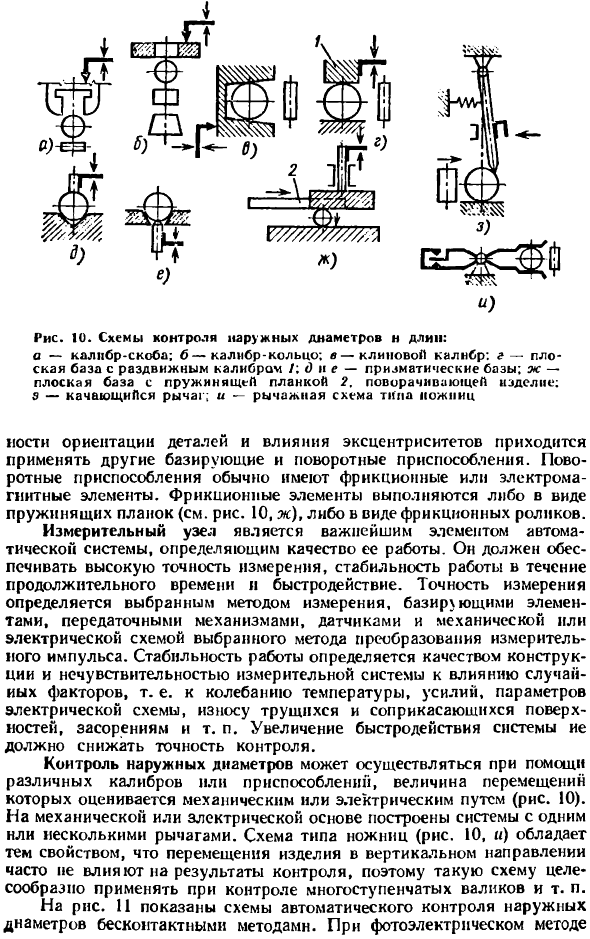
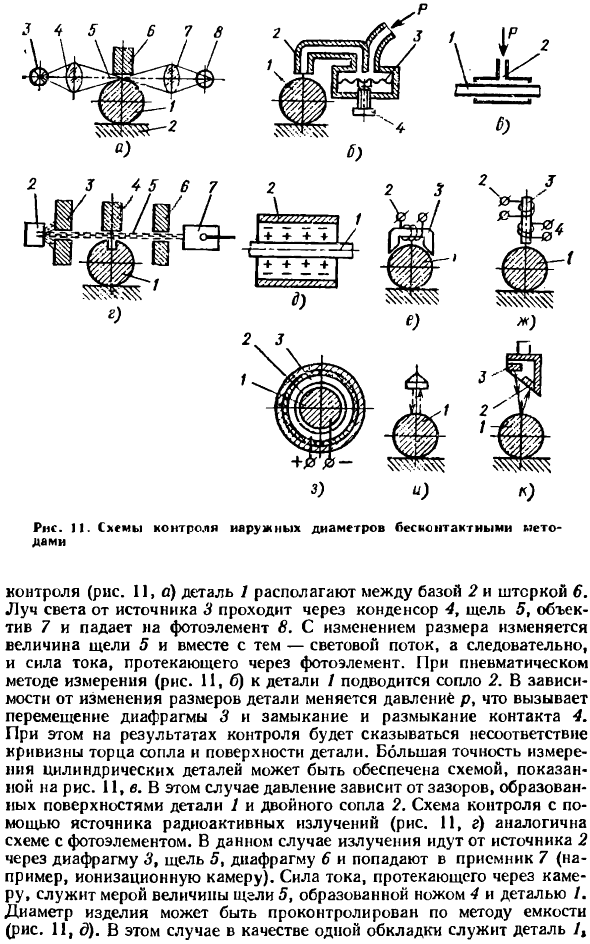
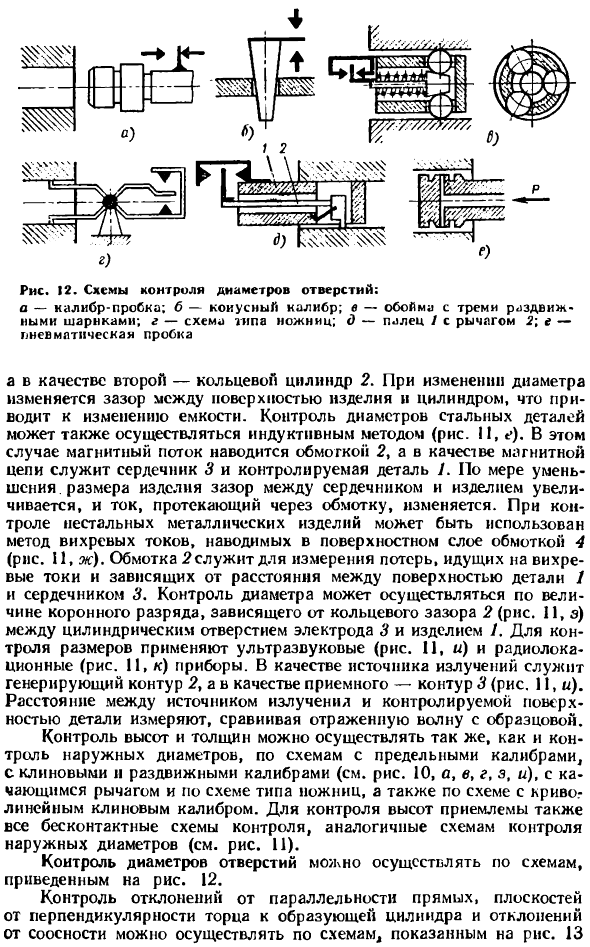
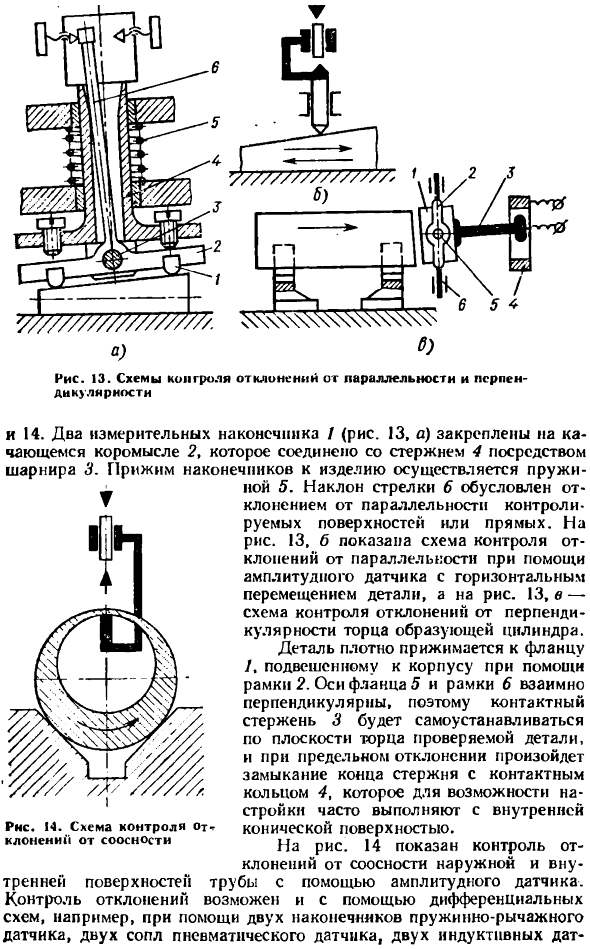
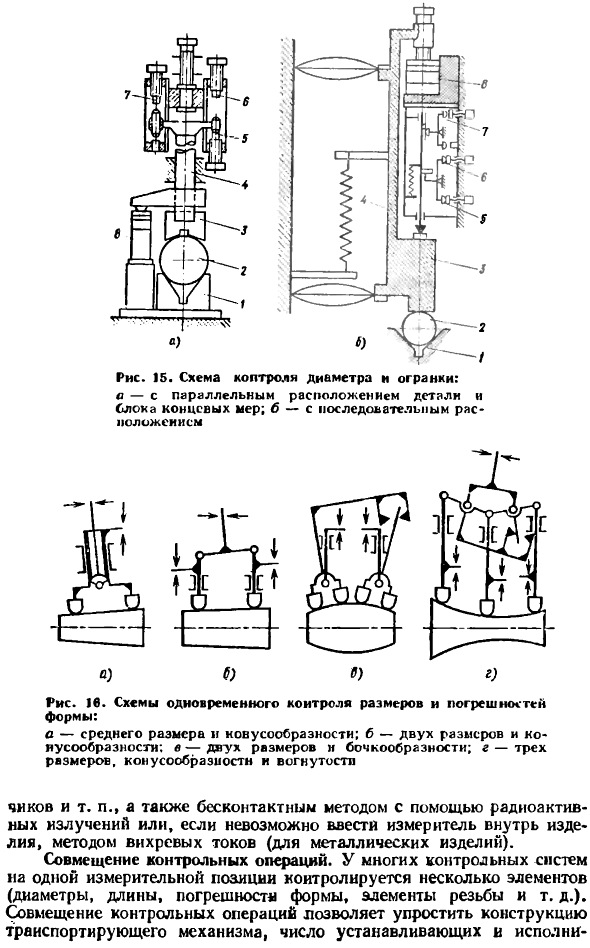
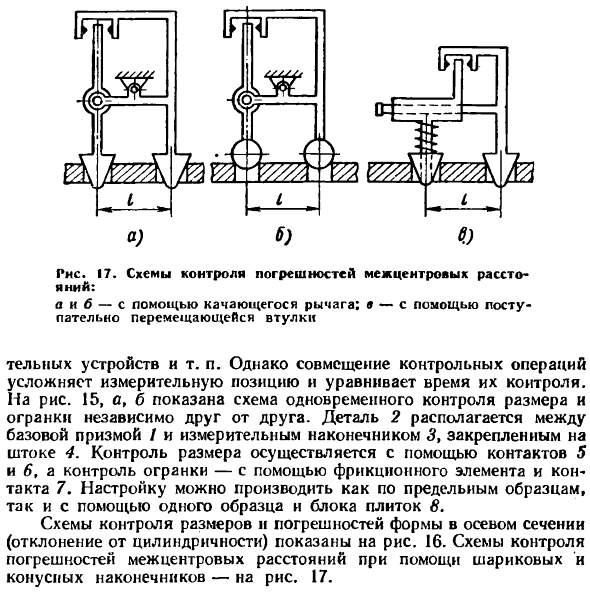

Устройства измерительных позиций автоматических контрольных систем
- Позиции измерения включают в себя: Механизм установки и удаления продукта. Механизм фиксации для надежной фиксации компонентов во время измерения и приложения сильного давления к измерительной базе. Механизм блокировки для предотвращения повреждения измерительного наконечника при установке или удалении продукта. Механизм передачи для передачи результатов измерения от контактной вставки, которая находится в контакте с поверхностью компонента, к измерительной микросхеме, а также местоположение датчика и общая сумма результатов измерения для удобства.
