Оглавление:
Управление качеством как научная концепция возникло на рубеже 19 и 20 веков, когда развитие промышленной революции в Европе и США положило конец ремесленничеству, а переход к крупносерийному и массовому производству потребовал новых подходов к организации труда и качеству.
В 1970-х годах на заводе Colt в США родилась идея стандартного качества: Оружие теперь собиралось не из подогнанных друг к другу деталей, а из партии взаимозаменяемых частей. Появилась должность инспектора, который не допускал сборки неподходящих деталей. Эта идея стандартного качества была разработана в начале 20-го века Г. Фордом в автомобильной промышленности (работа по калибровке). Он был первым, кто использовал конвейерную ленту в сборочных работах. Поточное производство увеличило производительность труда на порядок, что позволило производить относительно дешевую продукцию. Научное обоснование системы поточного производства дал Ф. Тейлор, а научное управление качеством, основанное на принципах отбраковки непригодной продукции, сформулировали А. Файоль и М. Вебер.
Несмотря на значительные достижения в организации производства, уровень качества продукции оставался низким в первой половине 20-го века, а хорошее качество достигалось за счет значительных затрат на усовершенствование и усиление контроля.
Во второй половине 50-х годов в Японии, сильно зависящей от экспорта своей продукции, началось движение за постоянное улучшение качества. Агитатором этого движения стал американский ученый Э. Деминг, который не нашел последователей у себя на родине и отправился в Японию для реализации своих идей. Вместе с учеными М. Джураном (США) и К. Исикавой (Япония) он разработал новую систему управления качеством, которая впоследствии была названа TQC — Total Quality Control System. Эта система была в значительной степени ориентирована на потребителя и ориентирована на массовое и сознательное вовлечение руководителей и сотрудников производственной компании в работу по повышению качества продукции. Эта система нашла большой отклик во всех промышленно развитых странах мира, включая СССР. Конечно, это произошло во многом благодаря «японскому феномену», который заключался в том, что в послевоенный период Япония имела ежегодный рост ВВП (валового внутреннего продукта) почти на 10% в течение более 20 лет, несмотря на систематические экономические кризисы в капиталистических странах. Японский феномен особенно беспокоил советских экономистов, поскольку он не вписывался в марксистские экономические теории.
Триумф японского опыта управления качеством во всем мире привел к масштабному обогащению этой системы разработками ученых и опытом практиков в странах с развитой экономикой Европы и Северной Америки. Она положила начало разработке серии международных стандартов качества ISO 9000, основанных на наиболее ярких результатах мирового опыта.
Новая система управления качеством, обогащенная международным опытом, во многих литературных источниках 1980-х годов получила название TQM — Total Quality Management или Total Quality Management System.
В 1990-х годах термины «система качества» и «сертификация системы качества» стали выходить на первый план в обеспечении качества продукции. Новая система управления качеством, похоже, только зарождается.
Главное отличие новой системы от вышеупомянутых заключается в том, что потребитель получает гарантию качества не одного образца продукции, а всего производства. Это достигается путем сертификации (подтверждения соответствия) системы качества компании, которая гарантирует качество продукции и ее экологичность на всех этапах жизненного цикла.
Современная компания, выходящая со своей продукцией на международный рынок, использует элементы всех вышеперечисленных систем менеджмента качества для достижения запланированного качества продукции. Схематично это можно выразить в виде «качественного шторма».
На первом этаже башни находится отдел контроля качества, задача которого — не допустить попадания некачественной продукции к потребителю, что включает использование методов статистического контроля. На втором этаже находится Управление качеством, целью которого является увеличение выхода качественной продукции. На третьем этаже находится отдел планирования качества, целью которого является обеспечение максимально полного удовлетворения потребностей клиентов. На четвертом этаже находится отдел экологии качества, целью которого является эффективное сочетание требований обеспечения качества и экологических требований к продукции компании.
