Оглавление:
В настоящее время качество из вторичного фактора становится важнейшим условием успешной работы предприятий и восстановления экономики страны в целом. Поэтому, как бы трудно ни было, но чтобы выжить на рынке, компании должны постоянно решать проблемы, связанные с обеспечением необходимого качества продукции.
Обеспечение качества всегда было одной из самых сложных задач при производстве продукции и предоставлении услуг. Эффективным средством успешного решения данной проблемы является внедрение положений международной серии стандартов ISO 9000, которые содержат только стандартизированные элементы доказательств обеспечения качества и рекомендации по созданию системы качества.
Но помимо этого, система качества должна быть основана на новой философии качества, новой культуре производства, которая полностью зависит от воли и желания менеджера компании, а также от традиций и опыта, которые он должен создавать, сохранять и развивать лучшее из прошлого.
Первые стандарты систем качества, названные BS 5750, были разработаны Британским институтом стандартов и приняты в 1979 году. Впоследствии эти стандарты были приняты Международной организацией по стандартизации в качестве основы для первой версии серии стандартов ИСО 9000, принятой в 1987 году. Вторая версия с незначительными изменениями была принята ИСО в 1994 году. Третья версия стандартов была опубликована 15 декабря 2000 года.
Стандарты ИСО, как правило, носят рекомендательный характер, но документы серии ИСО 9000 были приняты в качестве национальных стандартов более чем в 90 странах, включая США, Россию, Канаду, Японию, государства-члены ЕС и многие развивающиеся страны. Сертификация сторонних организаций на соответствие этим стандартам проводится более чем в 40 странах мира.
Международные стандарты серии ISO 9000 определяют требования в области менеджмента качества и обеспечения качества и являются основополагающими для формирования и функционирования системы качества в компании.
Соответствие системы качества предприятия международному стандарту ISO 9000 является обязательным условием подтверждения его надежности как поставщика продукции стабильного качества.
Международная организация по стандартизации (ИСО), основанная в 1946 году, разработала более 9300 конкретных стандартов.
В 1987 году была принята первая версия универсального стандарта ИСО 9000 для организации систем менеджмента качества, которая сразу же привлекла внимание мировой общественности. ISO 9000 основан на стандартах системы качества BS-5750, разработанных Британским институтом стандартов (BSI) и принятых в 1979 году.
Серия стандартов ISO 9000 описывает модель, в соответствии с которой система менеджмента предприятия разрабатывается с позиции обеспечения качества. Важной особенностью стандартов ISO 9000 является их универсальность для каждой сферы бизнеса, каждой компании — от крупного производственного холдинга до малого предприятия.
В 1987 году ИСО опубликовало пять стандартов ИСО (ИСО 9000-87, ИСО 9001-87, ИСО 9002-87, ИСО 9003-87, ИСО 9004-87) и глоссарий терминов по обеспечению качества (ИСО 8402-86).
Следующая версия серии стандартов ИСО 9000 появилась в 1994 году и по существу повторила структуру версии 1987 года, удалив и расшифровав некоторые непонятные моменты. 15 декабря 2000 года была опубликована последняя версия серии международных стандартов ISO 9000 (ISO 9000:2000), официально заменившая стандарты, принятые в 1994 году. В настоящее время стандарт ISO 9001:2000 заменяет стандарты ISO 9001, ISO 9002, ISO 9003 предыдущей версии, что имеет ряд существенных отличий. Например, набор документов, который раньше состоял из 24 стандартов, теперь включает 5 основных стандартов:
- Система менеджмента качества ISO 9000:2000. Основные принципы и словарь.
- Система менеджмента качества ISO 9001:2000. Требования.
- ISO9004:2000 Система менеджмента качества. Руководящие принципы по улучшению.
- ISO19011:2000 Руководство по проверке систем менеджмента качества и охраны окружающей среды.
- ISO 10012 Гарантия качества измерительного оборудования.
Одним из сильнейших двигателей распространения стандартов ИСО является Европейский экономический союз (ЕС). В частности, в Договоре об учреждении ЕС 1992 года содержится положение о принятии ISO 9000 в качестве основного стандарта для использования в международной торговле. В России аутентичный стандарт ИСО 9001:2000 (стандарт серии ИСО 9000) версии 2000 ГОСТ Р ИСО 9001-2001 существует с 15 августа 2001 года.
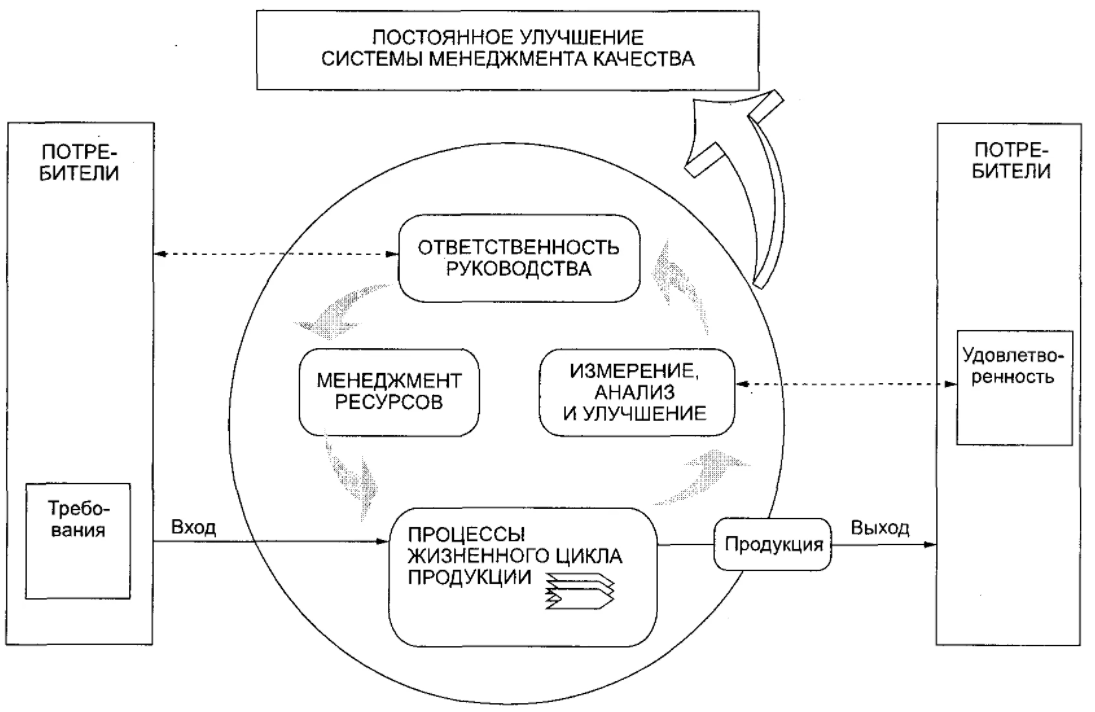
Российский опыт управления качеством
Движение за повышение качества продукции существует в России со времен индустриализации. Со временем стало ясно, что устойчивое повышение качества продукции не может быть достигнуто отдельными, даже большими, но изолированными мерами. Только систематическое и всестороннее взаимоувязанное осуществление технических, организационных, экономических и социальных мероприятий на научной основе позволяет быстро и устойчиво повышать качество продукции.
Факторы, влияющие на качество продукции, можно обобщить в трех блоках: Качество производимой продукции зависит от внутренних (внутренних) обстоятельств, человеческого фактора и внешних условий.
Давайте проследим шаг за шагом последовательность реализации системного подхода к организации работы по совершенствованию ЦП в отечественной практике.
В 1950-е годы преобладала саратовская система бездефектного производства и поставок продукции с первого представления (ВВП).
Целью системы является создание производственных условий, позволяющих работникам выпускать продукцию, не отклоняясь от технической документации.
Основным критерием количественной оценки качества работы работ работника являлся процентный показатель объема работ, принятый на первой презентации, рассчитываемый как процентное отношение количества лотов, принятых на первой презентации, к общему количеству лотов, произведенных работником и представленных в ККР.
Определенное количество материального и морального стимулирования зависело от процента доставки продукта с первой презентации.
Внедрение системы ВВП стало возможным:
- Обеспечить строгое соблюдение технологических процедур;
- повысить персональную ответственность сотрудников за качественные результаты их работы;
- лучше использовать моральные и материальные стимулы для работников;
- создать условия для широкого использования движения в целях повышения качества продукции.
Моральные стимулы привели к появлению званий «Мастер золотых рук», «Отличный качественный работник» и так далее. С течением времени функции QCD изменились — управление стало избирательным, а основой стал самоконтроль. Последние выявили недостатки, не зависящие от работника, что привело к проведению «дней качества» и созданию постоянных комиссий по качеству. В ряде компаний процент количества рабочих дней без дефектов из общего количества рабочих дней был заменен процентом количества рабочих дней без дефектов.
В то же время система ВВП имеет ограничительную сферу действия; она распространяется только на работников основных производственных цехов.
Система работает по принципу «есть дефект — нет дефекта», без учета многообразия дефектов и их различной степени влияния на качество выпускаемой компанией продукции.
В принципе, БИП было закреплено в зарубежных программах «с нулевым дефектом» и сохранено во всех отечественных программах. Более того, когда отмечался десятилетний юбилей КГУП, он был зарегистрирован только в 30000 компаниях, а ВВП на тот момент — в 60000.
Львовская версия саратовской системы — система безошибочной работы.
(SBT) была впервые разработана и внедрена в начале 1960-х годов на Львовском заводе телеграфного оборудования и ряде других предприятий Львова.
Целью системы является обеспечение выпуска продукции отличного качества, высокой надежности и долговечности за счет повышения ответственности и мотивации каждого сотрудника компании и производственных коллективов за результаты своей работы.
Основным критерием, характеризующим качество работы и определяющим уровень материального стимулирования, является коэффициент качества работы, который рассчитывается для каждого работника предприятия, каждого бригады за определенный период времени (неделя, месяц, квартал), с учетом количества и важности допущенных производственных нарушений. Система создает классификатор основных видов нарушений производства: Каждое нарушение соответствует определенному коэффициенту уменьшения. Максимальная оценка качества работы и максимальный размер премии устанавливаются для тех сотрудников и бригад, которые не имели нарушений в течение отчетного периода.
Внедрение SBT сделало это возможным:
- для количественной оценки качества работы каждого сотрудника, каждой команды;
- повысить интерес и ответственность каждого сотрудника, каждой команды за качество своей работы;
- Совершенствование трудовой и производственной дисциплины всех сотрудников компании;
- вовлечь всех сотрудников компании в конкуренцию для повышения качества продукции;
- Сократить потери, связанные с браком и претензиями, и повысить производительность труда.
Львовская СБТ, как и саратовская система БИП, состояла в том, что применялась в основном на стадии производства продукта. Попытки применения принципов бездефектной работы в научно-исследовательских и проектных организациях хорошо известны, однако SBT широко применялся на промышленных предприятиях для оценки и стимулирования исполнительных (не творческих) работ.
Система CANARSPI
Система CANARSPI (Качество, Надежность, Срок службы первых изделий) была впервые разработана и внедрена на Горьковском (Нижний Новгород) машиностроительном предприятии в 1957-1958 годах. В этой системе особое внимание уделялось повышению надежности продукции за счет повышения технической подготовки технологов-проектировщиков и технологов-производителей, на долю которых приходится 60-85% обнаруженных на заводе дефектов. Были созданы прототипы оборудования, деталей, систем и изделия в целом, проведены их исследовательские испытания. Значительное развитие получили опытное производство, стандартизация и унификация, системы общих технических стандартов, таких как Единая система конструкторской документации (ЕСКД), Единая система подготовки технологической продукции (ЕСТП).
Особенностью системы CANARSPI является то, что она выходит за рамки этапа производства и включает в себя множество видов деятельности как на этапе исследований и проектирования, так и на этапе эксплуатации. На этапе исследований и проектирования опытных образцов большое внимание уделяется выявлению причин неисправностей и их устранению в предпроизводственный период.
Данная задача решается путем развития научно-исследовательской и экспериментальной базы, повышения коэффициента унификации, широкого применения методов моделирования и имитационного моделирования, ускоренных испытаний, а также конструкторско-технологических испытаний изделий в процессе технологической подготовки к производству. Результаты работы изделия учитываются в системе как обратная связь и используются для совершенствования конструкции изделия и технологии его производства.
Принципы бездефектной работы и бездефектного производства широко распространены в компании CANARSPI.
Внедрение системы CANARSPI на ряде предприятий Горьковской области стало возможным:
- сократить время изготовления новой продукции до заданного уровня качества в 2-3 раза;
- повысить надежность выпускаемой продукции в 1,5-2 раза, увеличить срок службы в 2 раза;
- сократить трудоемкость и цикл сборки в 1,3-2 раза;
Планирование повышения качества продукции и управление КП в соответствии с этим критерием, а также расширение внимания к качеству на протяжении всего жизненного цикла продукта были разработаны в системе NORM.
Система NORM (Научная организация труда по увеличению срока службы двигателя) впервые была разработана и внедрена на Ярославском двигателестроительном заводе в 1963-1964 годах.
Целью системы является повышение надежности и долговечности выпускаемых двигателей.
Система NORM основана на принципе последовательного и систематического контроля ресурса двигателя и его периодического увеличения, основанного на повышении надежности и долговечности деталей и узлов, ограничивающих ресурс двигателя; основным показателем в системе является ресурс двигателя до первого капитального ремонта, выраженный в часах работы двигателя. Планируется рост этого показателя в системе.
Организация работы в системе основана на циклическом принципе. Каждый новый цикл повышения ресурса двигателя начинается после достижения ранее запланированного уровня ресурса двигателя в производстве и включает в себя определение его фактического уровня, выявление деталей и узлов, ограничивающих ресурс двигателя; планирование оптимального уровня повышения ресурса двигателя; разработку и апробацию технических рекомендаций по обеспечению запланированного уровня ресурса двигателя; разработку комплексного плана конструкторско-технологических мероприятий по разработке двигателя с новым ресурсом в производстве; реализацию комплекса конструкторско-технологических мероприятий по разработке двигателя с новым ресурсом в производстве.
На этапе производства система NORM содержит положения систем BIP и SBT; на этапе строительства — наиболее важные положения системы CANARSPI.
Внедрение системы NORM позволило увеличить срок службы ярославских двигателей с 4000 до 10000 часов до первого капитального ремонта, продлить гарантийный срок двигателей на 70% и сократить потребность в запасных частях более чем на 20%.
Достижение запланированного уровня качества стало возможным благодаря комплексному подходу к СМК, сочетающему опыт предыдущих систем на всех этапах жизненного цикла продукта.
CSUCP
В 1975 году на прогрессивных предприятиях Львовской области появились комплексные системы управления качеством продукции (CQMS). Целью СМК было создание продуктов, соответствующих лучшим мировым аналогам и достижениям науки и техники. С 1978 года Госстандарт разработал и утвердил систему основных функций СМК. В связи с внедрением СМПС, метрологического обеспечения производства (МОП), многоуровневого анализа неудач и статистического контроля качества, были созданы группы качества, разработаны программы качества на предприятиях и в ассоциациях, внедрена сертификация продукции, широко развита сеть высших и низовых организаций и сеть учреждений повышения квалификации специалистов в области менеджмента качества, внедрены курсы по стандартизации и СМПС в программах высшего образования. В 1985 году было отмечено, что за десятилетие с помощью ПСМКВ удалось создать и успешно внедрить конкурентоспособную продукцию, увеличить долю производства высшей категории качества в 2-3 раза, значительно сократить потери из-за дефектов и рекламаций, сократить время разработки и внедрения новой продукции в 1,5-2 раза. В то же время было отмечено, что на многих предприятиях при построении систем менеджмента качества (СМК) нарушались основные принципы комплексного системного подхода, что приводило к формализму в этой работе и, по сути, к отсутствию системы. Основными причинами этого являются отсутствие экономической мотивации компаний к совершенствованию СМК и, соответственно, системы, а также внедрение СМК в компаниях с помощью чрезмерных административных методов. Это заставило многих поверить, что СМК не оправдана и не должна быть внедрена. В то же время уже во время реструктуризации экономики и перехода к коммерческому учету стало ясно, что ЦП стал основным условием жизнеспособности компаний, особенно на внешнем рынке.
Дальнейшее развитие СМК происходило в рамках систем управления более высокого уровня: от отраслевого и территориального до государственного, на основе разработки «качественных» программ и их включения в национальные экономические планы. Так была организована внешняя среда систем управления качеством. В 1978 году были разработаны и утверждены Госстандартом основные принципы Единой государственной системы менеджмента качества (ЕГМК).
CSAMS и EIR.
Внутри компаний менеджмент качества продукции также занимался более широким кругом вопросов. Во многих компаниях решение задач по улучшению качества продукции связано с эффективным использованием ресурсов. Примером такой системы была Днепропетровская СМК и ЭИР.
Созданы комплексные системы повышения эффективности производства (КСЭПП) и, наконец, система управления предприятиями и объединениями (ГОСТ 24525). Вопросы управления качеством в этих экономических системах занимали долю от одной пятой до одной пятнадцатой (по количеству целевых подсистем управления). Конечно, Госстандарт в одиночку уже не мог управлять вышеупомянутыми системами в целом, и другие ведомства (Госплан, ГКНТ, Госкомтвуд и т.д.) не видели в этом необходимости.
С переходом к рыночным условиям исчезли направляющие методы управления, возникла конкуренция товаропроизводителей, которые непосредственно ощущали требования мирового сообщества к качеству продукции.
Большой заслугой Госстандарта в период перехода на рынок стала работа по гармонизации отечественных стандартов систем качества с международными, отражающими отечественный опыт в области управления качеством. Несмотря на негативные последствия экономического кризиса в России, уже в фазе выхода из кризиса, наблюдается четкая ориентация на повышение качества продукции.
Преобразование в ISO 9000
Переход от экономики планирования затрат к новому периоду ее развития, когда отпускная цена на продукцию уже не является единственным критерием решения для потребителей сформулировать требования к желаемому качеству продукции, потребовал соответствующей реструктуризации и от высшего руководства отечественных предприятий.
В переходный период экономики компании сталкиваются с необходимостью поиска внутренних резервов для своего развития. Единственным способом получения средств на развитие является снижение себестоимости («цена минус, а не себестоимость плюс»). Только качество существующего производства позволяет экономить средства на развитие.
Согласно ISO 9000, система качества — это совокупность организационных структур, процедур, процессов и ресурсов, необходимых для осуществления менеджмента качества.
В соответствии с отечественной терминологией систему качества следует рассматривать как организационно-техническую систему, состоящую из трех основных компонентов: организационной структуры; технического и методологического обеспечения.
Осознание того, что в настоящее время управление компанией должно осуществляться через качество, привело к реорганизации центров качества заводской продукции в Директорат качества (DQC) с прямым подчинением его директора Генеральному директору — Председателю компании и наделением соответствующими полномочиями. В DQC назначены соответствующие организационные структуры, которые обеспечивают выполнение функций системы качества.
Технология структурного анализа и проектирования (технология SADT) была использована для оптимизации организационной структуры DpK, а ее применение автоматизировано. Часть технологии SADT, называемая IDEFO, в настоящее время стандартизирована. Использование технологии SADT позволяет «раскрыть» функцию системы вплоть до самого низкого уровня — конкретных исполнителей, нормативных документов (форм) и т. д. Проведен структурный анализ и моделирование функционального потока ЦОД и его основных служб, оптимизирован поток информации и материалов. Это позволило определить следующие основные функции:
- Внешний — взаимодействие с поставщиками, с потребителями;
- Внутреннее — внутреннее управление, основанное на аудите продукции, технологических процессов, систем качества; документация и обеспечение непрерывного развития систем качества; управление контрольно-измерительным и испытательным оборудованием, а также затратами на качество и его оптимизацию.
Техника SADT — StructuredAnalysisandDesingTechnique — представляет собой графическую нотацию и подход к описанию систем.
Выполнение этих функций подкрепляется соответствующей нормативной документацией, информационными системами и обучением персонала.
Техническая поддержка системы качества как для PQF, так и для других областей завода состоит из контрольно-измерительного оборудования, испытательных стендов, компьютеров, информационных сетей, универсального программного обеспечения и др. Осуществляются следующие мероприятия: Модернизация и развитие локальных информационных систем, расширение их возможностей за счет внедрения нового аппаратного и программного обеспечения; интеграция локальных сетей подразделений в единую информационную систему ДПК и всего предприятия в целом; закупка компьютерного оборудования, нового тестового оборудования.
Методическое обеспечение системы качества включает в себя: Методы, методики, процедуры, реализуемые в нормативно-технической документации системы качества; система мотивации сотрудников к качественной работе; проблемно-ориентированное (прикладное) программное обеспечение; программы, учебные пособия для обучения сотрудников.
Реорганизация системы качества, несомненно, повлияла на нормативную документацию. В частности, была полностью пересмотрена структура действующей системы и содержание соответствующих корпоративных стандартов, выявлены недостающие документы и недостатки существующих, выделены фундаментальные и взаимодополняющие СТП, установлен их рейтинг и критически оценен. Построена шестиуровневая документационная пирамида системы качества, включающая: концепцию развития системы, философию качества, политику качества; общие руководящие принципы и ведомственные руководства по качеству; основные процедуры и методы системы качества; инструкции; фактические документы (бланки, протоколы и т.д.).
Компания проводит детальный анализ методов и процедур, а также результатов оценки качества готовой продукции.
На странице курсовые работы по менеджменту вы найдете много готовых тем для курсовых по предмету «Менеджмент».
Читайте дополнительные лекции:
- Элементы качества
- Менеджмент в телекоммуникациях
- Потребность и необходимость управления в деятельности человека
- Отчеты системы менеджмента качества
- Стратегическое и оперативное управление затратами предприятия
- Планирование деятельности малого предприятия
- Матрица ЭСИСП и рейтинг ЭСИСП. Преимущества и недостатки
- Процесс коммуникации
- Группы рисков в менеджменте
- Бихевиористские теории лидерства