Оглавление:
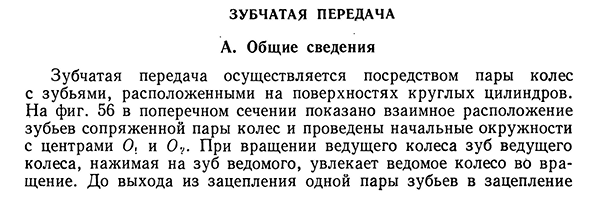
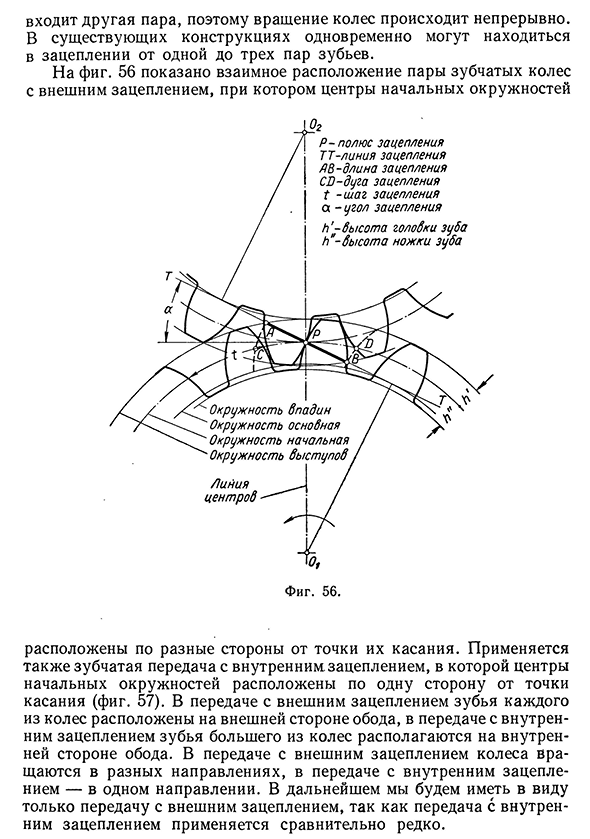
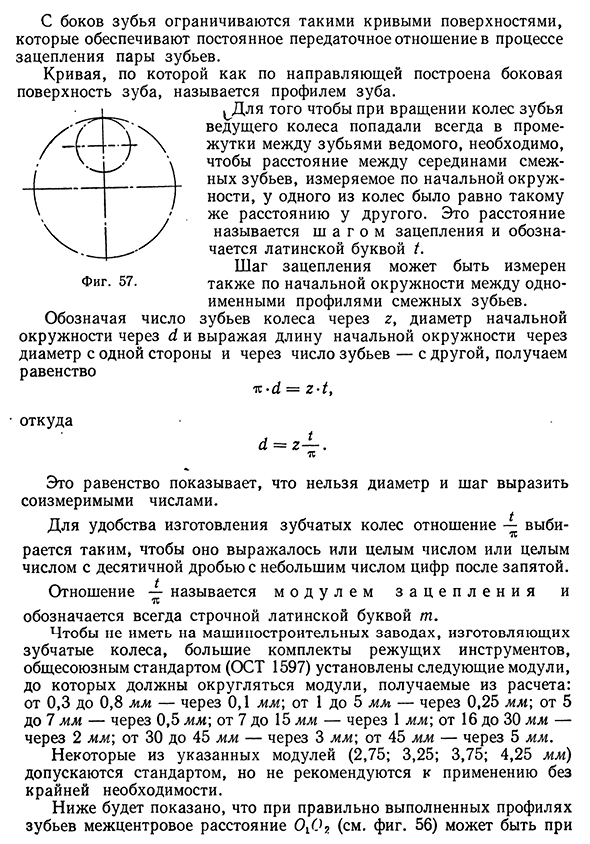
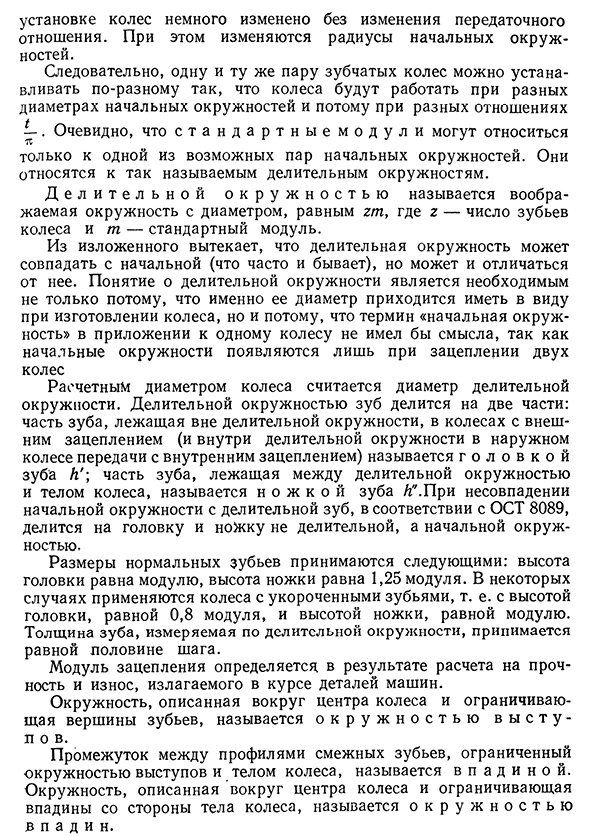
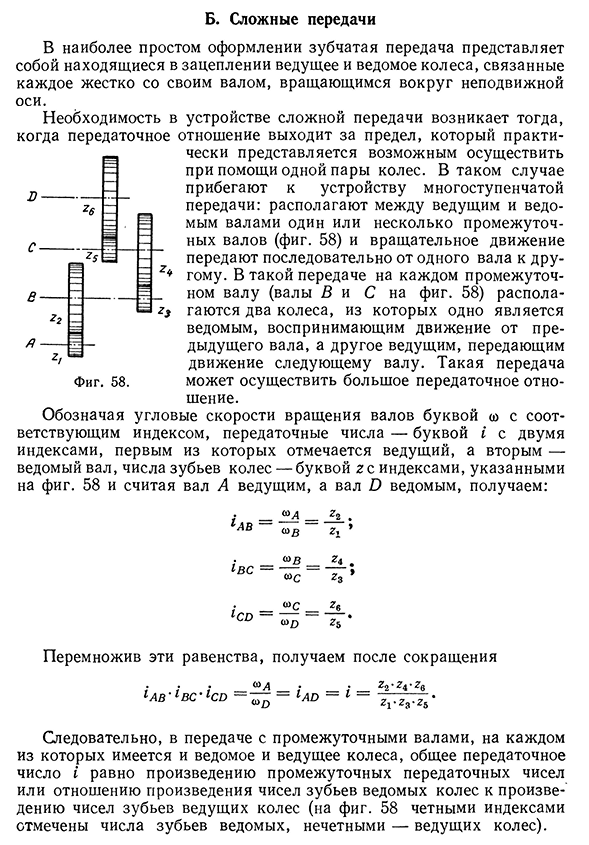
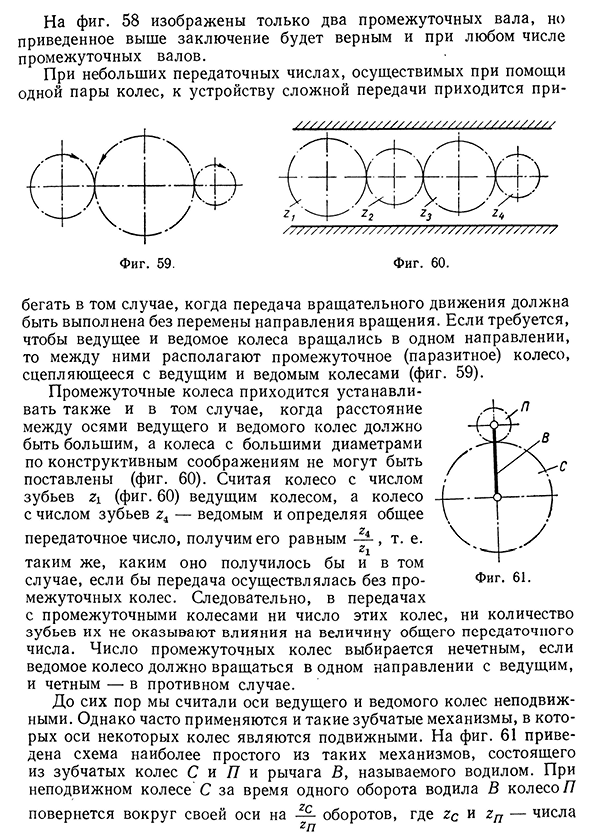
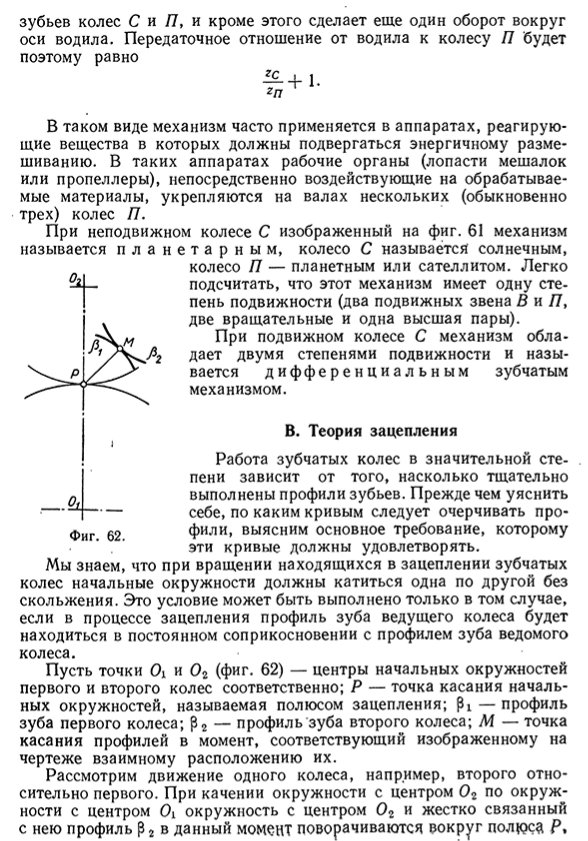
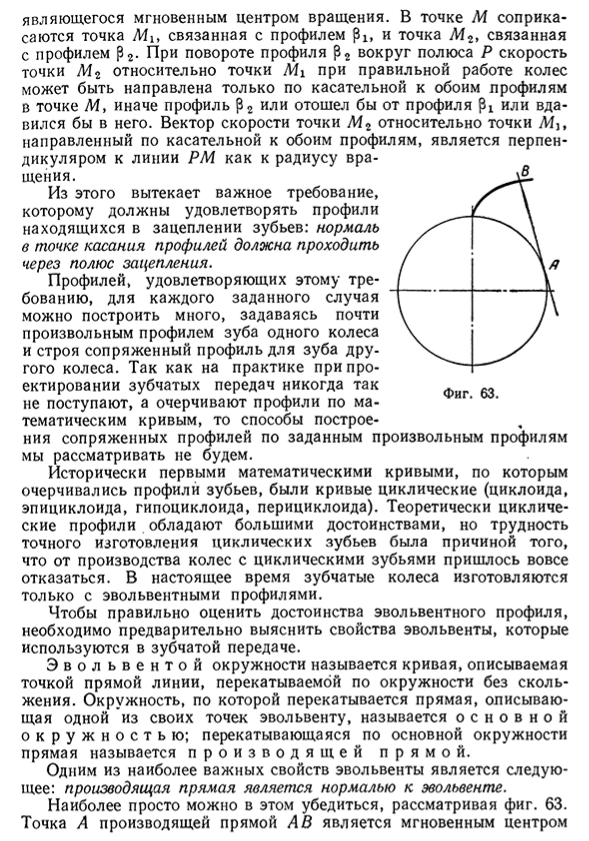
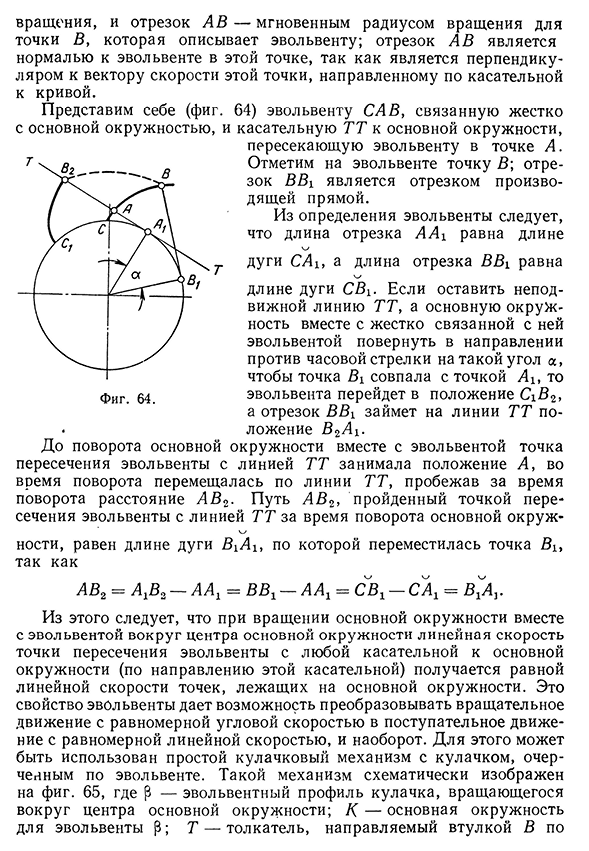
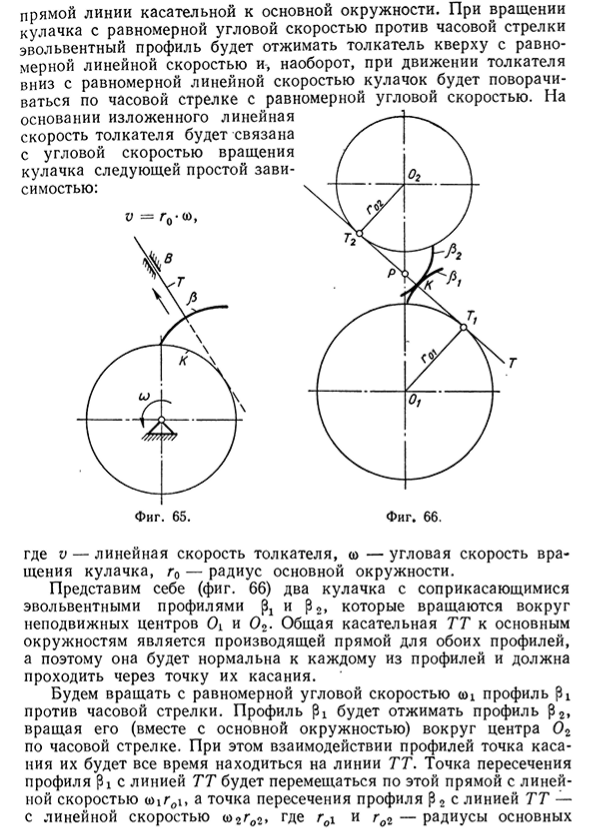
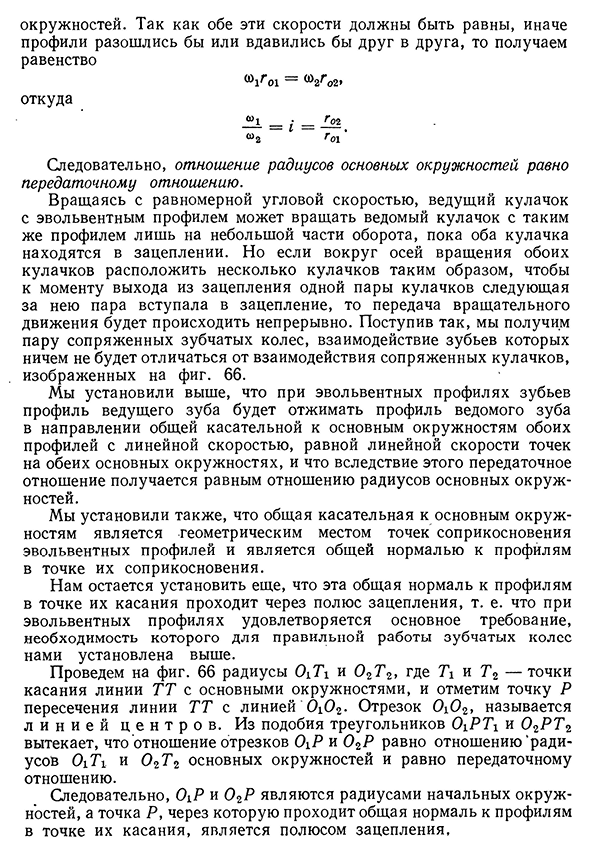
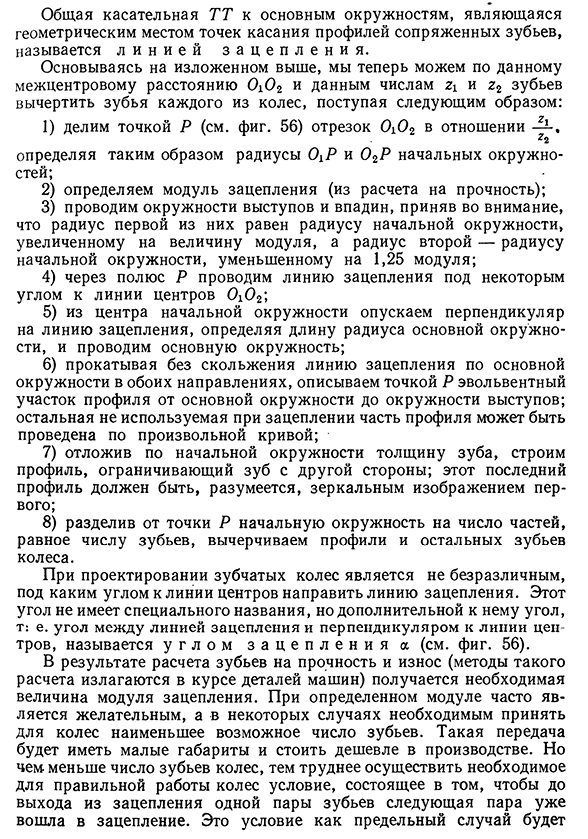
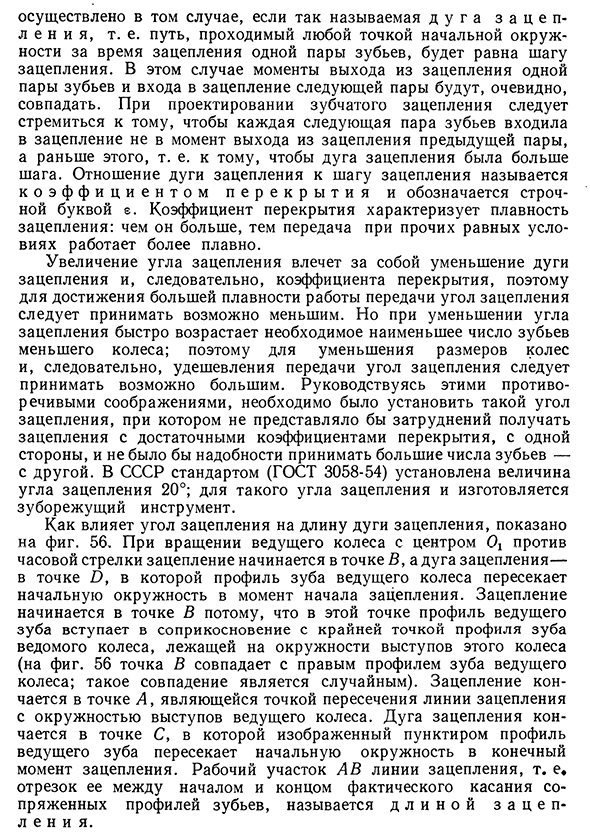
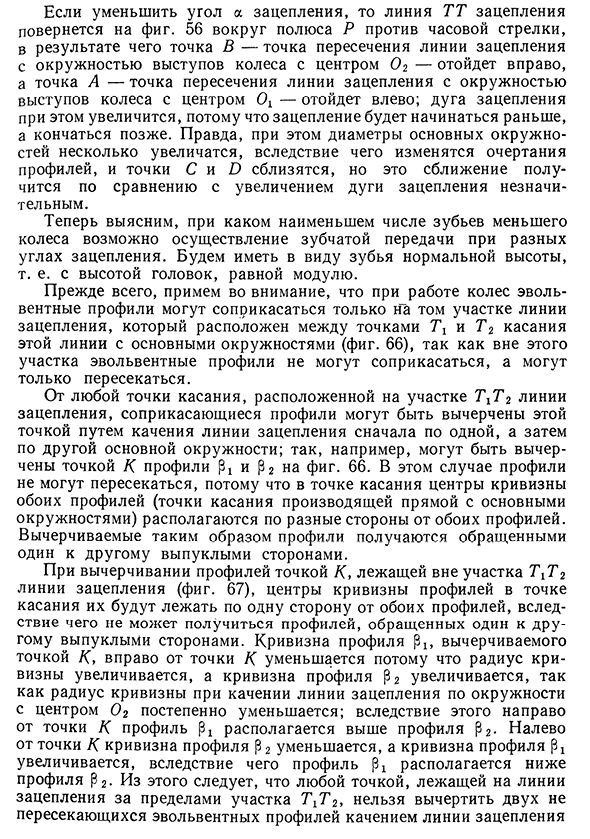
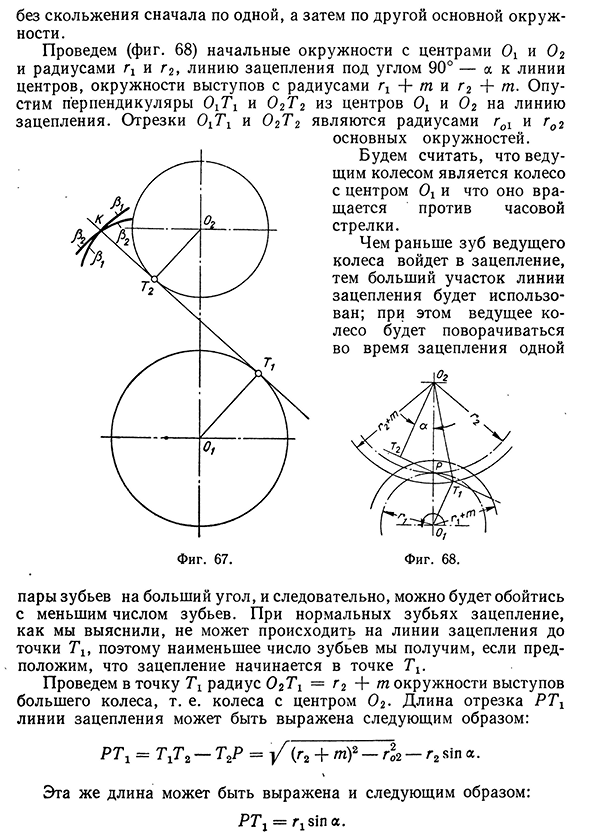
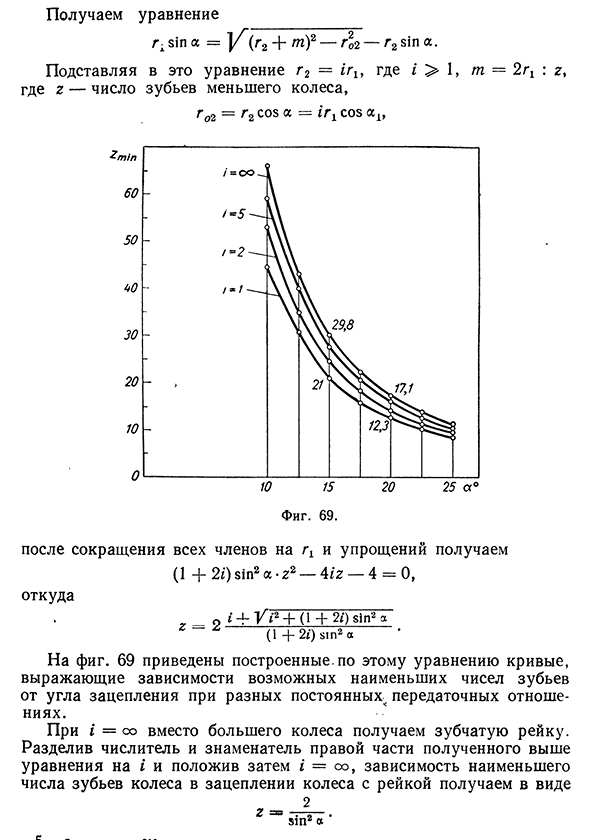
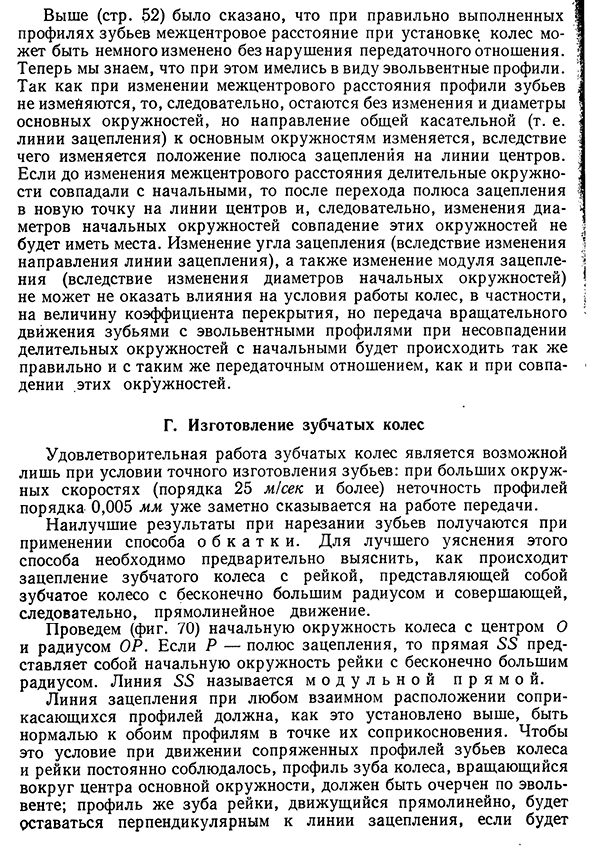
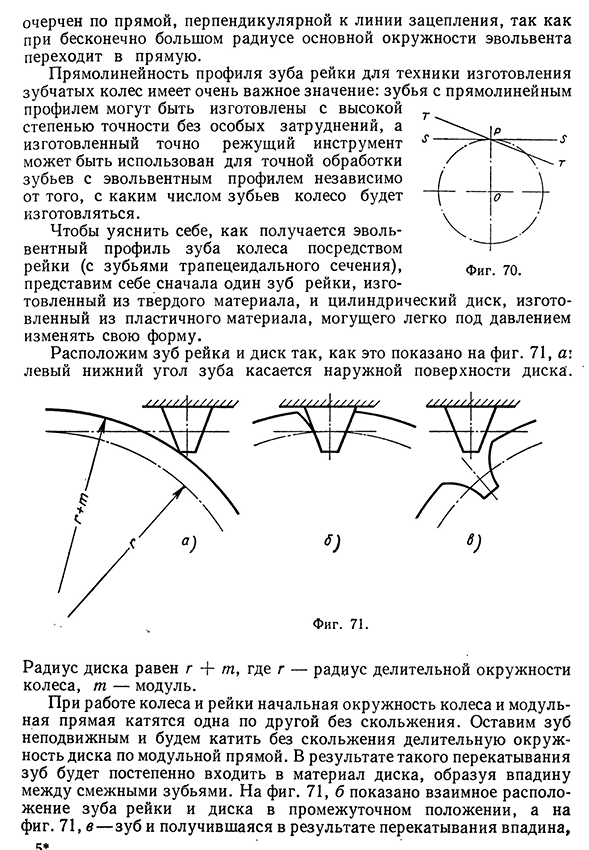
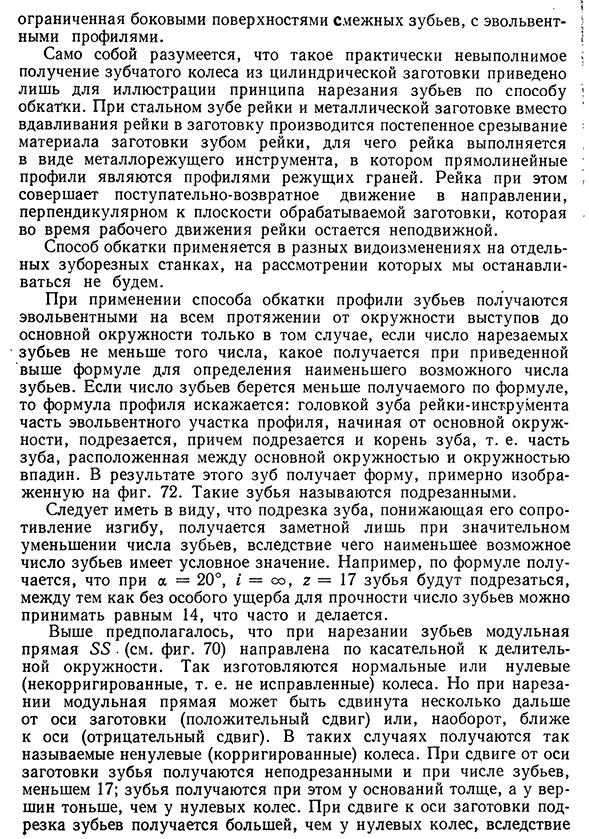
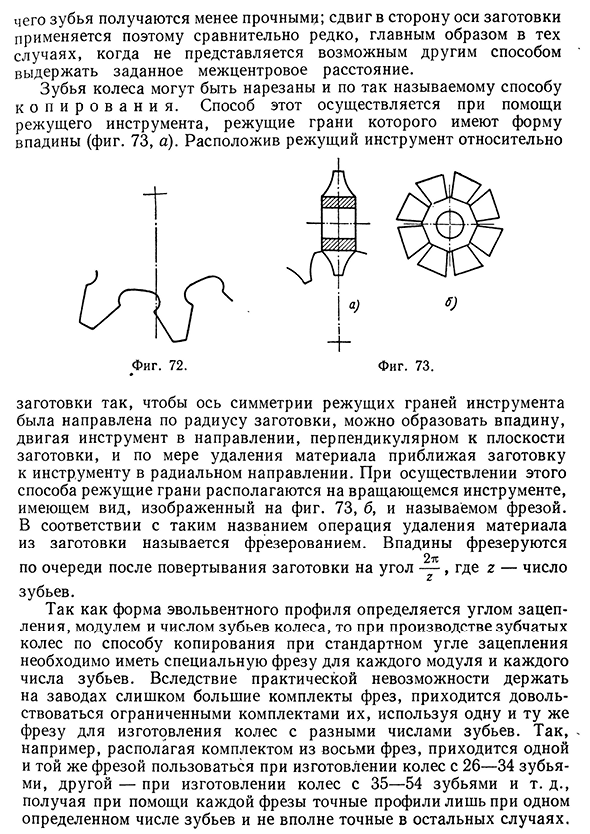
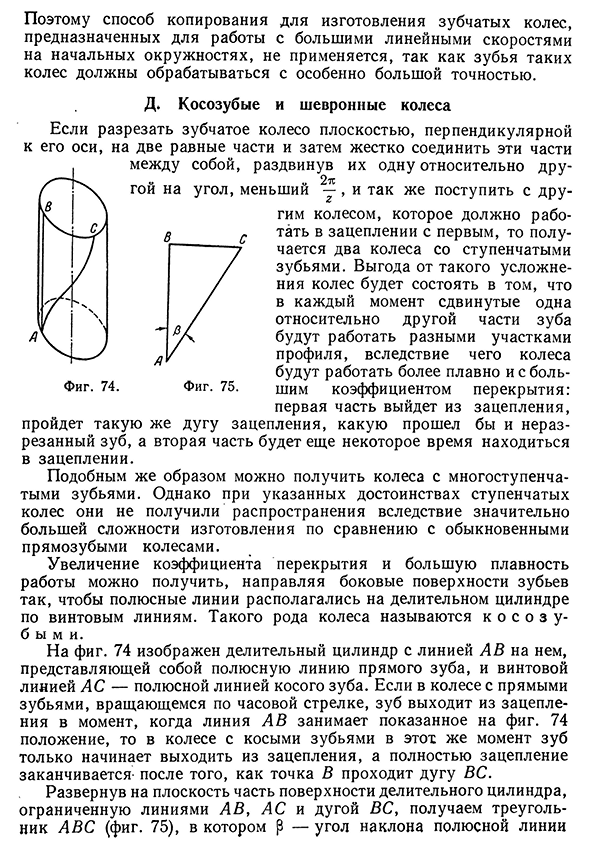
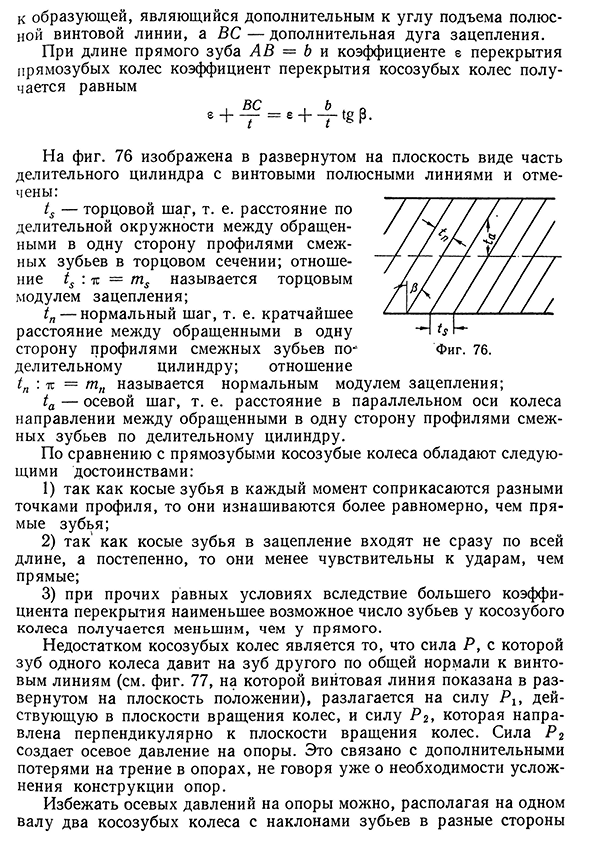
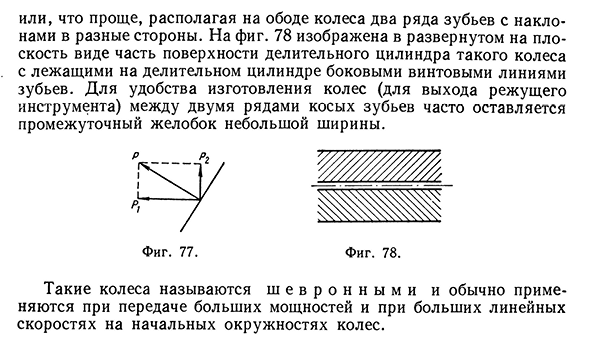

Зубчатая передача
- А. Общие сведения Зубчатая передача осуществляется посредством пары колес с зубьями, расположенными на поверхностях круглых цилиндров. На фиг. 56 в поперечном сечении показано взаимное расположение зубьев сопряженной пары колес и проведены начальные окружности с центрами О. и О?. При вращении ведущего колеса зуб ведущего колеса, нажимая на зуб ведомого, увлекает ведомое колесо во вращение. До выхода из зацепления одной пары зубьев в зацеплениеЗубчатая передача 51 входит другая пара, поэтому вращение колес происходит непрерывно. В существующих