Узлы начала и поворота детали в месте измерения, используемые для контроля эллиптичности, разрезов, отклонений от выравнивания и т. Д. Узел вертикального перемещения детали в позиции измерения. Используется при необходимости для контроля отклонений от цилиндрической формы, параллельности, плоскостности и т. Д. Узел для установки датчиков, трансмиссий и других механизмов для измерения местоположения.
С развитием науки и совершенствованием методов и средств производства улучшается качество на оптимальном уровне. Людмила Фирмаль
Узел измерения, который создает сигнал для оценки контролируемой переменной. В некоторых конструкциях механизм установки и удаления изделия одновременно служит неподвижным элементом. В комбинированном механизме крепежный элемент также является транспортным устройством. В большинстве конструкций крепежный элемент имеет переводной стержень 1 (фиг. 8), подачу 4 с транспортного диска 5 на основную поверхность 2 и наконечник расходомера 3, а также специальную систему рычага 7 кулачка 6 на распределительном валу.
Проехал через Монтажный механизм может иметь форму диска с горизонтальной или вертикальной осью вращения и устанавливать деталь после соответствующей технической или контрольной операции под наконечник измерительного устройства. Исправлен механизм. Стержни обычно используются в качестве крепежных элементов. Стержень устанавливает деталь в положение измерения (см. Рисунок 8). В зависимости от того, как детали закреплены, эти элементы могут быть классифицированы как механические, пневматические, гидравлические, электромагнитные и электромеханические.
Устройства автоматического управления в основном используют два типа элементов: механические элементы и электромагнитные элементы. С последним, ферромагнитные продукты могут быть установлены. Они конструктивно просты, но не создают достаточно больших зажимных усилий и имеют большие габаритные размеры. также После измерения детали должны быть размагничены. В противном случае частицы, такие как металлические фрагменты и пыль, прилипнут. Арест элемент и снаряжение. Механизм блокировки обычно имеет форму рычага, который отклоняет наконечник датчика на величину свободного движения.