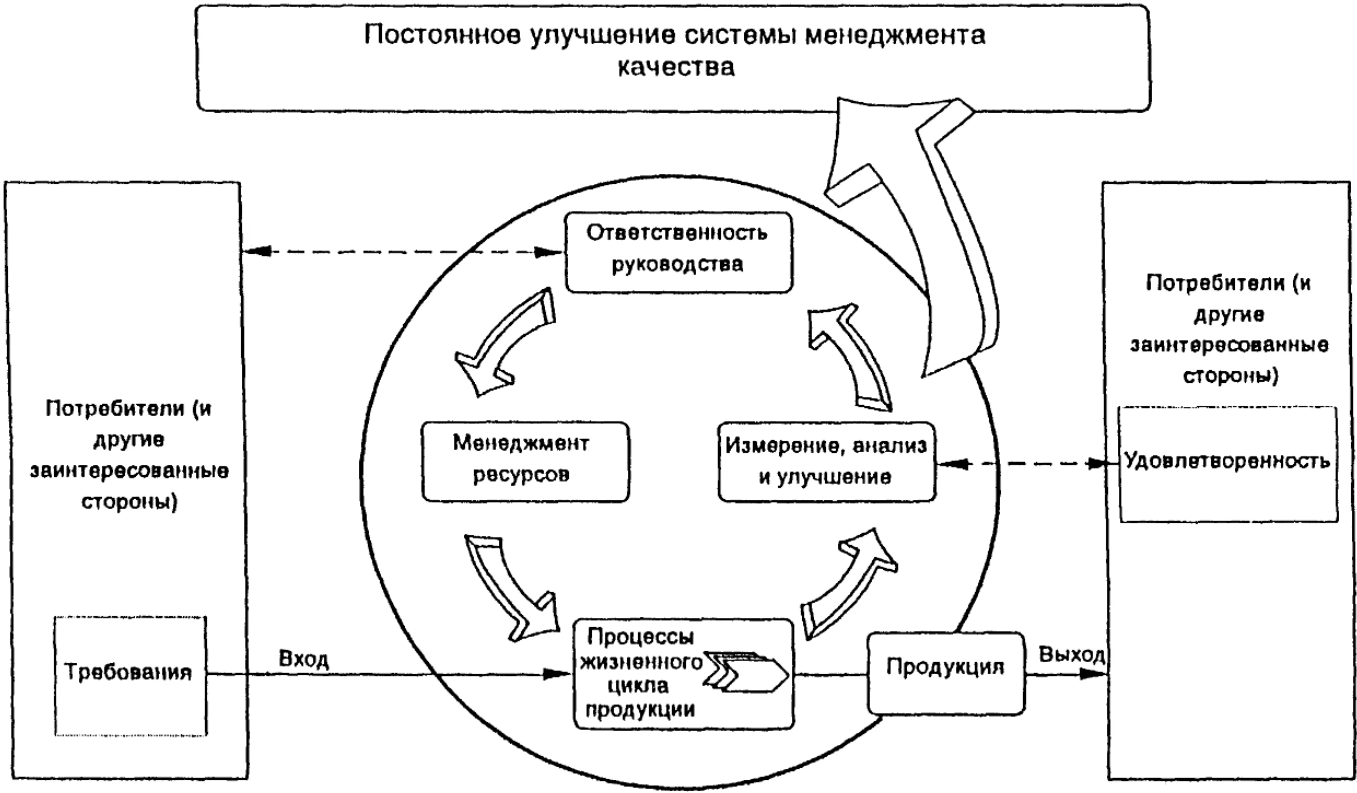
Получение информации о качестве продукции
Сбор объективной и представительной информации о параметрах исследуемой детали или процесса является важным фактором для правильной оценки качества детали или характера процесса. Целями сбора информации о продукте являются:
- Контроль и регулирование производственного процесса;
- Анализ отклонений от заданных требований;
- Контроль продукции.
Как только цель сбора данных установлена, она становится основой для определения типа сравнения, которое необходимо провести, и типа данных, которые необходимо собрать. Например, предположим, что есть вопрос о вариации показателя качества продукции. Если проводится одно измерение в день, невозможно оценить изменение в течение дня. Для выявления работника, совершающего ошибки, необходимо взять отдельные образцы, чтобы можно было сравнить производительность каждого образца. Такое разделение группы данных на несколько подгрупп по определенному признаку называется стратификацией или расслоением. Анализируя группу данных, всегда помните о возможности стратификации.
В реальных приложениях желательно записывать данные в простой и удобной для использования форме. Такой формой является контрольный лист — бумажный бланк, на котором заранее распечатываются параметры, подлежащие контролю, чтобы данные измерений можно было легко и точно записать. Она служит, с одной стороны, для облегчения сбора данных, а с другой — для автоматической подготовки данных к дальнейшей обработке.
Контрольный список для регистрации типов ошибок. Каждый раз, когда экзаменатор замечает ошибку, он делает пометку (один росчерк) в листе. Если есть 4 штриха, они зачеркиваются пятым штрихом. В конце дня эксперт может быстро подсчитать количество и разновидности дефектов. Недостатком этого листа является то, что данные не могут быть стратифицированы.
Это можно легко сделать с помощью контрольного списка причин дефектов. Лист предназначен для того, чтобы помочь вам отобрать необходимую информацию о дефектах, возникших не только по вине рабочего или из-за плохой регулировки машины, но и для выявления возникновения дефектов, вызванных усталостью во второй половине дня или изменением условий труда рабочего.
Наиболее типичным примером статистического контроля качества является статистический приемочный контроль. Основная идея такого контроля заключается в том, что качество контролируемой партии продукции оценивается на основе характерных значений небольшой выборки из этой партии. Приемочный контроль отличается качественными и количественными характеристиками. При контроле на основе качества каждая проверенная единица продукции относится к определенной группе (хорошая или дефектная продукция), и последующие решения принимаются в зависимости от соотношения количества продукции, входящей в эти группы. Такой контроль называется альтернативным контролем. В случае контроля по количественным характеристикам определяются значения одного или нескольких параметров единиц продукции и в зависимости от этих значений принимаются последующие решения (среднее арифметическое значение параметра, стандартное отклонение).
Для организации приемочного контроля по качественным характеристикам необходимо установить стандарты контроля, т.е. критерии принятия решения (число принятия, число отказа) и правила приемки. На практике наиболее широко используются три вида приемочного контроля:
- одноэтапный, когда решение о принятии или отбраковке партии продукции основывается на результатах контроля только одной пробы или образца;
- многоступенчатые, когда решение о принятии или отбраковке партии принимается на основе последовательных испытаний (больше или равно 2) проб или образцов, причем максимальное число проб фиксируется заранее;
- последовательные, когда решение о принятии или продолжении испытания принимается после оценки каждой последовательно испытанной единицы продукции (пробы, образца).
Отдел инженерного контроля.
ОТК — отдел технического контроля. Независимый структурный участок производственной организации, осуществляющий независимый контроль соответствия продукции установленным требованиям и гарантирующий это соответствие заказчику. Отдел технического контроля подчиняется высшему руководству организации (непосредственно техническому директору), что обеспечивает независимость контроля.
Требования к продукции указываются в контрактах (договорах), нормативной (стандартах) и технической (конструкторско-технологической) документации. Факт приемки изделия ОТК и гарантийные обязательства организации фиксируются в паспорте изделия (или другом документе, его заменяющем: Сертификат, этикетка, наклейка, акт приемки, инструкция по применению).
Задача ОКР — не допустить выпуска продукции предприятия, не соответствующей требованиям стандартов и технических условий, конструкторской и технологической документации, условиям поставок и договоров, а также повысить ответственность всех звеньев производства за качество продукции.
Функции отдела технического контроля:
- Контроль качества и комплектности изготовленных деталей
- Анализ и технический учет брака и дефектов продукции предприятия
- организация сбора и систематизации информации о качестве продукции и надежности потребителей
- Контроль качества сырья, полуфабрикатов и компонентов, поставляемых на завод для производства основной продукции
- Контроль за комплектацией, упаковкой и сохранением готовой продукции
- Контроль за своевременной подготовкой и осуществлением мероприятий, связанных с внедрением новых стандартов и технических условий
- Контроль над наличием торговой марки (бренда компании) на готовой продукции
- Систематический контроль за состоянием эксплуатируемых средств измерения и контроля и их своевременное представление на государственные испытания
- Контроль качества продукции и проверка инструментов, используемых в компании
- Подготовка и представление техническому директору предприятия на утверждение и своевременное выполнение графиков периодических (повторных) типовых испытаний серийной продукции в соответствии с требованиями ГОСТ Р, ТУ, а также испытаний на соответствие основных технологических процессов
- надзорный контроль за соблюдением условий хранения на складах и в цехах компании комплектующих, сырья, материалов и готовой продукции
- учет показателей качества выпускаемой продукции по всем производственным подразделениям
- Организация и внедрение передовых методов контроля и оценки качества продукции
- проведение выборочных проверок качества готовой продукции, сырья, материалов, полуфабрикатов и комплектующих изделий, качества выполнения отдельных технологических операций и переходов, качества и состояния оборудования и инструмента, условий производства, хранения и транспортировки продукции, не предусмотренных утвержденным технологическим процессом
- Участвовать в тестировании новых и модифицированных образцов продукции и выпуске технической документации на эти продукты для обеспечения условий эффективного контроля качества
- участие в работе по подготовке продукции к сертификации и принятию декларации о соответствии
- участие в подготовке договоров на поставку в компанию сырья, материалов, полуфабрикатов, комплектующих и инструментов с целью согласования условий их качественной приемки
- Формирование предложений, направленных на совершенствование требований к качеству производимой и потребляемой компанией продукции, совершенствование нормативно-технической документации, устанавливающей эти требования, а также предложений, направленных на стимулирование производства высококачественной продукции и борьбу с производством некачественной продукции.
Отдел технического контроля выполняет свои функции через своих сотрудников и обучает производственный персонал методам контроля и самоконтроля на каждой технологической операции.
Самоконтроль, осуществляемый непосредственно работником, выполняющим работу, является наиболее эффективным средством обеспечения качества продукции.
В процессе работы рабочий и бригадир постоянно проверяют правильность обработки, проверяют соблюдение геометрических форм по чертежам изделия и т.д. В этом случае технический контроль выборочно проверяет качество обработки и правильность размеров изделия.
Международные и региональные стандарты качества
Система качества может быть эффективной только в том случае, если она функционирует в системе менеджмента качества в тесном взаимодействии со всеми видами деятельности, влияющими на качество продукции, и отвечает следующим требованиям:
- обеспечивает управление качеством на всех этапах цикла качества;
- гарантирует, что все сотрудники компании вовлечены в управление качеством;
- определяет обязанности руководства;
- обеспечивает неразрывную связь мероприятий по качеству с мероприятиями по снижению затрат;
- обеспечивает проведение профилактических проверок для предотвращения несоответствий и дефектов;
- обеспечивает выявление дефектов и предотвращает их попадание в производство и к потребителю,
- устанавливает процедуры для периодического обзора, анализа и улучшения системы;
- определяет и обеспечивает документирование всех системных процедур.
Международные стандарты на системы качества серии ISO 9000 как важная часть системы менеджмента качества были разработаны для единого подхода к решению вопросов управления качеством и максимального удовлетворения требований потребителей, устранения различий и гармонизации требований.
Эти стандарты описывают элементы, которые должна содержать система качества, но не то, как они должны быть реализованы.
Состав и содержание элементов системы качества.
Ответственность руководства. Стандарт требует от руководства обязательного выполнения следующих ключевых моментов:
- Политика в области качества;
- Распределение полномочий между сотрудниками, ответственными за качество;
- обеспечение качественной работы необходимыми ресурсами;
- назначение представителя руководства, ответственного за качество;
- проведение внутренних проверок (аудитов).
Система качества (структура). Стандарт ISO 9001 требует от компании разработки, документирования и поддержания системы качества таким образом, чтобы продукция соответствовала установленным требованиям. В этом разделе также определены основные документы системы качества:
- Руководство по качеству (руководство по системе качества);
- документированные процедуры системы качества (метод и рабочие инструкции);
- Планы качества (планы с мероприятиями по внедрению и развитию менеджмента качества).
Периодическая проверка контракта. Чтобы избежать риска, связанного с несоответствием требований заказчика в поставляемой продукции, стандарт требует, чтобы поставщик разработал и поддерживал документированные процедуры, обеспечивающие рассмотрение и координацию этой работы в рамках контракта.
Управление дизайном. Стандарт подразумевает подход к проекту как к одному из видов продукции (интеллектуальной). «Петля качества» для проекта имеет свои стадии жизненного цикла:
- Планирование проектирования и развития. Компания должна подготовить планы для каждого вида деятельности по проектированию и разработке. Планы должны обновляться по мере развития процесса проектирования;
- Организационное и техническое сотрудничество (между различными группами, вносящими свой вклад в процесс проектирования);
- Входные данные для проектирования;
- Результаты проекта;
- Анализ проекта. Стандарт рекомендует, чтобы анализ проекта проводился рабочими группами сотрудников проектного офиса из разных отделов;
- Проверка проекта на соответствие исходным данным;
- утверждение проекта.
Управление документацией. Существующие записи должны быть доступны, своевременно рассмотрены и утверждены уполномоченным персоналом. Записи должны быть доступны во всех зонах обеспечения качества, а устаревшие записи должны быть удалены.
Закупка продукции. Необходимо обеспечить качество поставок от связанных сторон. Это предусмотрено стандартом посредством оценки и выбора субподрядчиков, тщательного изучения логистической документации, приемочного контроля.
Управление процессами. Стандарт требует от поставщика определить и спланировать процессы производства, установки и технического обслуживания, которые непосредственно влияют на качество продукции.
Проверка и тестирование. Контроль качества — это подтверждение соответствия заданным требованиям к продукции, который включает в себя входной, промежуточный и окончательный контроль.
Корректирующие или предупреждающие действия. Поставщик должен разработать и поддерживать документированные процедуры применения корректирующих и предупреждающих действий.
Регистрация данных о качестве. Поставщик должен разработать и поддерживать документированные процедуры идентификации, сбора, индексации, доступа, подачи, хранения, обслуживания и удаления зарегистрированных данных о качестве.
Обучение персонала. Внедрение современного менеджмента качества требует высокой квалификации сотрудников компании, их высокой мотивации на качественную работу и приобретение знаний и навыков для обеспечения качества работы.
Обслуживание. Если послепродажное обслуживание продукции осуществляется по договору, необходимо разработать и поддерживать процедуры по обслуживанию и проверке продукции на соответствие установленным требованиям.
Статистические методы. Фактическое использование статистических методов для контроля и регулирования процессов признано полезным на всех без исключения этапах «цикла качества».
Гибкость
Создаваемая система качества должна учитывать специфику предприятия, его размер, структуру и организацию производства. Система качества должна быть гибкой, чтобы не вступать в противоречие с изменениями, которые могут стать необходимыми в будущем. При выборе варианта системы оценивается и интерпретируется каждый ее элемент.
ISO 9000 — это серия стандартов ISO, используемых при создании и совершенствовании систем менеджмента качества организаций. Серия стандартов на системы менеджмента качества была разработана Техническим комитетом Международной организации по стандартизации.
Стандарты серии ISO 9000, которые были приняты в качестве национальных стандартов более чем в 90 странах мира, применимы к любой организации, независимо от ее размера, формы собственности или сферы деятельности.
Сертификация проводится в соответствии с единственным в серии стандартом, содержащим требования: ISO 9001. ISO не сертифицирует на соответствие ISO 9001. существует двухступенчатая система подтверждения соответствия. Специально созданные испытательные организации (органы по сертификации) сертифицируют системы менеджмента качества отдельных организаций. Они, в свою очередь, аккредитованы национальными органами по аккредитации. Однако существуют и независимые системы аккредитации.
Соответствие требованиям и рекомендациям ISO 9001 свидетельствует о способности компании поддерживать стабильное качество и повышать эффективность работы. Кроме того, соответствие требованиям ISO 9001 свидетельствует об определенной надежности поставщика. С точки зрения многих западных и японских компаний, соответствие требованиям ISO 9001 — это минимальный уровень, позволяющий выйти на рынок. Сам сертификат ISO 9001 является внешним, независимым подтверждением того, что требования стандарта были выполнены.
Целью разработки стандартов серии ISO 9000 было стабильное функционирование документированной системы менеджмента качества компании-поставщика. Изначально стандарты серии ISO 9000 были ориентированы на отношения между заказчиком и поставщиком. С принятием в 2000 году следующей версии стандартов серии ISO 9000 больше внимания стало уделяться способности организации удовлетворять потребности всех заинтересованных сторон: Собственники, сотрудники, общество, клиенты и поставщики.
ISO 9000 является основополагающим стандартом, и его термины и определения используются во всех стандартах серии 9000. Настоящий стандарт обеспечивает основу для понимания основных элементов системы менеджмента качества в соответствии со стандартами ISO.
В России сертификация ISO проводится организациями, аккредитованными Федеральным агентством по техническому регулированию и метрологии.
В России новый стандарт ISO 9001:2000 признан национальным стандартом (ГОСТ) с 15 августа 2001 года, так что в настоящее время в Российской Федерации действует серия стандартов ГОСТ Р ИСО 9000 версии 2001 года, которая абсолютно идентична международному стандарту ISO 9001 версии 2000 года.
HACCP (Hazard Analysis and Critical Control Points) — это концептуально простая система, с помощью которой предприятия пищевой промышленности могут определить и оценить риски для безопасности производимых ими продуктов питания, внедрить необходимые технологические средства контроля для предотвращения рисков или поддержания их в приемлемых пределах, контролировать работу средств контроля и вести постоянный учет. HACCP в настоящее время признана наиболее эффективной системой обеспечения безопасности продуктов питания, поставляемых потребителям по всей стране.
Цели
Стандарт предназначен для достижения следующих целей:
- Повышение уверенности в безопасности продуктов питания и продовольственного сырья благодаря тому, что внедрение системы ХАССП полностью предотвращает или снижает до приемлемого уровня риски угрозы жизни и здоровью потребителей;
- Повысить стабильность качества пищевых продуктов и продовольственного сырья путем упорядочения и координации работы по управлению рисками при производстве, транспортировке, хранении и реализации на основе принципов ХАССП;
- Содействие международной торговле путем повышения доверия иностранных партнеров к компаниям, в которых действует международно признанная система HACCP;
- Содействие государственному контролю и надзору за соблюдением обязательных требований стандартов в процессе производства путем установления обоснованной номенклатуры контрольных точек в технологическом процессе и системы их мониторинга.
Основные требования к русской версии HACCP:
- учет применимых государственных стандартов и санитарных норм при выборе потенциально опасных факторов.
- учет источников информации, фактически доступных российским компаниям, при выборе опасностей, подлежащих учету.
- учет существующих традиционных систем производственного и санитарного контроля при выборе критических контрольных точек процесса.
- комплексный подход к управлению безопасностью продукции в рамках системы HACCP, включая систему надзора, корректирующих и предупреждающих действий.
- обучение специалистов компании проведению внутренних аудитов системы ХАССП.
- максимальная алгоритмизация экспертных решений при выборе критических контрольных точек.
Семь принципов ХАССП составляют основу окончательного свода правил.
Принцип 1: Для каждого процесса должен быть проведен анализ рисков. Цель анализа — выявить и перечислить риски возможного загрязнения пищевых продуктов, которые с достаточной степенью вероятности могут возникнуть в процессе производства конкретного продукта, и разработать превентивные меры, чтобы избежать возникновения риска.
Принцип 2: Необходимо определить критические контрольные точки на каждом этапе процесса.
Принцип 3: Должны быть определены критические пределы, при достижении которых необходимо предпринять действия для предотвращения развития рисков, связанных с определенными критическими контрольными точками.
Принцип 4: Должна быть установлена процедура мониторинга критических контрольных точек. Контроль является неотъемлемой частью HACCP и состоит из системы наблюдений и измерений.
Принцип 5: В плане HACCP должны быть указаны корректирующие действия, которые необходимо предпринять, если уровни критических контрольных точек выходят за установленные пределы.
Принцип 6: Необходимо разработать и внедрить эффективную процедуру регистрации для документирования организации и функционирования всей системы HACCP.
Принцип 7: Системы HACCP должны подвергаться систематическим аудитам.
Чтобы запустить систему HACCP, компания должна сначала создать план HACCP. Когда компания внедряет план HACCP, она устанавливает контроль на каждом этапе производственной системы, где могут возникнуть проблемы безопасности из-за биологических, химических или физических опасностей.
В качестве практической рекомендации для компаний, заинтересованных в данной работе, следует отметить, что разработка и внедрение системы ХАССП требует привлечения компетентных специалистов, как в области технологии производства продуктов питания, так и в области менеджмента качества и методологии ХАССП. Специалисты компании, в первую очередь команда HACCP, должны быть специально обучены.
ISO 10001:2007 Менеджмент качества — Удовлетворенность потребителей — Руководство по кодексам поведения для организаций. Стандарт содержит руководство по планированию, проектированию, разработке, внедрению, поддержанию и совершенствованию кодексов поведения для удовлетворения потребностей клиентов. Стандарт применим к связанным с продукцией кодексам, относящимся к содержанию обещаний, данных организацией потребителям, которые касаются ее поведения. Такие обещания и связанные с ними положения (условия) направлены на повышение удовлетворенности клиентов.
ISO 10001:2007 предназначен для использования любой организацией, независимо от типа, размера или поставляемой продукции, включая организации, разрабатывающие практические кодексы удовлетворенности клиентов для использования другими организациями.
На странице курсовые работы по менеджменту вы найдете много готовых тем для курсовых по предмету «Менеджмент».
Читайте дополнительные лекции:
- Экономическая оценка управления качеством
- Оптимизация продуктового портфеля на примере отдела закупки и сбыта предприятия
- Управление конфликтом как функция руководства
- Аудит структур организации
- Системный подход к менеджменту в предпринимательской деятельности
- Методы оптимальных решений
- Методология и методы исследования в менеджменте
- Менеджмент на автомобильном транспорте
- Жизненный цикл организационной структуры
- Лилиан Гилбрет, консультант по менеджменту