Оглавление:
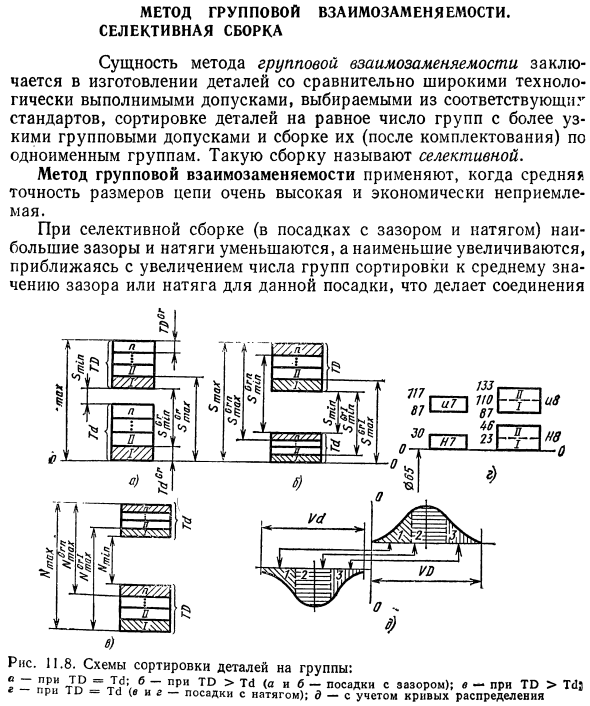
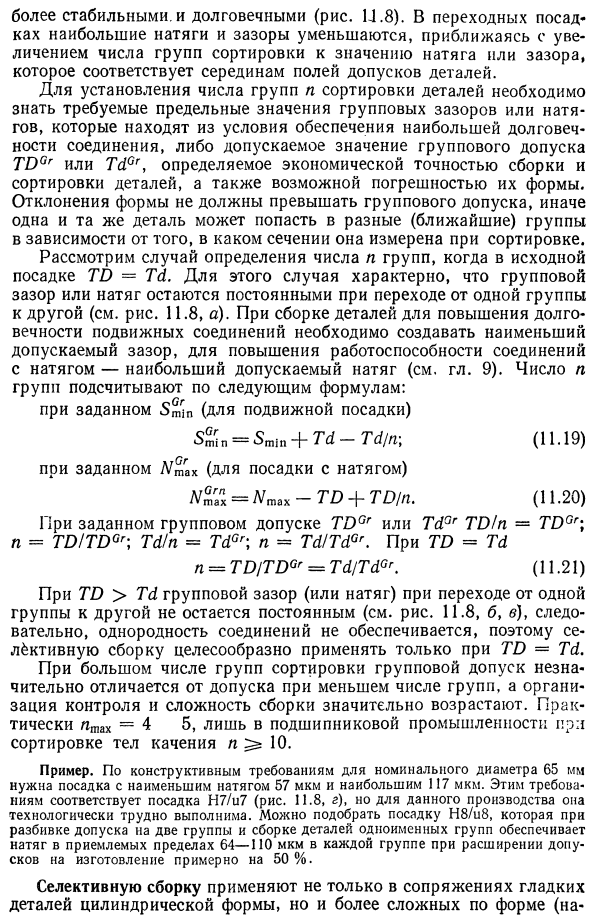
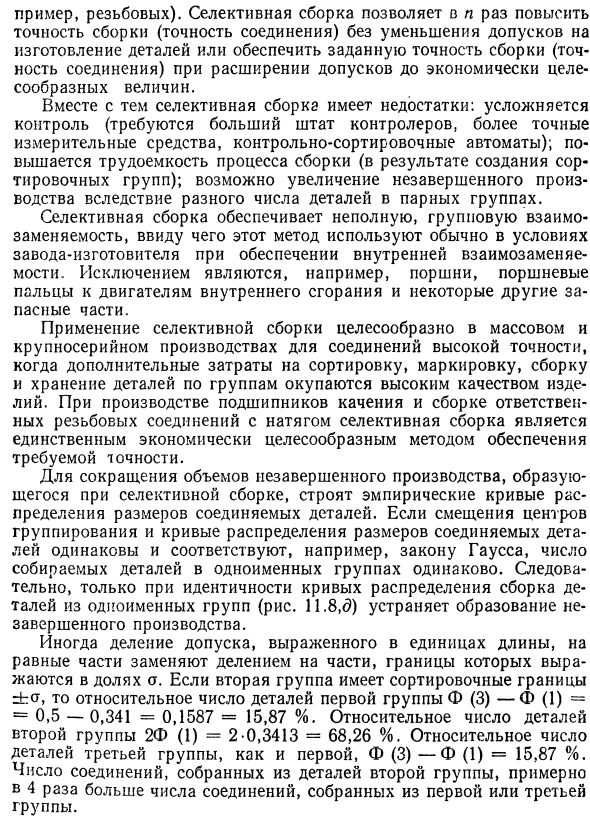

Метод групповой взаимозаменяемости. Селективная сборка
- Суть метода групповой совместимости состоит в том, чтобы производить детали с относительно широкими технически выполнимыми допусками, выбранными из соответствующих стандартов, классифицировать детали на одинаковое количество групп с узкими групповыми допусками и одинаковыми Сборка в группу имен (после завершения). Эта сборка называется выборочной.