В некоторых случаях датчики сами перемещаются, создавая большие удары. Основным требованием механизма передачи и блокировки является поддержание высокой точности положения измерения. Часто невозможно или нежелательно размещать датчик рядом с элементом управления, и используется механизм передачи, обычно в форме рычага (рис. 9, в) или стержня (рис. 9, 6). Эти компоненты требуют пружинных опор, чтобы исключить влияние износа на стабильность показаний прибора.
Ошибка, возникающая в результате передачи измерительного импульса штоком и рычагом, увеличивается с увеличением числа звеньев передачи с одинаковым общим передаточным числом. Поэтому в большинстве устройств используется только одно промежуточное звено рычага или стержня. Узлы для компонентной базы, ротации и перевода. Для облегчения вращения детали опираются на два ролика, в качестве роликов часто используются высокоточные шарикоподшипники. Если он основан на внутренней цилиндрической поверхности, в качестве основания можно использовать только отверстие или отверстие и торец детали.
Используется, когда нет необходимости фиксировать фактическое положение оси отверстия на основе сформированного отверстия. В противном случае для устранения зазора между отверстием и базовым элементом используются различные устройства с гидропластами, ступенчатыми или коническими оправками и т. Д. Непосредственное управление ошибкой в форме ролика — это самый простой способ отцентрировать деталь и повернуть деталь. Одиако с комплексной точки зрения скоба a-калибра; кольцо 6 калибров: калибр в клине.
Основание с скользящим калибром G основание из призмы dpe; g-плоское основание с пружинным стержнем 2. Поверните изделие. Поворотный рычаг и ножничная навеска Для влияния ориентации и эксцентриситета компонентов необходимо использовать другие базовые и вращающиеся устройства. Поворотные приспособления обычно имеют фрикционные или электромагнитные элементы. Фрикционный элемент имеет форму пружинного стержня (см. Рис. 10) или фрикционного ролика. Измерительный блок является важнейшим элементом автоматизированной системы, определяющей качество работы.
Он должен обеспечивать высокую точность измерений, стабильность во времени и скорости. Точность измерения зависит от выбранного метода измерения, базового элемента, зубчатых колес, датчиков и механической или электрической схемы выбранного метода преобразования импульсов измерения. Эксплуатационная стабильность определяется качеством конструкции и нечувствительностью измерительной системы к воздействию случайных факторов, таких как температура, силы, параметры электрической цепи, трение и износ контактной поверхности и засорение.
Увеличение скорости системы снижает точность управления. Наружный диаметр можно контролировать с помощью различных калибров или устройств, а смещение оценивается механически или электрически (рис. 10). Системы с одним или несколькими рычагами построены механически или электрически. Рекомендуется использовать схемы ножничного типа (рис. 10 и) при управлении такими продуктами, как многоступенчатые ролики, поскольку перемещение продукта по вертикали не часто влияет на результат контроля.
На фиг.11 показана схема для автоматического контроля наружного диаметра бесконтактным способом. Фотоэлектрический тип Контрольная (рис. 11, а) часть 1 размещена между основанием 2 и шторкой 6. Свет от источника 3 света проходит через конденсатор 4, щель 5 и линзу 7 и попадает на фотоэлемент 8.
- При изменении размера размер щели 5 также изменяется, и в то же время — интенсивность светового потока и, следовательно, тока, протекающего через фотоэлемент. В методе измерения давления воздуха (рис. 11b) сопло 2 вставляется в деталь . Давление p изменяется в зависимости от размера детали, диафрагма 3 перемещается, и контакт 4 открывается и закрывается. Сопла и поверхности компонентов. Показанная схема повышает точность измерения цилиндрических деталей.
В этом случае давление зависит от зазора, образованного деталью , и поверхности двойного сопла 2. Схема управления с использованием источника излучения (рис. 11, г) аналогична схеме фотоэлемента. В этом случае излучение от источника 2 проходит через диафрагму 3, щель 5, диафрагму 6 и в приемник 7 (например, ионизационную камеру). Сила тока, протекающего через камеру, служит мерой размера зазора 5, образованного ножом 4 и частью I. Диаметр продукта можно контролировать с помощью объема (рис. 11, д). В этом случае часть Рисунок 12. Схема контроля диаметра отверстия.
Если калибр для прохождения не проходит, если есть калибр, то деталь не проходит, размер такого вала ограничивается минимально допустимым размером детали. Людмила Фирмаль
Палец 1 с D-рычагом 2. электронная пневматическая заглушка При изменении диаметра зазор между поверхностью изделия и цилиндром изменяется, меняя объем. Контроль диаметра стальных деталей также может быть выполнен индукционным методом (рис. 11, е). В этом случае магнитный поток индуцируется обмоткой 2, а сердечник 3 и управляемый блок 1 функционируют как магнитная цепь. Размер изделия, зазор между сердечником и изделием увеличивается, а ток, протекающий через обмотку, изменяется.
При мониторинге изделий из цветных металлов можно использовать метод вихревых токов, индуцированных в поверхностном слое обмоткой 4 (рис. II, g). Обмотка 2 используется для измерения потерь на вихревые токи и зависит от расстояния между поверхностью компонента 1 и сердечником 3. Диаметр можно контролировать размером коронного разряда. Произведение кольцевого зазора 2 (фиг. 11h) между цилиндрическими отверстиями электрода 3.
Используйте ультразвуковое (рис. 11, i) и радарное (рис. 11, k) оборудование для контроля размера. Генератор 2 работает как источник излучения, а схема 3 — как приемник (рис. 11 и). Расстояние между источником и контрольной поверхностью детали измеряется путем сравнения отраженной волны с эталоном. Контроль высоты и толщины выполняется так же, как контроль внешнего диаметра, в соответствии с ограничителями, клиньями и скользящими датчиками (см.
Рисунок 10, a, c, d, h, i, поворотными рычагами и ножницами в соответствии со схемой. Как изогнутая схема, как Калибр линейного клина. Любая бесконтактная схема управления, аналогичная схеме управления внешним диаметром, также может быть использована для контроля высоты (см. Рисунок 11). Диаметр отверстия можно контролировать по схеме, показанной на рисунке. 12.
Отклонения от параллельности прямых, плоскостей от перпендикулярных торцов к шинам цилиндров и отклонения от выравнивания могут быть выполнены согласно схеме, показанной на рисунке. 13 14. Два измерительных наконечника (фиг. 13, а) установлены на качающемся рычаге 2, соединенном со стержнем 4 шарниром 4. Кончик наконечника изделия — пружина 5. Наклон стрелки 6 обусловлен отклонением контролируемой поверхности или прямой от параллельности.
На фиг.13b показана схема контроля отклонений от параллельности с использованием амплитудного датчика с горизонтальным перемещением детали, а на фиг.13b на фиг.13 с показана вертикальность торца цилиндрической шины. Это контрольная диаграмма отклонения. Поскольку оси фланца 5 и рамы 6 перпендикулярны друг другу, контактный стержень 3 самоцентрируется вдоль плоскости торца тестируемой детали, при этом наибольшее отклонение конца штока закрыто контактным кольцом. , Благодаря возможности регулировки его часто выполняют на внутренних конических поверхностях.
На рисунке 14 показан контроль отклонения от внешнего и внутреннего выравнивания Поверхность трубы с использованием датчика амплитуды. Отклонение также можно контролировать с помощью дифференциальной цепи. Например, используйте два наконечника для датчика пружинного рычага, два сопла для пневматического датчика и два индуктивных датчика. I) Я) 9) в) Рисунок 1с. Схема одновременного контроля размеров и ошибок формы: a-medium и kovusobraznosti; размеры b-2 и формы соединения: размеры a-2 и стволы.
Бесконтактный метод с использованием радиоактивного излучения, такого как метод Чикова, или вихретоковый метод (для металлических изделий), когда счетчик не может быть введен в изделие. Комбинация контрольных операций. Во многих системах управления несколько элементов контролируются в одном и том же месте измерения (диаметр, длина, ошибка формы, винтовые элементы и т. Д.). Комбинация управляющих операций упрощает ряд транспортных механизмов проектирования, настройки и реализации.
Однако комбинация операций управления усложняет положение измерения и делает время управления равномерным. На рисунках 15, a и b показаны схемы одновременного контроля размера и резки независимо друг от друга. Часть 2 находится между базовой призмой прикрепленной к стержню 4 и измерительным наконечником 3. Управление размером осуществляется с помощью контактов 5 и 6, а фаски управляются с помощью фрикционных элементов и контактов 7.
Используйте один образец и блок плиток. Схема (отклонение от цилиндрической формы) для контроля погрешностей размеров и формы сечения вала показана на рисунке. 16. Схема контроля ошибок от центра к центру с использованием шарикового и конического наконечника.
Смотрите также:
Решение задач по метрологии с примерами