конструкциях одновременно могут находиться в зацеплении от одной до трех пар зубьев. На фиг. 56 показано взаимное расположение пары зубчатых колес с внешним зацеплением, при котором центры начальных окружностей Линия центров P полюс зацепления ТТ-линия зацепления А В-длина зацепления СВ-дуга зацепления t -шаг зацепления а угол зацепления h ’-высота головки зуда h -высота ножки зуба Фиг. 56. Окружность впадин Окружность основная Окружность начальная Окружность выступов расположены по разные стороны от точки их касания. Применяется также зубчатая передача с внутренним, зацеплением,
в которой центры начальных окружностей расположены по одну сторону от точки касания (фиг. Людмила Фирмаль
57). В передаче с внешним зацеплением зубья каждого из колес расположены на внешней стороне обода, в передаче с внутренним зацеплением зубья большего из колес располагаются на внутренней стороне обода. В передаче с внешним зацеплением колеса вращаются в разных направлениях, в передаче с внутренним зацеплением — в одном направлении. В дальнейшем мы будем иметь в виду только передачу с внешним зацеплением, так как передача с внутренним зацеплением применяется сравнительно редко. 452 Плоские механизмы для передачи вращательного движения С боков зубья
ограничиваются такими кривыми поверхностями, которые обеспечивают постоянное передаточное отношение в процессе зацепления пары зубьев. Кривая, по которой как по направляющей построена боковая поверхность зуба, называется профилем зуба. ^Для того чтобы при вращении колес зубья ведущего колеса попадали всегда в промежутки между зубьями ведомого, необходимо, чтобы расстояние между серединами смежных зубьев, измеряемое по начальной окружности, у одного из колес было равно такому же расстоянию у другого. Это расстояние называется ш а г о м зацепления и обозначается латинской буквой t. Шаг зацепления может быть измерен также по начальной окружности между одноименными профилями смежных зубьев, Обозначая число зубьев колеса через г, диаметр начальной окружности через d и выражая длину начальной окружности через диаметр с одной стороны и через число зубьев — с другой, получаем равенство • откуда тс-d — Z-t, d = Это
- равенство показывает, что нельзя диаметр и шаг выразить соизмеримыми числами. Для удобства изготовления зубчатых колес отношение — выбирается таким, чтобы оно выражалось или целым числом или целым числом с десятичной дробью с небольшим числом цифр после запятой. Отношение ~ называется м о д у л е м з а ц е п л е н и я и обозначается всегда строчной латинской буквой пг. Чтобы не иметь на машиностроительных заводах, изготовляющих зубчатые колеса, большие комплекты режущих инструментов, общесоюзным стандартом (ОСТ 1597) установлены следующие модули, до которых должны округляться модули, получаемые из расчета: от 0,3 до 0,8 мм — через 0,1 мм; от 1 до 5 мм — через 0,25 мм; от 5 до 7 мм — через 0,5 мм; от 7 до 15 мм — через 1 мм; от 16 до 30 мм — через 2 мм; от 30 до 45 мм — через 3 мм; от 45 мм — через 5 мм. Некоторые из
указанных модулей (2,75; 3,25; 3,75; 4,25 мм) допускаются стандартом, но не рекомендуются к применению без крайней необходимости. Ниже будет показано, что при правильно выполненных профилях зубьев межцентровое расстояние O J)2 (см. фиг. 56) может быть приЗубчатая передача 53 установке колес немного изменено без изменения передаточного отношения. При этом изменяются радиусы начальных окружностей. Следовательно, одну и ту же пару зубчатых колес можно устанавливать по-разному так, что колеса будут работать при разных диаметрах начальных окружностей и потому при разных отношениях . Очевидно, что с т а н д а р т н ы е м о д у л и могут относиться только к одной из возможных пар начальных окружностей.
Они относятся к так называемым делительным окружностям. Д е л и т е л ь н о й о к р у ж Людмила Фирмаль
н о с т ь ю называется воображаемая окружность с диаметром, равным ztn, где z — число зубьев колеса и ш — стандартный модуль. Из изложенного вытекает, что делительная окружность может совпадать с начальной (что часто и бывает), но может и отличаться от нее. Понятие о делительной окружности является необходимым не только потому, что именно ее диаметр приходится иметь в виду при изготовлении колеса, но и потому, что термин «начальная окружность» в приложении к одному колесу не имел бы смысла, так как начальные окружности появляются лишь при зацеплении двух колес Расчетным диаметром колеса считается диаметр делительной окружности. Делительной окружностью зуб делится на две части: часть зуба, лежащая вне делительной
окружности, в колесах с внешним зацеплением (и внутри делительной окружности в наружном колесе передачи с внутренним зацеплением) называется г о л о в к о й зуба Л’; часть зуба, лежащая между делительной окружностью и телом колеса, называется н о ж к о й зуба Л».При несовпадении начальной окружности с делительной зуб, в соответствии с ОСТ 8089, делится на головку и но)кку не делительной, а начальной окружностью. Размеры нормальных зубьев принимаются следующими: высота головки равна модулю, высота ножки равна 1,25 модуля. В некоторых случаях применяются колеса с укороченными зубьями, т. е. с высотой головки, равной 0,8 модуля, и высотой ножки, равной модулю. Толщина зуба, измеряемая по делительной окружности, принимается равной половине шага.
Модуль зацепления определяется в результате расчета на прочность и износ, излагаемого в курсе деталей машин. Окружность, описанная вокруг центра колеса и ограничивающая вершины зубьев, называется о к р у ж н о с т ь ю в ы с т у п о в . Промежуток между профилями смежных зубьев, ограниченный окружностью выступов и телом колеса, называется в п а д и н о й . Окружность, описанная вокруг центра колеса и ограничивающая впадины со стороны тела колеса, называется о к р у ж н о с т ь ю в п а д и н .54 Плоские механизмы для передачи вращательного движения Б. Сложные передачи В наиболее простом оформлении зубчатая передача представляет собой находящиеся в зацеплении ведущее и ведомое колеса, связанные каждое жестко со своим валом, вращающимся вокруг неподвижной оси. Необходимость в устройстве сложной передачи возникает тогда,
когда передаточное отношение выходит за предел, которьй практически представляется возможным осуществить при помощи одной пары колес. В таком случае прибегают к устройству многоступенчатой передачи: располагают между ведущим и ведомым валами один или несколько промежуточных валов (фиг. 58) и вращательное движение передают последовательно от одного вала к другому. В такой передаче на каждом промежуточном валу (валы В и С на фиг. 58) располагаются два колеса, из которых одно является ведомым, воспринимающим движение от предыдущего вала, а другое ведущим, передающим движение следующему валу. Такая передача может осуществить большое передаточное отношение. Обозначая угловые скорости вращения валов буквой <о с соответствующим индексом, передаточные числа — буквой i с двумя индексами, первым из которых отмечается ведущий, а вторым — ведомый вал, числа
зубьев колес — буквой z с индексами, указанными на фиг. 58 и считая вал А ведущим, а вал D ведомым, получаем: i _ <В _ . <»С *3 ’ 1вс *5 Перемножив эти равенства, получаем после сокращения 21‘ г 3’г 5 Следовательно, в передаче с промежуточными валами, на каждом из которых имеется и ведомое и ведущее колеса, общее передаточное число i равно произведению промежуточных передаточных чисел или отношению произведения чисел зубьев ведомых колес к произведению чисел зубьев ведущих колес (на фиг. 58 четными индексами отмечены числа зубьев ведомых, нечетными — ведущих колес).Зубчатая передача 55 На фиг. 58 изображены только два
промежуточных вала, но приведенное выше заключение будет верным и при любом числе промежуточных валов. При небольших передаточных числах, осуществимых при помощи одной пары колес, к устройству сложной передачи приходится при/ / / / / / / / / / / / / / / / / / / / / / / / / / / / / / / / / / / / /7777777777777777777777777777777777777 Фиг. 60. бегать в том случае, когда передача вращательного движения должна быть выполнена без перемены направления вращения. Если требуется, чтобы ведущее и ведомое колеса вращались в одном направлении, то между ними располагают промежуточное (паразитное) колесо, сцепляющееся с ведущим и ведомым колесами (фиг. 59). Промежуточные колеса приходится устанавливать также и в том случае, когда расстояние между осями ведущего и ведомого колес должно быть большим, а колеса с большими диаметрами по
конструктивным соображениям не могут быть поставлены (фиг. 60). Считая колесо с числом зубьев (фиг. 60) ведущим колесом, а колесо с числом зубьев z4 — ведомым и определяя общее передаточное число, получим его равным — , т. е. z i таким же, каким оно получилось бы и в том случае, если бы передача осуществлялась без промежуточных колес. Следовательно, в передачах с промежуточными колесами ни число этих колес, ни количество зубьев их не оказывают влияния на величину общего передаточного числа. Число промежуточных колес выбирается нечетным, если ведомое колесо должно вращаться в одном направлении с ведущим, и четным — в противном случае. До сих пор мы считали оси ведущего и ведомого колес неподвижными. Однако часто применяются и такие зубчатые механизмы, в которых оси некоторых колес являются подвижными. На фиг. 61 приведена
схема наиболее простого из таких механизмов, состоящего из зубчатых колес С и 77 и рычага В, называемого водилом. При неподвижном колесе С за время одного оборота водила В колесо 77 повернется вокруг своей оси на оборотов, где хс и zn — числа г п56 Плоские механизмы для передачи вращательного движения зубьев колес С и 77, и кроме этого сделает еще один оборот вокруг оси водила. Передаточное отношение от водила к колесу 77 будет поэтому равно ^ + 1 . В таком виде механизм часто применяется в аппаратах, реагирующие вещества в которых должны подвергаться энергичному размешиванию. В таких аппаратах рабочие органы (лопасти мешалок или пропеллеры), непосредственно воздействующие на обрабатываемые материалы, укрепляются на валах нескольких (обыкновенно трех) колес 77. При неподвижном колесе С изображенный на фиг. 61 механизм называется п л а н е т а р н ы м , колесо С называется солнечным, колесо 77 — планетным или сателлитом. Легко подсчитать, что этот механизм имеет одну степень подвижности (два подвижных звена В и 77, две вращательные и одна
высшая пары). При подвижном колесе С механизм обладает двумя степенями подвижности и называется д и ф ф ер ен ц и ал ьн ы м зубчатым механизмом. Фиг. 62. В. Теория зацепления Работа зубчатых колес в значительной сте. пени зависит от того, насколько тщательно выполнены профили зубьев. Прежде чем уяснить себе, по каким кривым следует очерчивать профили, выясним основное требование, которому эти кривые должны удовлетворять. Мы знаем, что при вращении находящихся в зацеплении зубчатых колес начальные окружности должны катиться одна по другой без скольжения. Это условие может быть выполнено только в том случае, если в процессе зацепления профиль зуба ведущего колеса будет находиться в постоянном соприкосновении с профилем зуба ведомого колеса.
Пусть точки Oi и О2 (фиг. 62) — центры начальных окружностей первого и второго колес соответственно; Р — точка касания начальных окружностей, называемая полюсом зацепления; pi — профиль зуба первого колеса; р2 — профиль зуба второго колеса; М — точка касания профилей в момент, соответствующий изображенному на чертеже взаимному расположению их. Рассмотрим движение одного колеса, например, второго относительно первого. При качении окружности с центром О2 по окружности с центром Oi окружность с центром 02 и жестко связанный с нею профиль р 2 в данный момент поворачиваются вокруг подноса Р,Зубчатая передача 57 являющегося мгновенным центром вращения. В точке М соприкасаются точка 7И1, связанная с профилем рх, и точка М 2, связанная с профилем р2. При повороте профиля ₽2 вокруг полюса Р скорость точки ТИ2
относительно точки 7И1 при правильной работе колес может быть направлена только по касательной к обоим профилям в точке М, иначе профиль ₽2 или отошел бы от профиля рх или вдавился бы в него. Вектор скорости точки ТИ2 относительно точки Mi9 направленный по касательной к обоим профилям, является перпендикуляром к линии РМ как к радиусу вращения. Из этого вытекает важное требование, которому должны удовлетворять профили находящихся в зацеплении зубьев: нормаль в точке касания профилей должна проходить через полюс зацепления. Профилей, удовлетворяющих этому требованию, для каждого заданного случая можно построить много, задаваясь почти произвольным профилем зуба одного колеса и строя сопряженный профиль для зуба другого колеса. Так как на практике при проектировании зубчатых передач никогда так не поступают, а очерчивают профили по математическим кривым, то способы построения сопряженных
профилей по заданным произвольным профилям мы рассматривать не будем. Исторически первыми математическими кривыми, по которым очерчивались профили зубьев, были кривые циклические (циклоида, эпициклоида, гипоциклоида, перициклоида). Теоретически циклические профили обладают большими достоинствами, но трудность точного изготовления циклических зубьев была причиной того, что от производства колес с циклическими зубьями пришлось вовсе отказаться. В настоящее время зубчатые колеса изготовляются только с эвольвентными
профилями. Чтобы правильно оценить достоинства эвольвентного профиля, необходимо предварительно выяснить свойства эвольвенты, которые используются в зубчатой передаче. Э в о л ь в е н т о й окружности называется кривая, описываемая точкой прямой линии, перекатываемой по окружности без скольжения. Окружность, по которой перекатывается прямая, описывающая одной из своих точек эвольвенту, называется о с н о в н о й о к р у ж н о с т ь ю ; перекатывающаяся по основной окружности прямая называется п р о и з в о д я щ е й п р я м о й . Одним из наиболее важных свойств эвольвенты является следующее: производящая прямая является нормалью к эвольвенте. Наиболее просто можно в этом убедиться,
рассматривая фиг. 63. Точка А производящей прямой АВ является мгновенным центром58 Плоские механизмы для передачи вращательного движения вращения, и отрезок АВ — мгновенным радиусом вращения для точки В, которая описывает эвольвенту; отрезок А В является нормалью к эвольвенте в этой точке, так как является перпендикуляром к вектору скорости этой точки, направленному по касательной к кривой. Представим себе (фиг. 64) эвольвенту С А В, связанную жестко с основной окружностью, и касательную Т Т к основной окружности, пересекающую эвольвенту в точке А. Отметим на эвольвенте точку В; отрезок В Bi является отрезком производящей прямой. Из определения эвольвенты следует
, что длина отрезка А А г равна длине дуги CAi, а длина отрезка ВВГ равна длине дуги CBi. Если оставить неподвижной линию ТТ, а основную окружность вместе с жестко связанной с ней эвольвентой повернуть в направлении против часовой стрелки на такой угол а, чтобы точка Bi совпала с точкой Дх, то эвольвента перейдет в положение СХВ2 , а отрезок ВВХ займет на линии Т Т положение В2Д1. окружности вместе с эвольвентой ТТ занимала положение линии ТТ, пробежав за ДВ2, пройденный точкой время поворота основной окруж-по которой переместилась точка До поворота основной пересечения эвольвенты с линией время поворота перемещалась по поворота расстояние Л В2 . Путь сечения эвольвенты с линией Т Т за ности, равен длине дуги B iA i, так как АВ2 = А1В2 — АА± = ВВг — ААХ = СВ1 — СА± = ВХЛГ точка А, во время переИз этого следует, что при вращении основной окружности вместе с эвольвентой вокруг центра основной окружности линейная скорость точки пересечения эвольвенты с любой касательной к основной окружности (по
скорости точек, лежащих на основной окружности. Это свойство эвольвенты дает возможность преобразовывать вращательное движение с равномерной угловой скоростью в поступательное движение с равномерной линейной скоростью, и наоборот. Для этого может быть использован простой кулачковый механизм с кулачком, очерченным по эвольвенте. Такой механизм схематически изображен на фиг. 65, где ₽ — эвольвентный профиль кулачка, вращающегося вокруг центра основной окружности; /С — основная окружность для эвольвенты р; Т — толкатель, направляемый втулкой В поЗубчатая передача 59 прямой линии касательной к основной окружности. При вращении кулачка с равномерной угловой скоростью против часовой стрелки эвольвентный профиль будет отжимать толкатель кверху с равномерной линейной скоростью и-, наоборот, при движении
толкателя вниз с равномерной линейной скоростью кулачок будет поворачиваться по часовой стрелке с равномерной угловой скоростью. На где v — линейная скорость толкателя, <о — угловая скорость вращения кулачка, г0 — радиус основной окружности. Представим себе (фиг. 66) два кулачка с соприкасающимися эвольвентными профилями и р2, которые вращаются вокруг неподвижных центров Oj. и О2. Общая касательная ТТ к основным окружностям является производящей прямой для обоих профилей, а поэтому она будет нормальна к каждому из профилей и должна проходить через точку их касания. Будем вращать с равномерной угловой скоростью 1, m = 2гх : z, где г — число зубьев меньшего колеса, Го2 = Г2 cos а = l r xcos ai> после сокращения всех членов на гх
и упрощений получаем (1 + 2/) sin2 а • z2 — 4/z — 4 = О, откуда _ о * + “И2 + 0 + 2) sin2 а (1 + 2Z) sin2 а На фиг. 69 приведены построенные, по этому уравнению кривые, выражающие зависимости возможных наименьших чисел зубьев от угла зацепления при разных постоянных передаточных отношениях. При i — оо вместо большего колеса получаем зубчатую рейку. Разделив числитель и знаменатель правой части полученного выше уравнения на i и положив затем i = со, зависимость наименьшего числа зубьев колеса в зацеплении колеса с рейкой получаем в виде 2 Z 30 sin2 а ’ 5 Зиновьев 61266 Плоские механизмы для передачи вращательного движения Выше (стр. 52) было сказано, что при правильно выполненных профилях зубьев межцентровое расстояние при установке колес может быть
немного изменено без нарушения передаточного отношения. Теперь мы знаем, что при этом имелись в виду эвольвентные профили. Так как при изменении межцентрового расстояния профили зубьев не измейяются, то, следовательно, остаются без изменения и диаметры основных окружностей, но направление общей касательной (т. е. линии зацепления) к основным окружностям изменяется, вследствие чего изменяется положение полюса зацепления на линии центров. Если до изменения межцентрового расстояния делительные окружности совпадали с начальными, то после перехода полюса зацепления в новую точку на линии центров и, следовательно, изменения диаметров начальных окружностей совпадение этих окружностей не будет иметь места. Изменение угла зацепления (вследствие изменения направления линии зацепления), а также изменение модуля зацепления (вследствие изменения диаметров начальных окружностей) не может не оказать влияния на условия
работы колес, в частности, на величину коэффициента перекрытия, но передача вращательного движения зубьями с эвольвентными профилями при несовпадении делительных окружностей с начальными будет происходить так же правильно и с таким же передаточным отношением, как и при совпадении этих окружностей. Г. Изготовление зубчатых колес Удовлетворительная работа зубчатых колес является возможной лишь при условии точного изготовления зубьев: при больших окружных скоростях (порядка 25 м/сек и более) неточность профилей порядка 0,005 мм уже заметно сказывается на работе передачи. Наилучшие результаты при нарезании зубьев
получаются при применении способа о б к а т к и . Для лучшего уяснения этого способа необходимо предварительно выяснить, как происходит зацепление зубчатого колеса с рейкой, представляющей собой зубчатое колесо с бесконечно большим радиусом и совершающей, следовательно, прямолинейное движение. Проведем (фиг. 70) начальную окружность колеса с центром О и радиусом ОР. Если Р — полюс зацепления, то прямая SS представляет собой начальную окружность рейки с бесконечно большим радиусом. Линия SS называется м о д у л ь н о й п р я м о й . Линия зацепления при любом взаимном расположении соприкасающихся профилей
должна, как это установлено выше, быть нормалью к обоим профилям в точке их соприкосновения. Чтобы это условие при движении сопряженных профилей зубьев колеса и рейки постоянно соблюдалось, профиль зуба колеса, вращающийся вокруг центра основной окружности, должен быть очерчен по эвольвенте; профиль же зуба рейки, движущийся прямолинейно, будет оставаться перпендикулярным к линии зацепления, если будетЗубчатая передача 67 очерчен по прямой, перпендикулярной к линии зацепления, так как при бесконечно большом радиусе основной окружности эвольвента переходит в прямую. Прямолинейность профиля зуба рейки для техники изготовления зубчатых колес имеет очень важное значение: зубья с прямолинейным профилем могут быть изготовлены с высокой степенью точности без особых
затруднений, а изготовленный точно режущий инструмент может быть использован для точной обработки зубьев с эвольвентным профилем независимо от того, с каким числом зубьев колесо будет изготовляться. Чтобы уяснить себе, как получается эвольвентный профиль зуба колеса посредством рейки (с зубьями трапецеидального сечения), представим себе сначала один зуб рейки, изготовленный из твердого материала, и цилиндрический диск, изготовленный из пластичного материала, могущего легко под давлением изменять свою форму. Расположим зуб рейки и диск так, как это показано на фиг. 71, ал левый нижний угол зуба касается наружной поверхности диска. Фиг. 71. Радиус диска равен г + т, где г — радиус делительной окружности колеса, т — модуль. При работе колеса и рейки начальная окружность колеса и модульная прямая катятся одна по другой без скольжения. Оставим зуб неподвижным и будем катить без скольжения делительную окружность диска по модульной прямой. В результате такого перекатывания зуб будет постепенно входить в
материал диска, образуя впадину между смежными зубьями. На фиг. 71, б показано взаимное расположение зуба рейки и диска в промежуточном положении, а на фиг. 71, в— зуб и получившаяся в результате перекатывания впадина, 568 Плоские механизмы для передачи вращательного движения ограниченная боковыми поверхностями смежных зубьев, с эвольвентj ными профилями. I Само собой разумеется, что такое практически невыполнимое ; получение зубчатого колеса из цилиндрической заготовки приведено лишь для иллюстрации принципа нарезания зубьев по способу i обкатки. При стальном зубе рейки и металлической заготовке вместо вдавливания рейки в заготовку производится постепенное срезывание материала заготовки зубом рейки, для чего рейка
выполняется в виде металлорежущего инструмента, в котором прямолинейные профили являются профилями режущих граней. Рейка при этом • совершает поступательно-возвратное движение в направлении, перпендикулярном к плоскости обрабатываемой заготовки, которая во время рабочего движения рейки остается неподвижной. Способ обкатки применяется в разных видоизменениях на отдельных зуборезных станках, на рассмотрении которых мы останавливаться не будем. При применении способа обкатки профили зубьев получаются эвольвентными на всем протяжении от окружности выступов до основной окружности только в том случае, если число нарезаемых зубьев не меньше того числа, какое получается при приведенной выше формуле для определения наименьшего возможного числа зубьев. Если число зубьев берется меньше
получаемого по формуле, то формула профиля искажается: головкой зуба рейки-инструмента часть эвольвентного участка профиля, начиная от основной окружности, подрезается, причем подрезается и корень зуба, т. е. часть зуба, расположенная между основной окружностью и окружностью впадин. В результате этого зуб получает форму, примерно изображенную на фиг. 72. Такие зубья называются подрезанными. Следует иметь в виду, что подрезка зуба, понижающая его сопротивление изгибу, получается заметной лишь при значительном уменьшении числа зубьев, вследствие чего наименьшее возможное число зубьев имеет условное значение.
Например, по формуле получается, что при а = 20°, / = оо, z = 17 зубья будут подрезаться, между тем как без особого ущерба для прочности число зубьев можно принимать равным 14, что часто и делается. Выше предполагалось, что при нарезании зубьев модульная прямая SS . (см. фиг. 70) направлена по касательной к делительной окружности. Так изготовляются нормальные или нулевые (некорригированные, т. е. не исправленные) колеса. Но при нарезании модульная прямая может быть сдвинута несколько дальше от оси заготовки (положительный сдвиг) или, наоборот, ближе к оси (отрицательный сдвиг). В таких случаях получаются так называемые ненулевые (корригированные) колеса. При сдвиге от оси заготовки зубья получаются неподрезанными и при числе зубьев, меньшем 17; зубья получаются при этом у оснований толще, а у вершин тоньше, чем у
нулевых колес. При сдвиге к оси заготовки подрезка зубьев получается большей, чем у нулевых колес, вследствиеЗубчатая передача 69 чего зубья получаются менее прочнымц; сдвиг в сторону оси заготовки применяется поэтому сравнительно редко, главным образом в тех случаях, когда не представляется возможным другим способом выдержать заданное межцентровое расстояние. Зубья колеса могут быть нарезаны и по так называемому способу к о п и р о в а н и я . Способ этот осуществляется при помощи режущего инструмента, режущие грани которого имеют форму впадины (фиг. 73, а). Расположив режущий инструмент относительно i Фиг. 73. т заготовки так, чтобы ось симметрии режущих граней инструмента была направлена по радиусу заготовки, можно образовать впадину, двигая инструмент в направлении, перпендикулярном к плоскости заготовки, и по мере удаления материала приближая заготовку к
инструменту в радиальном направлении. При осуществлении этого способа режущие грани располагаются на вращающемся инструменте, имеющем вид, изображенный на фиг. 73, б, и называемом фрезой. В соответствии с таким названием операция удаления материала из заготовки называется фрезерованием. Впадины фрезеруются по очереди после повертывания заготовки на угол — , где z — число зубьев. Так как форма эвольвентного профиля определяется углом зацепления, модулем и числом зубьев колеса, то при производстве зубчатых колес по способу копирования при стандартном угле зацепления необходимо иметь специальную фрезу для каждого модуля и каждого числа зубьев. Вследствие практической невозможности держать на заводах слишком большие комплекты фрез, приходится довольствоваться ограниченными
комплектами их, используя одну и ту же фрезу для изготовления колес с разными числами зубьев. Так, например, располагая комплектом из восьми фрез, приходится одной и той же фрезой пользоваться при изготовлении колес с 26—34 зубьями, другой — при изготовлении колес с 35—54 зубьями и т. д., получая при помощи каждой фрезы точные профили лишь при одном определенном числе зубьев и не вполне точные в остальных случаях.70 Плоские механизмы для передачи вращательного движения Поэтому способ копирования для изготовления зубчатых колес, предназначенных для работы с большими линейными скоростями на начальных окружностях, не применяется, так как зубья таких колес должны обрабатываться с
особенно большой точностью. между гой на Д. Косозубые и шевронные колеса Если разрезать зубчатое колесо плоскостью, перпендикулярной к его оси, на две равные части и затем жестко соединить эти части собой, раздвинув их одну относительно друо угол, меньшии — , и так же поступить с другим колесом, которое должно работать в зацеплении с первым, то получается два колеса со ступенчатыми зубьями. Выгода от такого усложнения колес будет состоять в том, что в каждый момент сдвинутые одна относительно другой части зуба будут работать разными участками профиля, вследствие чего колеса будут работать более плавно и с большим коэффициентом перекрытия: первая часть выйдет из зацепления, пройдет такую же дугу зацепления, какую
прошел бы и неразрезанный зуб, а вторая часть будет еще некоторое время находиться в зацеплении. Подобным же образом можно получить колеса с многоступенчатыми зубьями. Однако при указанных достоинствах ступенчатых колес они не получили распространения вследствие значительно большей сложности изготовления по сравнению с обыкновенными прямозубыми колесами. Увеличение коэффициента перекрытия и большую плавность работы можно получить, направляя боковые поверхности зубьев так, чтобы полюсные линии располагались на делительном цилиндре по винтовым линиям. Такого рода колеса называются к о с о з уб ы м и. На фиг. 74 изображен делительный цилиндр с линией АВ на нем, представляющей собой полюсную линию прямого зуба, и винтовой
линией А С — полюсной линией косого зуба. Если в колесе с прямыми зубьями, вращающемся по часовой стрелке, зуб выходит из зацепления в момент, когда линия А В занимает показанное на фиг. 74 положение, то в колесе с косыми зубьями в этот же момент зуб только начинает выходить из зацепления, а полностью зацепление заканчиваетсяпосле того, как точка В проходит дугу ВС. Развернув на плоскость часть поверхности делительного цилиндра, ограниченную линиями А В , А С и дугой В С, получаем треугольник А В С (фиг. 75), в котором р — угол наклона полюсной линииЗубчатая передача 71 к образующей, являющийся дополнительным к углу подъема полюсной винтовой линии, а ВС — дополнительная дуга зацепления. При длине прямого зуба АВ = Ь и коэффициенте в перекрытия прямозубых колес коэффициент перекрытия косозубых колес получается равным е + — = е + — tgp. часть отмена фиг. 76 изображена в развернутом на
плоскость виде делительного цилиндра с винтовыми полюсными линиями и чены: ts — торцовой шаг, т. е. расстояние по делительной окружности между обращенными в одну сторону профилями смежных зубьев в торцовом сечении; отношение ts : тс = ms называется торцовым модулем зацепления; tn — нормальный шаг, т. е. кратчайшее расстояние между обращенными в одну сторону профилями смежных зубьев по делительному цилиндру; отношение tn : tz = mn называется нормальным модулем зацепления; ta — осевой шаг, т. е. расстояние в параллельном оси колеса направлении между обращенными в одну сторону профилями смежных зубьев по делительному цилиндру. По сравнению с прямозубыми косозубые колеса обладают следующими достоинствами: 1) так как косые зубья
в каждый момент соприкасаются разными точками профиля, то они изнашиваются более равномерно, чем прямые зубья; 2) так как косые зубья в зацепление входят не сразу по всей длине, а постепенно, то они менее чувствительны к ударам, чем прямые; 3) при прочих равных условиях вследствие большего коэффициента перекрытия наименьшее возможное число зубьев у косозубого колеса получается меньшим, чем у прямого. Недостатком косозубых колес является то, что сила Р, с которой зуб одного колеса давит на зуб другого по общей нормали к винтовым линиям (см. фиг. 77, на которой винтовая линия показана в развернутом на плоскость положении), разлагается на силу Plf действующую в плоскости вращения колес, и силу Р2, которая направлена перпендикулярно к плоскости вращения колес. Сила Р 2 создает осевое давление на опоры. Это связано с дополнительными
потерями на трение в опорах, не говоря уже о необходимости усложнения конструкции опор. Избежать осевых давлений на опоры можно, располагая на одном валу два косозубых колеса с наклонами зубьев в разные стороны72 Плоские механизмы для передачи вращательного движения или, что проще, располагая на ободе колеса два ряда зубьев с наклонами в разные стороны. На фиг. 78 изображена в развернутом на плоскость виде часть поверхности делительного цилиндра такого колеса с лежащими на делительном цилиндре боковыми винтовыми линиями зубьев. Для удобства изготовления колес (для выхода режущего инструмента) между двумя рядами косых зубьев часто оставляется промежуточный желобок небольшой ширины. Фиг. 78. Такие колеса называются ш е в р о н н ы м и и обычно применяются при передаче больших мощностей и при больших линейных скоростях на начальных окружностях колес.
Смотрите также:
Предмет Теория Машин и Механизмов ТММ
Плоские механизмы для передачи вращательного движения общие сведения | Кинематическая пара |
Фрикционная передача | Классификация кинематических пар |