Метод групповой совместимости используется, когда средняя точность размера цепи очень высока и экономически неприемлема. При выборочной сборке (согласование зазора и помех) максимальный зазор и помехи будут уменьшаться, минимально увеличиваться, а с увеличением количества групп сортировки средний зазор или помехи для конкретной посадки будут увеличиваться, и соединение будет Будет создан Он более стабилен и долговечен (рис. 1.1.8). При переходной посадке максимальные помехи и зазор уменьшаются и приближаются к значению помехи или зазора, соответствующему средней точке допуска детали, по мере увеличения числа групп классификации.
Уровень устанавливают на испытуемую поверхность с помощью ампул 3, так что ампула 2 находится в горизонтальной плоскости. Людмила Фирмаль
Чтобы установить количество групп для классификации деталей, допуск на групповой допуск TO0g или TaOg определяется условиями, обеспечивающими максимальную долговечность соединения, или экономической точностью сборки и сортировки деталей. Вы должны знать требуемый групповой разрыв или пределы помех от значений и возможных ошибок формы. Отклонения от формы не должны превышать групповой допуск. В противном случае одни и те же детали будут сгруппированы в разные (ближайшие) группы в зависимости от сечения, измеренного во время сортировки. Рассмотрим случай определения количества n групп, когда TE) = TO в начальной подгонке.
В этом случае обычно групповой разрыв или помехи остаются постоянными во время перехода между группами (см. Рис. 11.8, o). При сборке деталей необходимо создать минимально допустимый зазор для увеличения срока службы подвижного соединения. Чтобы повысить работоспособность соединений с посадками с помехами, необходимо создать максимально допустимые помехи (см. Главу 9). Количество групп n рассчитывается по следующей формуле. Для конкретного 5 ^ n (для мобильной посадки) 5t1n = 5t1 + ta-tasch-, (11.19)
Для конкретного LGT (для плотной посадки) = Lgtakh GO + TO l. (11.20) Допуск данной группы TOvg или Taag Tyn = GO0 ; n = m m0 ; Ta1n = Taa, n = Ta Ta0 . Когда идти = та n = to toag = ta taa . (11.21) Когда GO Ta, разрыв группы (или интерференция) при переходе от одной группы к другой не поддерживается постоянным (см. Рис. 11.8, б, в), поэтому совместная однородность не гарантируется Поэтому рекомендуется использовать выборочную сборку только с GO =.
- Если групп сортировки много, допуск группы несколько отличается от допусков для небольшого числа групп, что значительно увеличивает организацию управления и сложность сборки. Эффективно pgai1 = 45, только для подшипниковой промышленности Элемент качения сорт n 10. Пример. Согласно проектным требованиям, номинальный диаметр 65 мм требует посадки с минимальными помехами 57 мкм и максимум 117 мкм. Посадка H7 I7 отвечает этим требованиям (рис. 11.8, d), но технически сложно достичь в этом производстве.
Fit H8 i8 может быть выбран. Это позволяет разделить допуски на две группы и собрать одну и ту же группу деталей, чтобы обеспечить взаимную посадку в диапазоне допусков от 64 до 110 микрон в каждой группе. Пятьдесят процентов Выборочная сборка сопрягает не только гладкие цилиндрические детали, но и более сложные формы ( Пример, нить). Выборочная сборка увеличивает точность сборки (точность соединения) в n раз, не уменьшая допуски на изготовление компонентов, или расширяет допуски до экономически допустимого значения, обеспечивая при этом требуемую точность сборки (Точность подключения). В то же время выборочная сборка имеет свои недостатки.
Однако массовое производство имеет большой экономический эффект и способствует частичной и полной автоматизации технологических процессов. Людмила Фирмаль
Управление является сложным (требует больше контроллеров, более точных измерительных приборов, органов управления и сортировщиков). Увеличивает сложность процесса сборки (в результате создания групп сортировки). Вы можете увеличить объем незавершенного производства, потому что количество деталей в группе пар отличается. Выборочная сборка обеспечивает неполную совместимость групп. В результате этот метод обычно используется в соответствии с требованиями производителя для обеспечения внутренней совместимости. Исключением являются, например, поршни, поршневые пальцы двигателей внутреннего сгорания и другие запасные части.
Выборочная сборка рекомендуется для массового производства и массового производства высокоточных составов, когда дополнительные затраты на классификацию, маркировку, сборку и хранение деталей в группах оплачиваются высококачественными продуктами. При производстве подшипников качения и сборке критических винтовых соединений с помехами выборочная сборка является единственным экономически целесообразным способом обеспечения требуемой точности. Чтобы уменьшить объем незавершенного производства из-за выборочной сборки, создаются эмпирические кривые распределения размеров соединяемой детали.
Если кривые смещения центра группировки и распределения размеров соединенных деталей совпадают, например, в соответствии с законом Гаусса, количество собранных деталей в одной группе одинаково. Поэтому сборка деталей одной группы (рис. 11.8.5) исключает формирование продолжающейся работы, только если кривые распределения идентичны. Разбиение допусков, выраженных в единицах длины, на равные части может быть заменено делением границы на части, представленные дробью a.
Если вторая группа имеет границу сортировки ± o, относительное количество деталей в первой группе составляет Ф (3) -Ф (1) = = 0,5-0,341 = 0,1587 = 15,87%. Относительное количество деталей во второй группе составляет 2F (1) = 2, 0,3413 = 68,26%. Относительное количество частей третьей группы и первой группы, Ф (3) —Ф (1) = 15,87%. Количество соединений, собранных из второй группы, примерно в четыре раза превышает количество соединений, собранных из первой или третьей группы.
Смотрите также: